Challenging Glass 6
Conference on Architectural and Structural Applications of Glass
Louter, Bos, Belis, Veer, Nijsse (Eds.), Delft University of Technology, May 2018.
Copyright © with the authors. All rights reserved.
ISBN 978-94-6366-044-0, https://doi.org/10.7480/cgc.6.2198
Authors:
Louis Dellieu, Perrine Leybros, Julien Jeanfils | AGC Glass Europe – AGC Technovation Center, Belgium
Due to the recent terrorist attacks, the market demand for security glazing has rapidly grown and turned from a “bank counters” market to a facade market. In this context, it appears to be legitimate to ask the question of the applicability of current standards to this changing environment: Are they still adapted to fulfil the security requirements of the market ? If not, which adaptations could be performed ? In the present talk, the current European standards dedicated to the security glazing resistance against explosion pressure - EN 13541 - is reviewed and compared to its ISO standard pendant - ISO 16934 - and alternative - ISO 16933 -. Moreover, based on numerical simulations, the current extension rules applicable to the specific case of the explosion resistance of insulating glazing units - EN 1279-5 - are discussed as well.
1. Introduction
The World is changing. The overall terrorist threat to the security of the European Union (EU) has increased over recent years and remains on a sharp upward trajectory. The recent attacks in the EU represented a clear shift in the intent and capability of jihadist terrorists to inflict mass casualties on urban populations designed to induce a high state of well-publicized terror. The population respond is unappealable: a safer environment becomes mandatory.
Taking this on board, the security industry needs to adapt to these fast pace changing patterns. Especially, on the security glazing market, a new business model is being set up to respond to a demand which has shift from bank counters-like products to large building facade. In this context, it appears to be legitimate to ask the question of the applicability of current standards to this changing environment: Are they still adapted to fulfill the security requirements of the market? If not, which adaptations could be performed?
In this paper, the emphasis is put on explosion resistant glazing systems. The current European standards dedicated to the security glazing resistance against explosion pressure - EN 13541 - is reviewed and compared to its ISO standard pendant - ISO 16934 - and alternative - ISO 16933 -. Moreover, based on numerical simulations, the current extension rules applicable to the specific case of the explosion resistance of insulating glazing units - EN 1279-5 - are discussed as well.
2. The blast wave
Each standards which will be discussed are based on parameters characterizing the blast wave. Its simplest from has been described and termed by a Friedlander waveform (Krehl and Peter 2009) (Fig. 1).
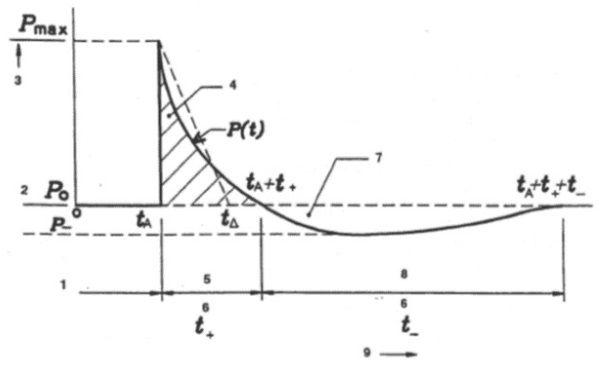
A blast wave can be generated by the detonation of a high explosive. This results in a sudden release of energy that causes the air to be highly compressed and driven at supersonic speeds, during which air molecules cannot respond as they would to a normal input of energy. As a result the air “shocks up” to form a blast wave.
Blast waves have properties predicted by the physics of waves. For example, they can diffract through a narrow opening, and refract as they pass through materials. Like light or sound waves, when a blast wave reaches a boundary between two materials, part of it is transmitted, part of it is absorbed, and part of it is reflected. When a blast wave encounters the surface of a target structure, it is reinforced and reflected. The target initially experiences what is termeda peak reflected pressure, denoted Pmax which is, strictly speaking, the overpressure above the atmospheric pressure P0. Moreover, in a true free-field explosion, as the energy of the expanding gases becomes dissipated, their momentum falls and they begin to contract. The effect on the blast wave is to produce a rarefaction, which manifests itself as a period of “under-pressure” (under P0) known as the negative phase. It is this phase that, combined with the tendency of panels to undergo elastic rebound, often causes window glass to bulge or fall towards the blast source.
