First presented at GPD 2017
Laminated glass is a high-performance construction material comprised of glass and polymer interlayer which is bonded together under a heat and pressure process. Laminated glass is typically subjected to performance testing meant to evaluate the capability of the material in its resistance to damage or attack. Edge delamination typically results from damage or attack originating at the edge of laminated glass where the interlayer is exposed. Edge delamination affects the aesthetics of laminated glass and may be described as a material characteristic known as edge stability.
Determination of the edge stability of a laminated glass construction is complex but can be examined through various methods of test. Exposure of the laminate to moisture and chemicals, specifically at the edge, is the basis of various test protocols that result in the development of edge stability ratings.
This paper will present exposure protocols including natural weathering, sealants, salt fog and immersion that are used to determine the edge stability characteristic of laminated glass configurations. Rating processes and results will be discussed for various interlayers. The attending will be familiar with the test scope, purpose and results interpretation of the included testing. This information allows the specifier to make an informed choice in selecting installation methods, system design and laminated glass products.
Natural Exposure
Edge stability is a performance property that indicates an interlayer’s resistance to delamination when subjected to a hot and humid environment with exposed edges. For natural exposure, a commercially operated site near Miami, Florida (USA) for exposed edge stability testing was selected. Edge stability, as defined here, is a long-term test with the samples exposed to the natural outside environment.
The edges are unprotected and consequently are wet in the early morning (dew) and during episodes of fog or rain. It should be noted that Arizona is another natural exposure site that is used for durability testing of laminates. The purpose of this site tends to be for the evaluation of polymer degradation by UV radiation versus edge stability as the climate is hot and dry. As such, edge defects in PVB laminates are not commonly noted or analyzed for long term natural exposure in Arizona.
The Edge Stability Number (ESN) is a weighted sum of "percent defect lengths" where the weight increases as the square of the depth (expressed in sixteenths of an inch – rounded metric provided for reference only). The maximum ESN number is 2500 with a minimum number being zero, therefore the smaller the number the better the edge stability in this environment. This means that any product with 6 mm delamination band all the way around the sample would be rated at 2500 (Figure 1). Any product exhibiting an ESN of less than 500 is considered exceptional. The ESN number is the averaged rating for all specimens of the sample set using the following calculation method:
PCT1 = % defect length with depth < 1/16 inch (1.6 mm)
PCT2 = % defect length with depth = 1/16 inch to < 1/8 inch (1.6 mm to 3 mm)
PCT3 = % defect length with depth = 1/8 inch to < 3/16 inch (3 mm to 5 mm)
PCT4 = % defect length with depth = 3/16 inch to < 1/4 inch (5 mm to < 6 mm)
PCT5 = % defect length with depth = ±1/4 inch (> 6 mm)
ESN = 1*PCT1 + 4*PCT2+9*PCT3+16*PCT4+25*PCT5
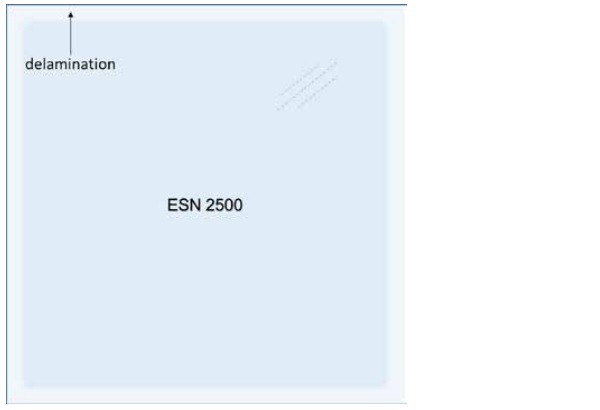
A sample set typically consists of 10 laminates prepared using standard laboratory conditions. These specimens are mounted with exposed edges on a rack facing South with 45-degree slope in accordance with ASTM D1435. They are exposed for a set duration with on-site ratings every 6 months.
Figure 2 shows the difference between conventional PVB and structural PVB interlayers, both exposed at the abovementioned site for the corresponding duration. Using the guideline that an ESN of 500 is considered exceptional, the performance of structural PVB at 52 months is outstanding. The conventional PVB exposure was complete at 46 months, however structural PVB interlayer is being exposed for a longer duration.
