First presented at GPD 2017
1 Relevance of double skin facades in todays industry
The construction typology of the curtain wall arose with Joseph Paxton’s Crystal Palace and accelerated in the 20th century. Separating a building’s enclosing wall from its structure enabled an independent development of façade and structure, greater flexibility in design and incredible lightness of buildings. [1-3]
Initially, growing demands on user comfort, energy efficiency and maintenance were managed by technical advances in the performance of glazings, materials, jointing elements, and air conditioning. Advances in precission manufacture allowed the development of unitised systems, realizing cost and programme benefits through prefabrication and preassembly.
These developments influenced the classical massive wall constructions. Multi-layer or cavity walls were adapted to increase flexibility by seprating cladding and structure, gaining advantages through pre-assembled panels. [1-3] Figure 1 shows the mentioned construction typologies in principal.
Triggered by the energy crisis in the 1970’s, it was tried to increase user comfort in highrise buildings through natural ventilation. Rising demands for noise protection made double skin facades popular. This typology however was developed in the early days of the 20th century with the production hall of Steiff in Giengen on the Brenz, Germany and the Hallidie Building in San Francisco. [5]
Double skin facades usually use two layers of glass that air can flow in the intermediate cavity. Natural ventilation of the cavity, a fan supporting air circulation, or mechanical driven ventilation flaps are necessary to exclude overheating and condensation. The different and manifold parts make stick, double skin and unitised systems one of the more costly element of a building. [3]
Unitised facades dominate the curtain wall market especially for high-rise buildings because of the time saving on site, advantages for installation access, cost-savings by a semiautomated production for many equal units, and the quality improvements through preassembled products in a factory. Stick systems are typically used for low-rise buildings, entrance areas, or smaller developments. [1-3]
The improvement of curtain wall systems is related to the advancements made on frames, fillings, and sealants. Dimensions, durability, and anchoring techniques are improved to realise lighter constructions, allowing increased element sizes up to 3.2 x 15 m. Fabrication technology allows the production of bigger pane sizes, client-specific geometries, combinations of multilayer laminated safety glass or insulation glass and glass setups with different functional coatings. [1,6]
Desktop studys and calculations allow the assessment of the structural and physical performance during design.
As outlined before, a main driver for the ongoing development was an increasing awareness for energy saving. Improvements in coatings and double and triple layer insulation glass reduced the thermal losses through the transparent areas of a building.
This impacts as side-effect the visual quality of glazed facades. The cavity of double skin systems operates as thermal buffer and reduces the need for eye-catching coatings. Double skin facades using natural ventilation for high-rise buildings had advantages in user comfort and a greater transparency.
On contrary, double skin facades are faced with higher maintenance and cleaning cost. In design, increased wall zoning requirements lead to a reduced floor area available for usage and rent. [5]
Ongoing challenges are energy performance, the upcoming need to reduce the resource consumption, and to balance economical and user comfort demands in the most beneficial way. Different site conditions and holistic evaluation of economical, ecological and social aspects leads to a very multidimensional design task choosing the most reasonable solution.
The integration of the double skin concept within a unitised system is one of the latest developments. They are closely related to room-high box-type windows and exclude some major disadvantages of classical double skin concepts. An individual exchange of units is possible as well as reduced cleaning efforts to gain comparable maintenance cost to classical curtain wall systems.
The minimized width of the construction increases lettable floor space. Modern unitised double skin facades combine opaque and glazed multilayer constructions.
![Figure 1: Multilayer, rear-ventilated, stick and unitised construction alternatives [4]](/sites/default/files/inline-images/Fig1_3.jpg)
2 Concepts of double skin facades
Double Skin Façade is a generic term for transparent, translucent or opaque constructions, which typically use decoupled layers of construction elements or material. Two main constructive principals of curtain walls are used for double skin façades. Stick systems are dominated typically by natural ventilated concepts.
Unitised systems are dominated by box type windows, which have the possibility to clean the interior panes, or by closed-cavity and self-conditioning facades, which reduce the cleaning effort for the interior panes. Concepts integrate heating, ventilation, air conditioning, shading, and sound insulation, reducing energy consumption and increasing user comfort.
Functions, typically realised with energy consuming indoor installations, are moved into the façade to gain benefits of natural heat buffering and ventilation. Double skin facades serve various façade orientations, different climatic conditions and site-specific requirements. Beside the constructive principals, three separation concepts between cavity and interior space can be described.
Buffer systems [Figure 2a] establish a conditioned air system without an interaction. The air conditioning is realised by natural or mechanical ventilation. Extract-Air-Systems [Figure 2b] use the warm exhaust air of the interior space to increase constantly the temperature of the cavity. A mechanical ventilation system is used for the rooms. Exchange-Air-Systems [Figure 2c] use natural ventilation within the cavity to guide tempered air into the rooms and extract the used air for a constant exchange process.
