However, due to the complexity of this process, it is crucial to know all about the challenges and stumbling blocks that arise in order to act or react respectively.
This is the only way to ensure that the lamination process is smooth and stable, which in turn is a prerequisite for top quality and optimum end products.
In conjunction with excellent pre-lamination, this expertise also helps to reduce production costs, since process time and glass waste can be significantly reduced in this way. This particularly applies when complex foils or tempered glass are being used. Any defects that have occurred during lamination are clear to see after the first pressing of the glass in the pre-lamination or after the autoclave process.
With tempered glass, glass evenness is an important prerequisite for a high-quality glass laminate product. Due to the high temperature (above 600 ° C) and the ceramic transport rollers that are used, traditional tempering technology with roller furnaces can lead to so-called roller waves and other deformations in the glass, which can make the laminating process more difficult.
The glass should therefore at least comply with the standards EN 12150-1 for ESG and EN 1863-1 for TVG. In order to ultimately achieve good quality and a stable process, an even better glass quality is recommended.
The more even the tempered glass lites sheets, the thinner the foils which can be used, but the lamination process is also stabilised and delamination is prevented, which can also reduce the production costs and therefore the price of the product.
ATTENTION MUST BE PAID TO THE FOLLOWING POINTS FOLLOWING THE PRE-LAMINATION PROCESS:
- Edge seal
- Pressing force
- Pressed too cold
- Pressed too warm
- Glass offset
1. EDGE SEAL
A good edge seal is recognisable from the fact that the edge area of the laminated glass is transparent over a width of around 20 mm. This is a clear indication that the foil and glass are optimally bonded together.
On the other hand, the foil structure is still visible in the remainder of the laminate. It should appear even across the entire area. This shows that the pressing force of the pressing rollers and heating by means of convection or radiant heaters were always nice and even during lamination.
2. PRESSING FORCE
Two main technologies are used in pre-lamination to exert pressure with the pressing rollers:
- the hydraulic or pneumatic application of pressure using cylinders
- the spindle technology
THE HYDRAULIC OR PNEUMATIC APPLICATION OF PRESSURE USING CYLINDERS
The hydraulic or pneumatic application of pressing force using cylinders is simpler from a design point of view and therefore more cost-effective, but involves numerous challenges.
And if rectangular sheets of glass are not being used, but the diamonds or triangles which are gaining in popularity in architecture, for example, the complexity increases again significantly with this technology.
Quick and precisely timed pressure changes are also only possible to a limited extent. However, these are needed to create an optimal edge seal, particularly for large glass cutouts in the laminate.
The glass product also always has to be pressed in the middle of the pre-lamination with this technology, otherwise parallel pressing using a cylinder cannot be guaranteed.
The result can be an uneven edge seal or uneven laminate thickness, which in turn can complicate further processing and reduce the cycle time. As a result, permanent readjustments of the press are required, which may not only significantly increase glass waste, but also the costs.
THE SPINDLE TECHNOLOGY
Spindle technology is used much less often, which is probably because it is the more cost-intensive technology. Nevertheless, it has several advantages. Working with spindle technology is more sustainable and eliminates the above-mentioned problems.
This particularly applies to the production of special glass lites sheets in the architectural area, where the pressing process can be carried out very efficiently, resulting in highest quality and therefore also lower product costs due to less wastage.
This technology can also be adjusted at the push of a button, and the spindle is considerably more stable with regard to service life and process reliability. Furthermore, production can be carried out and continuously monitored due to the even pressure distribution on a reference side, which significantly simplifies the entire process.
A stable process and high product quality are also ensured here if production is not permanently carried out exactly in the centre of the system. If a servo spindle is used, very quick and precise pressing force adjustment is possible on the one hand, and on the other hand parallel pressing is possible thanks to the interlocking drive.
If the pressing force is incorrectly adjusted, the air bubbles between the glass and the foil are not squeezed out and the edge seal is insufficient. This phenomenon is already evident after the pre-lamination process, and can even lead to complete delamination in the autoclave process in extreme cases.
In the example shown here, pressing was first carried out with the correct force, and then with virtually no pressing force. After the pre-lamination, the glass product can appear as follows:
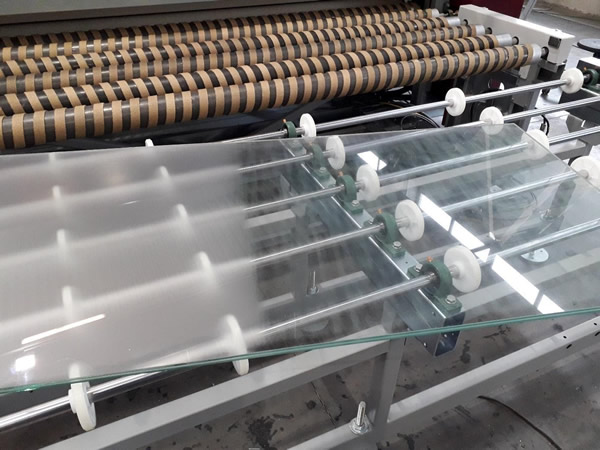
3. PRESSED TOO COLD
If too little energy is introduced before the pressing process, i.e. if the pressing is too cold, the transparent 20 mm (compare figure 1 with figure 2) at the edge of the laminated glass which are visible if you have an optimal result disappears. And this is a clear indication that the adhesion between the foil and glass is insufficient. Following the autoclave process this can lead to numerous problems, such as the so-called “blow-in” phenomenon (see also further down).
