Via Marcatutto 7, (Milano) Italy
Albairate 20080 MI
Italy
R.C.N. Solutions Srl
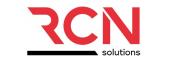
Find us on:
R.C.N. SOLUTIONS SRL is an Italian company founded in 1997. It is run by the Calvi family having over than 50 years of experience in the glass industry.
The company is located close to Milan, covering an area of 2.500sqm, 27,000 square feet.
At the beginning, the production was limited to fusing and bending kilns to be improved later with laminating kilns and chemical tempering plants.
RCN SOLUTIONS has been the first company in the world to launch a patent system to produce clear glass wash-basins, real jewels for interiors, perfect in shape and transparency. The process was based on the combination of three different temperatures working independently during the recipe.
Later in the 2000, a new scenario was taking shape for glass applications and requirements. The market was opening to new ideas in laminating systems to grant safety glass more and more.
RCN understood this way would have been a very important job and started to study process solutions issuing its first EVA laminating kiln in 2003, thou limited in size and production.
This system immediately met the approval of many companies worldwide who were looking for alternative to PVB and autoclave. Some glaziers had not the volumes to justify the investment for an autoclave, but wanted to enter the laminated market because safety glass was specified into several projects, even on a small scale.
All these different needs made RCN to take action to offer different machines sizes, and study additional combinations to enhance customers’ production. The Lammy line is still successful and still under development, able to offer jumbo size and over. In 2008, a new laminating machine has been introduced: Powerlam, the turn-around system for fast lamination, remarkably reducing the process timing. Powerlam is significant for all those companies who need to maximize standard productions and work on shifts.
The latest is RCN’s ISF - Integral Sequencing Framework - a production layout including all the RCN machines lines, working in sequence – bending, chemical tempering and lamination – the important step for manufacturing safety glass. On the top of the ISF, REVA BF: the EVA laminating interlayer, certified according to the EU norms by the Rosenheim Institute.
The recent, patent pending innovation is RD CLEAN CONCEPT, the system for clean edges after lamination, launched in 2021 and receiving great attention from small and big international companies who have understood the potentialities of a product allowing for time, costs and labor savings.
Under the motto “essential is better”, RCN machines and equipment are studied and manufactured to be simple but effective, granting performance and easy use and maintenance.
Machines would be nothing without an important backstage where commercial and technical teams work hand-in-hand sharing the same target: customer satisfaction. The RCN staff is working daily to encourage the ability of listening to customers’ needs, and on the importance of a good service.
The team is a real cohesive unit working with determination to find innovative solutions and new business challenges.
Especially in the last decade, RCN SOLUTIONS has enhanced the technical and commercial service and ensured flexibility in construction which is a very important issue in order to meet all the international requirements. In particular, the ability for flexibility in production is one of the most appreciated value of RCN SOLUTIONS.
R.C.N. SOLUTIONS IN DATES
The Early Days – the company started the business in 1997, focusing on the production of glass fusing and bending kilns, with an important development: the patented system to manufacture perfect glass wash-basins based on three different running temperatures, independently controlled by the PLC. This system granted the utmost clearness and the glass surface free from distortions. The novelty met a great success and showed a young, proactive company whose destiny was to become one of the most innovative spirit among the glass machinery manufacturers.
2000: a new development – the new century marks the creation of a new machines line. The laminating bagging system joint to an absolute new development, to be introduced in 2008: Powerlam, the autoclave-free, fast, turn-around laminating system.
This unique, semi-automatic, bag-free system, met a great international success and it is still one of the most demanded RCN machines.
In the same way, the Modular version of the bagging laminating line carried out by RCN has been an important issue in the glass industry, widely imitated by other manufacturers. The Modular line grants the purchase of one laminating machine that can be upgraded later by installing optional in order to increase production without buying a new machine, thus saving a lot of costs.
In the same way, RCN has developed glass bending kilns able to perform the most complicated curves based on a special technical design and construction.
2010-2020: the revolution – in ten years, the company invested to introduce new products on the market. In 2013, after years of cooperation with international chemical companies and further to several searches, RCN issued a new EVA chemical formulation, the one of REVA BF, the new certified, extra clear laminating interlayer, also distributed in the U.S.A and Canada since 2016.
In 2017, RCN introduced its last development, a project in progress since 2015, for the constructions of a chemical tempering line, under the brand “RIVA BY RCN”.
During this time, RCN has extended its sales and has currently some machines installed in Oceania too.
This new line has drawn the attention of some international companies such as AGC and Schott.
