This paper was first presented at GPD 2023.
Link to the full GPD 2023 conference book: https://www.gpd.fi/GPD2023_proceedings_book/
Authors:
Antti Aronen, Sami Kelin, Pekka Lyytikäinen
Glaston Oyj Abp, Finland
Abstract
Glass tempering is a process that can be made in many ways to get tempered glass that meets the standards. The selected way is usually chosen by the operator and is almost always based on experience instead of science. On top of this, the process is driven by regional and factory standards, factory targets and enduser demand. The main process targets are to meet the standards, but other process targets can be to optimize e.g., production rate, yield, anisotropy, or deformations. It is difficult to achieve all these targets at the same time. In the future, the process can be controlled by telling the machine what the target of the product is, instead of setting the tempering parameters. With a good understanding of the process and an increased number of measurements in the process, the automation level can be increased. Increased automation level helps to adjust tempering parameters depending on the internal and external variables. With all automated information, the tempering machine would recommend the loading pattern and set process parameters to meet the desired specification of the product.
Introduction
The general target in glass tempering is to process glass with a heat treatment process so that it has increased strength and safety compared to float glass, but its visual quality should be close to float glass. The visual quality and uniformity of tempered glass are not ever the same as the float glass has, because there are always some visual defects due to deformations and scratches, or quality is not uniform over the glass pane. Even the stress distribution is always non-uniform. The first target for each glass processor is that glass meets the standards. That should be met to get products approved for sale. In the standards are defined limits for strength, fragmentation, deformations, and other visual quality definitions. [1,2]. Often glass processors have more strict internal standards which they want to meet. Those can be related to e.g., deformations, stress levels or anisotropy.
The level of automation in tempering furnaces has increased during the last few years. With advanced technology and the lower price of new technical components, the increased number of measurements has made it possible to get more information about the process. This information helps to understand how furnaces and cooling work during the process. So far, the furnace operators have tried to understand the measurements to adjust the process, but recently automation has taken a part to help operators and adjustments have been done based on the automated rules. These rules are based on two things, the experience the process experts have got gathered over the years, and the physical theory of the tempering process. With current technology the possibility to automate these rules with computers is possible.
One target in automation is to reduce the need for highly experienced operators. Most tempered glasses are rectangular in shape, 4 – 12 mm thick clear or coated glasses. Plenty of tempering rules for those sizes can be automated and then also new operators are able to use tempering furnaces easily without long-time learning from experienced operators. Another target is that the tempering process takes the change of furnace state and environmental conditions into consideration automatically so that the same recipe can be used all around the day and year without the operator’s need to change parameters when automation makes small adjustments.
Tempering process
In general, the glass tempering process is quite simple. At first, glass is heated in a furnace to around 630 °C so that glass is soft for tempering to get residual stresses without high tensile stress during cooling. Then in the cooling part glass is quenched so that residual stresses are formed. The level of residual stress depends on the glass temperature before cooling and the cooling rate. [3,4] There are different methods to heat and quench the glass. A typical way to heat the glass is to use a furnace where glass is moving on ceramic rollers and heat is brought into the furnace with electrical heating elements. Usually forced convection is used to balance the heat transfer. Typically, in the cooling, the glass is also moving on the rollers and heat transfer is done with cooling air. [4] Even though the process in general is simple, the control of the process is complex. In the user interface, an operator can adjust several parameters to control heating elements, convection, conveyor movement, cooling pressures, nozzle distances, etc.
Based on the operator’s experience the process parameters are adjusted depending on the glass thickness, glass size, coating/ enamel, loading pattern, etc. Also, the state of the furnace and ambient environmental conditions influence how parameters need to be adjusted to achieve good-quality tempered glass. Parameters are often re-adjusted after load depending on the end quality of the glass. Typically, at this point, the changes are made to affect glass flatness or stress level.
The main things to control the process are the glass temperature level after heating and the temperature uniformity or profile of the glass pane. The higher temperature level helps with tempering, but it increases the deformations (roller waves and edge kink) in the glass. The temperature should be uniform over the glass pane to get an even stress level/breakage pattern over the pane. Also, the temperature profile over glass thickness should be symmetric during heating to hold the glass flat on the rollers.
In the cooling part, the main factors are the cooling rate level depending on the glass thickness and demanded stress level. Also, the heat transfer between the top and bottom surfaces should be balanced to keep the glass flat. One more important thing to achieve the desired stress level is the quenching time to avoid the relaxation of the stresses with too short a quenching time, especially for thin glasses when the cooling rate can be different between cooling sections.