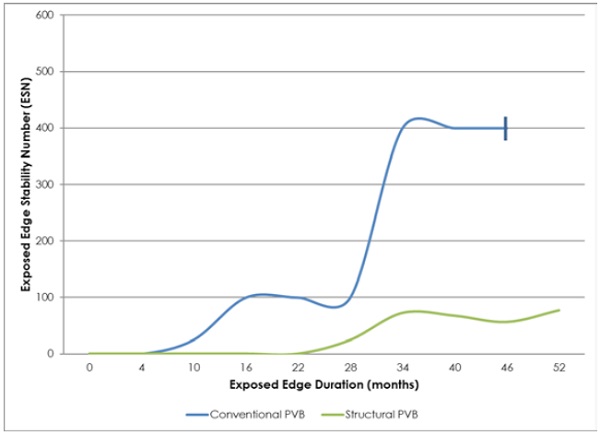
Figure 3 is a magnified photograph of a laminate exposed with no edge protection in South Florida, USA with an ESN of approximately 100.
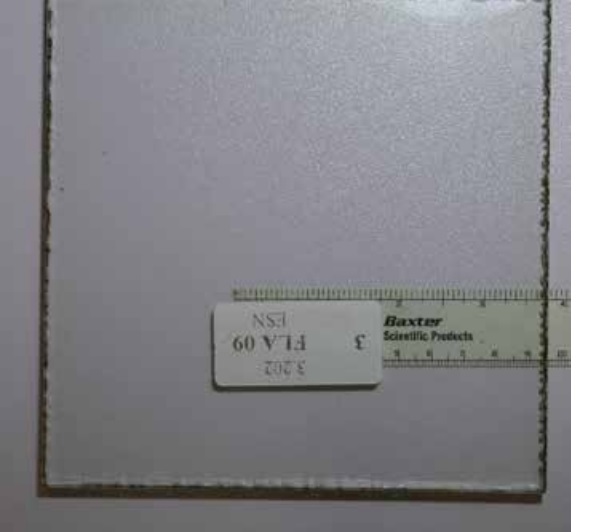
Data from Florida exposure programs continues to be gathered for various interlayers, it is impractical to keep the laminates exposed for longer than 5 years without compromising the edge with cleaning. The climate invites the growth of mold and fungus on the edge of the laminates, as seen if Figure 3. To effectively clean the edges for proper rating, the edge may be altered providing a false ESN.
Natural exposure tends to be the prevailing methodology to arrive at an ESN value, it however takes at least one year of exposure to discern existing or oncoming trends in product stability. The following sections describe alternate tests that serve as predictors or alternate mechanisms to evaluate the stability of a laminated glass edge upon exposure.
Salt Fog Exposure
Salt fog testing exposes laminates to a saline fog which is expected to simulate South Florida environmental conditions. This test protocol is designed to determine the reaction of laminates to a simulated hot and humid environment and allow conclusions to be reached about their longer-term performance and use in marine-like climates. Salt fog testing does not include intentional or concentrated solar radiation exposure.
Laminated glass specimens are produced using standard laboratory practices with conventional and structural PVB interlayers.
The specimens are exposed in a salt-fog cabinet for 12 weeks and evaluated visually for edge blush and delamination. The test is run in accordance with ASTM B117-11 Standard Practice for Operating Salt Spray (Fog) Apparatus. The method involves placing specimens in a hot (35°C) environment where the entire specimen (except for the section protected by the holder/frame) is uniformly surrounded by a fog that is created from a 5% saline solution (Figure 4).

A sample set consists of 6 laminated specimens for each interlayer type which are constantly exposed to this environment for the selected duration (12 weeks). Table 1 includes the laminate characterization in terms of initial adhesion, moisture and interlayer thickness prior to the laminates beginning exposure in the salt fog cabinet. The exception is the time out of the cabinet to rate samples and chamber maintenance (~ 1hr per week).
The specimens are rated visually for the appearance of edge blush and delamination. Corner edge blush or delamination was recorded diagonally from the corner while depth of blush or delamination from the straight edges was measured perpendicular to the edge. The depth and length of any edge effect was measured; average area and maximum depth are reported for the sample set in Table 2.
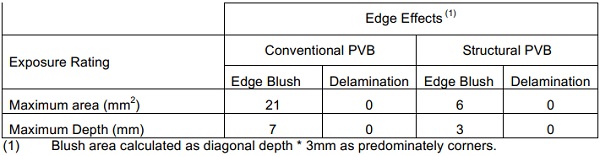
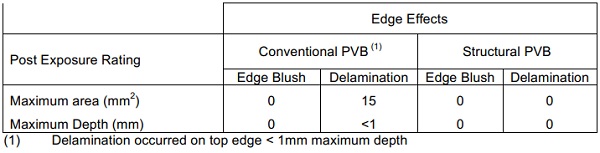
The samples remained for 60 days at ambient condition and were reevaluated with results shown in Table 3. Edge blush was no longer visible upon re-evaluation. The study indicates salt fog testing in accordance with ASTM B117 can generate edge blush and delamination in laminated glass samples in 12 weeks or less and may serve as an accelerated predictor test for ESN.
