Source:
Challenging Glass 7
Conference on Architectural and Structural Applications of Glass
Belis, Bos & Louter (Eds.), Ghent University, September 2020.
Copyright © with the authors. All rights reserved.
ISBN 978-94-6366-296-3, https://doi.org/10.7480/cgc.7.4491
Author:
David Antolinc - University of Ljubljana, Faculty of Civil and Geodetic Engineering, Slovenia
This paper presents the experimental results of a three-point bending test conducted on laminated glass at elevated temperature in an environmental chamber. The focus of the present research was on bending stiffness degradation of the laminated glass in correspondence to elevated temperature. The tested specimens were made of two fully tempered glass plates bonded with EVA and PVB interlayers.
For each type of laminated glass and set temperature, we prepared and tested 5 specimens. Each of the specimen was preconditioned to a set temperature before the experiment conduction in an environmental chamber. The tests were conducted at 23°C, 35°C and 60°C after the specimens had reached the defined contact temperature. During the experiment,the midspan deflection, longitudinal midspan deformation and the force at midspan were recorded.
In the end, the behaviour of two different types of laminated glass plates was compared based on measured midspan deflection, deformations and stiffness degradation. Based on the results it can be seen that the laminated glass with EVA interlayer behaves stiffer and that the stiffness degradation is almost linear and slower in comparison to the specimens with PVB interlayer.
1. Introduction
Structural glass in the form of laminated glass can have a different interlayer as binding material. Usually, PVB, EVA and more often in recent years inomer commercially labeled as Sentry Glass (SG) interlayer is used. Although quite extensive research on the behaviour of laminated glass with PVB and SG interlayers at various temperatures has been done, more research is needed for the laminated glass with EVA interlayer made by different manufacturers, which is also mentioned in (Serafinavičius et al. 2013) and more recently in (Martin et al. 2019) and (Sable et al. 2017).
It is clearly shown in (Sable et al. 2017) that the mechanical behavior of laminated glass with EVA interlayer is greatly influenced by the laminating temperature and curing time. Because there are limited experimental data recorded on the EVA laminated glass, we decided to conduct experimental research on this topic.
One of the first studies dealing with the temperature influence on the mechanical behaviour of laminated glass subjected to bending loading was done by Krüger (1998), who studied laminated glass with PVB interlayer only and demonstrated that the interlayer at temperatures above 40°C provides very small or no coupling between bonded glass sheets.
The comparison between PVB and EVA interlayer laminated glass subjected to short term bending load at temperatures of -20°C, 23°C and 60°C was studied by Pankhardt (2010). This study again demonstrated that the flexural stiffness of laminated glass is greatly influenced by the ambient temperature and it decreases with rising temperature. There is a large temperature step between 23°C and 60°C, which is why we decided in our study to investigate and compare the behavior for at least one more temperature at 35°C, as will be explained later.
Another important study and experimental analysis of laminated glass exposed to the temperatures of 20°C, 30°C and 40°C and loaded with long term four-point bending load of laminated glass with PVB, EVA and SG interlayers was conducted by Serafinavičius et al. (2013). They came to the conclusion that the specimens with both EVA and SG interlayers provide a relatively similar stable and stiff behavior in comparison to the specimens with the PVB interlayer where the largest deflections and tension strains at the laminated glass midspan bottom surface were recorded.
The EVA interlayer used in the research was from the Bridgestone Corporation and was named EVASAFE. As there are several manufacturers on the market, the author made a remark in the conclusions that in the further research also EVA interlayers of other manufacturers should be tested, which encouraged us to use the EVA interlayer with the brand name DayLight EV200 from the manufacturer Glaast Gmbh.
Based on previous experimental analyses of laminated glass at different temperatures under bending loading done by other authors and based on the capacity of our environmental chamber,we decided to conduct the three-point bending loading for short laminated glass specimens. One of the main motivations to conduct the present study was the lack of experimental results available in the literature and to clarify the failure mechanisms of laminated glass exposed to elevated temperature under short term load, which can easily occur in the case of a laminated bridge deck or balustrade on a hot summer day, as shown in Figure 1.
