Architectural Glass Laminating Guide - Part 3
By Luc Moeyersons
1. Assembly Room:
Standards of cleanliness:
- Over pressure and air locks.
- Special hats and clothing.
- Static charges can attract dust.
- Filtered conditioned air/replace filters on regular occasions.
- Only access by operators, no visitors, unless in special clothing.
- Avoid horizontal surfaces (dust collection).
- Daily cleaning of floor (with water)
- If vacuum cleaned, filter-unit/motor outside the clean room.
- Inspection lights are recommended.
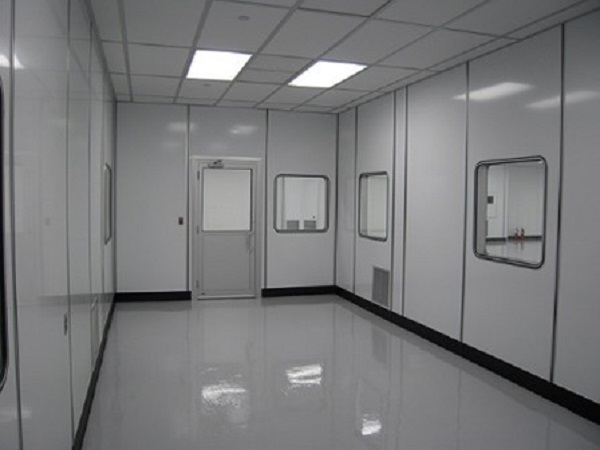
Clean Room classifications (ISO & Federal Standard)
Particles with a size larger than 35 microns are visible to the average human eye under normal lighting conditions. In a dark room where a beam of light falls in, particles with a size of 25 microns (or larger) become visible.
So, particles with a size above 25 microns are to be avoided.
They can float in the air and gently settling on horizontal surfaces and become airborne with air movement (when a person walks past) and finally settle on the PVB film.
A class 100 000 (Fed Std 209E) - ISO Class 8 should suffice for a glass laminating clean room.
Measurements to define the clean room class should be performed without operator(s) in that room (but various positions should be checked to verify uniformity of cleanliness/air flow).
For regular quality checks operators should be present during the evaluation in order to verify the real situation.
An average human being “carries” some 600 – 800 thousand particles per cubic foot along.
Uniforms keep this massive contamination potential within the uniform.
Filters (of the airco system) need to be cleaned/replaced regularly.
The clean air needs to pass the area’s that one attempts to keep particle-free first and being extracted (if possible) behind the people (see drawing below).
Cleaning the floor with water (at the end of the shift) does not create a major problem, the humidifier/dryer should be able to coop with the small increase in relative humidity.
Vacuum cleaning is O.K., provided the filter unit and motor are outside the clean room (connection through vacuum tubing system).
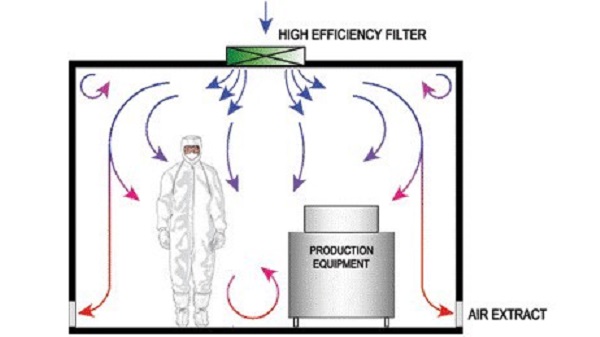
4.a. PVB unwinding and lay up systems.
There are four (slightly) different (automated) PVB unwinding systems:
Sheeting Transfer:
The bottom glass is laying statically on the conveyer and PVB is moved over the glass and put in place (manually or with robot arm).
Advantages:
This system can be used for multi lamination (multiple glasses and/or layers of PVB).
Disadvantages:
When the PVB sheeting is dragged over the glass (moved while in contact to the glass), wrinkles in the PVB film are created. This can interact with lay-up flatness or de-airing in the pre-nip (formation of air pockets).
Sheeting & Glass Transfer:
The bottom glass moves forwards, while the PVB sheeting is unwound. A robot arm ensures both movements happen at the same linear speed.
Advantages:
The lay-up quality (PVB sheeting flatness) is pretty good.
Disadvantages:
This system is less adequate for multi glass/multi PVB lay-up.
The glass would need to be moved back to the original starting position to allow the next layer of PVB to be laid down. (a second lay-up position is sometimes offered by the laminating line supplier, but this is not the most adequate solution. (cost, second unwinding position,…)
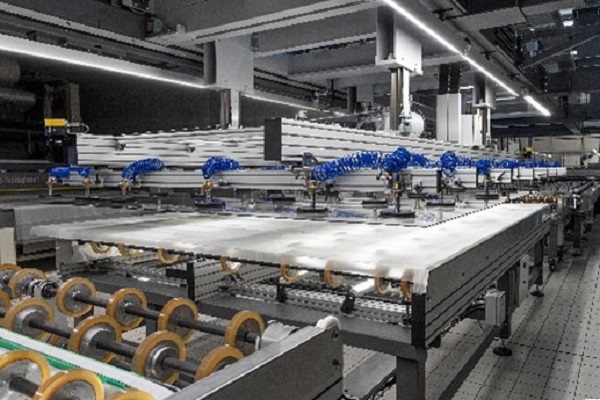
Roll Transfer:
The entire roll (and support/unwinding system) is moved over the glass that is laying statically on the conveyor.
