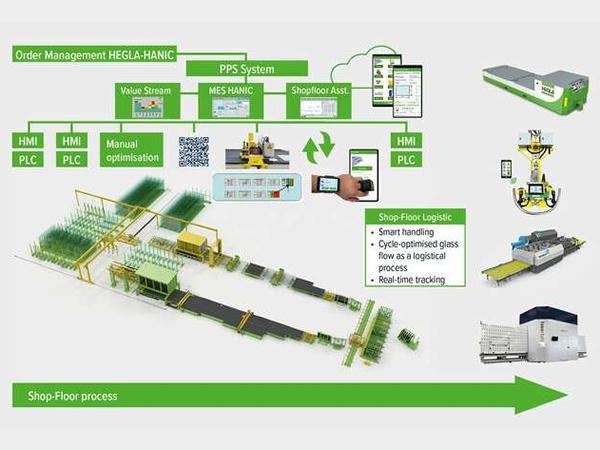
Date: 13 October 2020
While this term still describes a coherent, albeit somewhat broad, vision of the future with many buzzwords from a scientific point of view, many questions as to how it can be implemented in practice remain unanswered.
Digitalisation, networking and tracking as steps towards future production
“Industry 4.0 is not a theoretical end in itself without a goal, nor is it a universal instruction manual on how a glass processing company can prepare itself for the future,” said Bernhard Hötger. The technologies of digitalisation, networking, and the automatic capture and evaluation of data are steps towards future production. However, it is up to each individual company to determine the cases in which these technologies will lead to the desired result.
“To begin with, therefore, the entire value-creation process from order generation to production and after-sales service, as well as all machines, transfer points for data and sub-products and software, should be closely scrutinised. The second step then involves developing an overall concept and determining the most effective starting points,” the HEGLA Managing Director recommended. Information can be generated from the data thus obtained and turned into productivity.
Until just a few years ago, the focus of such optimisations was solely on production, with the automation and networking potential it offers. Hand in hand with technical progress, the focus expanded into new areas.
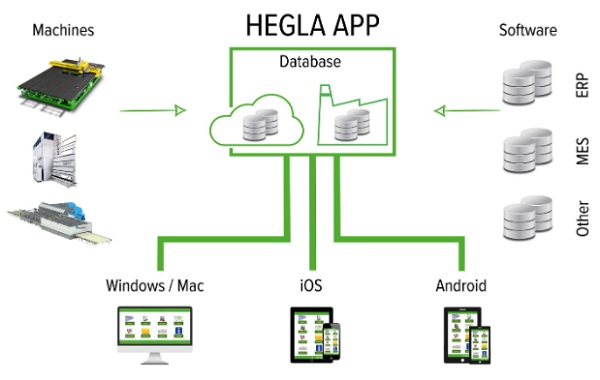
Further developing the value chain to make optimum use of resources and know-how
Bernhard Hötger is convinced that “with modern machinery from a quality supplier, pure system capacity is normally sufficient to enable on-time production even with high volume demands and a high degree of product variability”. As a rule, the number of employees is also appropriate to process the existing orders. Within the framework of the change process in Industry 4.0, the aim is therefore to further develop the entire value chain and personnel scheduling in such a way that the available resources and know-how can be used optimally.
It is also important to provide the glass at the right time when it is needed by the downstream process. The term “shop-floor logistics” describes the concept behind it.Production is optimised to such an extent that efficiency is no longer dependent on machines or individual factors, but rather glass flow is to be understood as a holistic, homogenised process.
Target/actual comparison and control options using data and tracking
With the change processes towards Industry 4.0, the capture and evaluation of data are becoming more important, as is software. Once the data from the systems and the processes are available, an exact target/actual comparison of the planning and the results is possible in real time. It is no longer based on probabilities, planned values and a partially recorded output. The information becomes even more accurate if, say, laser marking is also used in production.
As soon as a pane has been marked with a number or a QR code, it can be uniquely identified throughout the entire product life cycle and tracked in a process-safe manner at the production stations. The more information of this kind is collected, processed and made available, the more intertwined and transparent the processes can be made. When this data is provided in a targeted manner, for example to the HEGLA-HANIC continuous optimisation system, time variations are directly incorporated into the planning and may lead to an adjustment of the cutting plans with regard to preferred products or can be used to further optimise waste.
A greater degree of merging of information from additional sensors, data from the machine control system or the ERP software creates an even more precise picture of the processes, which also reveals the bottlenecks in the value chain in question. On the basis of the resulting key figures and contexts, individual processes can be changed and simulated, and ideal processes can be defined within the framework of process analysis. The knowledge gained is then integrated into process design to optimise the workflows for the company in question.
