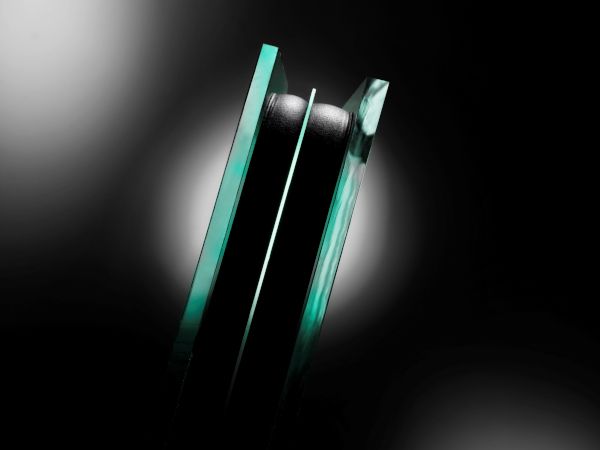
Date: 6 May 2025
On behalf of glasstec the author asked research and industry about the current state of the art, what its limits are and which applications can already be expected by the end of the year: Daniel Pfarr (TU Dresden), Peter Nischwitz (Glaston) and Bernhard Hötger (Hegla) answered.
Author: Marc Everling
Thin glass is gaining increasing relevance for reducing the weight of glass construction components: slimmer insulation glazing units make for lighter, resource-saving structures with a smaller carbon footprint in fenestration and façade construction. In the process of energetic renovation slim triple glazing units will be able to replace technically obsolete double-glazing units while conserving frames and sections. Thin glass also brings benefits for curved elements as it is far easier to cold bend – an advantage for both its optical characteristics (less distortions) and in terms of costs. Flat glass is referred to as thin glass when it is less than 3 millimetres thick. TSG up to 2mm thin and thermally toughened glass up to 1 mm in thickness is produced in special high-convection furnaces by evenly heating and cooling off the material especially fast. Until now tempering has only been possible up to this standard thickness – but with the great benefit of being able to process glass ribbon sizes and some manufacturers even being able to process extra-large glazing. Even thinner glass sheets, until now only used in such technical applications as display production, are chemically tempered but have only been available in smaller dimensions so far. They are laser-cut from extremely thin base glass, finished and finally chemically toughened for smartphones, for example. Chemically speaking, thin glass is a borosilicate glass, which – compared to classic soda lime sheets – stands out with greater strength and thermal resistance at the same thickness. These material characteristics are what make the processing of very thin glass possible in the first place. However, the reduced material thickness results in higher requirements for handling, transport and edge quality when sizing.
The first producers are now offering chemically tempered thin glass (0.5 – 0.7 mm) that is specifically designed for building physics requirements and particularly resistant, like Corning which is now launching its “Advanced Technical Glass” (ATG). This is designed to make for slimmer, lighter window elements with triple and quadruple glazing units, laminated sheet glass and laminated sheet stacks, for instance for smart glazing, combining a high optical quality with a scratch-resistant surface. The available sheet size of 2,200 x 3,200 mm now makes it relevant for IGU production.
Which thin glass applications are being researched?
Thin glass applications are the topic of research amongst others by the Institute for Building Construction of the Construction Engineering Faculty at the Technical University Dresden. According to Dipl.-Ing. Daniel Pfarr, scientific assistant at the faculty, thin glass holds great potential for making inroads in architectural applications – with thin glass used as the internal pane in triple glazing being just one example. “Those assuming thus far that thin glass would undergo strong deformation when used as an internal pane were wrong. Due to the mostly uniform isochoric pressure of the two adjacent spaces between the panes, deformations as a result of climatic loads become negligible compared to external impacts such as wind. Through chemical tempering very high surface strengths can be achieved – regardless of the glass thickness. The limitations here are only the limited formats available as well as the price. The thermal tempering customary for IGU production, which has the great benefit of allowing complete ribbon dimensions or even extra-large glazing, has so far not achieved the required gradient with such thin sheets – i.e. it has not reached the necessary temperature between the sheet core and the sheet surface.” With thin glass the core and the surface are located closer to each other than with standard float glass at a 4mm or 6mm thickness. This is why the compressive stress forming at the glass surface when cooling is not so high and the glass is not so heavily tempered. In a research project with Solling Glas the university is now conducting tests to ascertain up to which glass thickness thermal tempering is still technically feasible: “We have achieved very high strengths as well as standard-compliant fracture patterns for TSG of up to 2.6 mm; 3 mm are customary in the market. To attain this, we change the plant parameters during tempering and cool off the gas faster to reach higher tempering values. With these measures in place it will be possible to reliably temper glass sheets of up to 1.1 mm in future.”
