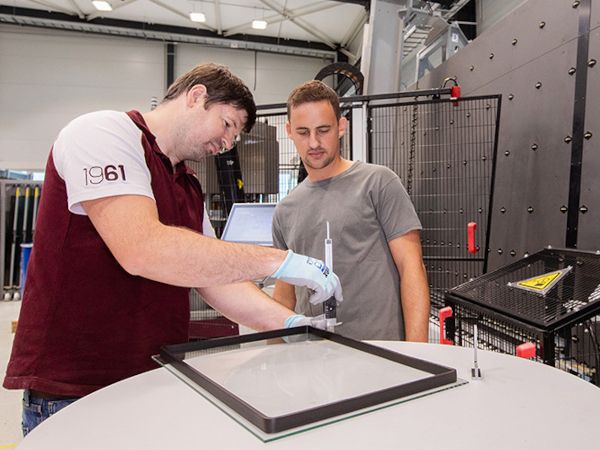
Date: 11 July 2025
LiSEC training courses are designed to equip customers with the knowledge and skills needed to fully leverage the potential of LiSEC solutions. The company has compiled a list of the most frequently asked questions from its TPA training course, intended for both newcomers and those looking to refresh their knowledge.
- Is it possible to reuse the material that has been drained into the collection drum?
To guarantee the quality of the TPA spacers, the material must be applied to the glass sheet at the correct temperature. After the machine has been at a standstill, a certain amount of TPA material must be drained until the correct temperature is reached. The TPA material contains a desiccant that is activated on contact with air, after which it can no longer be used. As such, it is not possible to reuse the drained material.
Tip for users! To prevent the TPA material from sticking to the collection drum, you can line the drum with the protective film that covers the surface when you open a TPA material drum. This makes cleaning much easier later on.
- The menu contains presets for different spacer widths. Can I also define my own spacer width?
The machine operator can create their own recipe for an individual spacer width. The simplest way to produce a 7 mm wide spacer is to clone the recipe for a 6 or 8 mm wide spacer. The recipe parameters must then be fine-tuned to avoid unsightly corners or deformations. The recommended settings sequence is: First check the straight lines, then the quantity, followed by the spacer width, corners and finally the closure.
Tip for users! If you know the desired widths in advance, you can request customised recipes when ordering the machine. These recipes will then be tested before the machine is delivered.
- Does the TPA material have to be black?
Alternatives are being researched, but black material is currently the best option because it does not become brittle due to UV radiation. Depending on the method of installation, the colour only slightly impairs the aesthetic properties of the insulating glass unit.
- I would like to increase production. Can I speed up the application of the TPA material?
The nozzle application speed automatically adjusts to the quantity of material flowing through it. More material results in a faster application speed, while less material means a slower application speed. This ensures that the application remains precise and consistent. The LiSEC TPA line offers other options for increasing production capacity: Counter sheets can be transported past the application head to reduce waiting times for applications.
- What do the TPA spacers look like at the seam? Can the closure be implemented in a clean and gas-tight way?
Technical tricks exist for closing TPA spacers cleanly and in a gas-tight manner, such as a pressure equalisation point and precisely adjusted offsets. The closure is made narrower and pressed to the desired width in the press, after which it is pulled apart with clamps to ensure that it expands correctly.
- What is the point of the material storage tank? Is it not possible to feed the TPA material directly from the drum to the nozzle?
The material storage tank acts as an intermediate link between the drum and nozzle to guarantee optimum processing of the material. It ensures that the TPA material can settle and acclimatise before it reaches the nozzle and facilitates temperature regulation. The material storage tank also serves as a pressure boosting station to build up the pressure required for the application. Seamless production is possible with two material storage tanks (20-25 l each): While the first storage tank is being used for production, the second can be filled with new material.
- I am considering changing material manufacturer. What cost and workload can I expect if I decide to do so?
The material behaviour varies depending on the manufacturer. Before delivery, all recipes are tested with the material specified by the customer and the machine is calibrated accordingly. When changing the material manufacturer, the old material must be rinsed out and the machine recalibrated for all 8 standard spacer widths. This requires about a 200 l drum and one day. We recommend requesting the support of a LiSEC technician or a specially trained employee for calibration.
Tip for users! When placing your order, LiSEC offers the option of specifying several material manufacturers and storing tested recipes for each respective manufacturer. Have your favourite supplier saved!