The blast wave is therefore composed of two phases: after a time of arrival ta there is a positive phase where the pressure is above the atmospheric pressure P0 (P ∈ [P0, Pmax]) during a time t+ and then a negative phase where the pressure is beneath the atmospheric pressure (P∈ [P-, P0]) during a time t-, as displays on Fig. 1. The equation for a Friedlander waveform describes the pressure of the blast wave as a function of time:
where t is the time and A a decay coefficient (lying between 0 and 4). By integration of the Friedlander equation (1) yields the area under the curve that represents the specific impulse, I+, as given in:
The limiting case occurs when the value of A = 0 and the decay curve is a straight line (Fig. 1); then the duration is the equivalent triangular duration, tΔ, as given in:
3. European standard EN 13541
While dealing with explosion-resistant security glazing for building applications, the European standard to follow is EN 13541 (European Committee for Standardization EN 13541, 2011). This European Standard concerns a method of test against blast waves generated using a shock tube or similar facility to simulate a high explosive detonation(Soloukhin, 1996). A simple shock tube is a tube, rectangular or circular in cross-section, usually constructed of metal, in which a gas at low pressure and a gas at high pressure are separated using some form of diaphragm. The diaphragm suddenly bursts open under predetermined conditions to produce a wave propagating through the low pressure section. The shock that eventually forms increases the temperature and pressure of the test gas and induces a flow in the direction of the shock wave.
The major points of EN 13541 are presented here below. Within this standard, the parameters Pmax, t+ and I+ allow defining four categories of blast wave listed in Table 1.
At this point, it is noteworthy to stress that the as-defined blast waves are valid only for industrial explosions, typically resulting from a gas cloud. More intense and shorter blast waves which correspond to explosive charges detonation will be described further.
The glazing is assumed to be resistant against a given blast wave (as defined above) if :
- The glazing shall not have any "through" holes, from the front to the back;
- No openings from the front to the back as defined in this standard shall be permitted between the clampingframe and the edges of the glazing.
Moreover, results of the tests can be further notated with the addition of an ‘S’ or ‘NS’. Suffix “NS”, no splintering,means that no fragmentation occurred of the last pane rear face of the test piece, suffix “S”, splintering, the last pane rear face (opposite to the blast loaded side of the test specimen) is fragmented, is broken or splinters of the glass are detached from the test piece.
The procedure for certification requires a glass size of 1100x900 mm and a frame bite of 50 mm. Moreover, it is important to stress that the glazing has a so-called attack face. This is the face of the explosion pressure resistant glazing, marked by the manufacturer and/or supplier, that is designed to face the explosive blast.
Finally, while dealing with an insulating glazing unit (IGU), extension rules described within EN 1279-5 can be applied (European Committee for Standardization EN 1279-5, 2005). Indeed, it is noteworthy that, when an explosion resistant glass component certified according to EN 13541 is used as the non-attack face of an IGU then there is no need to test. The classification of the insulating glass unit shall be the same as the glass component used. However, it will be shown further that this extension rule should be handle with great care.
4. Discussion on the applicability of EN 13541
Before starting to review the other alternative standards which could be used for categorizing the explosion resistant glazing, it is important to stress the major drawbacks of EN 13541.
4.1 Glazing size effects
The first and most critical point is the 1100x900 mm size of the tested glazing. As mentioned in the Introduction, the market demand is shifting toward security facade products. This new trend implies to work with bigger sized glazing, typically around 2-3 m², way out of the 1 m² size used within EN 13541. Moreover, the glazing blast response is truly dependent on its size : for a given composition, the bigger the size, the weaker the resistance to a given bomb blast.This phenomena is illustrated on Fig. 2 where the blast response of a laminated 1212.2 (12mm soda lime/0.76mm PVB/12mm soda lime) is calculated via a single degree of freedom (SDOF) method. It can be seen that, the simulation predicts a ER2 NS level of performance for the standard 1m² size 1212.2 (black square on Fig. 2). However, increasing/decreasing the height/width of the glazing dramatically decreases/improves its blast resistance performance according to EN 13541 as displayed on Fig. 2.
