Source: Glass Structures & Engineering
Authors: Philippe Letocart & Francis Serruys
DOI: https://doi.org/10.1007/s40940-025-00292-5
Abstract
Spontaneous glass breakage of thermally toughened glass due to NiS inclusions can be largely prevented by a Heat Soak Test (HST). This well-established test has been incorporated into the European standard EN 14179-1:2005. However, according to literature (Yousfi et al., Verre 16(1):38–54, 2010b), there might be a theoretical probability, that a potentially dangerous inclusion could lead to a breakage after a well-conducted HST. Glass processors may neglect to conduct the test for a variety of reasons (sometimes furnaces are not calibrated, are overloaded, a wrong temperature profile is run etc.), even advising not to perform it at all, preferring to replace the glass should failure on a building occur. In this paper, we will show that, due to recent advances in microanalysis techniques, it is now possible to state after a failure on a building whether the heat soak test was correctly conducted according the EN standard or not.
1 Introduction
Spontaneous glass breakage due to nickel sulphide inclusions in the glass melt is a well-known phenomenon. A recognised process to avoid spontaneous glass breakages on a building is the Heat Soak Test (HST), which is described in the European standard EN14179-1:2005. In this test, the thermally toughened glass is maintained for 2 h at 290 ± 10 °C prior to its installation. It is a test which should lead to the breakage of glass panes with a critical NiS inclusion.
However, for several reasons, the heat soak test has not been universally adopted by the glass processors. Some of them even advise against performing it, claiming it adds approximatively 10% cost on the product and it is theoretically not filtering 100% of all NiS inclusions. Moreover, it is not visible on the final product. Other reasons are the fact that the HST is also breaking glass panes with defects which would not lead to a breakage on a building (like refractory stones, Ni9S8, etc.) and that if a glass pane breaks in the furnace, usually the 2 to 4 panes close to the defective one also break or are damaged.
There is a general concern in the marketplace that the test is not always well conducted by the glass processors: furnaces not calibrated, overloaded or even test not done at all. All these issues cannot be verified on the final product.
For these reasons, a control mechanism to check if the HST was correctly conducted according to the standard is needed and was the trigger of the present study.
In the context of the energy efficiency, and sustainability objectives, flat glass producers are starting to use more cullet from post-consumer recycled glass. However, customers suspect the cullet from post-consumer recycled glass could be an additional source of metallic inclusions, which are the root cause of nickel sulphide inclusions, see Kasper and Stadelmann (2002). Even if it is probably untrue, an efficient way to show whether a glass breakage is linked to a poorly performed HST rather than on contaminated raw materials is urgently need. This was one more motivation for this work.
Based on the centre fragments of a broken glass from a building, this paper shows that it is possible in most cases to state if the heat soak test was performed according to the EN standard or not.
A second motivation for the analysis of inclusions, in addition to spontaneous glass breakage, is to know if different chemical compositions, which were previously not noticed at all, could also potentially cause a delayed glass breakage. The question from the glass producer’s perspective is whether they should avoid other types of materials in the vicinity of the glass manufacturing and within the raw materials.
2 Background
The generation of nickel sulphide inclusions in the glass melt and its criticality for the stability of thermally toughened glass has been widely discussed in the literature [for example Kasper (2019)]. In summary the quenching process required to produce thermally toughened glass traps nickel sulphide inclusions into a high temperature hexagonal α-phase of NiS, which is not stable at room temperature. NiS is a reaction product of the glass melt with small metallic inclusions issued from the raw materials and cannot completely be avoided (Kasper et al. 2002). Because this α-phase is metastable, it transforms slowly into a stable rhombohedral β-phase, which leads to a 2.5% increase of its volume at ambient temperature. If this inclusion is in the tensile stress zone within the glass thickness, the thermally toughened glass can break spontaneously, sometimes after years or decades.
Generally spoken, a nickel sulphide inclusion is a chemical compound containing several phases and to explain its behaviour in the glass melt and later in the glass, we need to consider the Ni–S phase diagram (Fig. 1).
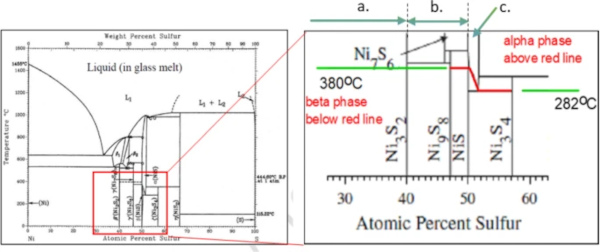
Simplifying, one can distinguish three main situations for the composition of a NiS inclusion in glass:
(a) Inclusions composed of Ni3S2 or (Ni3S2 + NiS): these do not cause spontaneous fracture, but also, they have never been identified in float glass due to its long dwell time in the glass tank.
