Source: Glass Structures & Engineering
Authors: Julian Hänig, Alina Gutjahr, Paulina Bukieda & Michael Engelmann
DOI: https://doi.org/10.1007/s40940-024-00287-8
Abstract
The demand for versatile and visually appealing glazed structures has been increasing in recent years. To meet contemporary architectural needs, a wider range of functionalities is required, including smart, bendable and thin laminated glazing. In particular, cold poured liquid optically clear adhesives (LOCA) are gaining prominence as interlayers for complex curved cold bending and smart integration, where conventional interlayer films impose limitations. Furthermore, new applications for cold bending of thin glass with LOCA for complex free-form geometries are currently under development. This paper presents the investigation of three LOCA for application as interlayers in laminated glass. Within a comprehensive experimental study, essential material properties were investigated. The research focuses on the viscoelastic, tensile, and creep properties of the LOCA. Additionally, the study considers how the materials age under radiation, high temperature and high moisture in accordance with the product standard for laminated glass. All results are summarized to provide a wide-ranging data base for dimensioning laminated glass made with LOCA. The investigations proof a wide-ranging suitability for laminated glass. The mechanical properties of the LOCA are comparable to conventional interlayer films. Two materials behave medium stiff to stiff and one is more flexible. All LOCA provide ductility which makes them suitable for laminated safety glass applications. High performances paired with the autoclave-free processing LOCA drives for new fields of applications for architectural glazings.
1 Introduction
Laminated glass is a composite that consists of two or more glass panes with a polymeric interlayer material. It was firstly introduced in the automotive industry for windshields to protect the passengers in case of accidental glass breakage. The flexible polymeric interlayer prevents falling glass shards. This was adapted to the building industry to fulfil the safety requirements for glass structures in case of glass breakage. Nowadays, numerous different interlayer films are used for laminated glass in building industry applications. With the increasing demand for versatile and visually appealing glazed structures, a wide range of interlayer films is available to fulfil the individual requirements. They can be grouped into ethylene–vinyl acetate (EVA), polyvinyl butyral (PVB), thermoplastic polyurethane (TPU) and ionoplast (e.g. SentryGlas®) interlayers. These interlayers are processed under temperature and high pressure according to manufacturer’s lamination guides.
Besides interlayer films, liquid optical clear adhesive LOCA interlayers that are cold-poured are applied to produce laminated glass for decades (H.B. Fuller | Kömmerling 2020a; b). Besides, for building industry applications, these materials are used in the automotive, optics, media industry (e.g. LCD Screens) as well as for combining glass with polycarbonate for security and bullet proof glazings (Weimar et al. 2018). Their curing process of polymerization is introduced by light, heat, moisture, two-component curing or a combination, depending on the manufacturer and polymer composition. LOCA materials are gaining prominence for complex curved cold bending and sensitive applications such as stone lamination, photovoltaics and screens, where conventional interlayer films impose limitations. The limiting factor is mostly the high pressure and high temperature during the autoclave process. LOCA systems require limited heat and no pressure during curing. This offers alternative options for liquid lamination solutions and enables the lamination with sensitive components. Furthermore, these materials require only limited energy during curing and less equipment compared with conventional interlayer film processing. (Scherer et al. 2018; Scherer et al. 2021; Wittwer et al. 2013, 2016). LOCA materials are frequently used for laminated glass and there are approvals by building authorities for application as laminated safety glass with shear coupling effects for an efficient glass design (e.g. DIBt 2016).
Most interlayers for laminated glass have been extensively investigated for the application in the building industry. Hence, the mechanical properties of most common interlayer films are well known and extensively described in a wide range of material investigations. Based on the experimental results simple linear or complex nonlinear material models can be derived for analytical calculations and numerical simulations. (e.g. Andreozzi et al. 2014; Botz et al. 2019; Sobek et al. 2000; Hána et al. 2019; Schuster et al. 2018; Rühl 2017; Kuntsche 2015; Kothe 2013; Kraus 2019).
Likewise, the application of laminated glass made with LOCA in the building industry requires the knowledge of precise material characteristics. Mechanical properties such as stiffness, strength, ductility, temperature dependency and durability play a key role for the structural design. In addition, it is particularly important to know the materials glass transition temperature range to evaluate the thermal stability and describe the mechanical behaviour within the application temperature range. Thus, the behaviour of the materials at different temperatures that are relevant for architectural application as well as varying loading rates and significant ageing due to environmental influences need to be determined. The understanding of the ageing on the mechanical properties is required in façades with high exposure to changes in environmental conditions, radiation and moisture. As of yet, the overall mechanical and thermomechanical properties of the different LOCA materials and their properties after ageing are not investigated in scientific papers. To enhance the understanding of various LOCA and provide an engineering-proof data basis of mechanical parameters for glass designers, further research is required. Furthermore, the different material applications and their processing are often unknown and hence, need to be introduced.
This paper is based on a research project for cold bending of thin glass employing LOCA that is introduced in the beginning of the paper. This serves as a general motivation for the investigation of LOCA to drive for new laminated glass innovations. Afterwards, the manufacturing process and special features of LOCA in relation to processing, curing and modification are revealed. This is followed, by the introduction of three different LOCA for laminated glass solutions. The main part focuses on the developed experimental test program for the assessment of the thermophysical and mechanical properties. The investigations include the evaluation of viscoelastic, tensile, and creep properties at hand of material specimens. Additionally, the study addresses the material properties after artificial ageing in accordance with the test standard for laminated glass (DIN ISO EN 12543-4 2022). All test procedures are described, the results presented and summarised in a wide-ranging data set for glass designing. Based on a discussion of results their suitability for possible applications and new glass innovations are evaluated. Finally, an outlook for further research closes the paper.
