Vehmaistenkatu 5
Tampere 33730
Finland
Glaston Corporation
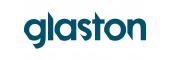
Glaston is a global company developing glass processing machines, services and solutions to the architectural, automotive, solar and appliance industries. The company also supports the development of new technologies integrating intelligence to glass.
Glaston delivers machines and services for production of heat-treated glass, insulated glass manufacturing, automotive and display glass processing. Our global offering is the most comprehensive in the market. Have a look!
Glaston operates globally with manufacturing, services and sales offices in 10 countries.
All about glass processing visit: www.glastory.net
Glaston seeing it through - architectural glass processing
Glaston seeing it through - automotive glass processing
Glaston seeing it through - appliances, solar and smart glass processing
Products
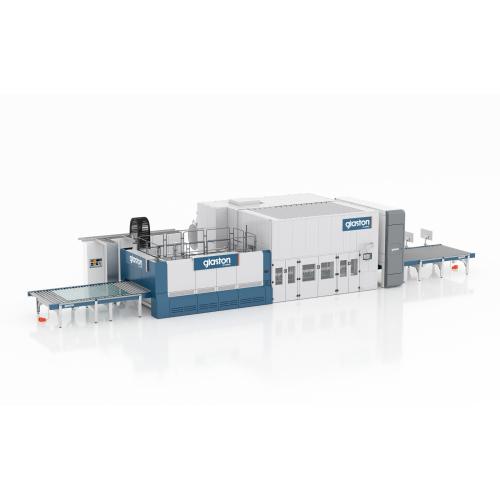
Glaston RC Series
Looking for a versatile tempering machine?
Here are three reasons why Glaston RC Series is your best choice
1. Capability to process any glass type, any thickness
2. Robust solution for continuous quality and output
3. Easiest to operate
The RC Series is designed to process all temperable glass types. It can be configured to meet even the highest capacity requirements with different convection options. The RC Series is always tailor-made to match specific customer requirements.
https://glaston.net/machine/rc-series/
Glaston FC Series
Need to produce high volumes of premium quality flat tempered glass?
Here are three reasons why Glaston FC Series is your best choice
- #1 for quality with any product or glass type
- Lowest production costs with high energy efficiency
- Highest automation level
Glaston FC Series flat glass tempering lines incorporate modern convection technologies and process automation for the highest yield and flexibility. What makes the difference is our high air volume convection systems, essential to producing world-renowned glass thanks to their superior heating accuracy. Chinook allows you to run at the highest yield, helping you minimize your energy consumption, while Vortex Pro gives you the highest flexibility with the utmost quality.
The tempering process Autopilot reduces the need for operator input and offers process control without parameters. The Autopilot automatically sets all necessary parameters based on the glass sheet placement on the line, enabling the operator to simply monitor the process.
https://glaston.net/machine/fc-series/
Glaston CHF Series
Need to produce high-quality flat tempered glass with serial production and high capacity?
Here are three reasons why Glaston CHF Series is your best choice
- Combine high capacity with high-quality
- Gain unmatched reliability
- Easiest to operate
The CHF Series concept provides the best solution for large production series of all glass types. The CHF Series platform is designed for evolving glass processing needs. The real key factor in terms of spotless glass quality is the Vortex heating and convection system. It enables unlimited heating uniformity and accuracy with its equally unlimited profiling and heating control.
https://glaston.net/machine/chf-series/
Glaston Jumbo Series
Need to produce small to ultra-jumbo sizes with the highest yield
of premium quality tempered glass?
Here are three reasons why Glaston Jumbo is your best choice
- Highest versatility for global demand
- Robust solution for continuous quality and output
- Highest automation level
Glaston Jumbo Series is built on the reliability and experience of 50 years of delivering high-end tempering lines worldwide. We have a peerless track record with large furnaces and tempering line lifetimes of 20+ years. Glaston Jumbo offers the best heating control available for high-quality results. It also gives you the extra capability to process Low-E glass in mixed sizes.
