Challenging Glass 6
Conference on Architectural and Structural Applications of Glass
Louter, Bos, Belis, Veer, Nijsse (Eds.), Delft University of Technology, May 2018.
Copyright © with the authors. All rights reserved.
ISBN 978-94-6366-044-0, https://doi.org/10.7480/cgc.6.2202
Author:
Jennifer Schneider | Kuraray America, Inc.
Engineers and designers are using glass in increasingly demanding applications such as stairs, floors, and bridges, large minimally supported facades and overhead glazing. The use of laminated glass in structural applications has become more recognized and preferred as safer choice to monolithic tempered or heat strengthen glass. Structural interlayers are stiff interlayers that increase the strength of the laminated glass enabling the glass structure to handle higher loads with thinner glass. The use of structural interlayers enables laminated glass use in the most demanding applications giving architects and engineers greater design freedom.
Today engineers and designers have options when choosing a structural interlayer for their application, Stiff PVB or ionoplast interlayer. Both interlayers provide improved post breakage strength and structural benefits; however, some significant differences in properties that affect the final laminate performance exist. Applications that require higher temperatures above 30⁰C and/or long load duration, ionoplast interlayers perform the best. When the load duration or design temperatures are lower stiff PVB isa good choice. From the laminators perspective properties such as yield and final laminate quality are important considerations as well.
There are differences between the structural interlayers seen during the lamination process that can influence lamination quality and yields. Stiff PVB process similar to standard PVB while standard ionoplast interlayers require some special processing. This may present a challenge for the laminators. Recent improvements in ionoplast interlayer technology now enable ionoplast to be laminated more similar to PVB giving laminators and engineers the best of both.
1.Introduction
The use of laminated glass is becoming more recognized as a safer alternative to monolithic glass due to its glass retention properties. When laminated glass breaks, the glass will remain in place providing protection from glass shards. While the glass retention provides some level of protection once the glass is broken, the post breakage strength is poor reducing its ability to withstand loads. Laminated annealed glass provides some residual post breakage strength however; laminated tempered glass is very poor.
Structural interlayers are stiff interlayers that provide a coupling effect with the glass, which increases the effective thickness of the laminate. This creates stronger laminates allowing the use of thinner glass or higher or longer load durations. Because Laminated glass with structural interlayer have much higher strength they can be used in more demanding glass applications such as minimally supported, floors, stairs, railings and very large glass panels. Structural interlayers have much improved post breakage performance when compared to standard interlayers. See Fig. 1 showing a comparison of structural interlayer vs standard PVB after breakage. The standard PVB does not have enough strength to support its weight and falls down while the structural interlayer remains upright. This greatly improves human safety.
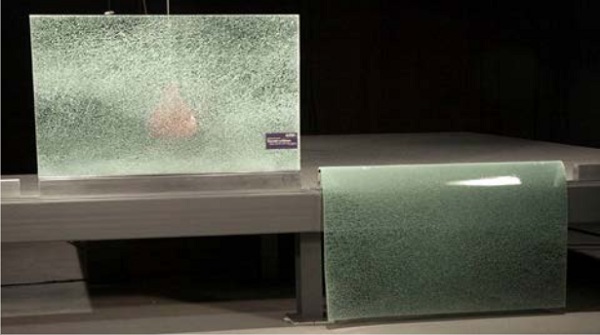
Today there are two types of structural interlayers, stiff PVB and Ionoplast interlayer. Stiff PVB are based on PVB chemistry with lower levels of plasticizer, which increases the modulus. Ionoplast contain no plastizers and are based on unique ionoplast chemistry. Both of these interlayers provide outstanding structural performance at room temperature and below however, as temperature rises the coupling effect of stiff PVB diminishes. Increasing temperature lowers modulus, which lowers the effective thickness. Fig. 2 shows the effect of temperature on effective thickness .The yellow line is 2 ply 5 mm glass with oil in the middle as a zero coupling control. The blue is monolithic 10 mm glass. The graph shows the stiff PVB and Ionoplast equivalent until just below 30 C.
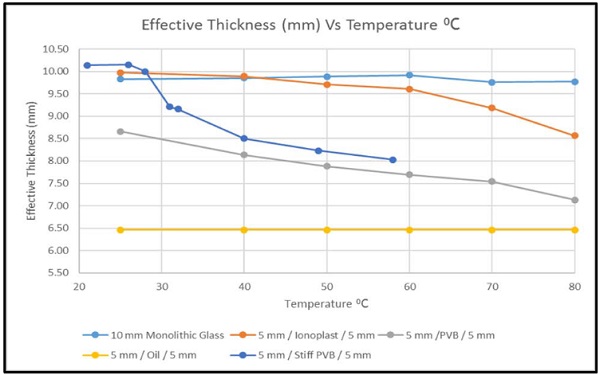
Both stiff PVB and Ionoplast lose modulus as temperature rises however stiff PVB has a more significant drop. See Table 1, which shows Young’s Modulus values for both Stiff PVB and Ionoplast at 30⁰c and 50⁰C.
