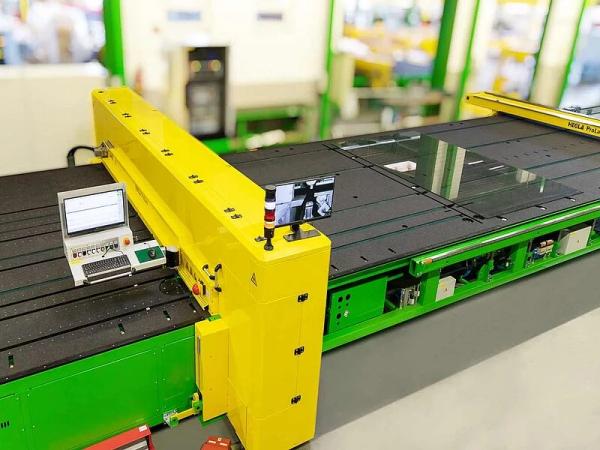
Date: 14 March 2023
The ongoing rise in the proportions of laminated safety glass used in glazed products is placing glass processors under increasingly tight constraints. More stringent safety regulations have increased international demand and led to more widespread use of LSG, both as a stylistic architectural element and for functional purposes.
At Vitrum 2019, HEGLA presented their laser diode heating system, a new process that makes the cutting process twenty per cent faster and can therefore deliver higher cutting capacity on the same footprint. The new technology, which has been part of the ProLam LSR series equipment for just under three years, promises four advantages.
Focussed heat application shortens the cutting process by 20 per cent
The centrepiece of the process is a new, patented laser diode heating system that replaces conventional heating tubes. The added technical value is generated by the physical properties of the laser. The laser diodes consolidate the thermal energy of the laser, focus it on the scoring contour and apply it precisely to the film. Without any of the otherwise typical radiation losses into the air and the surrounding glass, the film reaches the required transformation temperature much faster than when using conventional techniques. Having already been incised and broken out, the glass is pulled apart during the heating process and then cut as a knife passes through it. The diode strip is mounted in a fixed position above the cutting area so it remains cool and does not have to be folded away, which saves time. This position also means that the timing of the individual processing steps can overlap, accelerating the overall process. “A lot of our customers are already using the ProLam LSR, and are impressed with how much shorter their cutting steps have become. In terms of cuts per hour, the system achieves 20 to 30 per cent higher productivity,” reports HEGLA Managing Director Bernhard Hötger.
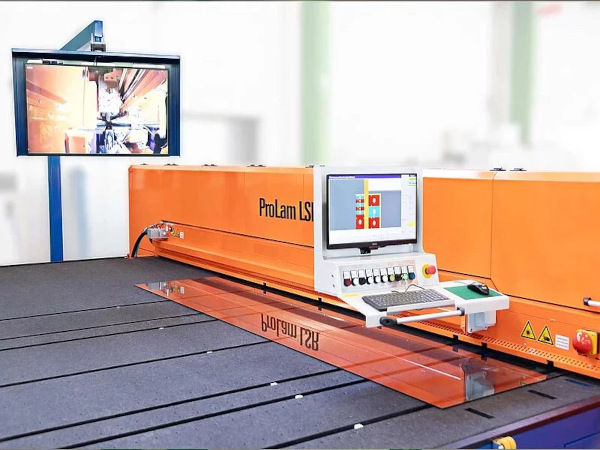
No waiting for the next cuts
The thicker the LSG and the film, the more time the laser can save for HEGLA’s customers. The consolidation of the energy and the very low radiation losses allow the heat to be focussed and applied along precise lines. When penetrating the glass, the laser retains more of its strength than conventional heaters, enabling the glass to be heated in a shorter time. “LSR technology features considerably lower heat loss into the surrounding pane and the air, resulting in two more advantages that are even greater than we expected when we first started developing the product,” says Bernhard Hötger. “Even when cutting thicker units, the glass only becomes warm to the touch at the edges. That means customers can move straight on to their next cut without waiting for the glass to cool down first.”
