First presented at GPD 2017
Abstract
The use of laminated safety glass in outdoor applications continues to increase, and as a result, questions about edge stability often arise. This is especially true where exposed edges are required to eliminate any sightline obstructions.
Although the vast majority of laminated glass will never experience any edge blemishes, sometimes it does happen. This paper will focus on the edge stability of PVB and ionoplast laminates and address the potential causes of blemishes.
Introduction
The role of glass in building construction has drastically changed in recent years. Laminated glass is now being used for safety, security, structural, and decorative components of buildings. With the increased application of laminated glass, as well as the recent code changes for balustrades in North America, laminated glass is being specified more and more for exposed edge applications.
Although the vast majority of exposed edge laminates will never experience issues, sometimes blemishes around the edges may occur. When these do appear, they can compromise the visual appeal of laminated glass.
There are a few reasons edge blemishes may appear, including the lamination process, compatibility with other building components, and the choice of the right interlayer for the application. This paper will focus on edge stability and discuss the potential causes of edge blemishes in laminated glass.
Background
What is edge stability of laminated glass? Edge stability is defined as the ability for the edges of laminated glass to resist discoloration, bubbling, delamination, or other blemishes over time when exposed to environmental conditions.
In addition to natural and accelerated weather via different test methods or regulations such as ANSI Z97.1, or ISO 12543-4, similar tests may be initiated to investigate the performance of the laminates in regards to specific installation conditions, such as high temperature, salt (fog) spray, or compatibility to sealants, grouts, and glass coatings.
Laminates with ionoplast interlayer have repeatedly performed well in edge stability testing. While laminates with traditional PVB have also performed well, they are more likely to experience edge blemishes. Although it may be difficult to determine the exact cause of the blemish after the fact, the potential reasons may be classified into two areas, the lamination process and the application conditions.
Lamination Process and Edge Defects The lamination process brings together heat and pressure, or vacuum, to remove the air and melt the interlayer between the lites of glass. Throughout the process, there are a few variables that play an important role in the edge stability of a laminate. These variables are adhesion of the interlayer to the glass, the quality of the glass, and edge seal.
Adhesion
The adhesion of the interlayer to the glass plays a major role in the edge stability of the finished laminate. As the adhesion level lowers, the likelihood for belmishes increases. During the lamination process, there are many factors that may affect the adhesion level.
The first factor is the cleanliness of the glass. When the glass arrives at the laminator, it can have cutting oil, release agents, dust, and other impurities on the surface. The glass must first be cleaned before lamination may begin. Modern glass washing machines are equipped with rotating brushes that clean the glass exceptionally well with only water.
Since the cleanliness of the glass surface and the quality of the water affect the adhesion of the interlayer to the glass, only demineralized water is recommended. The water should have a conductivity less than 20µS. Water from natural or municipal sources contains dissolved salts that impart hardness to the water. These salts are typically composed of Ca++, Mg++, Na+, and K+ ions.
The former two negatively affects adhesion even in low concentrations, while the latter two have a lesser but still measureable effect. The loss of adhesion, especially at the edge, may lead to edge bubbles or delamination Moisture content of the interlayer is the second key factor for adhesion.
PVB is hygroscopic, and its adhesion to glass is inversely related to its moisture content. It is produced with an optimum moisture content around 0.4%, and then the roll is hermetically sealed in a foil bag to prevent moisture absorption.
Once the foil packaging is open though, the PVB will start to absorb moisture from the air until an equilibrium is reached. To prevent this, any open rolls of PVB should be stored in an environment with a relative humidity between 25-30%. It is also recommended to replace the foil packaging and seal it, especially if the storage conditions are not adequate.
For ionoplast interlayer, it too absorbs moisture, but at a much slower rate. Because its optimum moisture content is lower than PVB though, it is recommended to always reseal the foil packaging, unless it is stored in the clean room below 10% relative humidity. The effects of either interlayer absorbing moisture is a reduction in the adhesion and potentially bubbles.
The adhesion between the interlayer and the glass is governed heavily by the ability of the polar groups from the interlayer to bond with the polar groups of the glass surface. Figure 1 depicts how good adhesion is formed through the hydrogen bonds between the polyalcohol groups of the PVB interlayer and the silanol groups of the glass.
In contrast, figure 2 shows how moisture content and ions from the wash water can reduce the adhesion by blocking the hydrogen bonds. Reduced adhesion at the edges may result in water ingress, blushing, bubbles, and or delamination.