Table 1: Young’s Modulus and Temperature
2.Post Breakage Performance Comparison
Laminated glass using structural interlayers provide substantial improvement in post breakage performance and safety as compared to standard laminated glass. Stiff PVB and Ionoplast behavior differently at higher temperatures, which can affect the post breakage strength of the laminate. Post breakage strength tests on point supported glass panels (1500 mm x 2000 mm) for a typical canopy application were conducted at University of Armed Forces in Munich, Germany. 9 panels with each of the 4 interlayers, Ionoplast (1.52 mm and 0.89 mm), Stiff PVB (1.52 mm) and standard PVB (1.52 mm) were tested at 3 different temperatures (-20⁰C, 21⁰C and 50⁰C).
The laminates were conditioned for 3 hours at each temperature then impacted by dropping a twin tyre impacted of 50 Kg from a height of 900mm. In all of the structures, this was not, adequate to break the glass, therefore the upper layer of glass was broken with a center punch. 100 Kg was loaded for 30 minutes. Additional 100 Kg was added with 15 minute time interval between each load. Max load used was 400 Kg.
At -20⁰C all interlayers sustained a 400 Kg load. At 21⁰ C both stiff PVB and Ionoplast could sustain a 400 Kg load. When temperature was raised to 50⁰C only the Ionoplast 1.52 mm could sustain 200 Kg load for more than 30 minutes. The Ionoplast at 0.89 mm sustained a 100Kg load form 30 minutes. Fig. 2 shows the performance at 21⁰C and Fig. 3 shows performance at 50⁰ C.
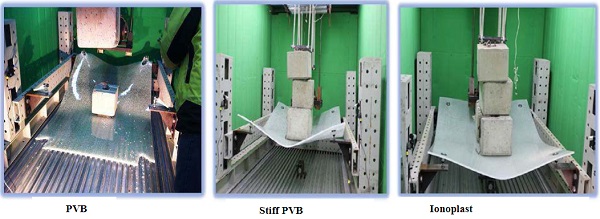
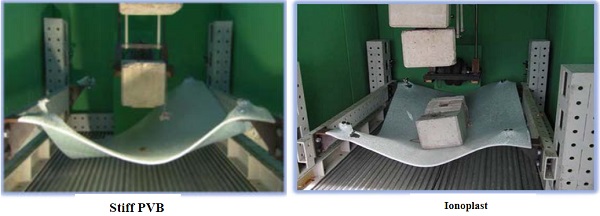
3.Edge Stability and open edge performance
The excellent post breakage properties of structural interlayers make them an ideal choice for use in minimallysupported glazing systems such as railings and fins. Glass is often chosen in a building construction because of its ability to create unobstructed views. Placing an end cap on a railing can negatively affect the view therefore leaving the edges open is more desired. A building owner sitting on their balcony with a glass railing would not want their beautiful view of the scenery to be blocked. In open edge applications, it is important that the edges do not degrade and become visually undesirable.
3.1Edge Stability Number (ESN)
The use of ESN is one way to quantify the edge stability of an open edge laminate. Laminates are exposed to natural weathering and the edges are inspected. A number is assigned based on a weighted system, which gives higher importance to progressively deeper defects ( bubbles or delamination). An ESN value of 0 means there are no defects such as delamination or bubbles. The maximum number assigned is 2500 and anything less than 500 is considered exceptional. Table 2 shows the ESN for standard PVB, Stiff PVB and Ionoplast after exposure in Florida. Standard PVB develops unacceptable edge appearance after 48 months while both Stiff PVB and Ionoplast are acceptable for open edge applications. It should be noted that lamination quality can effect these numbers and poor lamination may have worse ESN. The ESN is not a predictor of delamination beyond the edges of the laminate.
Table 2: ESN Comparison
3.2 Salt Spray
Testing Salt Spray testing is standard corrosion test done usually on metal products. There has been interest to understand how this Salt spray test effects the edge quality of open edge laminates. Typical Standard PVB, Stiff PVB and Ionoplast Interlayer were exposed to 3000 hours of salt spray per ASTM B117-11 Standard Practice for Operating Salt Spray (Fog) Apparatus. Fig. 4 shows the results. Ionoplast has the best edge performance followed by Stiff PVB. Unlike ESN the appearance of edge blush may be indicator of delamination beyond the edge. It should be noted that these results do not correlate to ESN.