High-quality glass edges
Consolidating the laser’s thermal energy also offers another benefit in terms of edge quality. “When the glass is pulled apart, only the heated film in the cut is stretched. Tests at the Fraunhofer Institute have shown that the remaining laminate remains unchanged by the local application of heat, reducing the previous causes of subsequent delamination to a minimum.
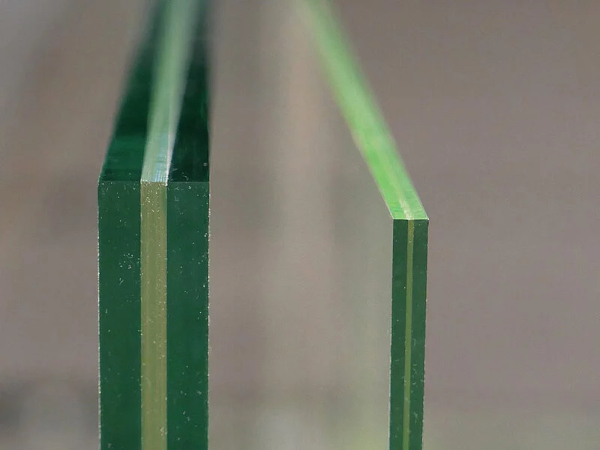
Shorter boot-up time saves energy
The laser diode strip is divided in half and, to save energy, each side is activated completely or partially depending on the length of the cut. The much shorter boot-up time also improves the system’s carbon footprint. When the system reaches 20,000 operating hours or more, the diode strip has proven to require less maintenance and be more durable than the conventional technology.
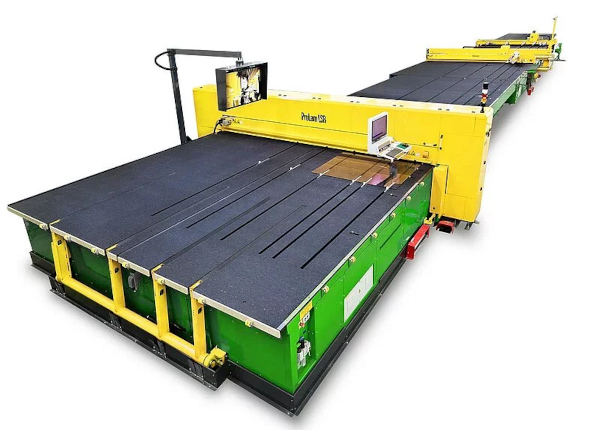
Adjustable to suit specific needs
The ProLam LSR comes equipped with the laser diode heating system as standard, and some existing systems in the ProLam series can also be retrofitted. Other features, such as the Kombi variant with automatic edge deletion, a float cutting head and built-in breakout bars add to the range of functions on offer. HEGLA boraident also continue to offer non-destructive laser printing to give your glass a bespoke, machine-readable marking. If the marking is applied before cutting takes place, the glass production process can be fully digitalized by scanning the code. This technology can be used for purposes such as triggering process steps during production, tracking workflows across the entire product life cycle, and reading the glass data using a scanner – even many years down the line. If required, additional information such as fire protection certificates can also be saved in the marking.
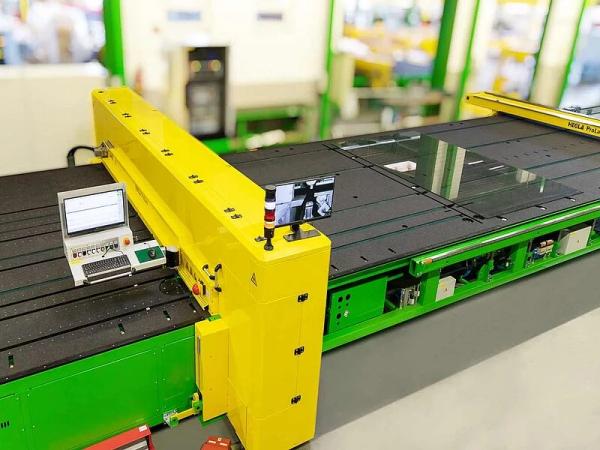

Add new comment