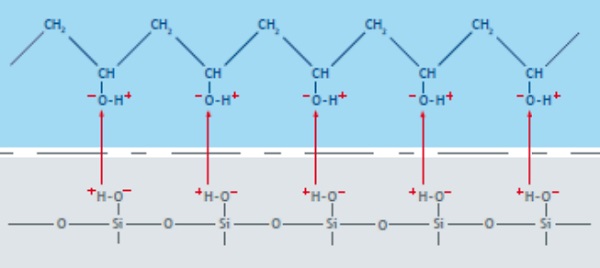
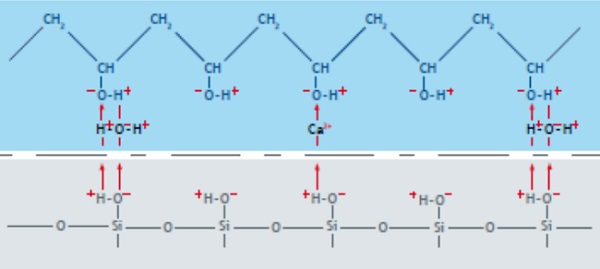
Quality of the Glass
Most of the glass used for lamination today is produced by the float process. Although standard float glass, also referred to as annealed glass, is of high quality and very flat, it not considered safety glass since it breaks into large, sharp, dangerous pieces.
The bending tensile strength of annealed glass is also relatively weak. To make it safer and stronger, the glass is subjected to a thermal strengthening process. The annealed glass is heated to approximately 600°C, and then cooled rapidly with jets of air.
The rate of cooling determines the degree of strengthening by locking the surface of the glass in a state of compression. The faster the cooling, the higher the compression, and the stronger and safer the glass becomes.
Fully tempered glass is cooled faster than heat-strengthened glass making it much stronger and giving it a smaller, safer break pattern. For lamination though, the potential issue with thermally strengthened glass is the inherent distortion imparted on it from the process. When the glass is heated that hot, it can start to deform and become wavy.
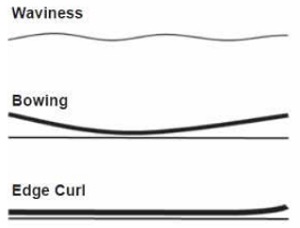
This distortion can result in an overall waviness, a general or local bow, or edge curl. Figure 3 depicts the typical distortions.
There has been a great improvement over the last few years with tempering furnaces, and some of the newer furnaces can produce exceptionally flat glass, but care must be taken to use the flattest glass possible for lamination.
Even the values specified in ASTM C1048 are not tight enough for lamination. A general rule is that the deviation of flatness should be below 10% of the interlayer thickness.
For a 0.76 mm interlayer, the maximum flatness deviation would be 0.076 mm. A deviation larger than this tolerance on the edge has the potential to develop bubbles or delaminate.
A laboratory study was initiated to determine the effect that edge curl has on the finished laminate. Two types of laminates were prepared using tempered glass with edge curl, see figure 4.
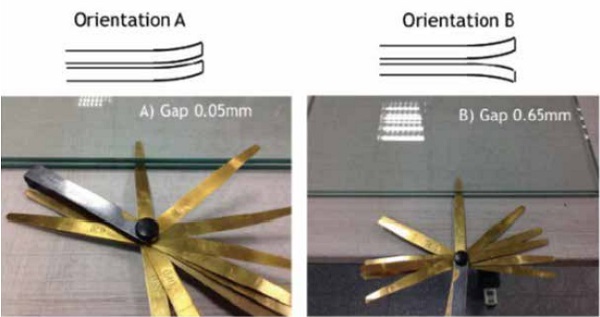
Orientation A matched the curls together so that they were nested, while orientation B placed the curls in opposite directions. The gap between the two lites of glass was measured and sample A had a gap of 0.05mm whereas sample B had a gap of 0.65mm.
The samples were then laminated using 0.76mm PVB and autoclaved together. After the autoclave, the samples were stored under high heat and humidity for several months at 85°C and 85% relative humidity. Samples with orientation A showed no visible blemishes, however, orientation B had numerous edge bubbles, see figure 5.