Employees receive useful information about process steps
The Managing Director of software business HEGLA-HANIC, Dr Jan Schäpers, advises his customers to collect data over longer periods to ensure it is available for evaluation later. He also recommends using cockpits at central production locations to transparently display machine data, maintenance dates, relevant key performance indicators (KPIs) or the current target/actual status of processing. This provides employees with useful information on their process step to aid decision-making or to facilitate their work.
In addition, the Shop-Floor Assistant app can be used to access cockpit data, machine data and maintenance intervals, among other information, regardless of location and manufacturer. In addition to the documentation for the individual systems, an internal ordering service or the request for an internal rack transport, the app offers functionalities for the identification of glass types by scanning the QR code, for example. Depending on data integration and transfer, the app may also be used outside production.
A single scan is sufficient on the building site, for example, to access the fire protection certificate for a pane, to order an identical glass type directly or to document the delivery of a rack by scan or photo. Complete data transfer along the whole value chain opens up the options considerably: The window fitting company can directly re-order a product via the app while enquiring about the required pane from its supplier, including its price, and can immediately give the customer a delivery date.
Machines, processes, and forms of interaction change and blend
“As networking, automation, and the intertwining of processes, software and machines continue to expand, ever more closely meshed systems are emerging whose flexibility depends not least on software and the ability to make adjustments in production planning,” said Bernhard Hötger. “On the one hand, this creates a glass flow that suits shop-floor logistics. On the other hand, it also results in machines, processes and the forms of interaction changing and blending even further.”
As part of the internal HEGLA 4.0 project, the machine controls will therefore also be designed to be even more user-friendly and will be thoroughly networked with HEGLA-HANIC software and the HEGLA app. Optionally, the parameters and key figures of the systems can be stored in a cloud, for example. Cutting-wheel monitoring makes the operator’s work easier, as do the advantages afforded by demand-oriented maintenance, which indicates when a threshold value is exceeded, e.g. for a drive’s input voltage.
“We used to be judged on whether we could scratch and break glass. That has since become a basic requirement. Today it is all about getting a standard piece of glass into the factory and then turning out a highly refined product to be used by the end customer. At HEGLA, our role in the production process is to ensure that our customer delivers a high-end product on the promised date and generates the calculated added value,” said Bernhard Hötger.
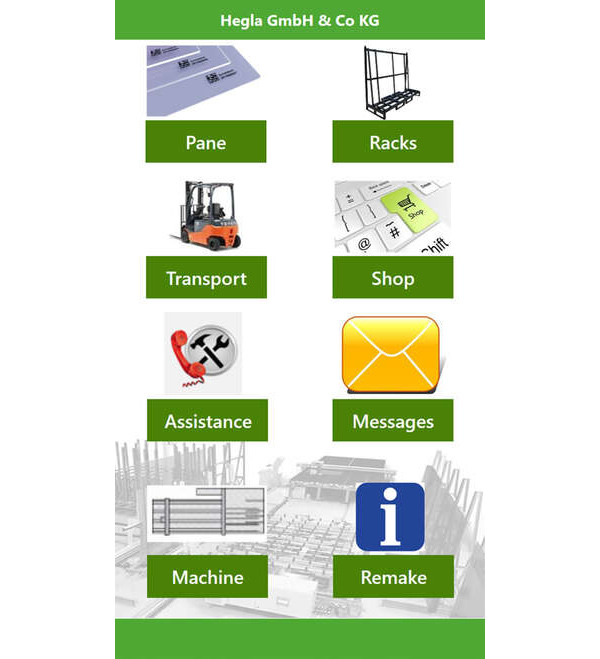
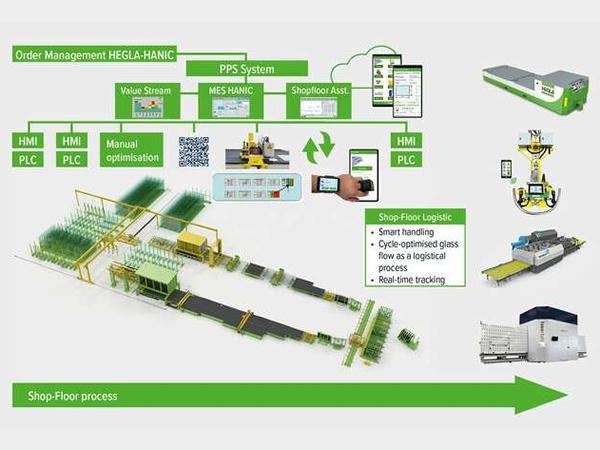

Add new comment