Advantages:
This system can be used for multi PVB layer lamination/lay-up.
Disadvantages:
Due to the movements of the large and heavy PVB roll stand, accuracy is less good and contamination from moveable parts (grease, fat, particles,…) is a larger risk.
This system does not seem to be commercially existing/available anymore in Europe.
Tensionless Sheeting Transfer:
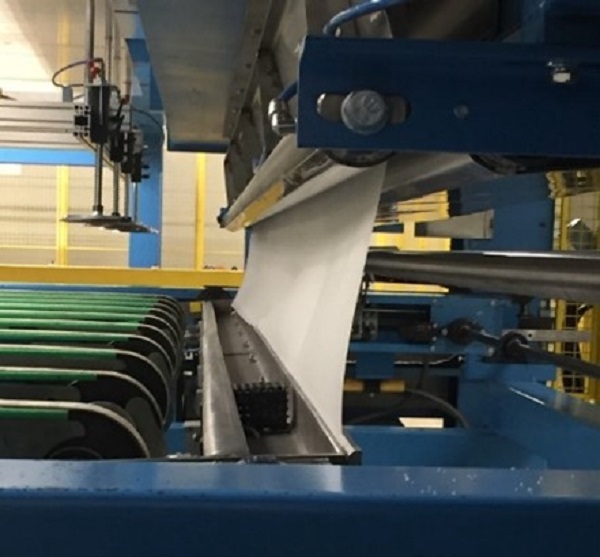
The PVB sheeting (at the beginning of the sheeting) is grabbed over the entire PVB width, while the PVB film is unwound, a roller is moved till halfway the laminate length. The PVB film is cut (ensuring the correct length) and the roller continues its path while the PVB (without tension) is laid flat on the second half of the static glass.
Advantages:
Due to the tension free lay down, no wrinkles are induced in the PVB and a flat lay-up is ensured.
Disadvantages:
Complexity, automation.
Thick, cold PVB at the end of the roll, can come down slightly curled up not allowing the grabbing device to take the film over the entire PVB width (“umbrella handle”).
A possible solution for these thicker PVB rolls, is to store these rolls (un-opened) 24 to 48 hours, prior of usage at room temperature (21 degrees C).
4.b. Completion of assembly:
After the top glass is laid down on the PVB sheeting, the laminate is moved to the trimming station.
The excess PVB is trimmed away.
Flush with the glass edge on the long sides of the laminate (90 degree to extrusion)
With the trimming knife under an angle of 45 degrees to ensure a little PVB is sticking out at the short edges (leading and trailing) (less than the thickness of the glass in order not to contaminate the nip roller (or vacuum bag)). (This in view of a higher risk for PVB to shrink (in a limited way) in extrusion direction versus at a 90 degree angle)
Trimming can be automated with trimming knife or rotative trimming disc.
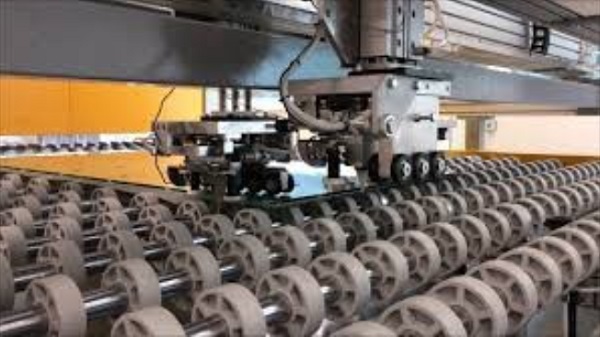
Challenges:
Contamination
Glass chips from inadequate trimming operation (glass edge is not perfectly aligned (breaking out of glass after scoring (cutting operation)))
These glass chips can sometimes be found in between both glass layers and become more visible after lamination/autoclaving.
Shrinkage of PVB
can be caused by:
- Incorrect glass or PVB temperature
- Stretching at unwinding
- Not enough time to relax.
- Poor trimming technique or equipment (local pulling, dull trimming knives,…)
Flat lay-up of the PVB
can be influenced by:
- PVB Caliper
- assembly system (see earlier)
- glass temperature
- sheet flatness
- sheet tackiness (“adhesion/stickiness” at room temperature).
5. Prepressing (or Pre-nipping)
Process Types.
Nip roller process.
This is mainly used for “simple” laminate constructions.
More than 90 % of the laminated glass produced is processed in nip roller processes.
Vacuum Process (bag or ring).
Less than 10 % of the laminated glass is produced in vacuum processes.
Vacuum processes are mainly used when a significant cost is already in the products to be laminated (tempered, printed, with holes, as well as multi-laminates) and the success level of the lamination should be close to 100 %.
Pictures are shown with reference to the source of the picture.
If the info is wrong, please contact author with correct info for document correction.
This information corresponds to our current knowledge on this subject. It is offered solely to provide possible suggestions for your own experiments. It is not intended, however, to substitute for any testing you may need to conduct to determine for yourself the suitability of our advice for your particular purposes.
This information may be subject to revision as new knowledge and experience become available. Since we can not anticipate all variations in actual end-use conditions, LAMI Solutions makes no warranties and assumes no liability in connection with any use of this information.
Nothing in this publication is to be considered as a license to operate under or a recommendation to infringe any patent right.