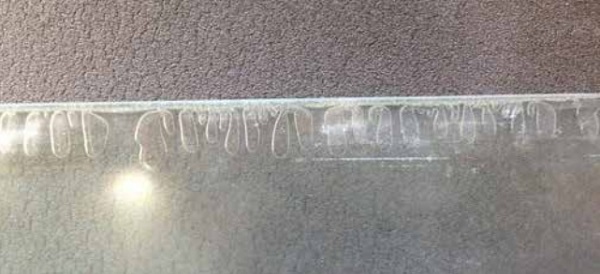
Edge Seal
The autoclaving process is the last step in the production of laminated glass. The conditions inside the autoclave allow for viscous flow of the interlayer resulting in an intimate contact with the glass. Any remaining air is dissolved and dispersed creating a clear laminate.
Once the laminates have been de-aired, they are placed on autoclave racks. There should be space between the laminates to allow channels for air flow to ensure even heating and cooling. The glass should be secured in position on the racks so there is very little movement during the autoclave cycle.
Excessive movement may lead to glass breakage. When securing the laminates, care must be taken to avoid excessive localized pressure. The localized pressure may lead to the interlayer extruding from the edges, creating a thinning of the interlayer at that point. This could lead to edge bubbles or delamination.
Once on the racks, the laminates should be placed as quickly as possible in the autoclave. Excessive delays could result in the edges beginning to separate, especially if the edge seal was not good. The autoclave is then heated to 135-145°C while pressurizing to 12-15 bars.
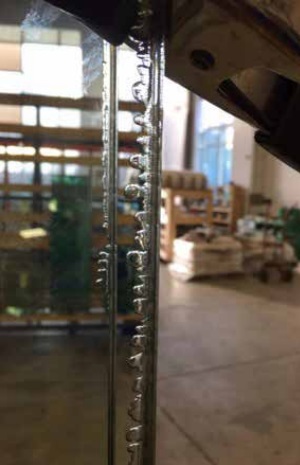
Once top heat and pressure is reached, it is held for at least 30 minutes, but the length of time is dependent on the glass thickness and load size. After the hold time is up, the glass is allowed to cool down while still under pressure.
The pressure should not be released until the interlayer/glass temperature is below 50°C, otherwise, small champagne or finger-like bubbles may start to appear, see figure 6.
Application Conditions and Edge Blemishes Besides the conditions of the laminating process, how and with what the laminate is installed with may potentially cause edge blemishes.
There are a variety of different ways to install laminated glass, while different, there are some basic precautions that should be followed for all installations. The first of which is contact with water.
Even with the best lamination conditions, laminated glass should not be allowed to sit in water for an extended period of time. For applications where the laminate has captured sides, weep holes or other ways for any accumulated water to drain should be included.
For exposed edge applications, drainage should be adequate enough as to not allow standing water to remain in contact with the laminate.
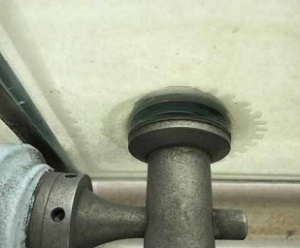
This is also true for point supported glass. If the point supports are not sealed properly, water can infiltrate the opening and may lead to delamination, as seen in figure 7.
In addition to water, any other chemical that may be in contact with the edge of the laminate should be tested for compatibility. This is especially relevant to sealants and grouts. Incompatibility of the sealant and grouts with the interlayer may result in edge bubbles, discoloration, or delamination.
There are a variety of sealants on market. While most are compatible with ionoplast laminates, PVB laminates may experience some minor edge blemishes. It is best to contact the sealant or interlayer manufacturer to determine compatibility.
As North America begins to move toward laminated glass for balustrades, and away from monolithic tempered glass, the topic of grouts has become increasingly popular. As discussed in the 2007 GPD paper “Outdoor glass baluster – new challenges,” cement-based grouts are not recommended for contact with laminated glass.
The last potential cause of edge blemishes is the environmental conditions where the laminate is installed and what interlayer is used. Is the laminate indoors, or outdoors? Is it in a dry environment, or a wet one? Is it close to an ocean? Is PVB used or ionoplast? Based upon these answers, different edge stability levels may be achieved.
For example, can ionomer laminates be installed in an open edge balustrade by the beach? To answer this question, salt spray testing was performed.
Salt Spray (Fog) Testing
Salt Spray (Fog) Test, is a standard corrosion test usually done on coated metal products in the architectural industry. However, it is starting to be requested for laminated glass railing applications in exposed edge conditions for coastal climates.