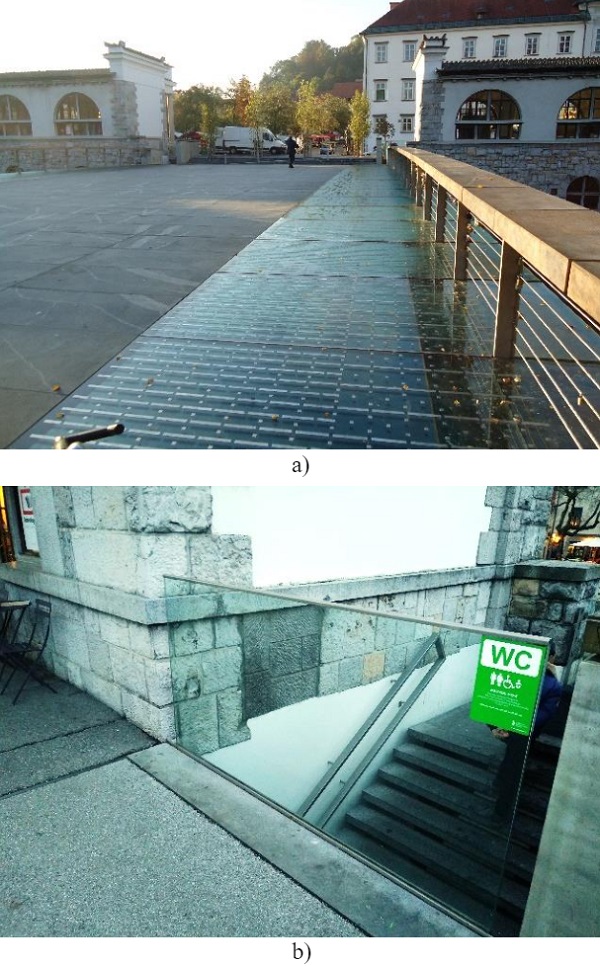
2. Overview of the test setup and the specimens
2.1. Test specimens
Two types of laminated glass specimens were prepared for three-point bending test, one with PVB and the another one with EVA DayLight EV200 brand interlayer. Specimens were assembled with two 350 mm long and 100 wide heat strengthened soda-lime silicate glass sheets, each with thickness of 5 mm with polished edges. The thickness of the polymer interlayer was 0.76 mm for both interlayer types (PVB or EVA).
The overall dimensions of the specimens were limited to the dimensions of the environmental chamber. Sets of five specimens were prepared and tested for each type of specimens and also for each level of ambient temperature of 23°C, 35°C and 60°C. Thus, altogether 15 specimens with EVA and 15 with PVB interlayers were prepared and tested. Bottom surface of each specimen was equipped with the strain gauge at the mid span and 30 mm from the lateral edge, oriented longitudinally to measure the maximum tension deformation during the test. One set of specimens is shown in Figure 2a), while in Figure 2b) the position of longitudinal strain gauge at the midspan is shown.
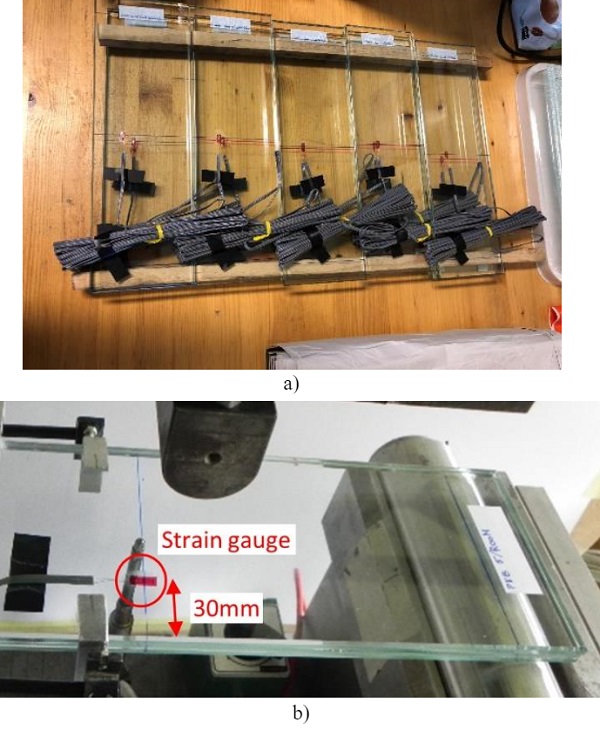
2.2. Test methods and procedure
To evaluate the temperature effect on the bending stiffness and strength of the considered laminated glass specimens,we conducted the three-point bending test with the dimensions and equipment as shown in Figure 3 and Figure 4. The span between the supports is 300 mm. The deflection at the midspan of the specimen was captured with the LVDT. Vertical load F was applied at the midspan with the loading rate of 4.8 mm/min until total failure of the specimen.