Some suppliers will support the changeover on site and train your personnel on the material specifications and characteristics. Ask your new supplier about this service.
- What quality features should I look out for to ensure optimum adhesion between the TPA spacer and the glass?
TPA material is processed at 130°, after which it has a consistency similar to chewing gum. The quality can be visually checked immediately after application. The TPA material should be black, glossy and evenly applied to the glass. The material must first expand on the counter sheet and establish a chemical bond with the glass. Freshly applied spacers are light grey and even, without air bubbles, while fully expanded spacers are black and shiny. The permissible expansion time is specified in the manufacturer's processing guidelines. If the desired results are not achieved within the specified time, the application process must be checked.
- The material manufacturer's label contains a lot of information. What details are important to me?
When changing to a new drum, the batch number on the label of the TPA material drum is most important. TPA material is mixed in batches of around 4 to 8 drums. As there may be slight differences between batches, it is advisable to use up all of the supplied batches and to check the recipes when switching to a new batch.
Tip for users! In the TPA program, you can enter the batch number in the production data for each drum. In the event of a complaint, this makes it easy for you to trace whether an entire batch has quality defects.
- Recipe settings are being implemented on my TPA line. What equipment do I need to have on hand for this?
TPA application quality checks are carried out during the machinery set-up, adjustment work and on-site technician visits. The main tools required here are a digital