(b) A compositional range from (at ambient temperature) Ni9S8 to NiS in random variable relation.
(c) So-called over-stoichiometric NiS(1+x) where the inclusion contains a sulphur excess slowing down the transformation speed considerably with increasing x (x being the sulphur excess).
Only NiS inclusions containing (at least partly) the 1:1 composition and those with a small sulphur excess are of interest, because this chemical compound is the only one to be subject to slow α to β phase transformation at ambient temperature.
To reduce the risk of spontaneous breakages on a building, the heat soak test (EN14179-1 standard), was introduced, and it is widely acknowledged that this test is effective in reducing the risk of a later spontaneous breakage. In this test, the thermally toughened glass is heated up to a temperature of 290 ± 10 °C for a period of 2 h. At this temperature, the phase transformation happens much faster, and potentially critical inclusions should break the glass, prior to its installation.
Anecdotal evidence suggests that there are a few theoretical cases where a NiS inclusion could have survived the heat soak test but would have resulted in a breakage later on a building.
These cases are:
- Over-stoichiometric NiSx with higher values of x and especially the case of x close to 1.047 even higher, close to its theoretical stability limit of 1.06, with the argument that the transformation speed is strongly reduced with increasing values of x and the heat soak test could have been too hot to allow a full phase transformation.
- High iron content cFe > 0.5% within the NiS matrix. Here also, the argumentation is that the transformation speed decreases rapidly with higher iron content.
- Other exotic elemental impurities, which are not well known and for which there is not much data available.
The goal of the present work is to demonstrate that all these theoretical possibilities can be shown by analysing the fragments of the inclusion after a breakage of a glass pane which is supposed to be heat soak tested according to the EN standard.
Consequently, if none of these theoretical possibilities can be verified by microanalysis, it can be stated with high certainty, that the heat soak test was not conducted according to the EN standard.
a. Stoichiometry influence.
Occurrence of over-stoichiometric inclusions:
- The probability that over-stochiometric NiSx inclusions (with x > 1) are generated in the glass melt and could trigger a glass breakage, has been discussed and summarised in detail by Kasper (2019). This paper shows that the mechanism for the formation of nickel sulphide inclusions in the glass melt can lead to a gradual enrichment of nickel with sulphur to form NiSx, with x starting from 0.89 (which corresponds to Ni9S8), to reach a theoretical value of 1.06 at which the inclusion is not stable anymore and decomposes spontaneously. The cause is the excessive vapor pressure, which increases exponentially with the proportion of sulphur.
- Assuming that each NiS inclusion is the result of a melt reaction with a metallic impurity of a different size (Kasper et al. 2002), the occurrence of stoichiometries is distributed according to following diagram (Fig. 2), which is originally based on papers by Laffitte (1956):

Hence, the occurrence of over-stoichiometric inclusions is much lower than those with stoichiometric and under-stoichiometric compositions.
Influence of the stoichiometry on the transformation. Yousfi et al. (2010b) studied the transformation speed as a function of the sulphur content, by analysing the properties of macroscopic compounds of nickel sulphide produced especially for the study. He showed that the transformation speed is strongly affected by the sulphur content, as well as iron content as seen on Fig. 3.
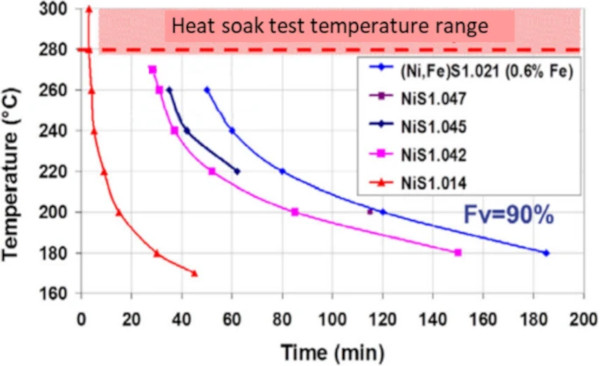
Hence, the temperature range of the heat soak test being close to the α to β phase change line (see Fig 1, area c.), could lead to the conclusion that the transformation kinetics may be not fast enough to break the glass however a slower transformation at room temperature could. This is especially the case for higher x values close to 1.06, where the α to β phase change line (Fig. 1) drops from 380 °C to 282°.