2 Liquid optically clear adhesives for laminated glass
2.1 Research on cold bent thin glass with LOCA
Current research deals with the application of thin glass in architecture to gain lightweight glass design for façades. To achieve the desired stiffness bend configurations play a significant role. This motivates to develop a production technology for cold bent thin glass that can be used for lightweight and highly transparent free-form shaped façade glazings. The followed up concept deals with glass elements made by at least two preformed thin glass plies in a thickness of 0.5–2.0 mm with a LOCA as stiffening core that holds the bent shape. The geometric rigidity of cold bent thin glass paired with a structural interlayer core may lead to novel glass applications such as glazings for secondary skin façades, lightweight roof glazings and complex shaped glass designs.
One main objective within the research is the development of an innovative manufacturing technique for handling and cold forming of thin glass as well as maintaining the shape for processing into laminated glass with LOCA. Therefore, the thin glass needs to be temporarily fixed in the desired bending shape. High demands are placed on the optical quality (homogeneous surface, congruent geometry) as well as on the geometric customisability during manufacturing for the implementation of variable bending geometries. Hence, geometric variation, high precision in shaping and adaptability are required. Adaptive manufacturing up to 1.0 m × 2.0 m in glass size is aimed. Three different concepts for cold bending are currently investigated and evaluated regarding their suitability. The first concept considers cold bending by force and subsequent fixing of the thin glass layers in the desired shape (Fig. 1a). For highly complex multi-curved geometries, a concept of full embedment (Fig. 1b) as well as adaptive moulds (Fig. 1c) are investigated.

Another focus is the development of a novel curing process for the cold bent thin glass panes. The key innovations are the LOCA application between two pre-formed thin glass panes, the entire material distribution during filling as well as the homogeneous curing. In order to avoid optical defects and alterations in thickness, congruent geometric layering, a gentle LOCA filling and uniform hydrostatic pressure are important. Additionally, the pot time is adjusted to size and geometry in order to guarantee optical quality. Especially for large glazing and complex geometries the pot time and hence the viscosity during filling is of particular importance. Finally, the panels are tested for lightweight glazing applications. Detailed description of the research findings will be presented in upcoming publications. This paper focuses on the wide-ranging experimental research on the material behaviour in order to evaluate their suitability for cold bending of thin glass.
2.2 LOCA processing
Liquid optically clear adhesives (LOCA), also known as cast resins, are cold poured between two or more glazing materials using the so-called cast resin process (Fig. 2). In the first processing step, the glass panes are sealed with an edge seal made of butyl, double-sided adhesive tape or silicone. The seal defines the thickness of the interlayer. In the second step, the cavity is poured (either by gravity or pressure) with the LOCA. An inclined tilting table is used to fill the LOCA properly without causing air bubbles during filling. After filling the openings are sealed with an EVA hotmelt. The low viscosity (< 100 mPa·s) allows for uniform distribution in the cavity. To counteract volume shrinkage during polymerisation, the cavity must be poured with an increased volume of LOCA that is defined by the shrinkage of the LOCA (2–12%). The curing (step 3) is usually initiated with high-energy ultraviolet (UV) or visible (VIS) radiation for single-component systems and in the case of multi-component systems, by reaction between the components at room temperature. During curing, the temperature level in the laminated glass does not rise above 50 °C whereas conventional autoclave processes require more than 110 °C at high-pressure levels of 10–12 bar. After curing (step 4) the final glass element can be refined like conventional laminated glass and processed into insulating glass units.
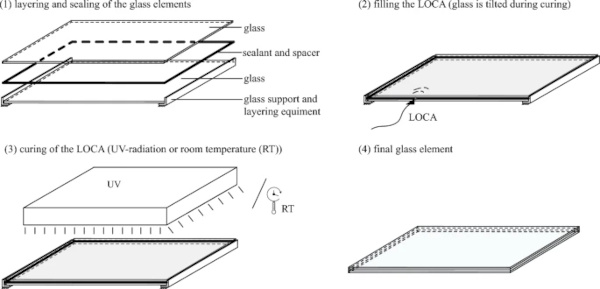
Figure 3 shows a sample production of a laminated glass with a LOCA interlayer. The material is poured into the intermediate cavity by a nozzle under pressure or by gravity with the required amount of LOCA until the air outlet is filled. During pouring the glass layout is tilted to avoid the formation of bubbles and force uniform distribution of material in the cavity.
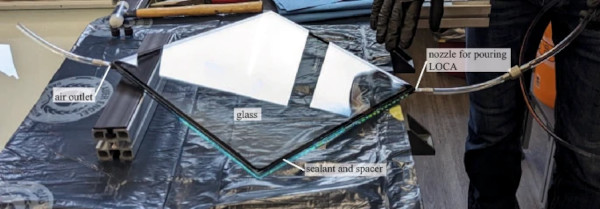
In general, the production using the cast resin process requires lower investment and operating costs compared with film processing in an autoclave that is very energy intense. Besides, the low temperature and non-pressurised process avoids damage to sensitive components such as electronics or thin integrated layers. The thickness, the LOCA properties and the curing process can be adjusted to the corresponding application of the laminated glass.
2.3 Materials
Three different commercial LOCA are examined and characterized in this study. These materials cover a wide range of material properties and curing parameters. Based on the polymer base two materials are categorised in two component polyurethane and one represents a UV-curing acrylate. The processing and material properties suits for a differentiated range of applications. Table 1 summarises the material base and representative properties provided by the manufacturer H.B. Fuller | Kömmerling.
Table 1 List of LOCA used for the study with representative properties from the technical data provided by the manufacturer (H.B. Fuller|Kömmerling 2018, 2020a, 2020b, 2022) - Full size table
K1 is a 2-component thermoplastic polyurethane with hard (thermoplastic) and softer cross-linked (elastomeric) shares. It cures by mixing of A and B components in a dosing system. The material cures at room temperature over time. The mixing of the components, the pot life, the thickness of the interlayer and the ambient temperature influences the curing time and the handling strength for further processing. The pot life can be modified according to the application and amounts to approximately 2–30 min. This directly affects the time till handling and overall curing time. Hence, increased output volumes in series production are feasible. The material is cured at room temperature but can be also speed up at elevated temperatures. This further increases production capabilities but requires energy during conditioning. High optical properties paired with high adhesion to a variety of materials (e.g. PC, PMMA, etc.) allow for wide ranging applications in automotive, aerospace and building industry. Latest developments deal with LED, display and smart film integration.