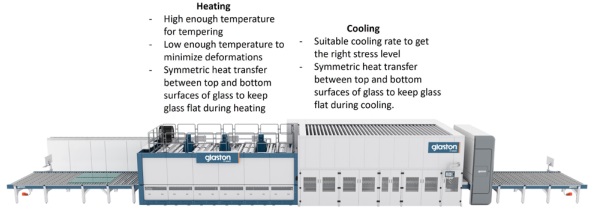
Automation of the tempering process
The automation level in tempering furnaces increases all the time. Some functions have already been automated and some are still under development. The main thing for automation is a deep understanding of the tempering furnace and the process. The understanding of the process has improved with experimental and theoretical work. The experimental knowledge of tempering furnaces has been increased by installing more measurement points, which are installed to get the right information from the process. Also, the test runs are important to see the function of the furnace at different phases of the process. When the process is understood so deeply that based on the function of the furnace and the result of the past tempered glasses the operator knows the rules of how to adjust the parameter to get the next load better, then these rules can be automated to be set by the computer. To compare the batches all the information from individual batches is collected in a cloud database.
The procedure of the automated tempering process is shown in Figure 2. The idea is that operator gives only the input parameters about the glass and targets. Then based on the cloud information and AI (Artificial Intelligence) the process parameters are set automatically by the machine.
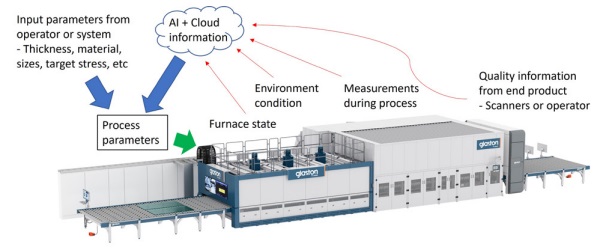
To improve the automated tempering process, it is important to know the next things when glass goes into the tempering process:
- What kind of glass will be heat-treated.
- What is the target stress level in glass (tempered or heat strengthened).
- The temperature level at the furnace.
- Environmental conditions.
For the process, it is always important to know the glass thickness, size, and total amount of glass in the batch as also, if the glass is clear, coated or it has other similar features. So far, the glass thickness and the information if the glass has coating or not, are given by the operator to the control system. The size and number of glasses are typically measured with some tolerance when loading is going to the furnace or when arriving at the loading table. All this kind of initial information is important for process control and should be informed to process already before glasses go in the furnace to prepare the furnace for the next loading. To increase the automation level of the tempering furnace this information should get automatically.
Either with separate measurements or from ERP (Enterprise Resource Planning) system. One important initial condition value is the edge quality of the glasses. If the edge quality is poor, then that must be considered in tempering parameters to get the glass to a higher temperature. The stress level, in coarse scale, can be chosen if the glass should be heat strengthened or tempered. That information is usually set by the operator, but with increased automation, the information could also be set by an ERP system. In the future, it would be possible to give the name of the standard that all the glasses should meet or even set a tighter stress range where all the glasses should be.
To help the tempering, the process should know what the state of the furnace is. E.g., the current temperature level when the next loading is planned to be sent in. Then the system could decide if it can move the next loading in or if it should wait to get the furnace to the desired minimum level. This helps to get all the glasses to a similar quality level. Also, the environmental conditions are important to know. The main information is the cooling air temperature, which affects the cooling rate. The possible change of cooling air temperature needs to be compensated with air pressure to keep the glass result constant.
Importance of automated feedback during the process and after the process
For an automated process, it is important to get feedback from the glass during the process and from the product. Information is collected to a cloud database as shown in Figure 2. During the process, there are several measurements in the furnace and the chiller. Also, the glass temperature is measured online after the furnace and after the process, the flatness, stress level, anisotropy and other needed quality values can be measured either manually or online. To optimize the process, measured information is in a huge role. This information could be used with machine learning systems for process optimization. Optimization would be easiest if one process parameter affects only one quality result, but usually, there is a combination of several process parameters which affect one quality result.
All the quality information cannot be done with automated direct measurement. For that information, the indirect measurement procedures need to be defined. As an example, this kind of information is the glass flatness in the furnace. It has been done so far only manually or tried to be analyzed from thermal scanner image. In some cases, there can also be manually defined quality values that the operator could measure and give the information to the system.
From feedback information, it is important to understand the process change and the measurement error. For this check the process condition inspection should be done regularly. This can be a reference run type check or continuous monitoring, where the measurement information is analyzed continually from long-term information. Machine condition information is important to make automated processes possible. The machine should give information or warning if some change in machine conditions is happening, especially if those affect the process. For this, the continuous monitoring of machines is important. Some changes in process can be compensated with process parameters, but if machine condition changes are too big then automated process parameter setting can be disabled.
Optimization of the tempering process
The aim of automated process optimization is to get the product quality to the target level and even further close to optimal quality. The typical quality change between the batches for operator-controlled and automatically controlled systems is shown in Figure 3.
