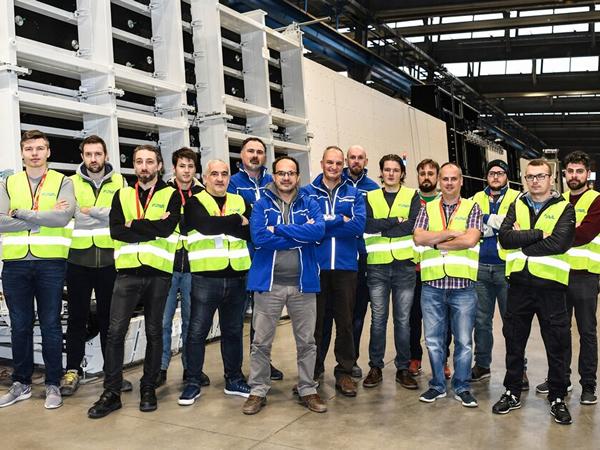
Date: 19 December 2019
Participants included the company's direct collaborators and those of partner agencies and customers' glassworks. An international group, hailing from the United States, Spain, the UK, Russia, Poland and Italy: the training sessions were provided at Forel headquarters in Treviso (IT), allowing for a mix of classroom sessions and practical demonstrations with working machinery.
The main – and extremely practical – training topic was the double glazing line, Forel's core business: in addition to illustrating new devices and the improvements introduced in the most recent models, Training Week provided an important opportunity for a deeper look at possible issues and at the most common maintenance operations required by complex systems. In order to offer participants the broadest perspective possible, the teachers were senior technicians from the technical office, from production and from service dept.
“Forel's decision to invest in continuous training for its technicians is the key to customer loyalty,” noted Franco Walter, Forel Service Manager “Customers who purchase our products rely on after-sales services that are complete, functional and always up to date. Great effort and care are, of course, needed to prepare the people tasked with providing assistance. Training sessions are held at Forel's main headquarters – where all of the systems that participants will work on are manufactured – in order to ensure that every glassworks will be served by skilled professionals who can solve problems in as little time as possible. The courses themselves are provided by the very people who designed, assembled, tested and inspected those machines over the years. Our Training Week, which consists of 3 sessions each year, guarantees the professionalism and preparation of our service network: it's an additional step we take to support our customers. A service that is recognised and appreciated all over the world”.
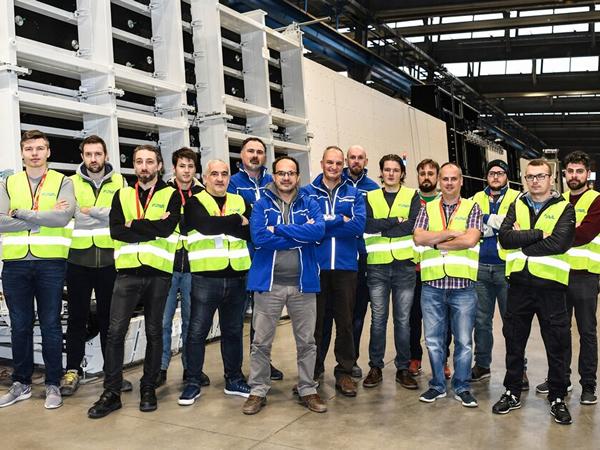

Add new comment