As mentioned above, three levels of ambient temperature were set for testing, 23°C, 35°C and 60°C. We set the temperature of 60°C as maximum temperature that can be expected in severe environmental circumstances in real civil engineering applications. For the future it is recommended that at the temperature level of 80°C the experiments are conducted according to the guideline ETAG 002 and the study conducted by the Santarsiero et al. (2017).
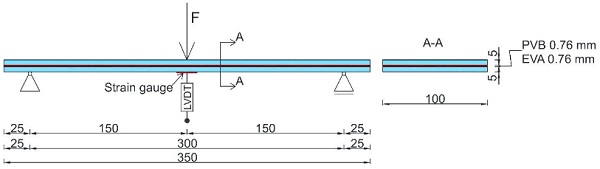
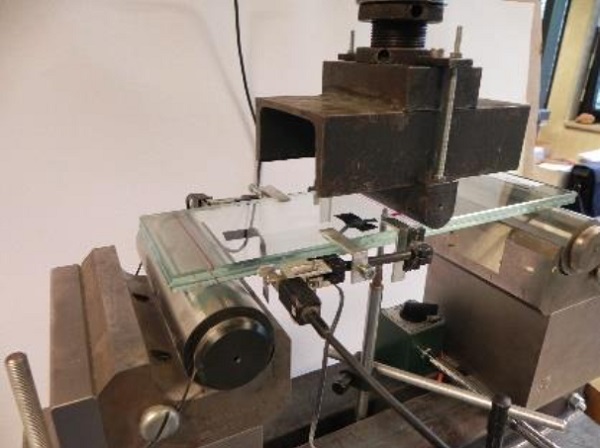
The dimensions of the specimens were limited with the size and capacity of the environmental chamber. Therefore, the maximum length of the specimen was 350 mm. For the experiment at the room temperature of 23°C, we did not use the environmental chamber, as can be seen in Figure 4. The operating range of the environmental chamber is between -150°C and +600°C, which enabled us to set the desired elevated temperature at +35°C and +60°C.
For each desired temperature we preheated the chamber and the specimen to the set temperature level. For this reason, we placed the specimens in a separate heating chamber for 24 hours to preheat them to the desired temperature and then we moved them to the preheated environmental chamber to conduct the three-point bending test. Thermocouple was used to check the contact temperature of the specimen.
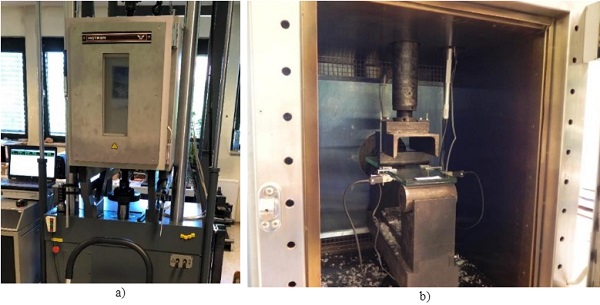
3. Experimental results and discussion
One of the main characteristics of laminated glass is that it has the ability to hold together broken glass fragments after the tensile strength of the glass has been exceeded and thus provide improved post-breakage behaviour that keeps the broken laminated glass sheet in place. The specimens with the PVB interlayer in our research showed that PVB has the capacity to connect the fragments after the glass breakage at ambient temperature of 60°C. Figure 6a) and b) shows the PVB laminated glass failure mode at 35°C and 60°C, respectively.
It is obvious that at 60°C the viscosity of PVB drops substantially, as the bending post-breakage stiffness is very low and can represent potentially hazardous behaviour. The specimens with the EVA interlayer showed similar failure modes, except at the ambient temperature of 60°C where all of the samples fell into two pieces, as shown in Figure 6c), which is very problematic in the case of overhead glazing, because it can fall down on the occupants.
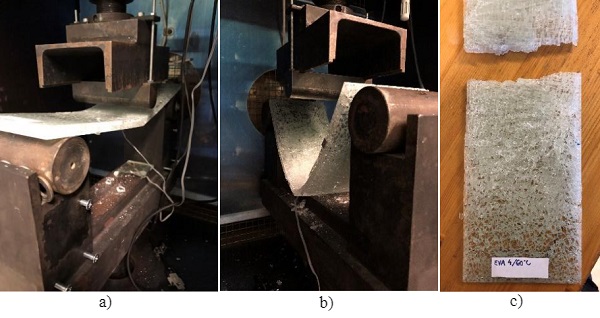
Based on the measured values of midspan deflection and the corresponding applied force, Figure 7 shows the bending stiffness of the laminated glass specimens with the PVB and EVA interlayers at ambient temperatures of 23°C, 35°C and 60°C. In all of the following diagrams the blue curve represents the results for the specimens with the EVA and the red curve the specimens with the PVB interlayer.