April 2020 – Easy Connect App installed in our machines to check the production cycle in real time by cell phone, tablet and PLC.
June 2020 – RCN launches ISF – Integral Sequencing Framework – a complete production layout including bending kilns, chemical tempering line and laminating system.
March 2021- RCN launches RD CLEAN CONCEPT – the revolutionary and definitive system for clean edges after lamination.
September 2022 - RCN launches MULTIPLIED – the jumbo size machine and over, built in modules.
RCN SOLUTIONS in numbers:
- 55 Powerlam installed world-wide
- more than 600 laminating machines, bagging system, installed world-wide in different sizes ad different layout
- more than 200 bending kilns installed
- 16 chemical tempering lines sold since 2017
- more than 30.000.000 sqm of REVA BF distributed
- more than 90 RD CLEAN CONCEPT installed since March 2021
For further information, visit our website: www.rcnsolutions.it.
Products
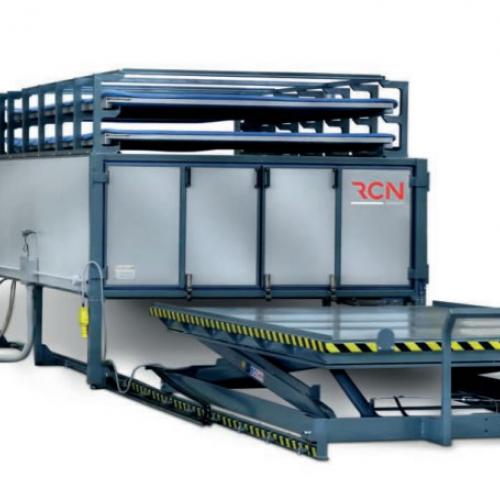
- LAMMY SYSTEM 2 MODULAR
- LAMMY SYSTEM 4
- SMART
- OVERSIZE MACHINES
- LINE PROJECTS
- ACCESSORIES FOR LAMINATION
- PRODUCTION EQUIPMENT
- SILIKOSOFT
POWERLAM
SPEED IN A TURN-AROUND SYSTEM
Semi-automatic laminating line for fast production, turn-around system, for flat glass only. The glass exits fully laminated and cooled down thanks to the automatic cooling system based on forced ventilation. Several machines installed worldwide in the last 12 years upon customers’ great satisfaction.
- Bag-free technology, one operator only
- Max workable thickness: 45mm
- Exclusive RCN Solutions project and production
- Possible process certification (CE)
- Process time 80% lower than other market’s choices
- Automatic opening of the chamber by means of the hydraulic unit
- Electrical heaters based on indipendent sections equipped with convection heat
- Uniformity of the temperature (tolerance ± 1°C)
- PLC – 10” touch screen. intuitive, interfaced to the management system
- Aspiration pump, 100m3/h, with pressure control
- Perforated kevlar transmission belt with “alligator” fixing system
- Loading/unloading synchro automatic conveyors
- Double sensors in/out equipped with alarms and photocells
- Glass positioning by means of pneumatic lifting pistons and ball-castors
- Automatic cooling system – RCN Solutions concept
- Line-up with existing machines and/or assembly systems
LAMMY SYSTEM 2 MODULAR
FLAT AND CURVED GLASS LAMINATION – MAX BENDING RADIUS 1500mm
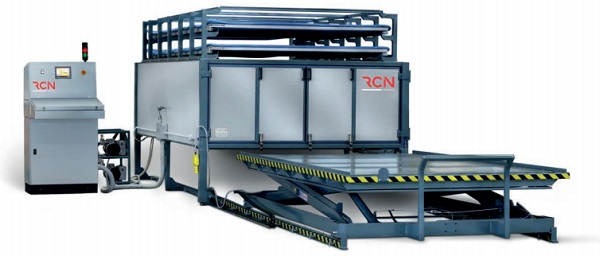
Main features: easy process, highly performing, compact solution
- Max workable thickness: 100mm
- Volcanized Silikosoft bags, long life, resisting to 280°C, made in Italy
- Heating system: radiation/convection, Hybrid-Pro Due
- Two aspiration pumps, one per shelf
- Retractable platform, capacity 1500/2000kg. Electrical movement
- Automatic cooling with lateral heat-escape door
- 7” Touch Screen PLC equipped with Easy Connect App
- Additional overtop shelves-storage structure, three positions and two additional shelves complete with aspiration bags and pump
- Version with one shelf and handling trolley available
LAMMY SYSTEM 4
LARGE VOLUMES
Laminating line for flat and curved glass, max radius 1200mm. Laminating line suitable for production of big volumes, also structured from upgrade of Lammy System 2. Main feature: production flexibility for both thickness and volumes. Two laminating chambers with indipendent operation, process and control, mastered by one PLC only.