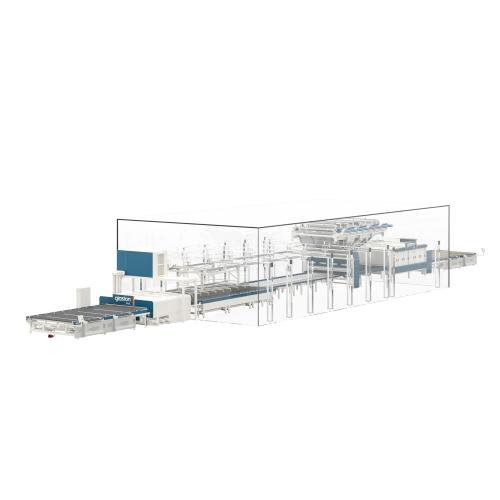
Here are three reasons why Glaston ProL is your best choice
- Unmatched yield and output
- Lowest operating cost – highest profitability
- Lifetime business growth
The very concept of ProL is based on reaching a production capacity balance with Low-E and clear glass. ProL uses full convection technology, which does not differentiate between glass types or product modes.
The convection system provides accurate and optimized heat transfer, giving you consistently superb glass quality and an up to 100% capacity increase compared to traditional infrared heating.
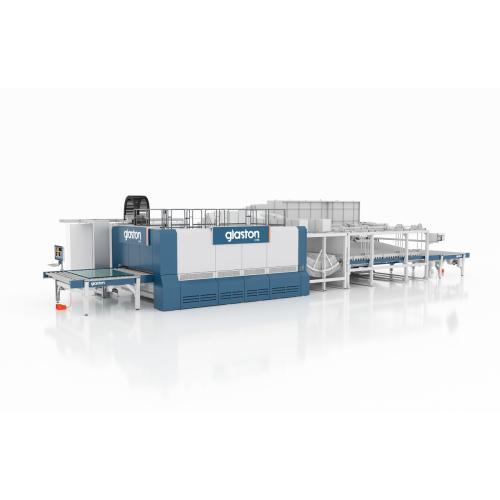
Here are three reasons why Glaston HTBS is your best choice
- Flawless quality with the most advanced heating control
- Highest yield
- Lifetime services
With over 50 years of process and machine building experience, Glaston HTBS is the answer to the most challenging needs of the automotive, appliance and furniture glass industries. It’s the #1 choice for the most demanding glasses, such as hopper glasses, which are large sidelites up to 2,400 x 1,700 mm with wide printed areas and cutouts. Whether you are producing big sidelites or small vents, the HTBS product range covers it.
Glaston ProBend
Need to produce premium quality bent tempered glass?
Here are three reasons why Glaston ProBend is your best choice
- Reach top-quality results from each run
- Save in production costs
- Grow your business for a lifetime
Glaston ProBend combines the latest know-how in heating with excellent control and optimization in the tempering process. ProBend is based on the unique Glaston Vortex Pro convection system, which enables efficient and accurate heat profiling. ProBend can temper Low-E glass, especially in large architectural sizes. It is also possible to bend and temper glass coatings against the rollers. Bending is performed by gravity or by pressing the glass against the rollers to assure high optical glass quality.
https://glaston.net/machine/probend/
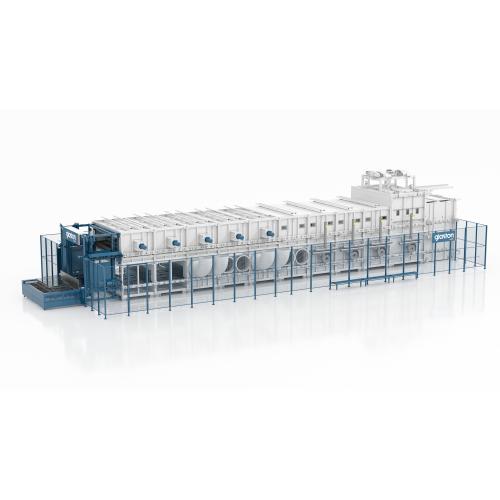
Glaston MATRIX EVO
Looking to produce the best windshields?