K2 as second 2-component thermoplastic polyurethane that is composed of a hard (thermoplastic) and softer cross-linked (elastomeric) shares, too. The material cures like K1 with an adjustable pot life between approximately 10–60 min. The material was developed for structural applications such as cold bending and stiff composite load-bearing behaviour (DIBt 2016). Latest research papers investigated the structural performance of thin glass composites (Hänig 2023) and of liquid embedded steel connections (Volakos et al. 2021, 2023) in laminated glass. The research shows that K2 is able to transfer significant loads uniformly into the glass layers. Prior reaching the ultimate load-bearing capacity large plastic deformations occur. Hence, structural performance is paired with a robust engineering design.
K3 is an acrylate that cures under UV-radiation. The polymeric structure is cross-linked. For curing, a uniform UV-radiation for at least 20 min is required. This is crucial for homogeneous polymerization and good optical properties in the laminated glass. The quick curing time, when compared to 2-component systems, allows for fast processing that makes it highly suitable for serial production. The required uniform curing limits the layer thickness to 4.0 mm.
The light transmission of the three examined LOCA materials (Fig. 4) within the visible spectrum (380–780 nm) is in the range or slightly exceeds the transmission rate of conventional laminated glass made with a standard-PVB. Within the UV spectrum (< 380 nm) a higher transmission is registered. In summary, increased transmission rates are attained when comparing to conventional standard-PVB.
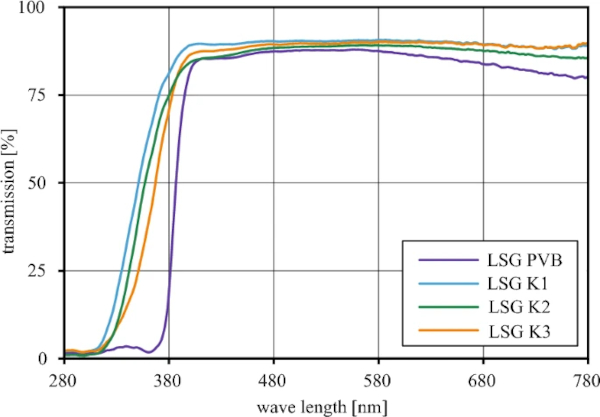
3 Experimental investigation
3.1 Overview—study approach
The objective of the experimental study is the evaluation of thermophysical and mechanical properties for designing laminated glass with LOCA. All examined materials are cured according to the manufacturing guidelines under controlled environment at laboratory conditions (+ 23 °C|50% RH). This ensured consistent curing of all test samples.
The experimental test program (Fig. 5) includes a dynamic mechanical thermal analysis (DMTA) to describe the general thermophysical properties. Further uniaxial tensile tests assess the mechanical properties. Different temperature levels are included to cover the relevant temperature range of the building industry. To provide information on the long-term stability, artificially aged samples are tested. The long-term viscoelastic behaviour is investigated in uniaxial creep tests. This represents a full valued database for the subsequent discussion, a comparison to conventional interlayers and the structural design of laminated glass.
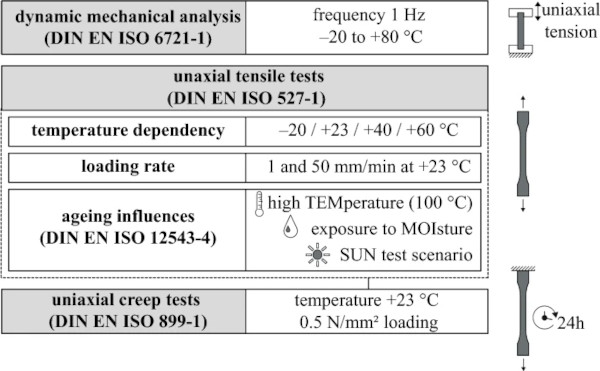
3.2 Dynamic mechanical thermal analysis
For initial assessment of the material behaviour dependent on temperature the viscoelastic and thermodynamic properties are evaluated by Dynamic mechanical thermal analysis (DIN EN ISO 6721-1 2019a; b). The materials are tested as a function of temperature (− 20 °C to + 80 °C) at a stress frequency of 1 Hz. Based on the results, the glass transition temperature ranges are evaluated to define the transition from a glassy, energy-elastic state to a rubbery, entropy-elastic state.
3.3 Uniaxial tensile tests
The uniaxial, quasi-static tensile tests (DIN EN ISO 527-2 2012) evaluate the in-plane stress–strain behaviour, the stiffness and the failure behaviour of the different LOCA. The mechanical properties are examined with a strain-rate of 1 mm/min that increases to 50 mm/min after exceeding the linear-elastic range. These tests are examined at a temperature of + 23 °C. The dependence of the mechanical properties on temperatures is conducted at – 20, + 40 and + 60 °C. Aged samples are tested to evaluate the long-term stability. The ageing comprises three different ageing scenarios in accordance with the durability criteria for laminated glass (DIN EN ISO 12543-3 2022a, b, c): exposure to high temperature, exposure to high moisture and exposure to sun radiation (Table 2). One has to keep in mind, that the interlayer material is normally not exposed to moisture in this amount as the LOCA is enclosed between the glass panes with a moisture border along the edges. Likewise, radiation testing is more intense compared to a laminated glass, as the cover glass absorbs radiation, especially at lower wave length.