![Figure 2: Double skin façades with different separation concepts between cavity and interior [7]](/sites/default/files/inline-images/Fig2_5.jpg)
Figure 2 shows the different separation concepts in principal. The air streams within the different separation concepts are driven either mechanically or naturally. Natural ventilated systems need careful design considering changing climatic conditions. Mechanically driven solutions are more robust in this regard, but need controlling and installation. Temperature and humidity conditions can be managed by mechanical driven openings, by fans, or air conditioning units.
The ventilation solutions vary in accordance to their assigned function. First, a second glass layer in front of the exterior cladding of a building [Figure 3a] is discussed. Ventilation openings are required at the bottom and the top of the outer pane to exclude an overheated construction. This typology utilizes multiple ventilation options.
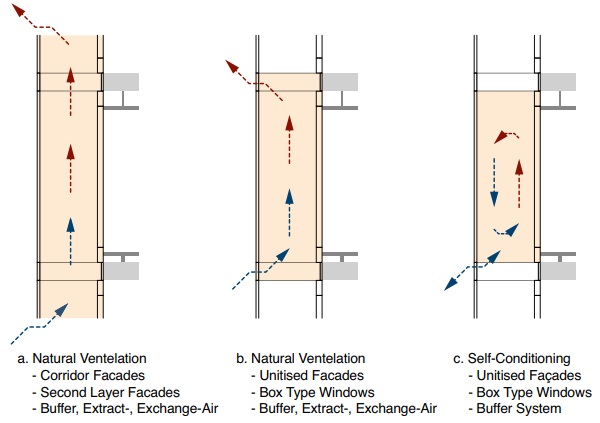
A corridor façade uses vertical or horizontal separations between the cladding sectors. Ventilation openings are spaced evenly to ensure used and heated air is mixed before re-entry in the cavity. The naturally driven shaft box façade guides the warm air into a combined shaft, posessing better thermodynamic properties with no negative influences through an exchange with used air.
Mechanical driven systems [Figure 3d] may use a centralized vent for the whole façade or share the installation with the conventional air conditioning system. Box window facades [Figure 3b] combine several advantages of windows.
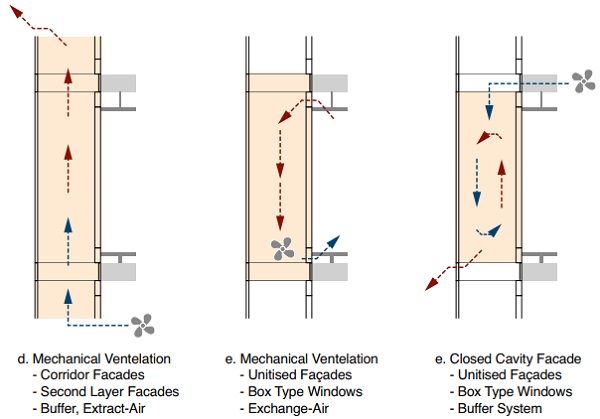
Story-high window elements are used as units. Each unit is accessible using typically an interior opening element and an external glass panel. Ventilation openings are installed at the bottom and top of each window for naturally ventilated alternatives. Mechanically driven systems [Figure 3e] use decentralized air conditioning units integrating the room’s heating and cooling system in the façade.
Box window facades enable the most individual adaptation of climatic and air conditioning characteristics for each window element. In addition, flexibility is gained on each floor and new room configurations can be established easier. The disadvantages are cleaning effort and cost. Integrating functions like air conditioning, natural lighting or light control into the façade increase the complexity and increase the design effort. [8]
Self-Conditioning Facades [Figure 3c] and Closed Cavity Façades [Figure 3f] reduce the constructive width compared to other unitised double skin systems. Constant filtration and sealed cavities makes cleaning of the interior panes obsolete.
The gained floor space, reduced maintenance and integrated shading devices provide a competitive setting in comparison to triple glazed units with interior or exterior shading devices. Closed Cavity Systems can manage climatic conditions with the need of pipework and a mechanical ventilation system. SelfConditioning Facades need a detailed assessment for every project to ensure performance over time.
3 limiting cases and challenges for unitised systems
For both constructions, the geometries are limited to sizes and shapes of huge glass structures. Glass tubes, flat and curved panes can be used with pane sizes up to 3,2 x 15 m and curvatures typical for hot bended panes. (Figure 4).
![Figure 4: Curved and Self-Conditioned Glazing for the Wagram Hotel, Paris [9]](/sites/default/files/inline-images/Fig4_4.jpg)
For closed cavity facades pressurised air supply or a venetelation syststem is used adopting the concept of pressurized multilayer ETFE-foil cushion constructions. Dried, filtered and sometimes temperated air is used for the cushion constructions in order to manage condensation. Mechanically driven vents or compressors, stainless steel pipework and valves are used as air supply system.
Filtration and exclusion of any contaminations of the supply air is essential in order to ensure a performing cavity condition. The system performance can be adjusted to a more tolerant or a more effective configuration for the glazed façade variante. Tightness of the elements and the pipework, an adjusted flow rate between 3 and 40 l/h∙m3 can fulfil the project specific demands in different climate zones.