b. Similarly, higher iron content in the NiS matrix decreases the transformation kinetics, as described by Yousfi et al. (2010b). The argumentation is like that of the stoichiometry, as iron slows down the transformation kinetics.
c. Finally, exotic contaminants like bismuth, selenium, cobalt etc. within the NiS matrix could have similar effects on the transformation kinetics. However, it’s important to differentiate between impurities which dissolve within the NiS matrix to those forming a separate phase. As there is currently no data on these phase transformations, when such contaminants are found within the NiS matrix, no statement on the efficacy of the HST can be made.
3 Methodology
We have established that there are a few theoretical cases where a NiS inclusion could have survived the heat soak test but would have resulted in a breakage later on a building.
However, the microanalysis observation of the vast majority of inclusions, which led to a spontaneous glass breakage, reveals that the heat soak test was not performed according to the standard or even not performed at all.
Figure 4 shows the systematic procedure to analyse an inclusion in order to reach a conclusion on the HST.
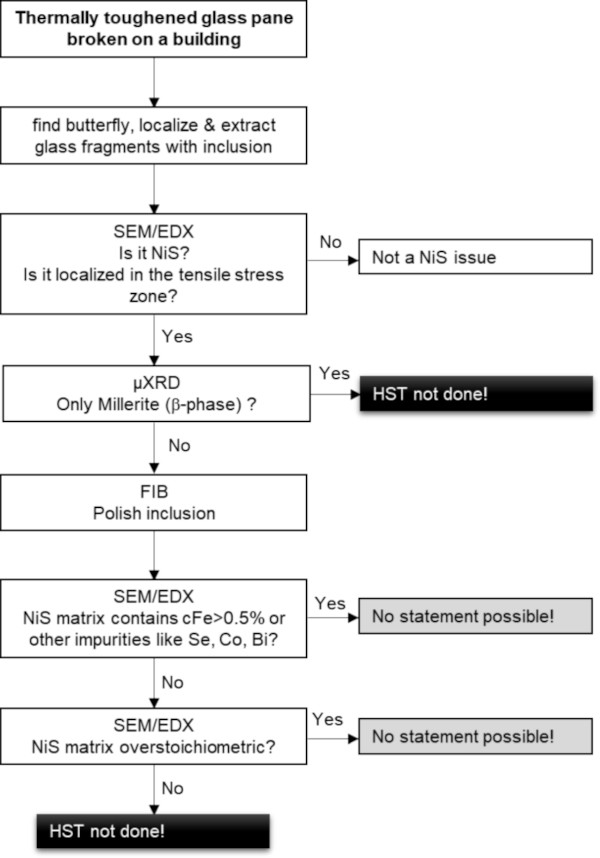
3.1 Step 1: Fracture analysis
The first step is the recovery of the glass breakage. The butterfly fragments are collected and observed by light microscopy (Fig. 5). The size of the inclusion as well as its position within the glass thickness is measured to check if the inclusion was in the tensile zone of the glass.
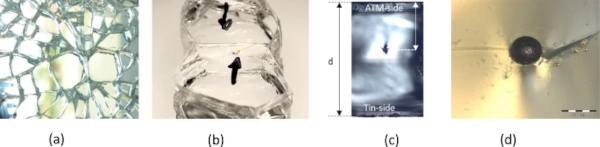
3.2 Step 2: SEM–EDX—inclusion size, composition and position in the glass and fracture analysis
The position of the inclusion, its size and the breakage pressure can be measured with the SEM (Fig. 6). Also, the element composition can be estimated from the sample.
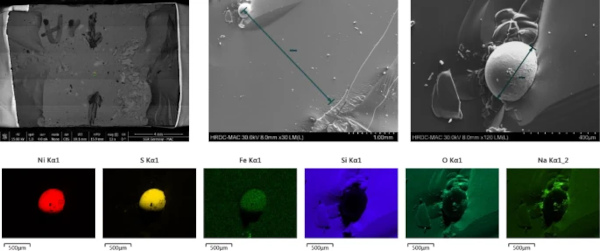
3.3 Step 3: X-rays microdiffraction (µXRD)
Modern X-ray diffraction analysis devices, with water cooled anodes, allow the direct analysis of NiS inclusions, without any further preparation. As the size of the inclusion is in the order of magnitude of the crystals within the inclusion, analysis with powder algorithms is possible, however only using a 2D-detector and integration of the signal over all possible crystallites' orientations. Figure 7 shows an example of such a generated diffractogram.