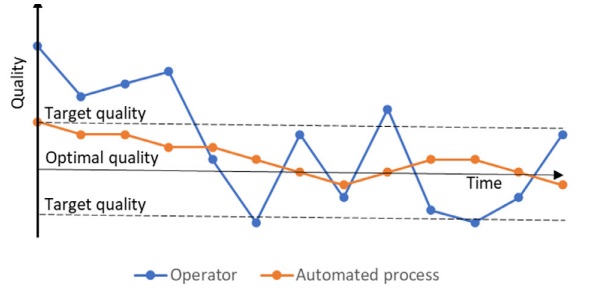
In automated systems, there are several good sides.
- The database from previous recipes from the same or similar machines can be used to get the first parameters.
- The automated process can be set to make smooth steps, not big steps.
- Takes process and environmental conditions into consideration avoiding changes only due to these condition changes.
- In mixed production consecutive batches will change and there is no time for the operator to optimize individual batch types. For automated process control, similar batches do not have to be in a row for optimization.
- Data can be extrapolated from previous data to new products and sizes.
In the process of optimization, the main target is that all the glasses should meet the standards. Usually, there is a recipe database where a possible initial recipe for the next batch can be found based on the information of the input parameters. After one batch this recipe is optimized for the next similar batch with the end quality values.
The target for optimization can also be more specific. Target can be e.g., set stress range, set flatness level, or set anisotropy value. Then again, the past database is used to find the best recipe to achieve the target quality for the glasses with the best production rate and yield.
Conclusions
The advance of the new operating model where the operator only gives the initial information about the batch and the target is the productive way to increase the average quality of the tempered glass and makes operators’ work easier. This model needs high-level automation and machine learning to optimize the process parameter setting. The information collected from the process and product is in a key role in the entire process optimization.
The tempering process has been heading in this direction already during the last few years, but the full potential of the new operating model has not been achieved yet. The information from the process needs to be well defined and the right method to analyze it is needed to get the right model or correlation to optimize the parameters. The knowledge and understanding of the tempering process have a significant role to improve this automatization. The increased automatization level increases also the importance to keep the tempering furnace in good condition. Broken heating elements or other parts change the optimization of the process and can head in the wrong direction. Measured information needs to be used also to find the broken parts in the system for maintenance and keep the furnace working level high.
Even though the automation level in the tempering furnace is increasing, complete automatization, so that all the possible glasses could be tempered automatically, is still far away because new tempered glass products are also being developed at the same time. These new products keep glass processors and operators on their toes and process experts are still needed.
References
[1] ASTM C1048-18: Standard Specification for Heat-Strengthened and Fully Tempered Flat Glass, ASTM International, 2018.
[2] SFS-EN 12150-1:2015: Glass in building. Thermally toughened soda lime silicate safety glass. Part 1: Definition and description, SFS, 2015.
[3] Aronen, A., Karvinen, R. Effect of glass temperature before cooling and cooling rate on residual stresses in tempering. Glass Struct Eng 3, p. 3–15, 2018. https://doi.org/10.1007/s40940-017-0053-6
[4] Le Bourhis, E., Glass: Mechanics and Technology, John Wiley & Sons, 2nd Ed., 2014.
Comments
Changing the tempering process control from settings to specifications involves a shift from arbitrary adjustments to precise, predetermined parameters. This transition ensures consistency and quality by aligning operations with defined standards rather than relying on variable settings. It enhances efficiency, reduces variability, and facilitates easier troubleshooting, ultimately improving overall process reliability. Chicago elevator service
Usually, there is a recipe database where a possible initial recipe for the next batch can be found based on the information of the input parameter.
The paper highlights significant progress in the automation of the glass tempering process, emphasizing the role of increased data collection and advanced technology in improving process control. By transitioning to systems that automatically adjust parameters based on desired product targets, the industry can enhance both the efficiency and quality of tempered glass production. Continued advancements and research in this area promise to further refine the tempering process, potentially overcoming current limitations and meeting higher standards of glass quality. SEO expert Cincinnati
The paper on glass tempering, presented at GPD 2023 by Antti Aronen, Sami Kelin, and Pekka Lyytikäinen, explores the tempering process, which is traditionally guided by operator experience rather than science. It discusses the challenges of meeting glass standards while optimizing production, yield, and visual quality. Automation is seen as the future, where machines could self-adjust based on product targets, minimizing operator intervention. Advanced measurement tools and increased automation could streamline glass tempering, ensuring consistent quality. parking lot paving naples fl
That's interesting. I've always wondered about the science behind tempered glass. It's cool how much experience plays a role in the process. I guess it's a bit of an art form, huh?
Paul | Spinal decompression naples
This article is very educational. I've always wondered how things are done including this tempered glass and now I am enlightened just how awesome it was made. Thank you so much for sharing such relevant information.
Residential Dumpster Rental
This paper presents an interesting perspective on the future of glass tempering, emphasizing the shift from operator-driven processes to automation-driven optimization. The idea of machines selecting tempering parameters based on desired product specifications rather than manual adjustments could significantly improve consistency, efficiency, and quality. BHI General Contracting