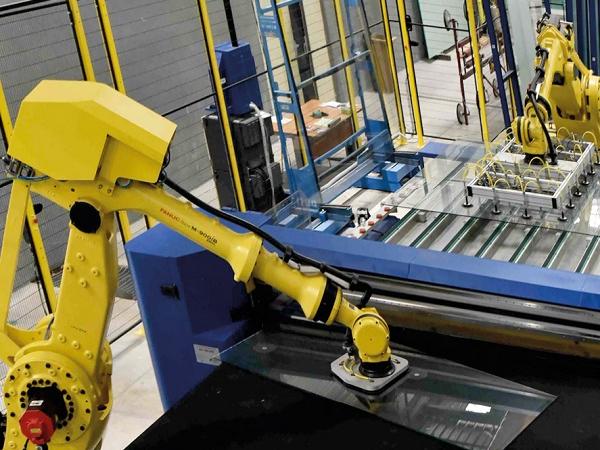
Date: 14 December 2022
In its factory in Brie-Comte-Robert near Paris, the traditional manufacturer TGVI and its software partner A+W have implemented a completely digitalized glass processing line that is the only one of its kind in France. The new production environment enables completely automatic production of TG, LAMI, and non-tempered float lites with the fastest delivery times and the highest quality.
Thirty employees working in three shifts ensure that even during peak periods, each lite lands exactly where it belongs, right on time. With its own vehicle fleet, the company reliably supplies materials for complex projects in and around Paris.
Traditional family-owned company
Trans Glaces Verres Industrie (TGVI) is a family-owned company that has specialized in fulf illing the flat glass industry’s most demanding requirements since 1983, especially those of the interior glass sector. For nearly forty years, this owner-managed company headquartered in Sarcelles (which is north of Paris) has provided the best customer service, the highest quality, and fastest delivery times. The customers of this Paris glass finisher include mirror manufacturers, glass craftsmen, and companies that equip retail establishments – it participates in many fascinating projects, especially in Paris. These projects bear witness to the company’s outstanding ability to deliver and the high quality of its products.
In 2019, TGVI acquired a new 10,500 sq m production facility in Brie-Comte-Robert (which is south of Paris), which bears the name TGVI South. With the A+W Business industrial software, the commercial part of the comprehensive A+W solution, the company creates quotations and orders, which, depending on the requirements, are produced in Sarcelles, or transferred to Brie-Comte-Robert for production. This solution, which is integrated with the A+W Production software, provides the optimized processes that TGVI requires for maximum customer service, reliable production, and the fastest delivery times.
“The A+W solution,” says Jules Benarrous, “ensures smooth flows from the customer’s initial inquiry to quotation and order creation, on through to the control of automatic production processes. It helps us work efficiently and reliably.”
High capacity for laminated glass
TGVI produces laminated glass in every size and thickness. All common types of glass are kept in automated glass storage systems that supply four LAMI cutting tables – cutting happens around the clock in three shifts. Intelligent A+W optimization software ensures the best yield and adherence to the desired cutting sequence. Large A+W Production terminals provide the employees at the cutting tables with the best overview of the cutting sequence and storage.
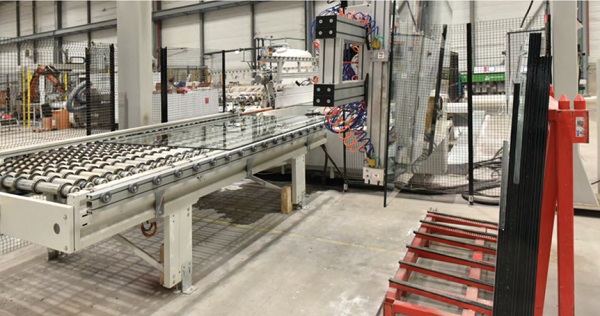
After cutting, the glass is processed further on the double edger or the INTERMAC CNC processing center. The data for control of the CNC machine is generated in the A+W CAD Designer or taken over from the customer. No programming is required for these machines.
At the outlet of the double edger, a robot conveys the lites directly to the correct rack. Software and machines work together optimally. This eliminates all picking work in dispatch.