POSSIBILITY TO INSTALL ADDITIONAL PRODUCTION LAYOUT
ex. Overtop storage unit, 3 positions or 5 positions, frontal or lateral positioning
- Max laminating thickness: 100mm
- Volcanized Silikosoft bags, long life, resisting to 280°C, made in Italy
- Heating system: radiation/ convection, Hybrid-Pro Quattro
- Four aspiration pumps (one per shelf)
- Lifting platform, capacity 1500/2000kg Electrical movement
- Automatic cooling by means of an heat-escape door
- 7” Touch PLC equipped with software for the two independent chambers
- Easy Connect App installed
- Extractible chambers partition
SMART
EASY AND ESSENTIAL
Kilns suitable for the industry of design, building and internal decoration. Multi-function machines: paint and marble drying, lamination with inserts, Led, etc. Flat and curved glass lamination. Radius: 250/500/1000mm.
1) SMART ESPACE
- Single chamber kiln with 4 shelves
- Volcanized vacuum bags, long life, resisting up to 280°C, made in Italy
- Heating system: radiation/convection
- Four aspiration pumps
- Semi-automatic lifting platform, capacity 1500kg
- 7” Touch Screen PLC – wall-mounted
- Easy Connect App
2) SMART XXL
- Single chamber kiln, single shelf
- Retractable handling trolley
- 1 aspiration pump
- Heating system: radiations in two indipendent zones
- 7” Touch Screen PLC – wall-mounted
- Easy Connect App
3) SMART XXL DOUBLE
- Single chamber kiln, double shelf
- Handling trolley, two positions, sliding on rails
- 2 aspiration pumps
- Heating system: radiation and convection
- 7” Touch Screen PLC – wall-mounted
- Easy Connect App
OVERSIZE MACHINES
FOR JUMBO SIZE GLASS
Following the great success of the laminating lines in modular system, RCN Solutions has developed a line based on the construction of coupling segments to satisfy the oversize glass sheets, maximizing the shipping costs.
LINE PROJECTS
ACCESSORIES FOR LAMINATION
This section lists all the equipment completing and helping the lamination process.
- Micro-porous adhesive tapes for high temperature
- Thermocutter/Blades
- Datalogger with flat thermocouple
- Anti-static roll
- ReVA 12 – clean edges helper, complete with the applicator
- Spare parts – The RCN kilns do not require spare parts in stock. Vacuum pump maintenance kit, bag reparation kit, aspiration hoses, valves, click-clack valves, and mesh for bags are available
PRODUCTION EQUIPMENT
- ROLLS-HOLDERS - To store and/or refrigerate the laminating interlayer rolls
- PORTIQUE - Automatic or semi-automatic glass transfer systems
- TABLES - Assembly table, tilting or fixed. The top of the table is equipped with lifting frame and ball castors
SILIKOSOFT
Lamination bags of any size, particularly designed for special laminations, for big thicknesses and curved glass. The Silikosoft bags have a special closing system by manual pression, developed by RCN more than ten years ago. This great sealing system is volcanized to grant resistance with special glass shapes or curves too. Long life and deflection memory . The Silikosoft bags can also be manufactured for laminations in ACV, flat or vertical with reinforced base and volcanized hooks.