Table 2 Representation of the artificial aging of the test specimens according to (DIN EN ISO 12543-4 2022) - Full size table
3.4 Uniaxial creep tests
Polymers show a viscoelastic material behaviour and tend to creep under long-term loading. For thermoplastic materials, this behaviour is accelerated by faster entanglement of the polymer chains. To investigate the time dependent stiffness of the interlayer, uniaxial creep tests (DIN EN ISO 899-1 2018a, 2018b) over 24 h at room temperature (+ 23 °C) are conducted. In order to investigate the creep at small strains occurring at intact state in laminated glass, a load level of 0.5 N/mm2 is chosen. This represents the estimated service condition for laminated glass under conventional bending load and allows for comparison to existing results. This represents the reference within this research and allows for a comparison to further research.
3.5 Dynamic mechanical thermal analysis
3.5.1 Test method
In the analysis (machine construction: Fig. 6) a dynamic sinusoidal, alternating tensile load is applied at a fixed frequency of 1 Hz and runs through a temperature range of – 20 °C to + 80 °C (1 K/min heating rate). This covers the building industry temperature range. The test specimens are cut to size from a 1 mm thick plate material that is cured between two PET sheets. Based on the resulting sinusoidal deformation, the storage modulus E' and the loss factor tan δ are determined (DIN EN ISO 6721-1 2019a; b, c). The glass transition is determined by the onset storage modulus curve (onset E') and the peak of loss factor (peak tan δ) according to (ASTM D4065-20 2020; ASTM E1640-18 2018).
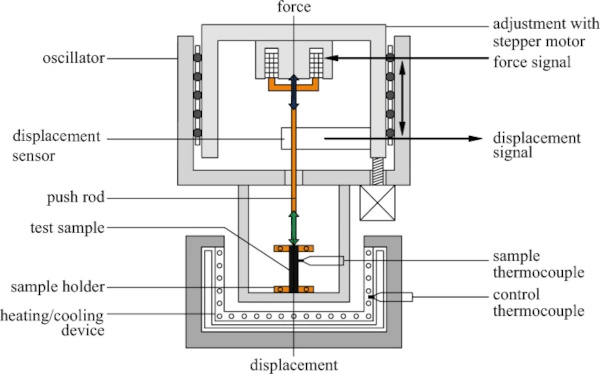
3.5.2 Thermomechanical properties
Figure 7 shows the thermograms for all the samples each material as a function of temperature. The solid line represents the storage modulus E' and the dashed line indicates the loss factor tan δ. Curves for the individual specimens are shown. At least three specimens are analysed for each material. The highlighted areas indicate the glass transition temperature range of each material based on the mean value of the test series.
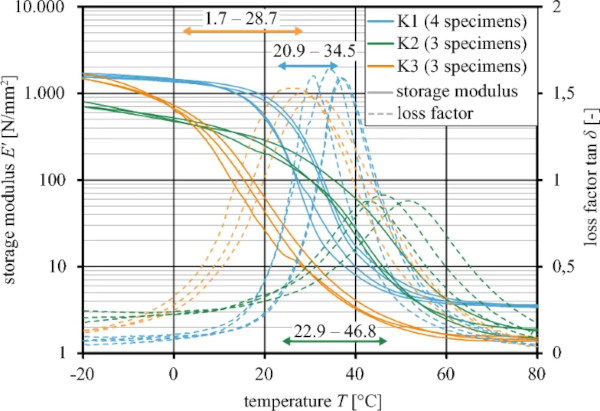
K1 demonstrates the highest storage modulus and hence indicates highest stiffness of the three materials. The glass transition ranges from + 20.9 °C (onset E') to + 34.5 °C (peak tan δ) with a steep drop of the storage modulus. At + 50 °C still a significant storage modulus of approximately 5 N/mm2 is recognised that decreases to approximately 3.5 N/mm2 at + 80 °C. This can be returned to the cross-linking of the polyurethane with thermoplastic and elastic components in the polymeric structure. Already low Young’s Moduli of > 1 N/mm2 allow for significant shear coupling effects in laminated glass occur (Kuntsche et al. 2019). Hence, even at elevated temperatures a structural load-bearing participation is to be expected at hand of the gained data.
The softening of K2 begins at a temperature of + 22.9 °C (onset E') and ends at + 46.8 °C (peak tan δ). This represents a widespread softening range of the thermoplastic polymeric components in the molecular structure. The stiffness above the glass transition temperature range approaches the limit in storage modulus of appx. 2 N/mm2. This indicates the remaining elastic stiffness at elevated temperatures.
Overall, K3 offers the lowest storage modulus. The softening range begins already at + 1.17 °C (onset E') and ends at + 28.7 °C (peak tan δ). At room temperature, the storage modulus already dropped below 20 N/mm2. Above the glass transition, only a very low storage modulus is remaining. In total, the UV-curing acrylate shows significantly lower stiffness compared to the other two LOCA.
3.6 Uniaxial tensile tests
3.6.1 Test method
A tensile test machine (Fig. 8) Instron UPM 5881 in combination with an optical extensometer measures contactless nominal (engineering) axial and transversal strains using high contrast measuring points on the specimens (white marks on black painted specimens). The machine is equipped with an integrated load cell, a climate chamber and feedback temperature control during testing.