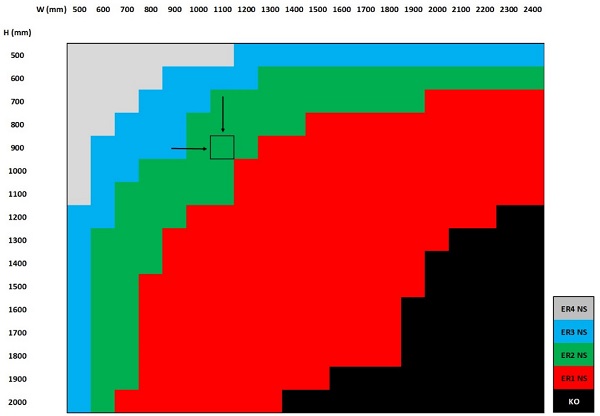
Therefore, although widely employed, characterizing a 2-3 m² glazing as its certified 1 m² correspondence cannot be applied.
4.2 Explosive loading
Explosive loadings can be considered in four broad cases (van Doormaal et al, 2013):
- Small charges in contact with the window or façade which are impractical to protect against this threat.
- Small charges representing person-borne improvised explosive devices
- Large charges representing vehicle-borne explosive devices
- Industrial explosions, typically resulting from a gas cloud
The blast waves described within EN 13541 in terms of overpressure (50 to 250 kPa) and load duration (≥ 20ms) correspond to the last case : industrial explosions. However, such intense and long explosive loadings do not match with the expected threat discussed in the Introduction, i.e. terrorist attacks. Indeed, small and large charges would be more representative.
4.3 Definition of the classification
Each level of performance described within EN 13541 are defined in terms of range (see Table 1). For example, the first level ER1 must verify that the blast loading is characterized by an overpressure between 50 kPa and 99 kPa. This definition means that a given composition certified ER1 NS should be able to resist up to 99 kPa. However, a composition which resist to 50 kPa does not imply that it will resist to 99 kPa. Indeed, resisting to 99 kPa would probably require the composition to be thicker. This example highlights the issues which could be encountered while dealing with ranges for describing the level of performance of the explosion resistant glazing. Indeed, such definitions would lead to an over-estimation of glazing performances which could be dramatic in case of attacks.
Additionally, as explained above, supplementary characteristics can be attributed to the glazing regarding its splintering behavior, i.e. NS or S. In the definition, the S-classified specimen is supposed to have its last pane rear face (opposite to the blast loaded side) fragmented, broken or having glass splinters detached after it got blast loaded. However, it can be argued that such a definition appears as pretty severe and does not allow a fair comparison between different glazing systems. Indeed, a barely fragmented glass will not have the same level of dangerousness than a sharp splinters ejector one. However, both will be classified in the same way, i.e. ERx S. Although extreme, this example perfectly stress the necessity of having a better basis for comparing the splintering behavior of security glazing.
4.4 The extension rules : panes contact issues
While the applicability of EN 13541 has been discussed above, the extension rules of this norm described within EN 1279-5 should be discussed as well. Indeed, such rules must be handle with great care, as explained below.
It is written within EN 1279-5 that, when an explosion resistant glass component certified according to EN 13541 is used as the non-attack face of an IGU then there is no need to perform testing. The classification of the insulating glass unit shall be the same as the glass component used. Let’s exemplify : if a laminated 1515.2 (two 15mm soda lime laminated with 0.76 mm PVB) is certified ER3 NS, therefore an IGU 44.2 / 15 / 1515.2 for which the attack face is the 44.2 with a 15 mm airgap, will be certified ER3 NS without any requirements of testing.
Such a direct extension may lead to an over-estimation of the IGU performances. Indeed, during the blast loading of an IGU, the two panes may enter in contact. This panes contact phenomena is illustrated on Fig. 3 where the IGU 44.2 / 15 / 1515.2 described above is blast loaded with an ER3-like blast wave (numerical simulation performed with ABAQUS). If the resulting shock is too high, the first pane may induce the breakage of the second pane, leading to the non-classification of the IGU according to EN 13541. However, according to EN 1279-5, if the security component placed as a protective face, i.e. 1515.2 in the example, is certified to an ERx NS/S level, the IGU will be classified at the same level.