sliding gauge for measuring the spacer height and width, and a small angle stop for checking the right angle to the glass sheet. This is particularly important for wider spacers due to their higher dead weight. Also useful are test sheets in various sizes, a high-quality measuring tape, markers for defining measuring points, cleaning paper, isopropyl alcohol and a drum for collecting the used test material.
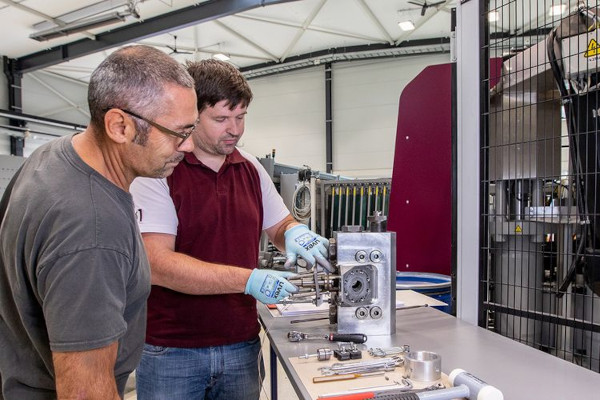
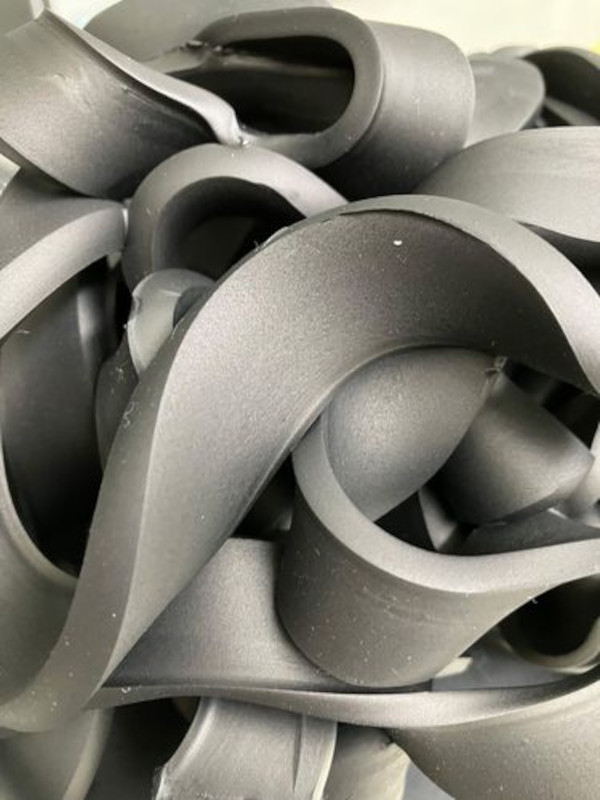
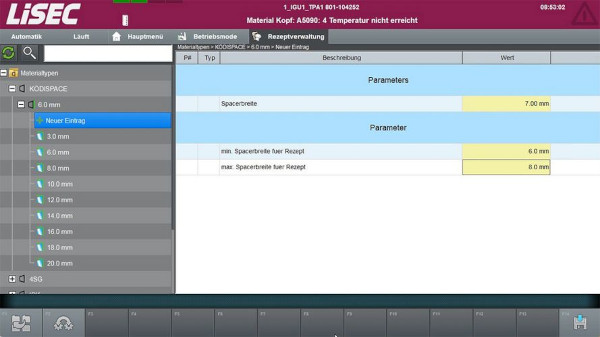
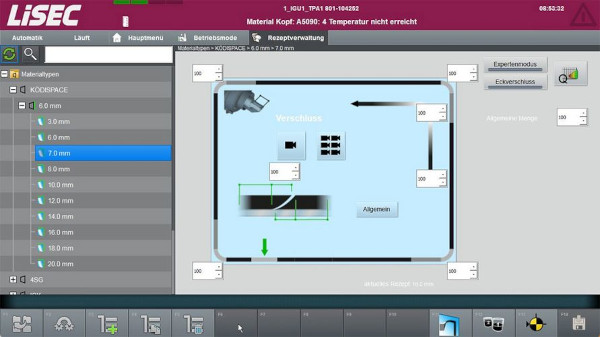
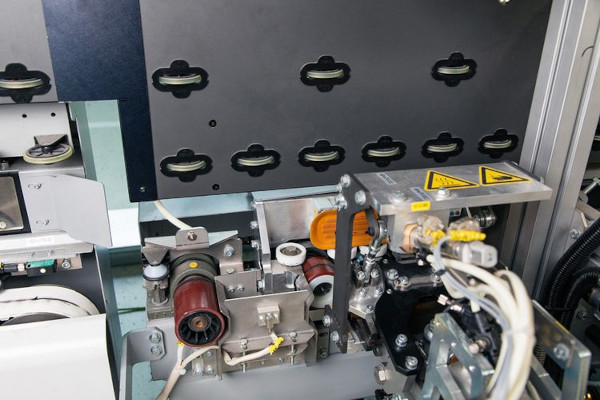
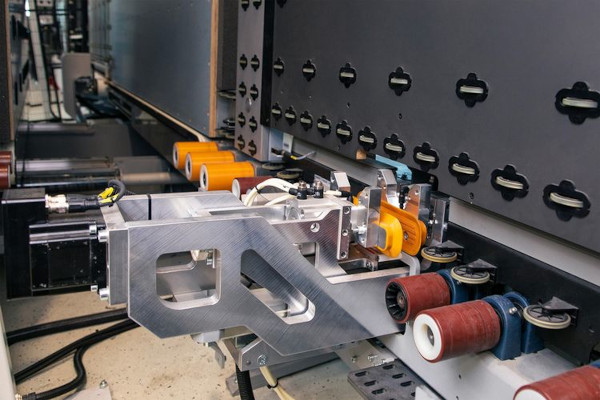
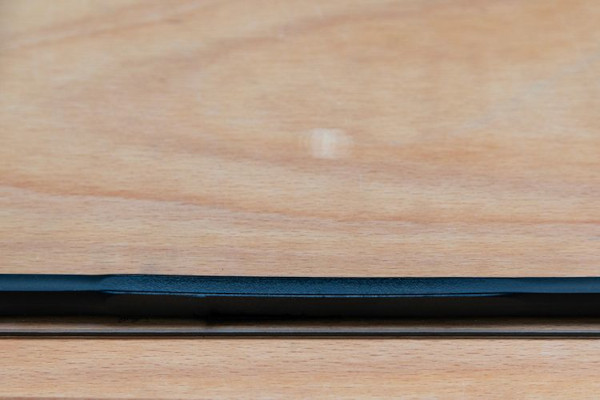
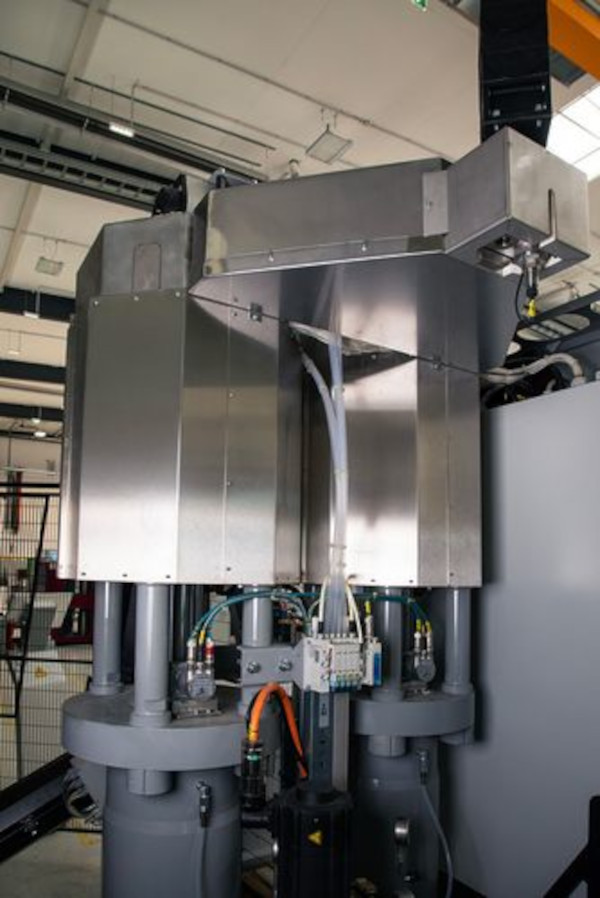
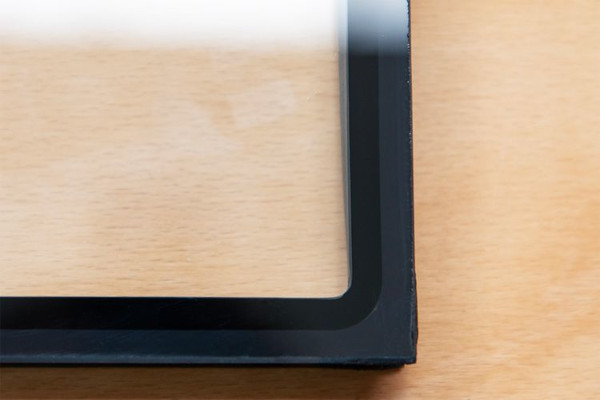
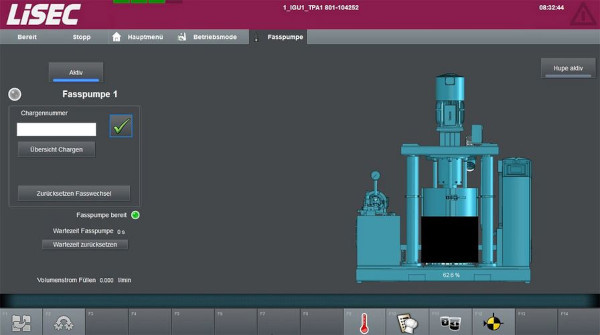
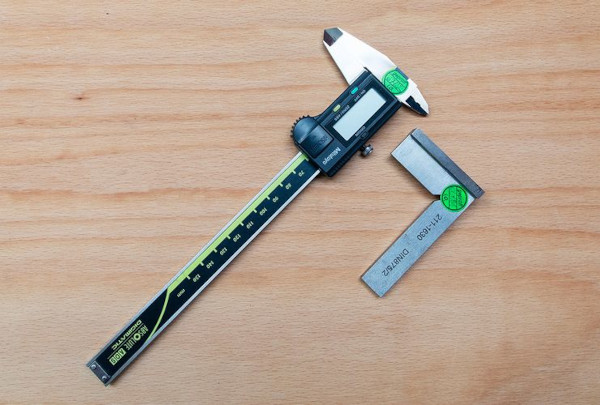
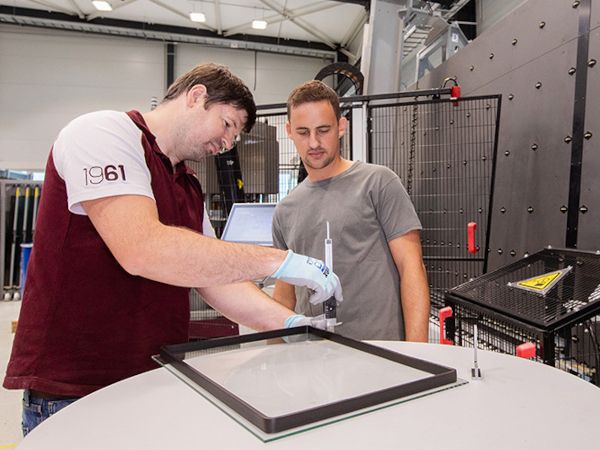

Add new comment