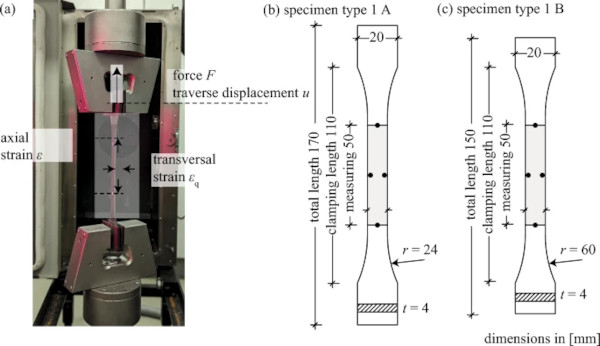
The tests are conducted according to (DIN EN ISO 527-2 2019a; b, c) with a loading rate of 1 mm/min in linear elastic range. To limit the duration of the test, after approximately 7.5% axial strain the loading rate is raised to 50 mm/min until breakage. Hence, the ultimate strength and strain are addressed at a loading rate of 50 mm/min. The reference test specimens are tested at normal climate conditions of + 23 °C and 50% RH (DIN EN ISO 291 2008). The temperature test series are tested at the individual temperature level without humidity control. Aged test series undergo the artificial ageing scenarios and are subsequently tested at normal climate conditions. All samples are preconditioned at the specific temperature for at least 24 h in a climate chamber.
The test samples are produced in a thickness of 4 mm and differ in geometry due to their production. Specimens that were moulded through injection are produced in geometry type 1A and mechanically cut samples are produced in type 1B. This allows for a further assessment of the influence of material processing on the mechanical properties. The equivalent nominal area (40 mm2) and clamping length (110 mm) allow for consistent comparison of mechanical properties. However, the strength can be affected by manufacturing method, as mechanical processing may induce minimal edge defects. These may lead to an early failure. Each test series consisted of minimum three (aged series) or five (all other series) test specimens. The nominal stress σ—strain ε behaviour, tensile Young’s modulus Et, tensile strength σu and ultimate strain at break εu are characterised in accordance with (DIN EN ISO 527–2, 2019).
3.7 Reference stress–strain behaviour
The reference stress–strain behaviour of the three materials is presented up to an axial strain of 5% (Fig. 9a) and until ultimate strain (Fig. 9b). Individual tests are marked in light colour whereas the mean value is highlighted in bold. The grey area indicates the linear elastic range for the determination of the Young’s modulus between ε = 0.05 to 0.25%. The reference tests are carried out on type 1 B specimens.
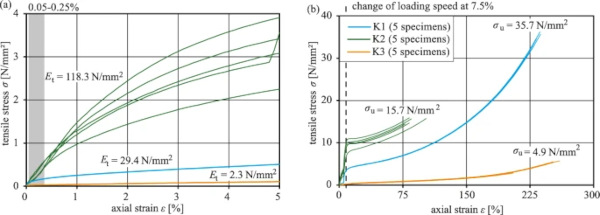
K1 exhibits a mainly elastic stress–strain behaviour with an initial high stiffness (Et = 29.4 N/mm2). After reaching the stress of approximately 4.5 N/mm2, the material exhibits reduced stiffness up until the ultimate strength (σu = 35.7 N/mm2) at a high ultimate strain of 237.2%. The material can be categorised into curve type d according to (DIN EN ISO 10350-1 2018a; b) representing an elastic material behaviour without yield point. K1 offers a high initial but reduced stiffness at increased stresses. This stress–strain behaviour is returned to the entanglement of the relatively stiff thermoplastic polymeric chains and the entanglement paired with the righty of the softer elastomeric polymeric chains in the molecular structure. This is characteristic for polyurethane with hard (thermoplastic) and softer cross-linked (elastomeric) shares.
K2 offers a high initial stiffness of Et=118.3 N/mm2. The material shows a similar stress strain behaviour than K1 with a reduction in stiffness at about 11 N/mm2. The material is also categorised into curve type d according to (DIN EN ISO 10350-1 2018a; b). The ultimate failure occurs at a stress of 15.7 N/mm2 and ultimate strain of 102.1%.
K3, shows a very linear stress strain behaviour and breaks at a relatively low tensile strength of 4.9 N/mm2 at however, a high ultimate strain of 245.2%. The Young’s modulus amounts to 2.3 N/mm2. The material is categorised into elastic material behaviour (curve type e) according to (DIN EN ISO 10350-1 2018a; b). In total, both PU show a relatively stiff behaviour at a different overall strength. The acrylate differs and behaves very flexible at the highest ultimate strain.
3.7.1 Temperature dependency
Figure 10 displays the stress–strain behaviour for all materials at different temperatures. Additionally, the mean values and standard deviation within the test series of the mechanical properties (Et, σu, εu) are summarised in Fig. 11. Figure 11 each temperature is marked by a different colour. The temperature test series consist of type 1 B specimens.
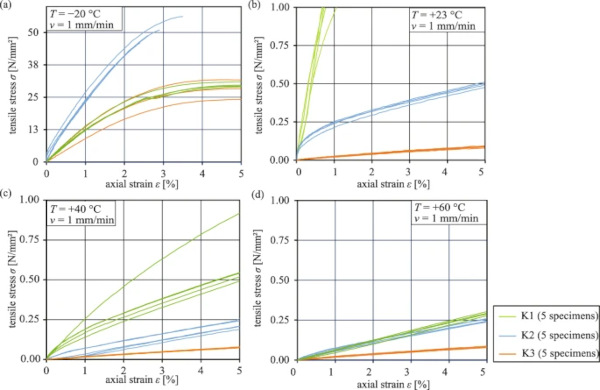
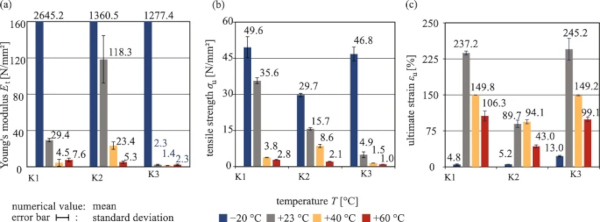
At lower temperature (–20 °C) K1 significantly increases its initial stiffness at a reduced ultimate strain of 4.8%. At increased temperature, thermoplastic polymeric chains soften significantly leading to lower stiffness. All in all, the Young’s modulus decreases from 2645.2 N/mm2 (–20 °C) to 4.5 N/mm2 (+ 40 °C), with a small increase to + 60 °C. This proofs that the glass transition range is already transcended at room temperature and no further significant softening occurs at higher tempereature. However, over the full temperature range high ultimate strains of minimum 106.3% are reached. The tensile strengths lowers from 49.6 N/mm2 at –20 °C to 2.8 N/mm2 at + 60 °C. Within the building industry relevant temperatures typical thermoplastic material behaviour is observed—significant temperature dependent material properties altering from very striff to very soft material behaviour. Overall, the high ultimate strains indicate significant ductility of the material at application temperature range.