Here are three reasons why Glaston MATRIX EVO is your best choice
- GET TOP-QUALITY RESULTS FROM EACH RUN
- SAVE ENERGY – AND MONEY
- GROW YOUR BUSINESS FOR A LIFETIME
When you are looking for superior windshield quality, flexible production as well as reliable and energy-efficient operation, Glaston Matrix is your choice. It’s perfect for both mixed and single-model production of car and truck windshields.
https://glaston.net/machine/matrixevo/
Glaston ScreenMax
Superior solution for bending large high-quality windshields
Looking to produce large high-quality windshields?
Here are three reasons why Glaston ScreenMax is your best choice
- MASTER YOUR GLASS FORMING PROCESS
- CHANGE AND GROW WITH YOUR NEEDS
- GROW YOUR BUSINESS FOR A LIFETIME
The ScreenMax automatic serial bending furnace is suitable for the serial bending of large bus and truck windshields. It is available with pin lifters and manipulators for easier loading and unloading of the glass and molds.
https://glaston.net/machine/screenmax/
Glaston LAK – Assembling Conveyor
Here are three reasons for choosing LAK
- CHOOSE FROM SEVERAL LAYOUT ALTERNATIVES ACCORDING TO YOUR PRODUCTION REQUIREMENTS
- CHOOSE A CUSTOMIZED LINE
- CHOOSE A TURN KEY DELIVERY WITH CLEAN ROOM AND STRORAGE FACILITIES
Our product range in the area of PVB assembling and de-airing covers all windshield sizes on the market and a wide range of capacity levels and process layout possibilities depending on client requirements.
https://glaston.net/machine/lak-assembling-conveyor/
Glaston IKU – De-Airing Conveyor
Here are three reasons for choosing IKU
- HIGH PERFORMANCE
- FLEXIBLE VERSATILITY
- PROVEN RELIABILITY
Glaston IKU semi-continuous de-airing conveyor incorporates proven technology for effective air removal as well as uniform heating for enhanced de-airing results. IKU covers all windscreen sizes on the market and a wide range of capacity levels while enabling various layout possibilities for your tailored processing needs.
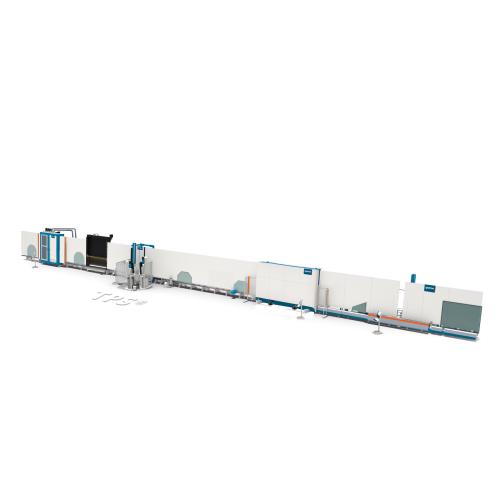
TPS® – Thermo Plastic Spacer
The original from the inventor
TPS® – Thermo Plastic Spacer is the premium insulating glass of the warm edge generation. The term “Warm Edge“ refers to a thermally-improved edge seal of an insulating glass unit. Materials that transfer significantly less thermal heat to the outside are used in place of conventionally used materials such as aluminum or steel. This leads to an increase in energy efficiency and a reduction in heating costs. Furthermore, TPS® reduces condensation.
Since 1994, we have accrued experience in warm-edge technology. Glaston is an industry leader as the inventor of TPS® production. So, you can rely upon the production of the future, placing your trust in this original product and our extensive experience.
https://glaston.net/machine/tps-thermo-plastic-spacer/
Glaston JUMBO & JUMBO XXL
The system solution for maximum requirements
Looking to aim big?