The testing is an accelerated weathering test based on ASTM B117 “Standard Practice for Operating Salt Spray (Fog) Apparatus.” The samples are exposed to 3,000 hours at 35°C while misted with a 5% NaCl water solution. The samples are removed and inspected at 500 hour increments and then returned to the chamber.
Four laminates were prepared with one being the control sample and three subjected to the weathering. The results were as predicted for the ionoplast laminates. After 3,000 hours, there were no visible edge defects noticed, figure 8.
Standard PVB however, began to experience a clouding of the edges around 1,000 hours, figure 9. In addition to standard PVB, our high adhesion grade PVB was also tested. As stated earlier, adhesion is a key factor in edge stability, and after 3,000 hours, the high adhesion PVB showed no signs of cloudiness or other edge defects, figure 10.
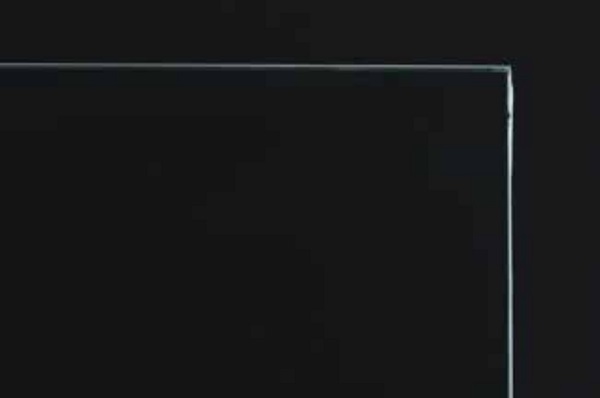
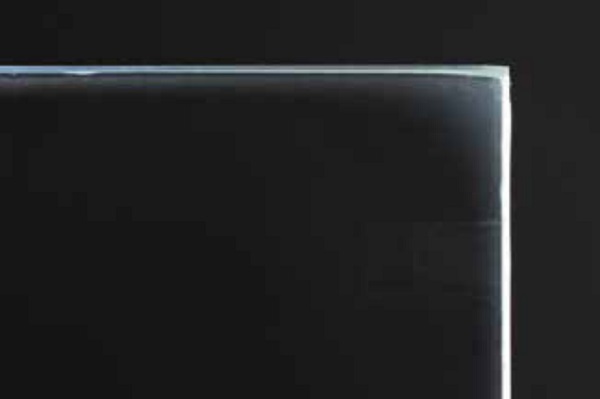
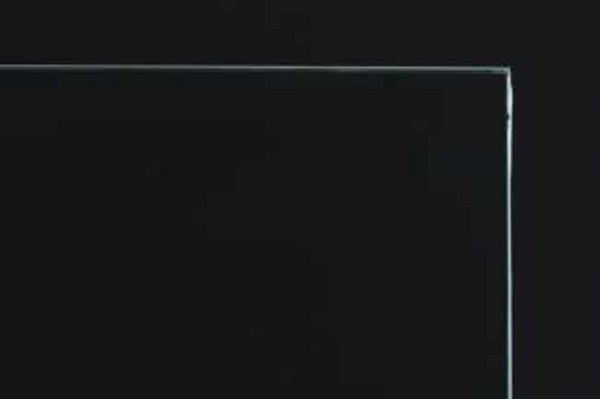
Conclusion
The use of laminated glass for exposed edge applications is increasing, and as such, so are the questions about edge stability. While the majority of laminates will never experience edge blemishes, it can sometimes happen.
Edge blemishes can be attributed to the lamination process, compatibility of materials, and choosing the right interlayer. When properly laminated and installed, the potential for edge blemishes decreases, leaving a clearer view.
References
[1] Kuraray Trosifol: Technical Manual, The Processing of PVB Film, Sixth edition, Kuraray Europe GmbH, 2012
[2] Keller, U. & Mortelmans, H.: Adhesion in Laminated Safety Glass – What mankes it work?, Conference Proceedings, Glass Performance Days, pp. 353-356, 1999.
[3] Kuraray Glass Laminating Solutions: SentryGlas® Ionoplast Interlayer Technical Manual For Structural Engineers, Kuraray, 2014
[4] Schmidt, M. & Nugent, W.: Outdoor Glass Baluster – New Challenges, Conference Proceedings, Glass Performance Days, pp. 206-209, 2007.
Comments
The use of laminated safety glass in outdoor applications continues to increase.