K2 softens significantly at increasing temperatures, too. However, at lower level. At – 20 °C the material shows a high stiffness (Et = 1360.5 N/mm2) at a reduced ultimate strain of 5.2°%. However, even at + 40 °C the material provides a representative Young’s modulus of 23.4 N/mm2 that reduces to 5.2 N/mm2 at + 60 °C. The tensile strengths decrease from 29.7 N/mm2 at – 20 °C to 2.1 N/mm2 at + 60 °C. The ultimate strain stays on a similar level at the temperatures of + 23 °C (89.7%) and + 40 C (94.0%). Only at higher temperature, the ultimate strain decreases. K2 shows significant temperature dependency within the temperature range relevant to building industry. This can be returned to a pronounced influence of the thermoplastic components in the polymeric structure that entangle faster at rising temperature.
K3 offers a stiff behaviour at lower temperature (Et = 1277.4 N/mm2). The ultimate strain is significantly reduced to 22.4%. At elevated temperature, the material softens significantly. The Young’s modulus is 2.3 N/mm2 (+ 23 and + 60 °C) and 1.4 N/mm2 (+ 40 °C) while the ultimate strain reduces from 245.2% (+ 23 °C) to 99.1% (+ 60 °C). The tensile strength lowers in a high range 46.8 N/ mm2 (– 20 °C) to 0.9 N/ mm2 (+ 60 °C). The investigated properties are very typical for a thermoplastic polymeric material.
3.7.2 Ageing influences
The influence of ageing on the mechanical properties describes the resistance of the materials to environmental influences. The tests are carried out on different test sample geometries. Mechanically processed specimens (type 1 B) are used for K1 and K3, as in the reference test. K2 test series consist of moulded specimen (type 1 A). Hence, for better comparison, additional tensile tests were carried with K2 specimen of type 1A at reference conditions. Figure 12 shows the mean values of the individual test series with the respective standard deviations. The aged series are marked with individual colours. The initial, unaged mechanical properties are indicated for appropriate assessment.
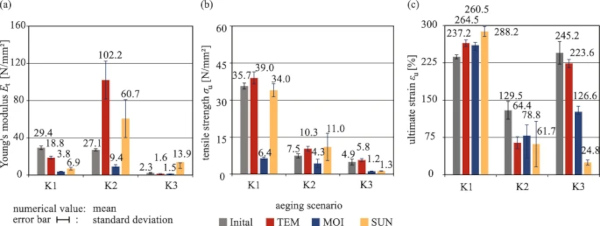
All ageing scenarios cause a decrease of the stiffness for K1. The Young’s modulus lowers from 29.4 N/mm2 (Initial) to 3.8 N/mm2 (MOI). The ageing scenario MOI also affects the tensile strength significantly with a decrease of 82% to 6.4 N/mm2, whereas the strength after TEM and SUN stays on the reference level. The resulted ultimate strain values are on a similar or even higher level. The results characterise an influence of moisture over time, which is typical for polymers. However, no moisture contents were detected during the tests.
Ageing at high temperature (TEM) as well as radiation (SUN) cause an increase of stiffness for K2 from 27.1 N/mm2 (Initial) to 102.1 N/mm2 (TEM) and 60.7 N/mm2 (SUN). The tensile strength increases to 10.3 N/mm2 (TEM) and 11.0 N/mm2 (SUN), while the ultimate strain decreases from 129.5% (Initial) to 64.4% (TEM) and 61.7% (SUN). This indicates a slight embrittlement of the material for these two ageing scenarios. The moisture ageing (MOI) causes, similar to K1, a significant decrease in stiffness (9.4 N/mm2) and strength (σu = 4.33 N/mm2; εu = 78.8%).
Aging at high temperature influences the properties of K3 insignificantly. Moisture causes a decrease of all mechanical properties (Et = 1.5 N/mm2, σu = 1.2 N/mm2, εu = 126.6%), indicating high susceptibility to moisture. Radiation (SUN) leads to an embrittlement. The Young’s Modulus increases from 2.3 N/mm2 (Initial) to 13.9 N/mm2 (SUN), whereas the tensile strength and ultimate strain decrease (σu = 1.3 N/mm2 and εu = 24.8%).
3.8 Uniaxial creep tests
3.8.1 Test method
Two mechanically processed specimens of type 1 B geometry (DIN EN ISO 527-2 2012) are tested per material in the uniaxial test rig (Fig. 8). The initial loading speed is set to 4 N/s until the stress level of 0.5 N/mm2 is reached. All tests are conducted at normal climate conditions of + 23 °C and 50% RH (DIN EN ISO 291 2008). The axial strains are contactless recorded over a 24-h period using optical extensometers at a measurement frequency that complies with the standard (DIN EN ISO 899-1 2018).
3.8.2 Creep behaviour
The results of the creep tests are evaluated as axial strain ε and creep modulus Ec over time. The permanent load of 0.5 N/mm2 is reached after approximately 5 s. In the evaluation, the initial deformation εc (t = 5 s) is subtracted from the measured strain to be in alignment with the short-term results. As a substitute, the initial strain ε0 is derived from the Young's modulus of the uniaxial tensile tests leading to the corrected strain values εc,corr (Eq. 1).
Figure 13 shows the results with specified properties at decades and after 24 h. The curves of all test specimens in each test series are in very good alignment. Hence, the results are considered to be reliable.