A second interesting application studied by the Institute is laminated thin-glass components with transparent plastic cores. These could in future be deployed as lightweight components in curtain walling. “The transparent core is extremely lightweight offering great potential for resource savings. Optically there are hardly any constraints – but we have to take a closer look at daylight transmission, U-values, g-values and similar properties. We could even imagine cold bent thin-glass elements with high stiffening.”
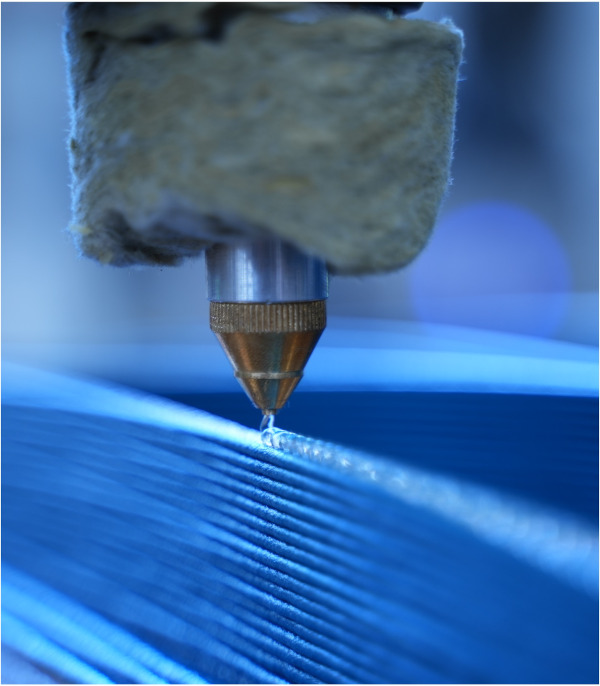
Photo: Daniel Pfarr, Institute for Building Construction
The third application researched by Pfarr and his colleagues are laminated thin-glass assemblies with additively manufactured cores: “We connect cold bent thin glass with 3D-printed structures.
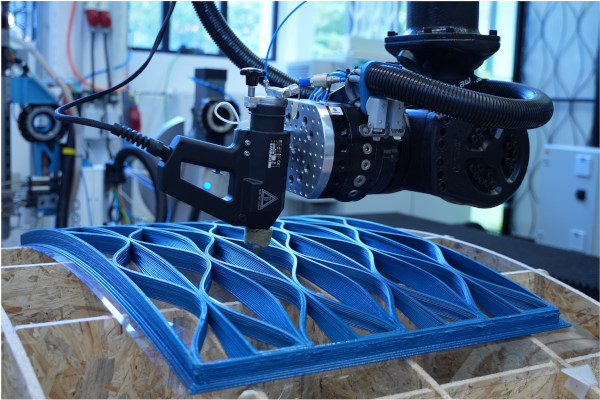
Photo: Daniel Pfarr, Institute for Building Construction
This opens up completely new design avenues with the stiffening achieved by the sandwich effect. The voids between the 3D-printed structure create spaces between the sheets with thermal effects comparable to insulating glass. This concept, however, is still under development, especially in terms of the robustness and durability when exposed to temperature fluctuations and UV radiation,” explains Pfarr.
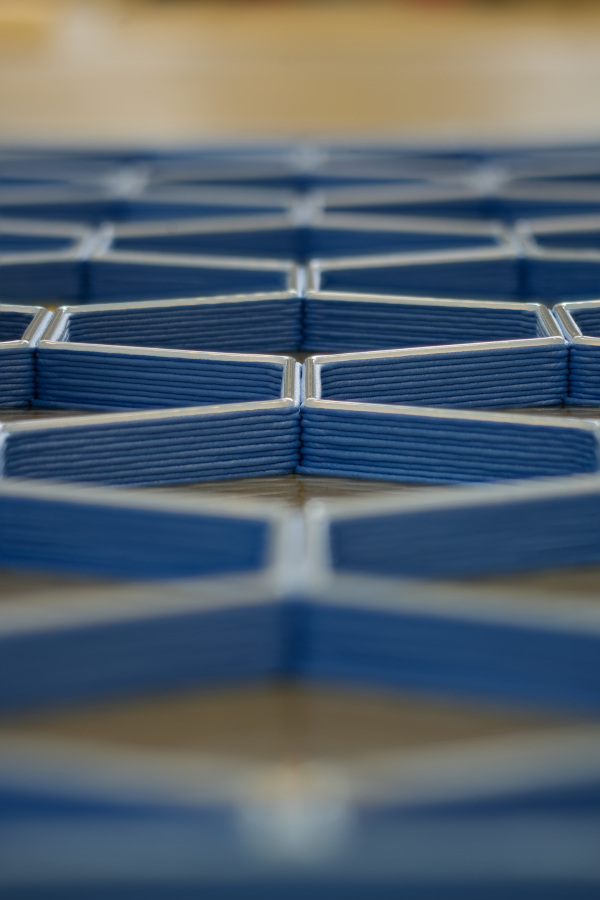
Photo: Daniel Pfarr, Institute for Building Construction
Handling: thin glass handled by IG lines?