Structural PVB interlayer in laminates performed better than conventional PVB in laminates with regard to edge blush development in this study. Both interlayers when exposed to continuous marine-like climate, as simulated by salt fog testing, have good durability as demonstrated by minimal and reversible edge blush development. The results of this test also indicate that Structural PVB is not as susceptible as conventional PVB to the development of minor edge delamination after removal from salt fog exposure.
Sealant Compatibility
Interlayers can react with non-compatible materials with which it may come in contact. As such, direct contact between interlayers with chemicals used in sealants or adhesives should be carefully examined and in some cases avoided. This test method aims at providing guidance information regarding sealant compatibility when the sealant is in direct contact with the laminate edge. Compatibility testing is conducted between commercially available sealants and interlayers as warranted by product introductions, product modifications or in the case of special projects.
Results are reported from testing, but sealant recommendation are not made by the interlayer manufacturers as variations and modifications in the sealants may occur from time to time. Tests are performed under a strict protocol allowing comparisons to be made between products tested. The test results may not reflect in-situ performance. A commercially available sealant that is consistently compatible with the laminated glass as tested following the prescribed protocol has not been identified. Based on market trends, silicone sealants as a family seem to be most commonly used with laminated glass.
Sealants may contain solvents that can be harmful to the interlayer. In most cases investigated, the sealants considered neutral in curing are routinely better performers in this compatibility assessment than those sealants that indicate acetoxy cure. Acetoxy cure sealants tend to have the highest incident of generating edge effects in laminated glass out of the silicone family of glazing sealants.
Sealants and other adhesives are required to maintain intimate contact with the laminate edge throughout testing in order to be evaluated for edge effects. The procedure used for testing is documented and published both by Eastman and the Glass Association of North America (GANA) as Standard Test Method for Laminated Glass Edges when in Contact with Sealants and Glazing Tapes. The exposure calls for a UV condensation chamber with UV313 bulbs set to an irradiance of 0.71 W/m2. The continuous exposure cycle is 16 hours UV at 66°C followed by 8 hours of condensation at 60°C. The total exposure duration is 3500 hours with 500-hour rating intervals.
Edge effects are normally seen as clear, very small, 2 mm – 3 mm (0.08 inch – 0.12 inch), edge bubbles, sometimes continuously occurring along an edge, other times very distinct and isolated. The extent of edge effects differs depending upon the sealant or adhesive. Edge effects from sealants and adhesives as seen in this testing are typically maximized in depth at approximately 10 mm (0.39 inch) from the edge, and often occur as a single bubble. Although a slight discoloration can occur with sulfide containing sealants and adhesives, normally the edge effect is clear and does not cause a color change in the interlayer
Occasionally a test cycle will result in minimal to no interaction between the laminated glass and the sealant or adhesive. This does not guarantee the same results in field as application, environmental and material deviations can affect the reactions. Sealants, adhesives, gaskets and setting blocks should be selected firstly on a basis for their desired performance (i.e.: compression, tensile strength, weatherproofing, structural, cosmetic), with edge effects being a consideration after a performance class or family has been established. Although gaskets and setting blocks can and do come in contact with the laminate edge, the data acquired using this test method is only valid when intimate contact with the laminated glass edge has been maintained for the full duration of the test.
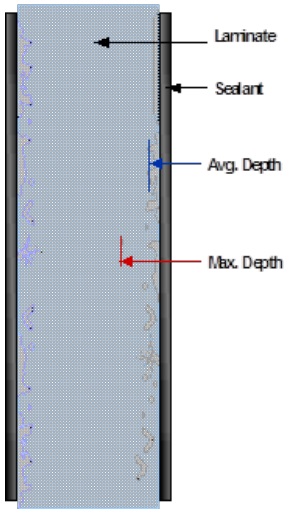
The data reported from this test are visually rated using the following criteria (Figure 5):
Average Depth Edge Effect: The depth on average, as determined visually, at which bubbles, discoloration or haze were observed. This reading is taken from the laminate edge towards the center of the laminate and measured in millimeters (mm). This number is rated at each exposure interval
Maximum Depth Edge Effect: The greatest depth of a bubble, discoloration or haze as measured from the edge of a laminate toward the center. This is the highest number recorded off any edge during any rating interval of a laminate in the set. Maximum depth is reported at the completion of the testing in millimeters (mm).