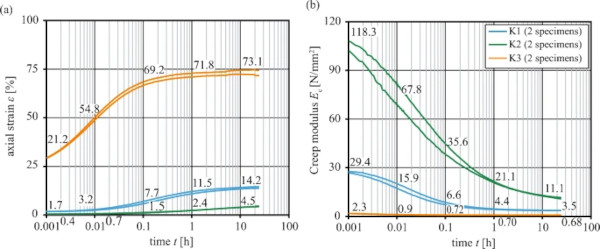
K1 reaches a strain after 24 h of 14.2%. The creep modulus lowers from 29.4 N/mm2 (0 s) to 4.4 N/mm2 (1 h) and a residual stiffness Ec,24 h = 3.5 N/mm2 after 24 h is determined. Within the first minute, the creep modulus lowers from 29.4 to 15.9 N/mm2, within the first ten minutes to 6.6 N/mm2.
The creep modulus of K2 lowers constantly. It starts at 118.3 N/mm2 and ends with a residual stiffness of Ec,24 h = 11.1 N/mm2. The strain reaches a value of 4.5%.
The creep modulus of K3 lowers from 2.3 N/mm2 (0 s) to 0.68 N/mm2 (24 h). The strain increases to a maximum of 73.1%.
3.8.3 Summary of mechanical properties
The mechanical single-point characteristics (Et, σu, εu) are summarised in Tables 3 and 4. Each table shows the mean values with standard deviation for each material and test series. The initial values, which were obtained from the unaged tests conducted at room temperature (+ 23 °C) are used as references. These values are crucial for establishing a percentage ratio to understand the change throughout the test series. Values below 100% indicate a decrease, while values above 100% indicate an increase of the mechanical property.
Table 3 Mechanical properties at different temperatures obtained by uniaxial tensile tests: mean value | standard deviation (ratio: value/ reference value). The tests are performed by a loading rate of 1 and 50 mm/min - Full size table
Table 4 Mechanical properties after ageing obtained by uniaxial tensile tests: mean value|standard deviation (ratio: value/ reference value). The tests are performed by a loading rate of 1 and 50 mm/min - Full size table
Table 4 presents the mean values of the mechanical properties and the relative changes compared to unaged test series. It is important to note that the test specimens for the materials K1 and K3 consist of cut material (type 1 B), while the test specimens for K2 are cast in a mould (type 1 A). The corresponding initial values represent the reference.
Table 5 summarises the time dependent Creep moduli for 1 h and 24 h.
Table 5 Creep modulus obtained at room temperature at a stress level of 0.5 N/mm2 Full size table
4 Discussion
4.1 Experimental results
For characterizing the mechanical behaviour of the different LOCA, the most material parameters relevant for design are derived in the presented experimental study. The DMTA reveals that all three materials have the glass transition within the building industry’s relevant temperature range. This is similar to conventional interlayer films, where the glass transition is transcended at elevated temperatures (Table 6). The 2-component polyurethanes K1 and K2 soften at temperatures above room temperature. Due to their stiff thermoplastic shares in the polymeric structure, significant stiffness up to room temperature is evident. At elevated temperatures softening leads to lower structural performance. K3 softens at temperatures close to 0 °C. Hence, a limited composite performance is to be expected already at room temperature. However, all LOCA offer a cross-linking in the polymeric structure that result in a residual elastomeric stiffness even at elevated temperatures.
Table 6 Summary of selected material properties of LOCA and conventional interlayer films (Kuntsche 2015a; Kothe 2013b) - Full size table
The uniaxial tensile tests at different temperatures reveal wide-ranging short-term mechanical properties at hand of stress–strain curves for 24 different test series. At – 20 °C the Young’s moduli of all tested LOCA rise by a high factor (11 and 550) at significantly higher strength due to the thermoplastic components that behave very stiff. At increasing temperatures, the Young's modulus and tensile strength are decreasing. This is returned to the typical entanglement of the polymer chains in thermoplastic materials. In general, the tested LOCA offer high elasticity and adequate ultimate strains. K2 is categorised as the stiffest material with medium strength, K3 as the softest material with the lowest strength and K1 as medium stiff with the highest strength.
The ageing tests revealed high standard deviation between the specimens. This can be returned to only a limited number of specimens and an indifferent change in the polymeric structure at a relatively small specimen. The moisture (MOI) has a negative impact on all mechanical properties for all LOCA. The water absorption and incorporation of water into the polymer chains of acrylates and polyurethanes influence the structural performance in significantly lower strength and a reduced Young’s Modulus. The effect of high temperatures (TEM) is only limited and cannot be generalised for the investigated LOCA. The radiation (SUN) embrittles the LOCA and shows a slight yellowing of all materials. The ageing is typical for polymeric materials. Likewise, conventional interlayer films are susceptible to moisture, temperature, and radiation (e.g. Kothe 2013; Kothe and Weller 2014).
The ageing of test samples of the pure material represents an exceptional case. Regarding the application of LOCA in laminated glass, the results of the ageing scenarios are exaggerated. In laminated glass, the interlayer is protected by the outer glass layers against moisture. The edges are sealed. Hence, only limited effects are to be expected in the main area. Likewise, the outer glass layers partly block the high-energy UV-radiation that should provide a lower effect on the interlayer properties.
The creep tests allow an assessment of the long-term load-bearing behaviour. Both polyurethanes K2 and K1 offer considerable long-term stiffness, that yield to high shear coupling effects in laminated glass. Furthermore, a residual stiffness is approached, which offers a continuous structural performance for laminated glass as already proven in Wittwer et al. (2013, 2016) for K2. In contrast, K3 shows large creep effects that are almost completed within the first minutes. Only a low stiffness is remaining. Therefore, the material may be unsuitable for laminated glass where long-term structural performance is required. The investigations represent an initial assessment of creep at room temperature over a limited load duration. In addition, the stress level is defined to cover only one general stress state. No linearity limits and further stress states were addressed to investigate nonlinear creep. Wide ranging creep tests at different stress levels, temperatures and increased time are reserved for future studies. To extend this study for a wider range of design scenarios, it is recommended to investigate low stress levels at + 40 and + 50 °C in and at + 60 °C above the glass transition temperature range. At low temperatures less creep is to be expected and of minor interest for laminated glass design.