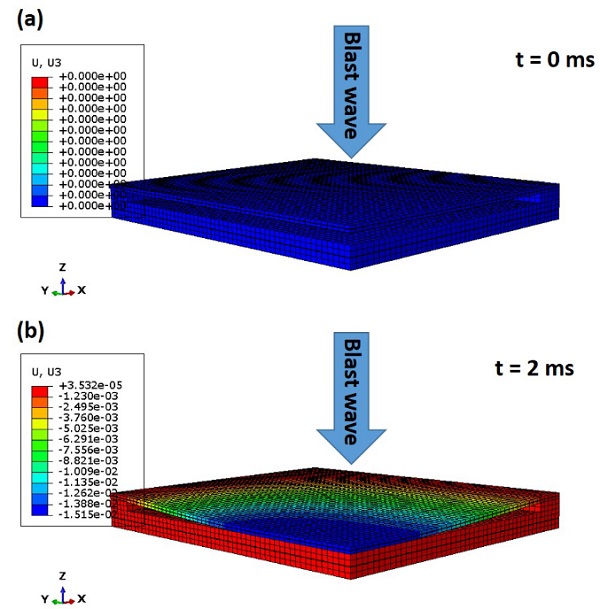
This illustrates that the standard EN 1279-5 does not take into account the panes contact phenomena described above which may lead to conflicting results between the reality and the normative space. This issue will not be discussed further although it was necessary to point it out.
5. The alternative standards
Although European standards must be used for public services in Europe, alternative standards to EN 13541 exist for classifying the blast-resistant glazing (van Doormaal et. al, 2013). Moreover, few of them allow to propose a solution to the above mentioned drawbacks of the current norm EN 13541. The detailed description of each norms and their comparison won’t be provided in the present proceeding but can be found elsewhere (Bedon et al., 2014). However, the main interesting focus of the most promising ones are listed here below.
5.1 ISO 16933
The increasing use of glazing designed to protect persons and property from accidental explosions, and from the effects of terrorist attacks with high explosives, has prompted the preparation of this International Standard : ISO 16933 (International Organization for Standardization ISO 16933, 2007). This International Standard provides a method for carrying out arena blast tests in order to assess and classify the response of glazing to the overpressure and impulse characteristics of high-explosive blasts. In this context, two kind of explosive charges are considered:
- Small charges representing person-borne improvised explosive devices
- Large charges representing vehicle-borne explosive devices
Nominal charge sizes and standoff distances for typical test frames compared to those normal to a large facade calculated to equate to the blast values for the satchel-bomb classifications are provided in Table 2. Nominal charge sizes and standoff distances for typical test frames compared to those normal to a large facade calculated to equate to the blast values for the vehicle-bomb classifications are provided in Table 3. By comparing the overpressure and the impulse of the blast wave within ISO 16933 and EN 13541, it can be seen that the explosion generated by an explosive material such as TNT leads to a much more intense (up to 3000 kPa for ISO 16933 vs 250 kPa for EN 13541) but shorter (around 10 ms maximum for ISO 16933 vs more than 20 ms for EN 13541) blast wave (those parameters can be easily adjusted by the amount of TNT employed and the respective standoff distance (see Table 2&3)). The main consequence is the design of the glazing : thinner glazing can be employed for resisting against consequent amount of TNT (high overpressure and very short load duration) while bigger glazing are required for resisting against less intense but longer blast wave (as described within EN 13541). Typically, 5 to 10 mm difference can be observed. It is noteworthy that the usual charges employed is TNT. However, alternative ones can used by following TNT equivalence rules (International Organization for Standardization ISO 16933, 2007).
Table 2: Nominal charge sizes and standoff distances for typical test frames compared to those normal to a large facade calculated to equate to the blast values for the satchel-bomb classifications (International Organization for Standardization ISO 16933, 2007).
Table 3: Nominal charge sizes and standoff distances for typical test frames compared to those normal to a large facade calculated to equate to the blast values for the vehicle-bomb classifications (International Organization for Standardization ISO 16933, 2007).
Table 4 =: Hazard rating criteria
Moreover, ISO 16933 provides criteria for rating the level of damage to the glazing and the hazard consequences to the area located behind the glazing. This rating corresponds to the (X) in Table 2 and 3. The classification can be found in Table 4.
The main advantages of this norm is the explosive blasts employed which represent the nowadays expected threats.Moreover, the hazard rating criteria allows to have a better comparison between the protection performance of different glazing systems and to classify in a better way the dangerousness of those glazing in the case of a splintering behavior.
However, the major problem of the sample size is still present. Indeed, ISO 16933 requires the samples size to be 1 m² (1100x900 mm).
5.2 ISO 16934
In a pretty similar way to ISO 16933, the norm ISO 16934 (International Organization for Standardization ISO 16934, 2007) defines a classification for blast-resistant glazing systems according to shock tube test. While ISO 16934 uses the same hazard rating than ISO 16933, the blast waves employed here are much more similar to the ones described within EN 13541 (Table 5).