4. PRESSED TOO HOT
However, too much energy is also not optimal. In this case the laminate is pressed too warm. This makes the foil too soft and sticky, which can be recognised from the fact that the glass package is almost transparent. The foil adheres too strongly to the glass before venting using a pressing roller, which means that the residual air cannot not be properly pressed out of the laminate.
This residual air expands in the autoclave or additional air is pressed into the laminate due to the lack of foil adhesion to the glass and the 12 bar of overpressure. This creates many circular bubbles, and the glass package does not appear transparent as it should.
Here again, the direct comparison of too cold vs. too hot:
THE FOLLOWING PHENOMENA CAN OCCUR AFTER THE AUTOCLAVE PROCESS:
Following the pre-lamination process, the laminated glass packages are fully pressed in the autoclave with a defined pressure and at high temperatures for a certain time.
The following quality problems can occur from this:
- Blow-in
- Air trapped
- Offset
- Autoclave cooling problems
- Bubble formation due to incorrect hold time
- Mineral and organic impurities
1. BLOW IN
So-called blow-in occurs if the recipe in the autoclave has not been correctly set - for example, if the pressure is increased too quickly and therefore air is pressed back into the laminate. This can also happen if there is no proper edge seal. This example shows how important it is to have a good edge seal.
2. AIR TRAPPED
Air trapped means that not all of the air has been pressed out of a laminated glass package. This quality problem can arise due to the following factors:
- Pre-lamination pressing not optimal
- Too hot in pre-lamination (foil too sticky)
- Roller wave with tempered glass
- Humidity too high
If too much heat is applied in pre-lamination, the foil becomes sticky and the air that is present cannot be properly pressed out of the glass package.
If glass is toughened (tempered), the high temperature and the ceramic transport rollers can cause wavy unevenness in the glass. This can result in the glass closing before the air can be pressed out of the glass package.
This unevenness in the toughened glass creates also results in different gap widths between the two glass lites sheets in a laminate, which then has to be filled by the foil. However, since the lamination foil can only compensate for unevenness to a limited extent, thicker foil or multiple layers thereof must be used in this case.
If the air humidity is too high, the foil is too "wet". At the high temperatures in the autoclave process, the moisture can evaporate which in turn results in bubbles. The connection between the foil and the surface of the glass, the so-called adhesion, is lost in this way.
3. DELAMINATION
With delamination, the glass and the foil become detached again. This phenomenon occurs if the PVB foil which is accessible at the side edge of the glass comes into contact with water or is continuously in contact with water, for example. However, delamination can also occur if difficulties have already arisen during the lamination process. This example (see picture) once again shows how important a good edge seal is.
Improper storage of the foil, resulting in too much moisture content, can also lead to delamination. The adhesion between the glass and the foil is therefore reduced, which can either lead to the first signs of delamination after the autoclave, which are evident from round bubbles (ice flowers) - or not until the product has been used in a façade, for example. However, the quality of the "gluing" is also reduced in this case.
When PVB foils are stored and processed, it is important to keep the temperature constant at around 18-22°C, and the air humidity at around 25-30% relative humidity. This requires a properly dimensioned climate chamber that is able to guarantee these conditions.
Material incompatibilities such as softener migration are also often the cause of delamination symptoms, which may not show in on the installed laminates until several months or years later.
4. OFFSET
The problem of offsetting can occur during the positioning and overlapping of the glass in the assembly area or during pre-lamination.
If each pressing roller in pre-lamination is driven by its own motor, these must be perfectly synchronized, since uneven speeds can otherwise result in an offset. Irregular wear of the pressing rollers can also lead to the occurrence of offsetting after a certain time. In the event of smaller laminates or thinner cover glass lites sheets, incorrect application of the pressing roller on the front edge of the laminate can cause glass displacement.
During the autoclave process, the laminates should always lie precisely at an angle of 90 ° from the clamping area to the rear wall support on the autoclave rack, since this can also lead to glass offsetting, which this particularly applies to large and heavy glass lites sheets.
5. AUTOCLAVE COOLING PROBLEM
Particularly because the parameters of pressure, time and temperature are so precisely defined, the autoclave plays a very important part in lamination. If, for example, the cooling register is defective or the cooling lines calcify, the cooling curve cannot be maintained and the laminated glass products are still too hot, whereas the pressure is already being reduced. This can lead to the formation of bubbles at the edges.
6. BUBBLE FORMATION DUE TO INCORRECT HOLDING TIME
The correct program must be created and selected depending on the glass structure of the lamination product. The holding time, i.e. the time during which pressure and temperature are present at the same time, plays an important role in this case. If the holding time is too short, the foil does not melt completely and thus free spaces in the laminate, caused by uneven glass, cannot be filled with the foil quickly enough.
7. MINERAL AND ORGANIC IMPURITIES
Impurities such as this are usually caused by the washing machine and are attributable to inadequate maintenance of the water treatment.
Examples of mineral impurities are lime and salts, for example, and examples of organic impurities are algae. Both can have a negative influence on adhesion in subsequent processes, which ultimately leads to delamination.
It can basically be said that organic and mineral impurities can primarily be traced back to water treatment. Cutting oil residue or other impurities on the surface of the glass can usually be attributed to the quality of the washing machine.
It must therefore always be ensured that the water treatment provides water with maximum conductivity of 10 µS. A washing machine that is suitable for a lamination system must prevent the carry-over of dirty water and dry the glass surfaces and glass edges in the drying zone in such a way that they are completely drip-free.
FAZIT
The lamination process is also becoming increasingly important in the glass industry. This is mainly due to the fact that the safety standards for installing glass components have been raised considerably and are constantly being improved. In order to make the production process stable and smooth, in-depth specialist knowledge is required. This is the only way to ensure that the end products have optimal quality and the technical safety requirements are fulfilled.