Here are three reasons why Glaston JUMBO and JUMBO XXL are your best choice
1. INSULATING GLASS UNITS UP TO 600 KG/M
2. MAXIMUM GLASS SIZE 3.3 X 18 M
3. GREEN PRODUCTION WITH OPTIMUM ENERGY EFFICIENCY
Glaston JUMBO and JUMBO XXL are insulating glass lines specially designed for manufacturing large-sized insulating glass units and façade elements up to 18 m in length.
https://glaston.net/machine/jumbo-and-jumbo-xxl/
Glaston VARIO
The individually configurable system solution for insulating glass using conventional, flexible and TPS® - Thermo Plastic Spacer
Looking for a customized insulating glass production line?
Here are three reasons why Glaston VARIO is your best choice
1. HIGH FLEXIBILITY AND EXCELLENT PRODUCTIVITY
2. LONG SERVICE LIFE WITH PREMIUM COMPONENTS
3. MULTIPLE LINE EXPANSION OPTIONS
https://glaston.net/machine/vario/
GLASTON SPEED
The benchmark in triple and quadruple insulating glass manufacturing using conventional, flexible, and TPS® - Thermo Plastic Spacer
Looking for the fastest possible insulating glass production?
Here are three reasons why Glaston SPEED is your best choice
1. PRODUCE TRIPLE UNITS AT THE SAME TIME OTHER LINES PRODUCE DOUBLE UNITS
2. IDEALLY DESIGNED WORK STEPS
3. CHOOSE BETWEEN CONVENTIONAL, FLEXIBLE OR TPS® SPACERS
https://glaston.net/machine/speed/
GLASTON COMFORT
The solution for standardized I.G. manufacturing
Looking for a fully equipped cost-effective production line?
Here are three reasons why Glaston COMFORT is your best choice
- NUMEROUS COMPONENTS AS STANDARD
- HIGH-QUALITY AND GAS-FILLED I.G. PRODUCTION
- RECTANGULAR AND SHAPED FORMATS
https://glaston.net/machine/compact-and-comfort/
GLASTON COMPACT
Start-up solution in automated insulating glass production
Looking to start automated insulating glass production?
Here are three reasons why Glaston COMPACT is your best choice
1. LOW INVESTMENT COSTS
2. COMPACT LINE LAYOUT
3. DIVERSE OPTIONS
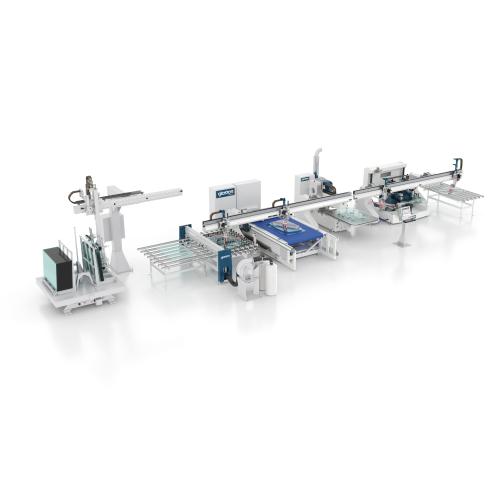
GLASTON CHAMP
The Glaston CHAMP EVO family includes product-specific lines for highly efficient and precise pre-cutting, shape cutting, breaking, grinding, and drilling of all automotive glass types. The standardized design offers not only a process-optimized cell layout but also various expansion options using upgrade kits.
Looking for highly efficient automotive glass pre-processing?