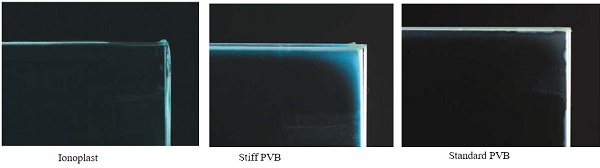
4.Lamination Process
Both stiff PVB and Ionoplast interlayers can be processed with standard glass laminating process and equipment. Stiff PVB processes very similar to standard PVB. Current Ionplast interlayers require some special considerations such as autoclave cooling rate and use of primer if laminating to the air side of glass. Autoclave cooling rate can affect the final laminate optical performance particularly in very thick laminates. Special attention is needed to ensure cooling rates are fast enough to prevent haze formation. This includes ensuring that there is proper air flow around laminates to eliminate any differential cooling rates.
Improvements have been made to the current Ionplast interlayers making laminate optics much less sensitive to cooling rate and acceptable adhesion when laminating to air side of the glass without the need for priming. This makes lamination of very thick multi ply laminates easier. Laminators no longer need to be as concerned about the effectiveness and uniformity of the cooling rate inside the autoclave. This next generation of Ionoplast materials allows laminators to have improved efficiency and quality while meeting the needs of their customers who specify an Ionplast interlayer. Because the laminate haze is less effected by cooling rate laminators may more densely stack the autoclaves for higher throughputs.
The below Fig. 5 shows haze formation of current Ionoplast and next generation Ionoplast. Interlayer caliper 3.2 mm with low iron 3 mm glass. You can see that the haze values are much lower vs current Ionoplast.
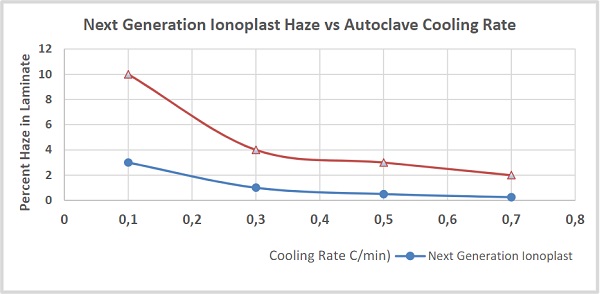
This new Ionoplast also provide better adhesion to the air side of the glass eliminating the need to use primers or to manage the glass orientation during the fabrication process. See below Fig. showing adhesion of air and tin side of the glass of current Ionoplast and new Ionoplast. New Ionplast has improved adhesion to both air and tin side of glass.
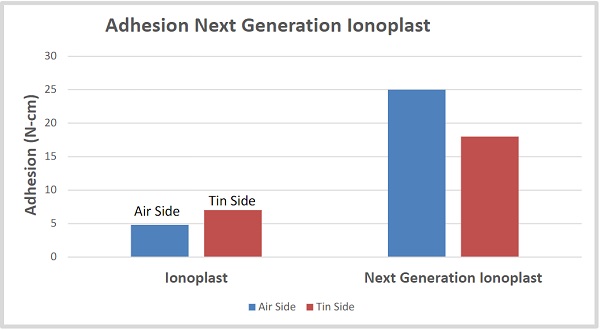
5.Conclusion
Today Engineers and Architects have many choices when it comes to interlayers for laminated glass systems. When designing a glazing system, performance requirements such as load duration, post breakage strength, open edge and use temperature need to be fully understood. Depending on the specific requirements, this will determine if a flexible interlayer or structural interlayer is required. Structural interlayers are a good choice when the glazing structure requires enough strength to handle higher loads with minimal deflection and/or if post breakage properties are important.
Some examples are minimally support systems, fins, railings, floors, stairs and overhead glazing. Use temperature needs to also be considered when deciding between Stiff PVB and Ionoplast. Ionoplast should be used in cases of higher temperature and longer load durations. While Stiff PVB are perfectly suitable when lower design temperatures are specified. If the applications will used in an open edge application particularly outdoors and/or in harsh environment such as near the ocean, then Ionoplast offers the best performance.
Next generation Ionoplast offers the laminator greater efficiency in achieving consistently high quality laminates. Laminators no longer need to be concerned about glass orientation as adhesion levels are acceptable regardless of air or tin side lamination. From an Architect or Designers view this gives them greater confidence in the final laminate will meet the optical requirements of the application.