- High adhesion capacity to the most complex shapes with moderate effort
- High resistance to tearing
- Higher performance with high temperatures
- Good resistance to compression
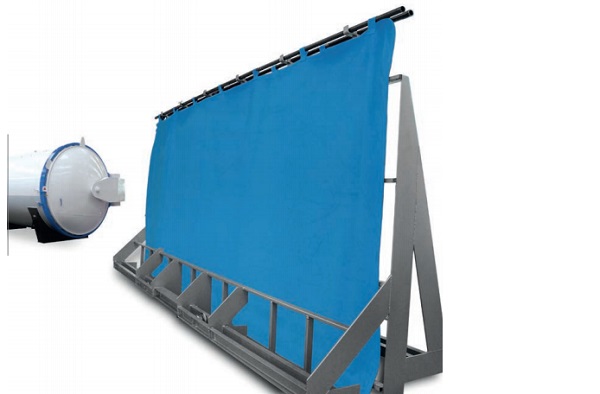
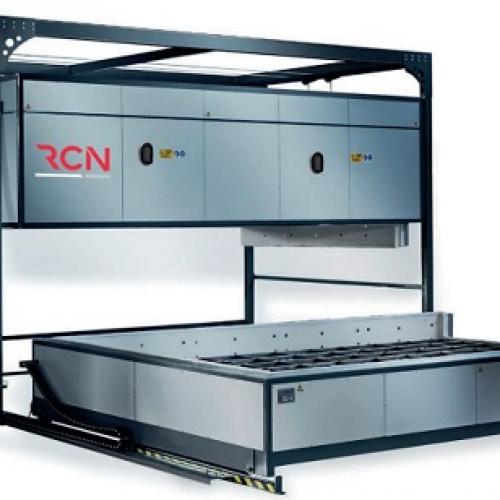
ECO BENDY
SPECIAL BENDING KILNS, DESIGNED FOR CURVES PARTICULARLY COMPLEX, WITH DOUBLE RADIUS TOO
CURVES PERFECTLY MATCHING FOR LAMINATION
Heating system in sections, 3 or 4 lower sections and 3 or 4 upper sections, with set-up of different temperatures controlled by the PLC
- Hydraulic kiln-top lifting
- Moulds-holder structure made of steel
- 6/8 thermocouples
- Electrical movement equipped with speed regulator
- The Bendy version is equipped of two heating zones only, one lower and one upper zone
- Pre-set for the external system for the production of 90° curves
- Possible radius: 900mm and 1200mm
Our chemical tempering plants are the result of years of studing and researching in cooperation with experts of the glass industry. The different plants and the possibility for customization have drawn the attention of some international companies, looking for added value products. However, our strength lies in the ability of satisfying all the enquiries, since the chemical tempering opens up to uncountable projects: from optical to aviation; from automotive to building. And we are here to listen.
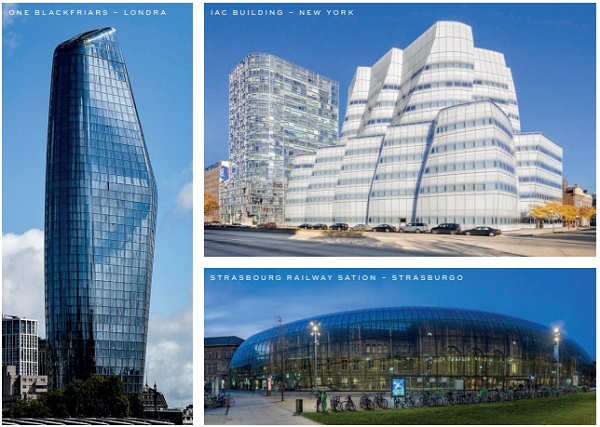
FEATURES
- High resistance against mechanical impact
- High resistance against scratches
- No optical distortion
- Tempering of thin glass possible
- Low energy consumption
APPLICATIONS
- Display and cover glass
- High speed trains and cars
- Boats and yachting
- Military applications
- Security glass and fire protection doors
- Architectural glass
- Aircraft industry
- Table ware
- Optical glass
- Lighting applications
- Washing machine windows
OPERATING PROCESS
- Glass preparation
- Rack loading
- Preheating
- Ion exchange in a salt tank
- Cooling
- Washing
- Drying
- Unloading
CUSTOMISABLE PRODUCTION SOLUTIONS AND CUSTOMIZED MACHINES
CT320
MANUAL VERSION 700x450mm kW 16 (base)+6 (cupola)
APPLICATIONS
- Optical glass
- Display & cover glass
- Pharmacy
- Lighting application
- Machine inspection window
CT330/331
AUTOMATIC VERSION 700x450mm / 1000x1000mm kW 16+6/39+12
APPLICATIONS
- Display & Cover glass
- Automotive
- Transport engineering
- Pharmacy
- Lighting application
- Machine inspection window
- Aircraft
- Optical glass
- Military applications
CT900/950
AUTOMATIC VERSION 2000x1000mm/3200x2200mm kW 60+24/100+40
APPLICATIONS
- Architectural glass
- Fire protection door
- Boat & yachting
- Aircraft industry
- Curved glass
- Display glass
- Insulated glass
- Shower doors
- Bullet proof glass
- Last generation laminating interlayer, top of the range, based on the use of raw materials supplied by international companies, without the use of recycled materials in production
- Chemical formula especially designed in cooperation with european laboratories and universities
- Suitable for all the special applications, in particular for all those jobs exposed to extreme weathering conditions