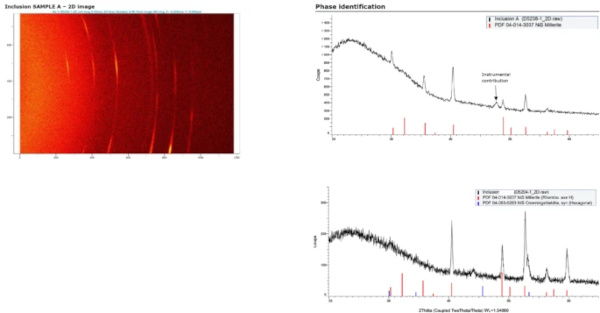
Where only millerite is present, it is possible to state at this stage, that the HST was not performed. NiS in 1:1 stoichiometry transforms very quickly and should have been completely transformed in the HST, leading to a breakage before being installed on a building.
3.4 Step 4: Sample polishing
The further analysis of an inclusion requires access to its interior structure, to allow SEM/EDX or EPMA analysis. The usual way to do this is to manually polish the inclusions (Kasper 2019). However, NiS has a higher expansion/contraction coefficient than the glass and so as the glass cools the NiS contracts leaving a gap around the inclusion. As a result, the inclusion does not stick to the glass fragment. This turns the manual polishing, even if it is conducted very carefully, into a lottery where the risk of losing the inclusion is over 50%.
The approach outlined in this paper is to polish the NiS inclusion with the help of a focused ion beam (FIB) machine, which is basically a SEM with a second column providing a focused gallium ion beam (a so-called dual-beam machine). This gallium beam can gently remove material and polish the inclusion until it reveals its interior structure. Figure 8 gives an example of such a polishing process.
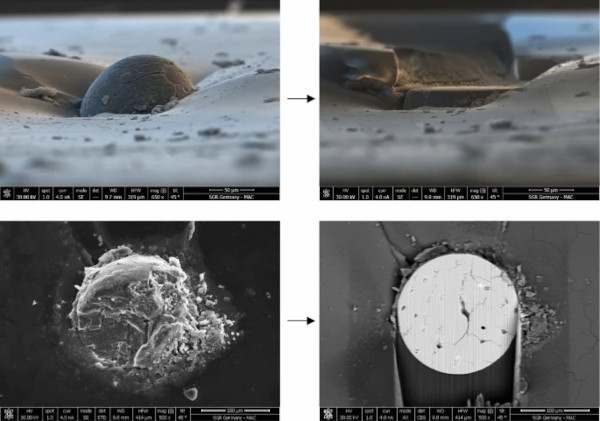
3.5 Step 5: SEM–EDX – iron localization and content, other impurities
Impurities such as iron are easily detected by a scanning electron microscope (SEM) in combination with an energy dispersive X-rays (EDX) system (Figs. 9 and 10) or by electron probe microanalysis (EPMA). Therefore, the possibilities b. (higher iron content) and c. (presence of other contaminants) can be excluded.
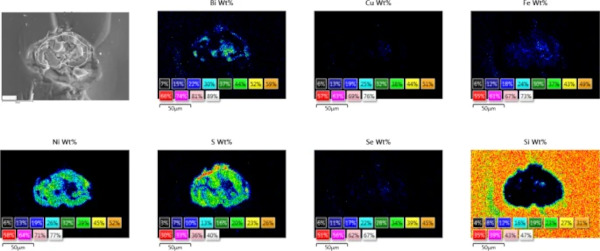
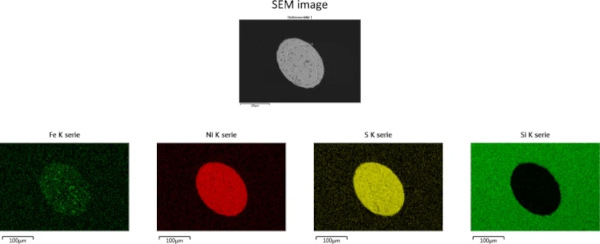
3.6 Step 6: SEM–EDX—NiS stoichiometry
When we undertake analysis of the stoichiometry, the precision of an EDX analysis is at its limit, but the electron probe microanalysis (EPMA) can provide good results (Yousfi et al. 2010a, b, c). It is always challenging to prepare the samples in an ideal way, considering that they are not always ideally flat and rarely clean. However, the stoichiometry of NiS has also a strong impact on its microstructure, as described by Yousfi et al. (2010a) and Kasper (2019). This means that a thorough observation of the microstructure can also lead to a clear statement on the sulfur proportion (see Figs. 11 and 12). The following specificities of the microstructure should be considered:
a. Globular or lamellar-eutectoid structure. According to Yousfi et al. (2010a, b, c), the transformation mechanisms change significantly with the sulphur content at the α-phase prior to the transformation. If the phase boundaries can be made visible (see next chapter), one can distinguish between two different microstructures after transformation depending on the stoichiometry:
- globular for near stoichiometric compositions and
- lamellar-eutectoid for over-stoichiometric compositions.