Self-conditioning facades adopt the concept of pressure equalized insulated glass, using natural ventilation without mechanical aid. Pressure compensation and air exchange is achieved by coupling the cavity to the exterior. The air exchange is necessary to balance the vapour conditions and control condensation.
The conditioning of the cavity is self-regulating during its entire service life. It is balanced by the coordinated interaction between the thermal properties of the façade and fluid-mechanical effects in the cavity and outside. The conditioning takes place with a minimal exchange of air not affecting the thermal performance significantly.
The design of a passive façade requires a precise understanding of the prevailing conditions regarding climate, micro-climate and site conditions. Relevant parameters are interior, exterior and cavity air temperatures as well as surface temperatures including their dew point temperatures.
The exterior and cavity humidity are relevant for the hydrothermal conditions, the resulting dew point and the surface temperatures. The factors are shown in a schematic section in Figure 5. [5,10,11]
![Figure 5: Schematic Drawing with Relevant Physical Factors [10,11]](/sites/default/files/inline-images/Fig5_5.jpg)
Designing for these parameters lead to a reliable and autonomous system. Critical situations for these systems are cooling phases during clear summer nights. High temperatures and high levels of humidity over the course of the day and a steep temperature drop over night due to clear sky radiation define the most relevant threshold. Tests showed that the effect of the temperature drops can be influenced through system design.
A continuous offset between surface temperature of the inner glass panes and the dew point is necessary. [5,10,11] Closed Cavity Systems relize this offset between surface temperature and dew point through a flow rate with dried air. A general issue for unitised buffer systems is its material usage especially when designing for integrated sunscreens. [12] The influence of elevated temperatures on used components and the compatibility of materials especially the used plastics needs to be considered during design.
The disadvantages of both systems require an continuous development with additional marketable technological solutions. The concept of closed cavity systems would be strenghtend greatly by avoiding mechanical ventilation and pipework. The required design of self-conditioning facades on the other hand is costly and complex. Buffer technologies using drying agents for humidity and phase change materials for temperature management are investigated in order to establish a natural ventilated but robust alternative.
Focus on environmental, architectural and social quality is needed in addition to the insulation properties of an assembly. A major issue of the future is resource consumption. A typical self conditioning façade emits two times and a closed cavity façade three times more greenhouse gas equivialnts than a spandrel and double-glazing curtain wall reference over its lifetime. [14]
Thus, energy and material flow analysis will gain importance. The design should inform the decision-making processes of the future in order to detect critical production steps or material choices early. [15]
6 Conclusion
An increasingly systematised approach within the planning process is required. Advanced double-skin façades like the selfconditioned or closed cavity system challenge the traditional glazed façade structures.
The self-conditioning concept demonstrates, that passive systems require a sound understanding of the system parameters and physical relations to operate the façade safely, saving energy whilst reducing maintenance effort.
Closed cavity systems are a typical active concept, which can serve different requirements through an easily adaptable mechanical solution. Both systems need to integrate shading solutions, lighter concepts and alternative insulation glass façades. [8]
Advanced façades need to be improved constantly and need to be assessed regarding their suitability for various climate change scenarios as well. Extreme weather conditions might occur earlier as predicted. These incresed demands regarding the planned and built environment must be balanced with additionally resources and energy. [8]
References
[1] Herzog, T.; Krippner, R.; Lang,W. (2004): façade manual, Birkhäuser.
[2] Knaack, U.; Klein, T.; Bilow, M. et al. (2014): Façades: Construction Principals, Birkhäuser.
[3] Crosbie, M. (2005): Curtain Walls: Recent Developments by Cesar Pelli, Birkhäuser.
[4] Schmid, Fabian C. (2015): Methodological and Systematic Design of Future Façade Solutions, Springer.
[5] Khoraskani, R. A. (2015): Advanced Connection Systems for Architectural Glazing, Springer International Publishing AG.
[6] Schittich, C, Staib, G., Balkow, D. et al. (2006): Glass Manual, Birkhäuser.
[7] Boake, T., Harrison K., Collins, D. et al. (2003): Understanding the General Principles of the Double Skin Facade System, University of Waterloo.
[8] Schmid, F.; Marinitsch, S. (2016): Methods and Technologies for Advanced Building Skin Design; Advanced Building Skins 2016 Bern.
[9] Seele GmbH
[10] Cseh, X. (2013): Numerical Modelling of Unpressurized Double-Skin Façades, BauhausUniversität Weimar.
[11] Fraunhofer Institut für Bauphysik (2014): Research Report.
[12] Rehner, C. (2014): Bauphysikalische Betrachtung von textilen Sonnenschutzelementen in einem geschlossenen, druckentspannten Fassadensystem, Augsburg: Hochschule Augsburg.
[14] Souviron, J. (2016): Producing Transparency: An Energy and Material Flows Analysis of Glazing and Membrane Façades and their Potential of Hybridisationean, Ecole Nationale des Ponts et Chaussées Paris.
[15] Sobek,W.; Schäfer, S. (1996): On the Seam: Joining Components made of Different Materials, in: Deutsche Bauzeitung 130/1996.1, S. 106–114.