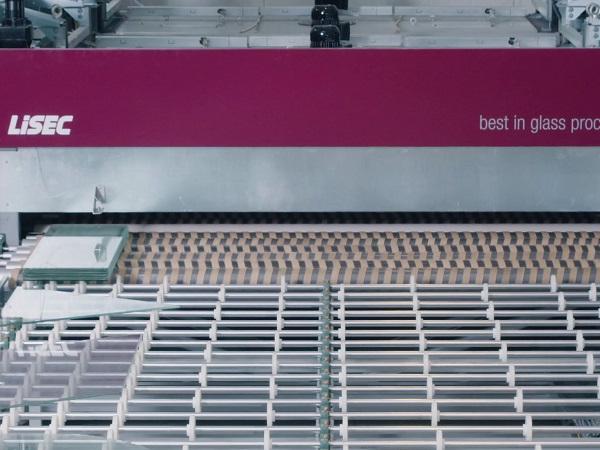
Date: 25 June 2021
SEMCO and LiSEC have more than the ultimate quality standards in common. Both companies place the highest value on individual implementation of customer requests and on premium solutions to customer needs.
With this in mind, we also worked together on the last joint project — replacement of a pre-lamination unit on an Armatec lamination line at SEMCO Glastechnik Neubrandenburg. The expectation: Millimetre-precise pre-lamination that optimally integrates into the existing line and can be adapted to the existing cleanroom.
SEMCO – GLASS MADE IN GERMANY
At a total of 19 sites in Germany, the SEMCO Group produces almost 5 million square metres of insulating and safety glass, and more than 5 million square metres of glass are coated. SEMCO’s product portfolio is comprehensive: From the sustainable multi-function product SEMCO Klimaglas to insulating glass applications for sound or break-in protection to glass construction and interior design applications, SEMCO treats every request as a completely individual project.
SEMCO strives to find an individual solution for every specific project. Starting with the creative idea and continuing through product design, production and delivery, SEMCO optimally supports the customer throughout the process. This is achieved through strong employee motivation, which — paired with a high level of environmental consciousness — makes intense customer focus and the resulting customer satisfaction possible.
The very high quality level and extremely reliable product delivery are ensured by internal flat glass production that draws on regional raw materials. The company’s own coating facility can also quickly and flexibly react to market developments. Alexander Akgül, technical director of the SEMCO Group, assures: “As a middle-sized company, we have always stayed close to our roots and live our team and family values throughout the company. On the one hand, our group structure makes us flexible enough to react quickly, and on the other hand large enough to offer our customers security and uniform quality over the years. At SEMCO, we invest in the future of the company and thereby in growing customer satisfaction and product quality.”
LAMINATING WITH LISEC FOR GROWING SUCCESS
In searching for a new pre-lamination unit for an existing laminated glass production line from Armatec, LiSEC learned about SEMCO Glastechnik Neubrandenburg. Together they developed a solution based on the technology used, the expected quality and replacement and speed that met SEMCO’s expectations.
Based on SEMCO’s expectations, LiSEC integrated the pre-lamination unit into the existing line with millimetre precision and adapted it to the existing cleanroom. No changes to the established spaces were needed. Additionally, LiSEC integrated automatic film trimming into the existing line. Coordination of the existing line components with their own controls and the controls of the new solution went off without a hitch. Even the safety zones were adapted to the new requirements.
After the project meetings and project confirmation, it took only two weeks before the conversion was done and production could be started up. Active support from the SEMCO employees was crucial to mutual success. “The constructive collaboration with SEMCO and their highly professional employees, along with their deep process knowledge made quick implementation of the project possible,” says Rupert Wellner, Sales Manager LAMI at LiSEC Germany.
Kevin Bosse, CEO of SEMCO Glastechnik Neubrandenburg, is impressed with the cooperation: “In LiSEC, we’ve found a partner who really understands what it’s about. The collaboration went harmoniously, and we were very satisfied that, in every phase, our LiSEC colleagues looked at the project from our point of view, so we could complete the installation very fast, and without any major downtime.”
A LISEC PRE-LAMINATING UNIT WITH PLENTY OF ADVANTAGES
The conversion’s benefits are many. For one thing, the line’s output increased by 10% to 20%, and operating the system is significantly easier. The system automatically controls and regulates all recipes. The operator just releases the system for inward transport. All major parameters are automatically validated by the system. Thanks to the replacement of the pre-lamination unit, the existing laminated glass line can now be run many more years with high quality.
At the same time, it achieves significant energy savings of about 25% to 30% compared to the old solution. This fits perfectly with SEMCO’s sustainability activities. Every year, recycling of used and broken glass routes so much material back into raw glass production that over 25,000 tonnes of CO₂ can be saved. And in its production facilities, in a project with energy provider EWE AG, SEMCO has successively converted all its sites to energy-saving LED lighting.
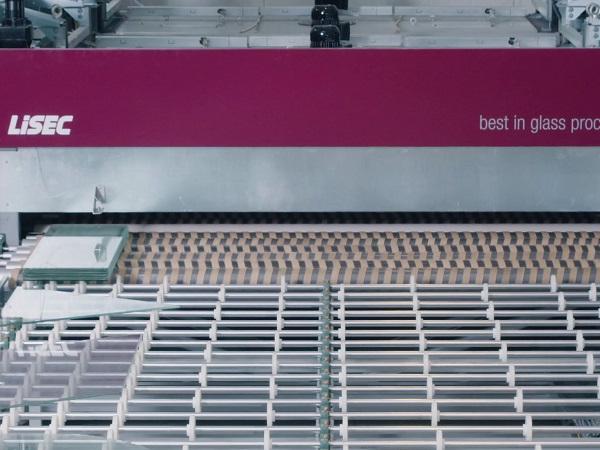

Add new comment