The DMTA is applied to provide the basis for evaluating the thermomechanical behaviour. Further, tests at different frequencies and a wider range of temperature can be implemented to extend the dataset. This unlocks the evaluation of material models (e.g. Prony series) for detailed description of the long-term properties. For final consideration in design, supplementary four-point bending tests are recommended for validation (see appraisals for laminated safety glass with shear action: DIBt 2020, 2021, 2022, 2023).
The tensile test results agree with earlier research on the material K2 (Wittwer et al. 2013, 2016), whereas according to the authors’ best knowledge, no research is published for K1 and K3. Hence, this paper provides a significant novelty in the field of cold poured LOCA. The experimental study makes use of standard tensile test methods for polymeric materials. The thickness of the specimens in the tensile and creep tests is referred to 4 mm. However, thinner interlayers can also be used. Hence, tests according to DIN EN ISO 527-3 may provide a better understanding of size effects and allow an on-par comparison to tensile tests on film materials. The tested ageing scenarios refer to the standardised test methods for laminated glass and reflect the minimum requirements. However, different layer thicknesses of more than 3 mm are feasible with LOCA, too. This then forms practically an adhesively bonded connection. For this purpose, it is recommended to also consider the ageing methods of (ETAG 002-1 1998) to establish a comprehensive data basis.
4.1.1 Comparison to conventional interlayer films
For final assessment and comparison to conventional interlayer films, the typical stress strain behaviour is provided in Fig. 14. Furthermore, the short-term mechanical properties and the glass transition are given in Table 6.
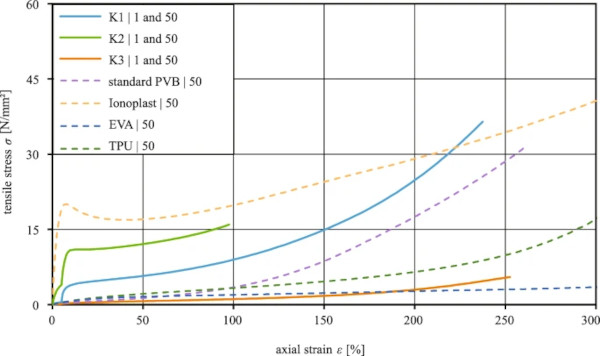
The comparison reveals a higher stiffness for both K1 and K2 compared to conventional interlayer films. Furthermore, the higher glass transition and cross-linked polymeric structure is indicative of a better temperature stability and less creep at room temperature. The strength of K1 exceeds conventional interlayers such as standard PVB, EVA and TPU. The strength of K2 is on a lower level in the range of an EVA interlayer. The K3 offers the lowest stiffness in the comparison. The elastic material behaviour at room temperature offers reduced strength at however, high ultimate strain indicating high ductility. The comparison is based on mechanical material testing. The polymeric differences due to crosslinking, adhesion to glass and composite behaviour are not addressed and need to be addressed in upcoming researches.
5 Summary, conclusions and outlook
This paper investigates LOCA for laminated glass solutions. The first part provides the motivation and gives an overview on potential use cases and the main differences of LOCA compared to conventional interlayer films. Within the second part, current research on cold bent thin glass with LOCA, the processing of cold pouring and the three investigated materials of the manufacturer (H.B. Fuller | Kömmerling) are introduced. The third part contains the experimental study: the evaluation of viscoelastic, tensile, and creep properties to assess the thermophysical and mechanical behaviour. The comprehensive evaluation of mechanical properties at different temperatures, the durability assessment and the creep tests provide a data set for designers and engineers.
All LOCA differ with regard to manufacturing from conventional interlayer films. The autoclave-free processing at room temperature brings benefits for complex composites. The low viscosity enables rapid filling and distribution in a variety of forms and interlayer thicknesses, thereby providing a wide range of potential applications. The investigated materials offer differences with regard to processing and mechanical behaviour. According to the findings, both polyurethanes (K1 and K2) are self-curing at room temperature and provide significant stiffness, which is even higher compared to conventional interlayer films such as PVB, EVA and TPU. In addition, the crosslinking in the polymeric structure and the associated good creep properties are beneficial for laminated glass applications that require long-term stability. Furthermore, multifunctional or sensitive layers such as displays, LEDs or PV-cells where soft embedding is required can be implemented. Hence, both polyurethanes offer high suitability for laminated glass with structural performance. In contrast, the UV-curing acrylate (K3) exhibits more flexibility than both investigated polyurethanes and conventional interlayer films. Main advantages of the UV-curing acrylate can be seen in the fast and sensitive curing process by UV radiation as well as its high flexibility and elastic material behaviour. This makes K3 mainly suitable for the integration of sensible layers, acoustic barrier glazings and quick curing productions.
With regard to their application for cold bending of thin glass, the mechanical performance of both polyurethanes proves high suitability. Their material stiffness, which is retaining over time due to crosslinking, provides the necessary dimensional stability and hence, a solid foundation for cold bending.
Upcoming investigations focus on the composite performance of laminated glass with LOCA. To assess and compare the mechanical performance, four-point bending tests (DIN EN 1288-3), ball drop tests (DIN EN 14449 2005) and pendulum impact tests (DIN EN 12600 2003) are scheduled. Furthermore, different concepts for cold bending are investigated and the load-bearing capacity as well as the suitability for lightweight curved glass façades are examined. This paves the way for novel applications in the building envelope with lightweight glass design and complex geometries.
Data availability
The data that support the findings of this study are available from the corresponding author upon reasonable request.