The specimens with the EVA interlayer generally show higher stiffness at most ambient temperatures compared to the specimens with the PVB interlayer, while it is very close at the temperature of 60°C. The glass transition temperature Tg of polymeric materials plays an important role in the temperature dependent behaviour of EVA and PVB interlayers because it indicates a temperature range in which the stiffness of the material decreases significantly (Kuntsche et al. 2019).
However, the average stiffness of the specimen with the EVA interlayer at room temperature is 0.5 kN/mm, where as with increasing ambient temperature it almost linearly drops down to 0.29 kN/mm. This behaviour corresponds to almost linear stiffness degradation of EVA interlayer in the temperature range from glass transition temperature Tg at -28°C up to the crystal melting temperature Tm at 70°C.
Meanwhile, the largest share of the stiffness degradation for the specimens with the PVB interlayer, which is related to the viscosity of the interlayer, happens within the temperature range of 23°C and 35°C and it drops from 0.34 kN/mm down to 0.27 kN/mm, respectively. In the temperature range from 35°C to 60°C only small degradation of stiffness down to 0.25 kN/mm is recorded. This behaviour corresponds to the fact that the glass transition temperature Tg of the PVB interlayer is at 38°C.
This is very close to the temperature of 35°C at which we tested our specimens and where the largest share of stiffness degradation occurred on our specimens. We can conclude that the interlayers have different behaviour due to different viscoelastic properties at the considered ambient temperatures and the values of stiffness for EVA and PVB laminated glass get very close to each other at the temperature of 60°C.
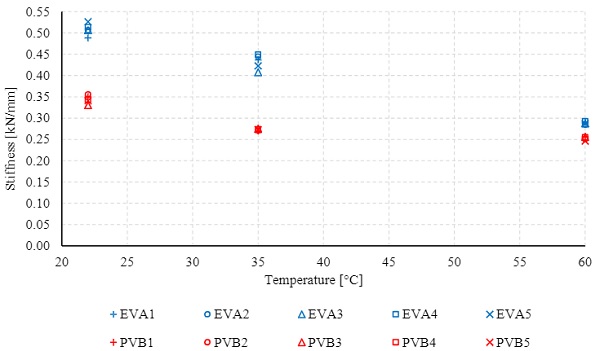
Figure 8 shows tension stresses evaluated at the bottom surface of the specimens, which are the consequence of the applied midspan bending load F=2.45 kN. This is the average failure load for the specimens with the PVB interlayer at the ambient temperature of 60°C. Since this is the lowest average load bearing capacity of all considered specimens, we took it as a reference force for other specimen at all ambient temperatures.
Tensile stresses were evaluated based on the measured tensile deformations at the midspan of the loaded specimens and are shown in Figure 9. It is obvious that the tensile stresses of the specimens with the PVB interlayer at 60°C are the same compared to the laminated glass with zero interlayer stiffness, which is represented with the dashed black line in Figure 8.
This means that the PVB interlayer at the ambient temperature of 60°C lost the shear stiffness almost completely. On the other hand, the remaining shear stiffness of the EVA interlayer at 60°C still enabled the coupling effect between the glass sheets. Thus, the average tension stresses were lower by approximately 15% compared to the stresses obtained on specimens with the PVB interlayer.
We can also see that the tension stresses evaluated on the specimens with the EVA interlayer do not change substantially in the temperature range between room temperatures of 23°C and 35°C, which means that in this temperature range the viscosity of the EVA interlayer does not change essentially. However, the specimens with the PVB interlayer showed that with increasing temperature from room temperature to 35°C, also the shear stiffness (shear modulus) of the interlayer changed and thus also the tensile stresses in the bottom glass sheet.