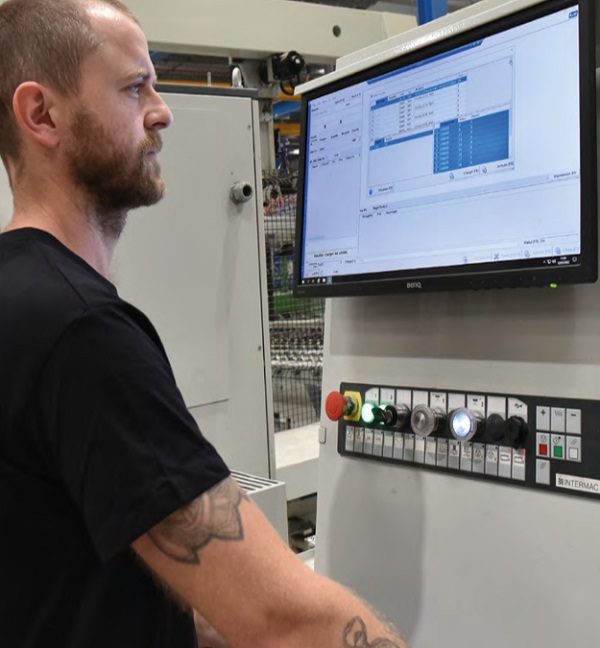
Total digitalization: The KEY to the FRANCESCA
In float processing and TG production, TGVI has worked with with its machine partner FORVET and A+W to create a fascinating, completely automatic solution, one that points to the forward-looking Industry 4.0.
Even cutting is done with robotic support and completely automatically with the FORVEY KEY solution: Two robots work constantly to feed the cutting table, position the lites, and load the FRANCESCA processing unit. The first robot loads the jumbo onto the table and conveys it to the first X-cut. Behind the cutting bridge lurks its “positioning colleague”: It turns the lite on the air pillow table for the Y-cut and, if necessary, makes all following cuts according to the results of the A+W optimization that controls the cutting process. Residual plates are conveyed back to storage and computer no. 1 places them on the correct rack. Even non-rectangular shapes can be cut.
The finished, cut lites are conveyed by the “positioning robot of the FRANCESCA CNC processing machine”, where all edge processings, millings, and drillings are performed at the usual top speed. Both the KEY cutting as well as the processing unit accept lites of different thicknesses, which allows greater freedom in optimization.
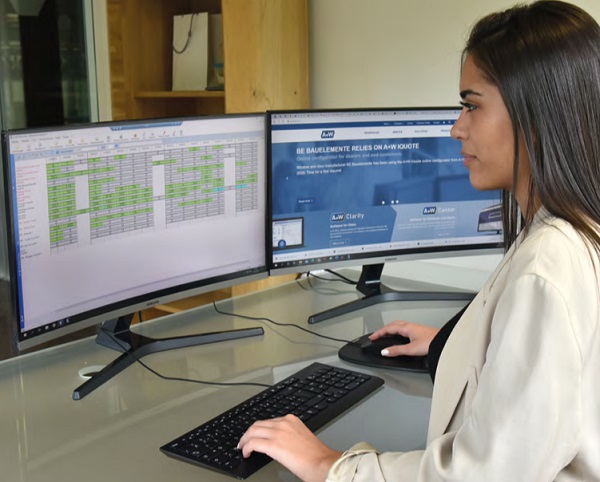
At the end of the FORVET CNC processing machine, we usually expect an employee who stores the finished lite on a rack. But that’s not the case at TGVI – for here, there is automation to the nth degree thanks to FORVET and A+W.
A shuttle transports the lites to a transport conveyor at the outlet of the FRANCESCA and feeds them into the SORTIFLEX intermediate buffer.
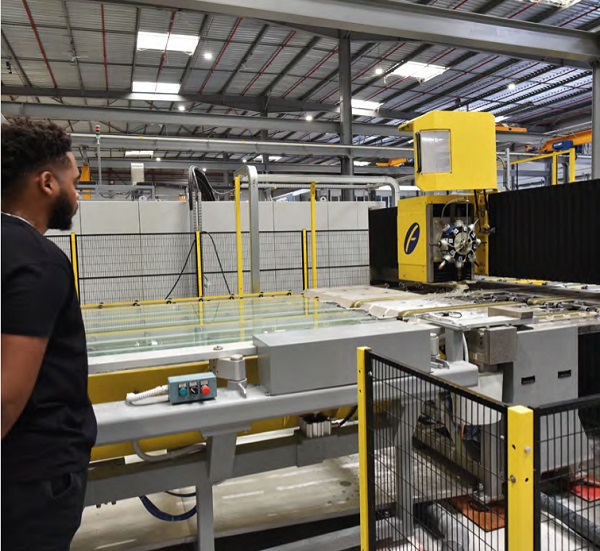
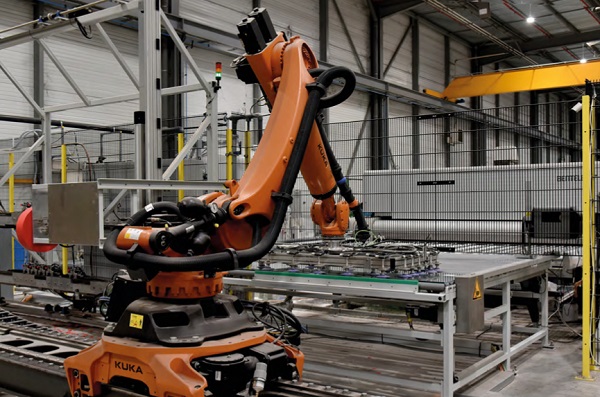
Into the furnace optimized by the SORTIFLEX
SORTIFLEX – what’s that again? This clever FORVET glass storage system consists of two overlapping vertical storage levels. The two levels double the number of available slots with the same footprint and therefore double the storage potential without requiring any more space on the floor. Depending on the length of the glass, each buffer position can accommodate several cut lites.