The first IGUs with 0.5 mm internal glass pane are expected to be available in late 2025, confirms Peter Nischwitz, Marketing Manager at Glaston Germany: “We see great potential for slim triple glazing with thin-glass internal panes, which can replace technically obsolete double glazing in well-preserved window frames – by simply exchanging the glass.” At glasstec 2024 the company introduced a new manufacturing process for IGUs that were equipped with Corning’s new ATG glass. Nischwitz explains: “Conventional IGU production methods proved unsuitable for the ultra-thin internal pane. This is why we developed a new technology and patented it in autumn 2024.
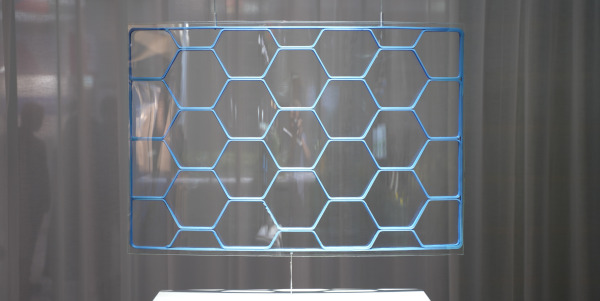
Foto: Daniel Pfarr, Institut für Baukonstruktion
Our new and fully automatic TPS line (Thermo Plastic Spacer) minimises the stress on the internal glass pane and reduces the risk of breakage also in mixed operating modes. The first lines are already in operation in the USA and preparations for installation at one of the big IGU manufacturers in the DACH region is underway.” In conventional triple-glazed IGU layouts all sheets end in parallel on the bottom edge. If the internal pane is only 0.5 mm thin, however, the load on its bottom edge would be too high; to minimise the risk of breakage an excellent edge finish would be required. Therefore, the thin-glass sheet in the new TPS system is a little shorter than the two external panes, slightly set back and completely embedded in the thermoplastic spacer complete with secondary sealing.
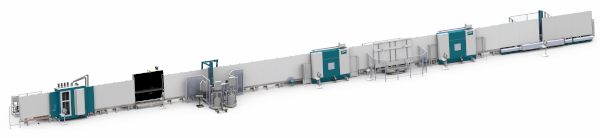
Photo: Glaston Germany GmbH
Feeding and sizing of the thin glass is done on Hegla lines entirely in an automated process to avoid damage by manual handling. Managing Director Bernhard Hötger shares the details: “Feeding can be done by a specifically adapted floor loading system plus corresponding suction cup offset. A flat conveyor belt replaces the typical felt covering on the cutting line and prevents slippage. Sensors capture the glass sheet position, rendering manual alignment superfluous.
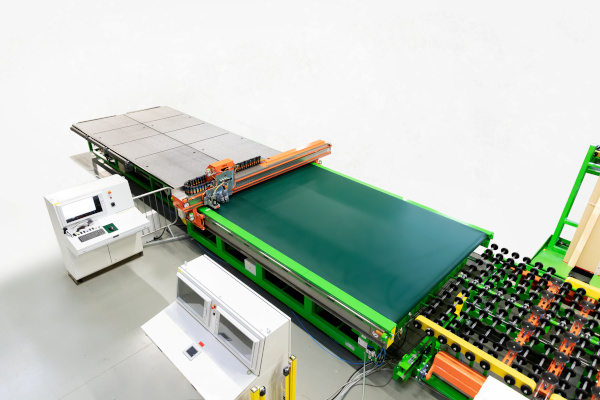
Photo: Hegla GmbH & Co KG
A special cutting head then scores the sheets to obtain an especially homogeneous edge, which is indispensable to downstream finishing. Transportation of the cut sheets is system-controlled; they are placed by the cutting system in compartments via a tilting air cushion table. Glass removal and handover to the IGU line is also automatic, so that edge damage is largely excluded.”