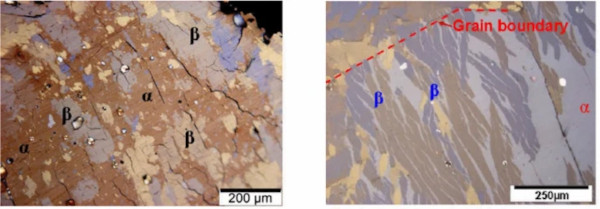
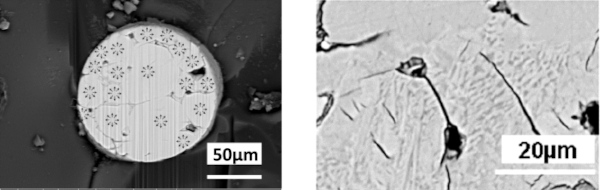
The different morphologies are governed by the transformation mechanisms which can be long range diffusion processes, massive transformation processes as well as the segregation of a Ni3S4 phase in the over-stoichiometric case.
In the case of near-stoichiometric compositions, the transformation occurs isotropically, starting at several positions simultaneously.
In the case of over-stoichiometric α-phase inclusions, according to Yousfi et al. (2010a) for an estimated stoichiometry starting at x = 1.02, the transformation implies a separation into a stoichiometric β-phase (millerite) and the segregation of Ni3S4 (polydymite). In this case a typical lamellar and lamellar-eutectoid morphology of the α and β phases forms.
b. Precipitation of Ni3S4 at the α to β phases interface. Because the β-phase of NiS is stoichiometric, the transformation of an over-stoichiometric α-phase implies the separation of the surplus sulphur, which occurs in the segregation of an Ni3S4 phase (Fig. 13). According to Yousfi et al. (2010a), this phase can be seen in SEM at the phase boundaries, see Fig. 6.
c. The observation of a foam-like structure for strongly over-stoichiometric inclusions (Fig. 14). The very high partial pressure of NiS at high over-stoichiometries leads, at glass melting temperatures, to gaseous decomposition products, mainly S2 according to Kasper (2019).
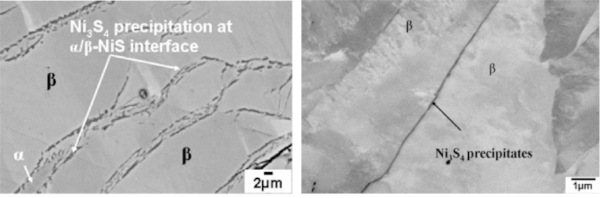
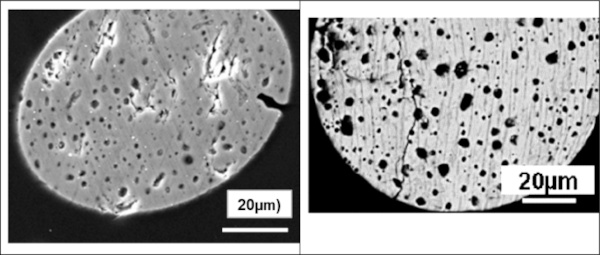
4 Conclusion
The question as to whether the heat soak test was conducted according to the EN standard is a question which arises often if a breakage occurs on a building. In most cases a statement is possible, and based on all inclusions analysed to date, we would conclude that the vast majority had not seen a well conducted HST. This would further lead to the conclusion that the HST, when properly conducted, is probably much safer than what it is thought to be. In fact, the over-stoichiometric inclusions with x > 1.047 do not transform and for 1 < x < 1.047 all inclusions break in the HST (Yousfi et al. 2010b). High Fe contents probably do not transform fast enough and are not an issue in the field.