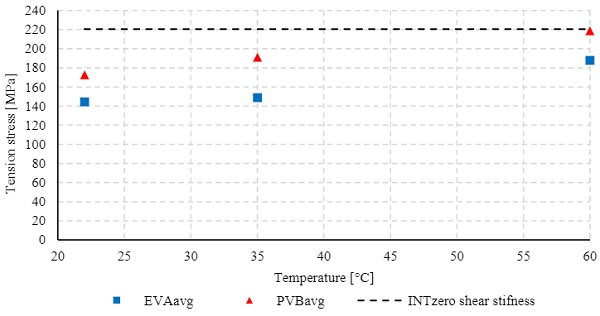
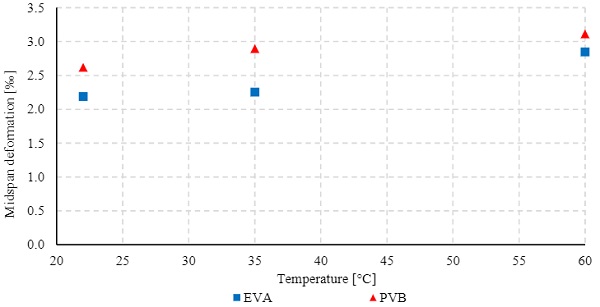
Figure 10 and Figure 11 show the average load bearing capacity and the corresponding midspan deflection of the laminated glass specimens at different temperatures, respectively. Again, the comparison is made for the specimens with the PVB (red curve) in the EVA (blue curve) interlayers. The average load bearing capacity through the whole range of the tested ambient temperatures is higher for the specimens with the EVA interlayer and it decrease almost linearly with the increase of the ambient temperature.
However, the specimens with the PVB interlayer exhibit decrease of load bearing capacity from 2.8 kN to 2.57kN in the range of temperature from 23°C up to 35°C. It is also obvious that the load bearing capacity stays almost unchanged at higher temperature of 60°C, which was reached on average at 2.54 kN.
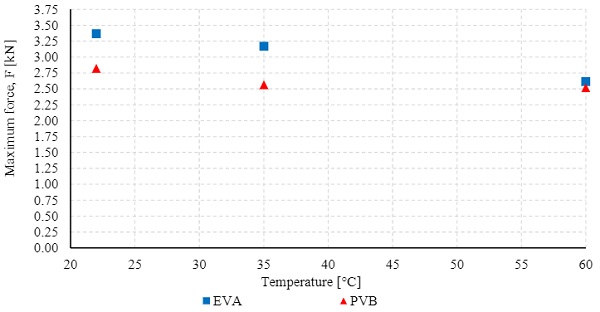
The diagram in Figure 11 shows midspan deflection corresponding to the average load bearing capacity for the considered specimens. Due to the higher stiffness of the specimens with the EVA interlayer, the deflections of those specimens are smaller through the entire range of elevated temperature. The deflections increase along with rising temperature almost linearly, which also corresponds to the stiffness diagram in Figure 7.
Similar correlation with the stiffness development regarding the temperature level canal so be made for the specimens with the PVB interlayer. The deflection of w=10.2mm at the temperature level of 35°C stays almost the same with the temperature rising up to 60°C, where it increases to w=10.45 mm, which is again in agreement with the bending stiffness of the specimens with the PVB interlayer shown in Figure 7.
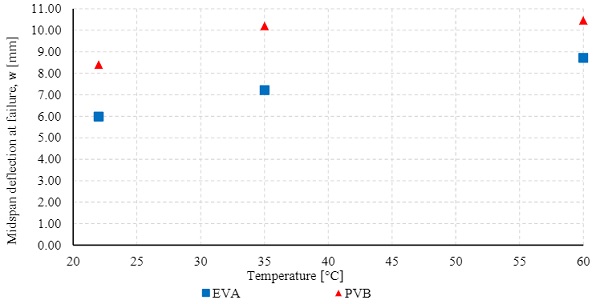
4. Conclusions
Based on the literature review, it is possible to get limited selection of information on the behaviour of laminated glass under elevated ambient temperature. Most of them have studied the influence of temperature on laminated glass behaviour under long term load or the comparisons of behaviour under short term loading at elevated temperatures, unlike the present study.
The lack of experimental studies and behaviour comparisons of laminated glass with the PVB and EVA interlayers at elevated ambient temperatures encouraged us to prepare the present study and experimental analysis. Three-point bending tests of laminated glass with the PVB and EVA interlayers at room temperature and two increased temperatures were conducted, where the following conclusions can be made:
- Laminated glass with the EVA interlayer tends to break and fall into two separate parts at ambient temperature of 60°C, which shows unfavourable behaviour in comparison to specimens with the PVB interlayer. The specimens with the PVB interlayer lost the post-breakage bending stiffness but it remained in one piece.
- Stiffness degradation of laminated glass with the EVA interlayer is on average linear regarding the temperature increase. However, the main change in shear stiffness of the PVB interlayer in regards to the room temperature happened at 35°C without any significant further change at higher temperature of 60°C. This behaviour of laminated glass also corresponds to the glass transition temperature Tg (38°C) of PVB interlayer at which substantial material stiffness degradation occurs.