Length Affected: The sum of the length of the laminate edge to which sealant is applied, measured in millimeters, of which bubbles, discoloration, or haze were observed during the exposure interval.
Percent Length Affected: The average length affected by edge effects divided by the total length of the laminate to which the sealant was applied. The overall length of the laminate with sealant applied is and weathered is 580 mm.
Average Area Affected: The average depth of edge effect observed multiplied by the average length.
Delamination Plateau: Maximum and Average depth consistent for last two rating periods.
Edge effects can “move” throughout the test and may vary from interval to interval. The maximum depth seen at any time throughout the exposure program is the reported value independent of the maximum depth at the termination of the testing.
The data in Figure 6 shows a data presented in a typical manner for structural PVB and a structral sealant. The summary data in Table 4 shows consolidated data by general silicone product type and laminated glass compatibility of both conventional PVB and structural PVB. The data shown should be used as a reference and guide for sealant selection but should not be deemed as a guarantee of performance.
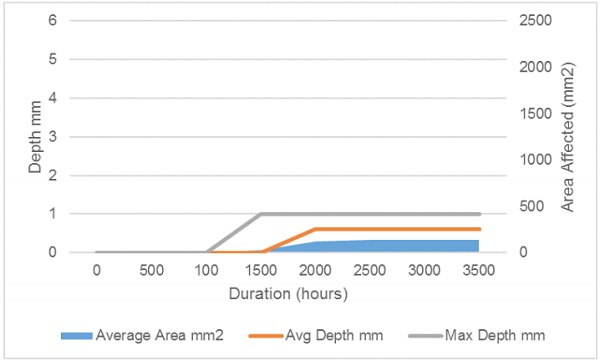
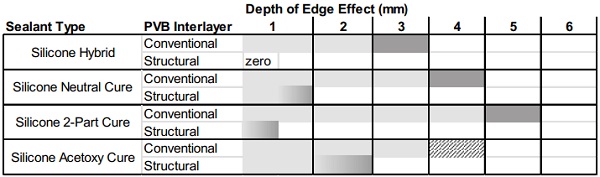
Immersion Testing
The immersion testing protocol involves the submersion of laminate specimens in various liquids for a total of 60 days plus controls that are kept in an ambient dry state. The laminates are inspected at various intervals to determine if any edge degradation occurs.
The objectives for this test are to: 1.) determine if contact of various liquids with exposed laminate edges has a detrimental effect on visual appearance of the laminate and edge quality, 2.) determine if cut edges versus polished edges are affected differently, 3.) evaluate laminates after storage for long duration to determine adverse effects from absorbed chemicals and 4.) determine test applicability as an accelerated ESN predictor.
This test did not review repetitive submersion after extended drying. There is no known national consensus standard that covers this type of testing, therefore the specifics of the test are provided.
The specimen construction consisted of laminated annealed glass with conventional PVB interlayer. The specimen size was nominal 10 cm x 10 cm. Lamination was performed using standard assembly and autoclave techniques. Half of the specimens were further fabricated after autoclaving by polishing edges. A zero-time rating for visual cloudiness and edge effects was performed.
The specimens were then divided so that two of each edge type were placed in the various liquids. The specimens were stacked horizontally on their flat surfaces in plastic containers with sufficient undiluted liquid to cover the tops of the laminates. Edges of the laminates were completely free of the containers edge to ensure maximum exposure to the cleanser (Figure 7).
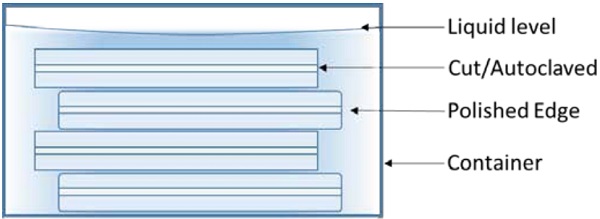
The specimens sat at ambient temperature covered by the respective liquids for a set period. The specimens were briefly removed from the liquid, rinsed with water to remove any residual cleanser and wiped dry with towel prior to examination. The specimens were rated in this manner each day for one week, then at 14, 21, 28 and 60 days.
The rating consisted of recording the ambient temperature, visual inspection for cloudiness, haze, discoloration, plus recording of maximum depth, average depth and length of any edge let goes. Any blemish was measured in mm. Immediately following the rating of the specimens, they were placed back in the liquid cleanser until the next rating interval. This technique was repeated at each interval until 60 days elapsed.