Table 5: Classification of explosion resistant glazing according to ISO 16934 (International Organization for Standardization ISO 16934, 2007).
From Table 5, it can be seen that the classification does not use any ranges which does not let any ambiguous results like ones we could have with EN 13541. Coupling this way of classification with the hazard rating renders shock tube classification much more convenient than with EN 13541.
However, the major problem of the sample size is still present. Indeed, ISO 16933 requires the samples size to be 1 m² (1100x900 mm).
5.3 EN 13123-1/EN13123-2
The EN 13123-1 (European Committee for Standardization EN 13123-1, 2001) and EN 13123-2 (European Committee for Standardization EN 13123-2, 2004) considerer no more the glazing but the whole window system : real size, real frame and so realistic results. These norms allow to work with a shock tube (EN 13123-1) and within arena testing with small charges (EN 13123-2).
The main advantages are the well-defined classes, i.e. no range and good representability of blast waves, and the used defined size. However, the same splinters criteria than the one described in EN 13541 is employed. Hazard rating would have been more convenient.
5.4 GSA - TS01:2003
The GSA-TS0:2003 (US General Services Administration Standard Test Method for Glazing and Window Systems Subject to Dynamic Overpressure Loadings, 2003) is a standard with and international recognition. Like EN 13123-1/EN13123-2, considers the whole window system and allows shock tube and explosive charge loading. For a similar amount of large explosive charge than those described within ISO 16933, the hazard rating is pretty similar to the one described within ISO 16933. Note that this standard does not consider small explosive charge such in ISO 16933.
The advantages for this standard are the same than for ISO 16933 : the explosive blasts employed which represent the nowadays expected threats. Moreover, the hazard rating criteria allows to have a better comparison between the protection performance of different glazing systems and to classify in a better way the dangerousness of those glazing in the case of a splintering behavior.
Moreover, while a fixed 1650x1200 mm is suggested within the standard, specified other dimensions are permitted.
6. Conclusion
As the terrorist threat is increasing, it becomes obvious that the current standards must be adapted. In this context, it was well established that the EN 13541 was not the one to adopt anymore to fulfil the current demand of security glazing. Alternatively, other standards could be employed used separately, mixed together or be a source of inspiration for writing a new and well adapted norm which will fit with this new reality the world is facing.
According to the above considerations, an ideal solution would be to have a standard comprising the three main kind of blast loading (industrial explosion, small explosive charges and large explosive charges) with fixed overpressure/impulse values and an detailed hazard rating. Additionally, classes of glazing dimensions, e.g. small (1 m²), medium (2 m²) and large (3 m²), could be considered for avoiding the glazing size issues. Such a solution would lead to a very complete classification, comprising data which could look like:
- Medium glass / 100kg – 25 m / No Hazard
or
- Large glass / 50 kPa – 20 ms / Minimal hazardIn that way, the certification does not leave any ambiguity or any over estimation of performances but would require a novel codification.
Acknowledgment
The authors thank AGC Glass Europe Business Unit for financial support.
References
Bedon et al., A comparison of existing standards for testing blast resistant glazing and windows, JRC (2014).
European Committee for Standardization, EN 13123-1 : Windows, Doors and Shutters – Explosion resistance; Requirements and classification –Part 1 : Shock Tube (2001).
European Committee for Standardization, EN 13123-2 : Windows, Doors and Shutters – Explosion resistance; Requirements and classification –Part 2 : Range test (2004).
European Committee for Standardization, EN 1279-5 : Glass in building - Insulating glass units - Part 5: Evaluation of conformity (2005).
European Committee for Standardization, EN 13541 : Glass in building - Security glazing - Testing and classification of resistance against explosion pressure (2011).
International Organization for Standardization, ISO 16933 : Glass in building — Explosion-resistant security glazing — Test and classification for arena air-blast loading (2007).
International Organization for Standardization, ISO 16934 : Glass in building — Explosion-resistant security glazing — Test and classification by shock tube loading (2007).
Krehl, Peter O. K., History of Shock Waves, Explosions and Impact, Springer (2009).
US General Services Administration Standard Test Method for Glazing and Window Systems Subject to Dynamic Overpressure Loadings (2003).
Soloukhin, R.I, Shock waves and Detonations in Gases, Mono Book, Baltimore (1996).
van Doormaal et al., Resistance of structures to explosion effects: Review report of testing methods, JRC (2013).