-Overall stiffness of the specimens with the EVA interlayer is approximately 35% higher at room temperature and 35°C. At the highest testing ambient temperature of 60°C the stiffness of both specimen types gets very close, where those with the PVB interlayer exhibit only 7% lower stiffness in comparison to the EVA interlayer specimens.
- The average tension stresses at the midspan of bottom glass sheet for specimen with the PVB interlayer are higher, as expected, in comparison to specimens with the EVA interlayer, due to the lower coupling effect between glass sheets. The tension stress of the specimen with the PVB interlayer at the ambient temperature of 60°C is practically the same as for the laminate with zero stiffness interlayer.
- Load bearing capacityof the specimen with the EVA interlayer is linearly decreasing with increasing temperature. The load bearing capacity of the specimen with the PVB interlayer is 16% and 19% lower at 23°C and at 35°C, respectively comparing to the specimens with EVA interlayer. As the stiffnesses of both types of laminates are at 60°C very close to each other, also the load bearing capacities do not differ greatly.
Laminated glass with the EVA interlayer exhibits more favourable overall behaviour at the elevated temperature, in comparison to the specimen with the PVB interlayer. The only shortcoming of the EVA interlayer is its tearing at the temperature of 60°C. Further research of bending laminated glass with smaller temperature step is recommended, as well as at temperatures below room and sub-zero temperatures.
5. Acknowledgements
The present experimental research on the influence of temperature on the laminated glass behaviour was conducted under author’s supervision within the diploma thesis with the title “Behaviour of laminated structural glass at elevated temperatures”, which was conducted and prepared by the graduation candidate Ms. Maksi Podobnik (Podobnik 2019). Her contribution to this research is greatly acknowledged.
6. References
ETAG 002 –guideline for European technical approval for structural sealant glazing systems (SSGS) Part 1: supported and unsupported system. European Organisation for Technical Approvals (2012)
Brackin, S., M.: Development of a procedure to evaluate the shear modulus of laminated glass interlayers. Master thesis. Texas A&M University, Civil Engineering (2010)
Haldimann, M., Luible, A., Overend, M.: Structural Use of Glass. IABSE, Zürich (2008)
Krüger, G.: Temperature effects on the structural behavior of laminated safety glass. Otto-Graf Journal. Vol. 9, 153-163 (1998)
Kuntsche, J., Schuster, M., Schneider, J.: Engineering design of laminated safety glass considering the shear coupling: a review. Glass Struct.Eng.(2019). doi:10.1007//s40940-019-00097-3
Martin, M., Centelles, X., Solé, A., Barreneche, C., Fernández, A., I.: Polymeric interlayer materials for laminated glass: A review. Constr.Build.Mater.(2019). doi:10.1016/j.conbuildmat.2019.116897
Pankhardt, K.: Temperature dependent flexural stiffness of load bearing laminated glass panes. Periodica Polytechnica Civil Engineering (2010). doi:10.3311/pp.ci.2010-2.07
Pankhardz, K., Balázs, G., L.: Temperature dependent load bearing capacity of laminated glass panes. Periodica Polytechnica Civil Engineering (2010). doi:10.3311/pp.ci.2010-1.02
Podobnik, M.: Behaviour of laminated structural glass at elevated temperatures. Graduation thesis. University of Ljubljana, Faculty of Civil and Geodetic Engineering (2019)
Sable, L., Skukis, E., Japins, G., Kalnins, K.: Correlation between numerical and experimental tests of laminated glass panels with visco-elastic interlayer. Procedia Eng.172, pp. 945 –952. Elsevier (2017)
Santarsiero, M.,Louter, C., Nussbaumer, A.: Laminated connections under tensile load at different temperatures and strain rates. Int.J.Adhes.Adhes.(2017). doi:10.1016/j.ijadhadh.2017.09.002
Serafinavičius, T., Lebet, P., J., Louter, C., Lenkimas, T., Kuranovas, A.: Long-term laminated glass four point bending test with PVB, EVA and SG interlayers at different temperatures. Procedia Eng.57, pp. 996 –1004. Elsevier (2013)
Serafinavičius, T., Kvedaras, A., K.,Sauciuvenas, G.: Bending behavior of structural glass laminated with different interlayers. Mech. Compos.Mater.(2013). doi: 10/1007/s11029-013-9360-4