Upon the final rating the rinsed and dried laminates were stacked and placed horizontally on top of the respective containers and allowed to equilibrate with the ambient atmosphere. The specimens were rated at 1 day and 1 week in the same manner as previously reported except for the rinse and dry step. Liquids used for exposure were: bleach, laundry detergent, glass cleaner, dish detergent and water. In general, no blemishes of any kind formed in the specimens before the 14-day rating.
At the 14-day rating period very slight edge blush (whitish “fog”) was seen on the bleach, glass cleaner and water specimens. The maximum depth of this blemish was 1 mm for the bleach and water and 2 mm for the glass cleaner. All specimens except the dry control exhibited some form of edge blush by the 21-day rating period. No edge let goes were seen during the entire 60 days of the submersion portion of the test. The edge blush continued to invade the laminate with time, but at no time during this testing did the edge blush exceed 4 mm (as seen on the glass cleaner specimens). The average depth of the blush was 2 mm.
Upon removal of the specimens from the submersion portion of the test, it was noted at the 1 day rating that most of the edge blush had greatly diminished or disappeared completely. There was still no edge delamination. At the 7 day, dry rating, minor edge haze was seen on the glass cleaner specimen and the water control. The let goes on all specimens were also restricted to the edge and in some cases, so small they were difficult to see.
The only exception to this is specimen number 9, glass cleaner, cut/ autoclaved specimen which had a visible delamination in the lower right hand corner of the specimen. The delamination was amebic in shape, located 15 mm from each edge with the leading front of the delamination 20 mm diagonal from the corner. The delamination was approximately 3 mm in diameter.
All specimens except the dry controls exhibited some form of edge blush during the exposure period. This edge blush essentially disappears on most specimens within one day of removal from the liquid. Most specimens developed a slight edge let go (release) after 1 week of sitting in ambient conditions after submersion. There does not appear to be a significant difference between the cut and polished edges, although some of the polished edges had lower levels of edge let go after drying. During the testing and subsequent drying it was obvious that the window cleaner was the harshest of the liquids with regard to laminate attack.
After six (6) years of laminates sitting in an ambient environment without light, the laminates were re-evaluated. All signs of blush were gone from every laminate. In the case of chlorine bleach, water and untreated edges all samples showed no defects for delamination or blush – even when edge delamination was recorded during testing. The other samples had typically uniform let-go around the edge with no sample having a delaminated depth of more than 4 mm. The samples did not develop deeper penetration of the delamination area, however the delamination area did in most cases become uniform around the edge, if it existed.
There was no significant difference between the cut/autoclaved edge and the polished edge specimens. However, the overall edge effect numbers are so small it is difficult to determine if there was any improvement or detriment to polishing the edges in this test. From the survey of products tested it appears that glass cleaner is the harshest cleanser from both and edge blush and a delamination perspective. It is not known if repetitive submersion and drying would alter these results or if exposure to other solvents or exposure at temperatures higher than ambient would have any effect. Note that no adhesion or other mechanical testing has been completed on these samples.
Based on the results of this testing it can be determined that limited (casual) contact with the tested liquids will not have a dramatic adverse effect on the visible acceptability of laminated glass made with conventional PVB interlayer. This test may also serve as a predictor for ESN performance.
Summary
It is clear that the four tests described have different delivery mechanisms to infuse the interlayer with moisture or chemicals that could in turn react and cause a delamination at the edge. Laminated glass is a highperformance construction material comprised of glass and polymer interlayer which is bonded together under a heat and pressure process.
Although this paper looks at the test methods to assess edge stability, it should be noted that causes of delamination, at the edge or in the body of the laminate, can be caused by many variables and are usually present in combinations rather than a single factor. Laminated product with PVB and non-PVB interlayers can be susceptible to delamination if not properly designed and laminated.
Causes of delamination can be interlayer type and thickness, glass warp, edge kink of glass, contamination, improper processing, storage and handling, or inappropriate installation and many other variables. A low ESN alone is not a guarantee against delamination, just as a heat soak test is not a guarantee against spontaneous breakage of tempered glass.
ESN is a rating that allows the user to make a decision regarding basic acceptability of a product for a given application. Edge delamination affects the aesthetics of laminated glass whereas center delamination can affect the impact characteristics and safety performance of the glazing at the time of impact, or after impact, should glass shards not be retained by the interlayer. Determination of the edge stability of a laminated glass construction is complex but as demonstrated, can be examined through various test methods.
An overall assessment of interlayer and laminated glass performance should be completed for each project to ensure the materials are capable of meeting the desired characteristics in-situ. Laminated glass offers many benefits from safety and security through UV screening, acoustic damping, structural and vibrant design options. This information allows the specifier to make an informed choice in selecting installation methods, system design and laminated glass products.