Photo: Hegla GmbH & Co KG
By Glaston accounts, the resulting triple glazing with ultra-thin internal pane can be as slim as double glazing and improve the Ug-value compared to double glazing by up to 20% – depending on the Low-E coating and gas filling. The use of weight and resource-saving IGUs is especially beneficial for residential housing and energetic renovation or when heavy sliding windows and doors pose weight-related closing problems.
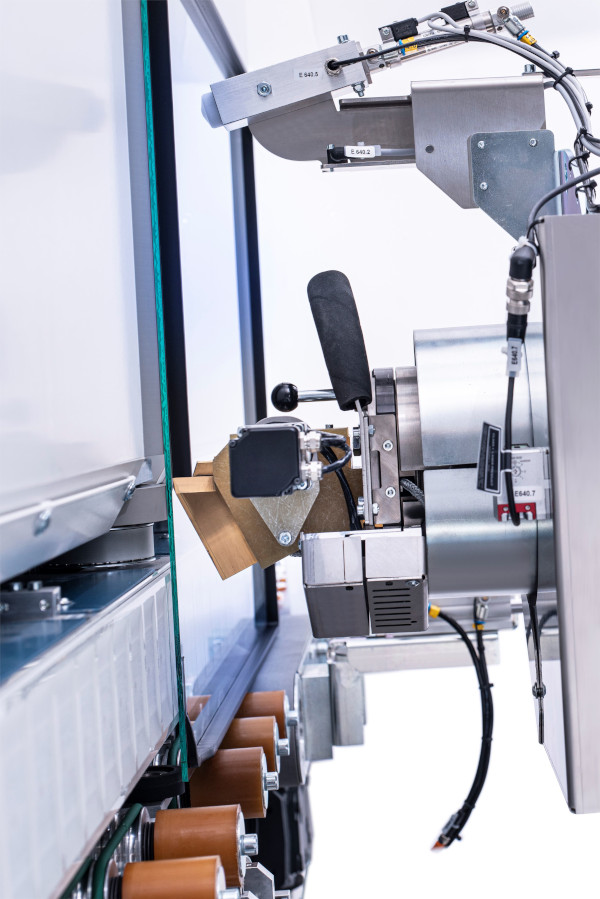
Photo: Glaston Germany GmbH
From October 20 to 23, 2026, glasstec 2026 in Düsseldorf will once again be the central and inspiring leading trade fair for the exchange of ideas on future topics in the glass industry. With its special show “glass technology live” and the associated “glasstec conference”, the trade fair brings together researchers, manufacturers and users who want to help shape the future.
For more information go to: www.glasstec.de
About the author:
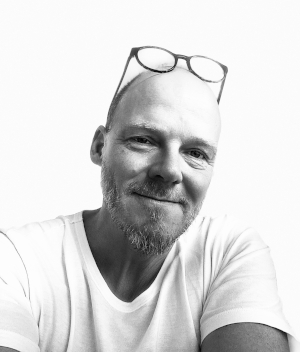
Marc Everling studied media education (Technical University Brunswick) and has been a communications and marketing specialist in the glass industry for more than 20 years. In 2021 he founded his networking agency specialising in communications consulting and press liaison for companies and associations that work and produce sustainably in the interests of the ecological transformation of the construction sector.
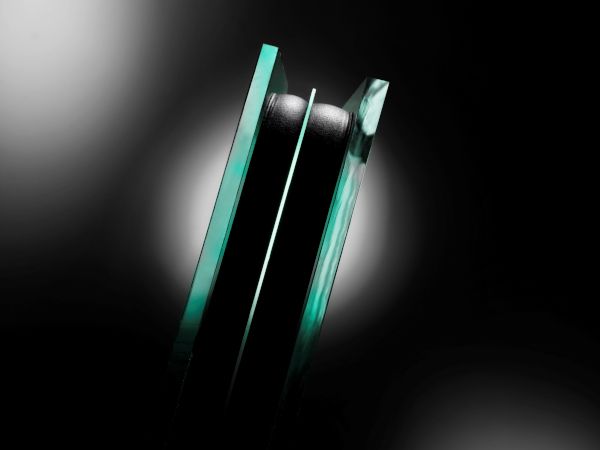

Add new comment