At TGVI, the glass for the TG system is kept here. It is fed directly into the inlet of the MAPPI furnace “pre-optimized” for the furnace bed, which, thanks to easy access to the slots of the SORTIFLEX, is an extremely elegant solution. And in this process, no human hands touch the washed lite either – automation does good things for quality!
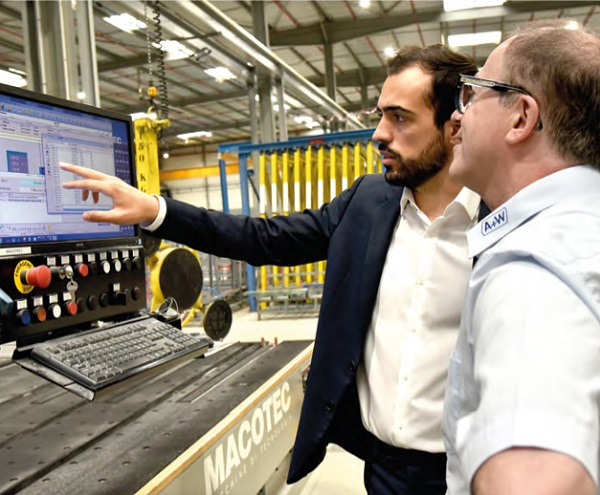
Only at the furnace outlet is the glass removed manually from the perfectly optimized furnace bed and placed on transport racks.
Of course the lites don’t have to move from the SORTIFLEX into the furnace. Several outlets are possible, which means that the lites can also be transported untempered directly to shipping racks.
This solution demonstrates what is possible today with close cooperation between glass finishers, machine builders, and software partners. Surely, you have noticed that no worker touches the lites from the feeding of the KEY system to the outlet of the MAPPI furnace – the employees monitor, check, and intervene only in case of faults. At TGVI in Brie, you can see the future of glass finishing.
Entrepreneurial courage – sophisticated concept TGVI’s business model is astonishingly simple and clear. With a focus on the interior glass market segment, enormous delivery capacity is achieved with maximum quality and the fastest delivery times thanks to consistent automation. For the production of orders, Jules Benarrous’s team is supported by state-of-the-art A+W capacity planning software, so it is extremely f lexible. The very motivated employees are also f lexible – this way, each order can be delivered on the promised delivery date: A courageous and winning concept.
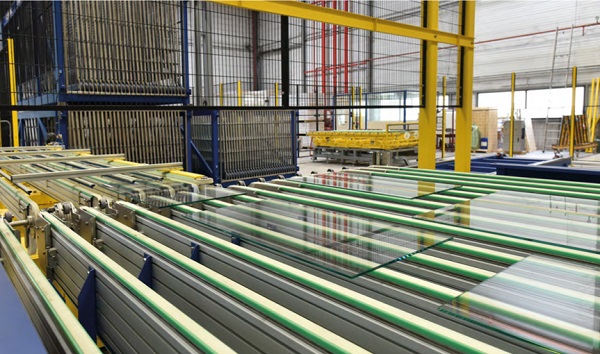
Contact: www.tgvi.fr
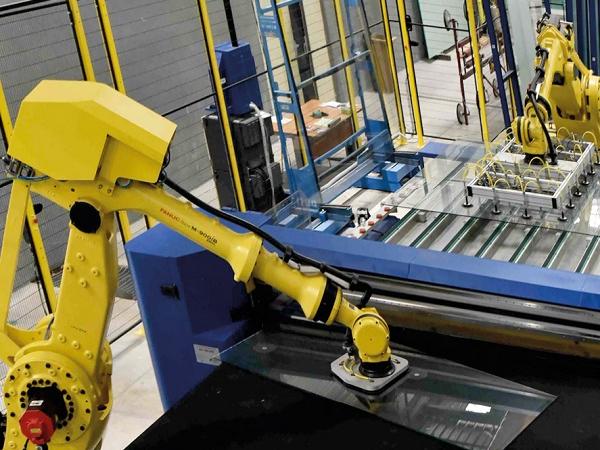

Add new comment