Here are three reasons why Glaston CHAMP equipment is your best choice
- HIGH REPETITION ACCURACY
- HIGH DEGREE OF AUTOMATION
- SHORT CHANGEOVER TIMES
The product range includes:
GLASTON CHAMP EVO WS – optimized solution for windshields
https://glaston.net/machine/champ-ws/
GLASTON CHAMP EVO BL – a clever solution for backlites
https://glaston.net/machine/champ-bl/
GLASTON CHAMP EVO SL – refined solution for sidelites
https://glaston.net/machine/champ-sl/
GLASTON CHAMP EVO QL – space-saving solution for quarterlites
https://glaston.net/machine/champ-ql/
GLASTON BRIGHT
The Glaston BRIGHT family includes product-specific lines for highly efficient and precise pre-cutting, shape-cutting, breaking, and grinding of thin glasses for
- Monitors, TV screens, and displays for mobile devices
- Automotive glass displays
- Solar applications
- Automotive glasses
The design offers not only a process-optimized cell layout, but also various expansion options using upgrade kits.
Looking for highly efficient thin glass pre-processing?
Here are three reasons why Glaston BRIGHT equipment is your best choice
- SHORT CYCLE TIMES
- HIGH REPETITION ACCURACY AND MINIMAL GRINDING ALLOWANCE
- EXCELLENT EDGE QUALITY
The product range includes:
GLASTON BRIGHT 9 – space-saving solution for thin glass displays
https://glaston.net/machine/bright-9/
GLASTON BRIGHT 25 – optimized solution for large displays
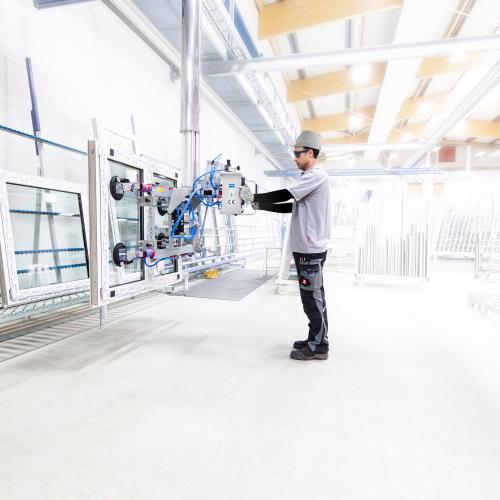
Glaston VACOOM’LIFTER
The new generation of handling equipment
Looking for a new-generation handling machine?
Here are three reasons why Glaston VACOOM'LIFTER is your best choice
1. INCREASED SAFETY STANDARDS
2. PROVEN, RIGID GUIDANCE
3. SENSORS FOR PREDICTIVE MAINTENANCE OF COMPONENTS
The newly developed Glaston VACOOM'LIFTER handling machine represents a successful combination of traditional equipment manufacturing processes and digital transformation. Let’s call it Glaston 4.0 in practical use.
More: https://glaston.net/machine/vacoom-lifter/
GLASTON EASY’LIFTERS
Ergonomic, universal handling equipment
Looking to handle flat glass efficiently?
Here are three reasons why Glaston EASY'LIFTERS are your best choice
1. CAREFUL LOAD HANDLING
2. MINIMIZED OPERATOR EFFORT
3. QUICK, EFFICIENT AND SAFE GLASS OR WINDOW LIFTING
Product types are:
- One-column lifters
- Two-column lifters
- Manipulators
- Accumulator lifters
- Special applications
- Window manufacturing
Read more: https://glaston.net/machine/easy-lifters/
Glaston Craneways and Slewing cranes
Individually integrated craneways and slewing cranes
Looking for an optimal addition to your glass-handling equipment?
Here are three reasons why crane ways and slewing cranes are your best choice
1. CUSTOMER-SPECIFIC X–Y LIGHTWEIGHT CRANEWAY DESIGN
2. MODULAR CONSTRUCTION SYSTEM
3. SLEWING CRANE AS A LOW-PRICE SOLUTION TO WORK IN A CIRCULAR AREA
Read more: https://glaston.net/machine/craneways-and-slewing-cranes/