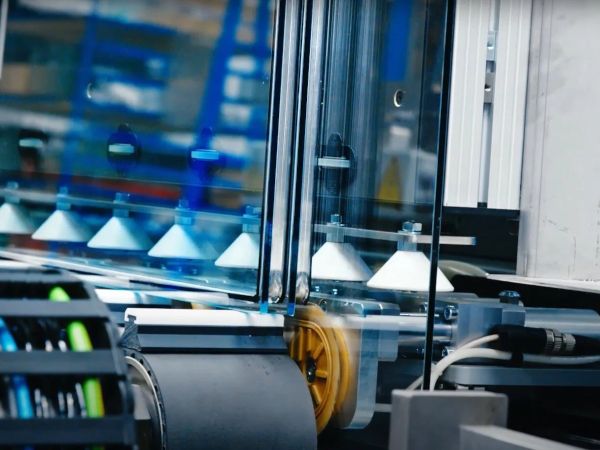
Date: 7 March 2025
The production of stepped glass units presents a significant challenge in IG production. Particularly facade units made of larger and heavier glass panes require specialized machinery and techniques to ensure safe transport and precise assembly. How does LiSEC approach these challenges?
Areas of Use for stepped Units
When it comes to IG units, there are specific applications in which the offset between the outer and inner pane is crucial. Examples include:
- Cold storage display doors: The mounting frame is covered by a larger, stepped glass pane for more aesthetic appeal.
- Glass facades: To create a continuous glass front on the outside, glass surfaces on buildings are constructed from stepped IG units. Stepped glass units also meet at the corners.
In both applications, the steps are on all four sides to completely conceal the underlying construction behind the glass pane.
HOW TO PRODCUE STEPPED Units
The production of units with steps on all four sides requires significant adjustments to the machine design in order to provide sufficient support for the glass at the stepped edge. To be able to process different step heights flexibly, the machines must be height-adjustable.
The latest generations of LiSEC machines are capable of producing steps with a height of 0 to 150 mm on the bottom edge and up to 200 mm on the other sides, with optional steps up to 1000 mm also possible. This adaptability is crucial to meeting the diverse requirements of different construction projects while ensuring the high quality of the glass units.
A big difference: the alignment of the glass pane
In a LiSEC insulating glass line the larger glass pane of a stepped unit is always aligned towards the rear wall. In the case of triple units, the larger glass pane is also aligned towards the rear wall, while the two smaller, identical glass panes are positioned in front of it. This alignment has two advantages:
- Especially the larger outer panes of facade glass are often made of laminated glass due to safety standards and wind loads. Guiding this pane close to the machine enables processing larger, heavier glass without tipping risk.
- Furthermore, the edge of the unit is accessible from the front side, which makes it possible to check the sealing quality or to carry out manual rework.
Continous support at the bottom edge
In the case of glass units with a step on the bottom edge, depending on the dimensions of the glass and the stability of the spacers, the smaller stepped glass may tip or sink due to its own weight. Therefore, the smaller glass panes must be supported at a higher position than the usual glass transport height.
To effectively address this challenge, LiSEC has developed machines that provide continuous bottom-edge support for all glass sheets, such as the AGP-A press and the VFL-1F / SRP-A sealing station. These machines ensure that all glass sheets are continuously supported from the gas filling press to the end of the production line.
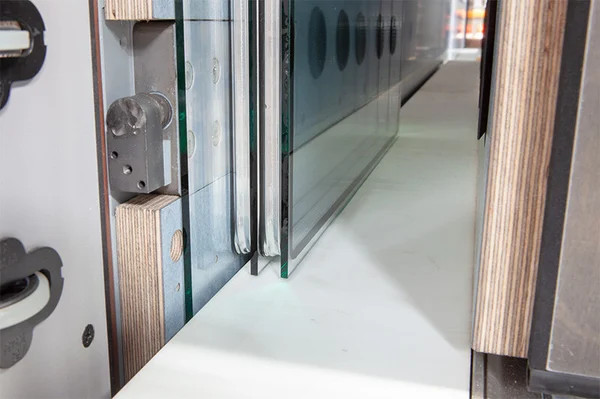
Step support in action
The use of stepped units increases reliability in production and enables excellent product quality. The video shows the production process with rigid and flexible spacers.
Summary
When producing high-quality IG units with steps on all four sides for use in facades, cold storage display doors and other applications, it is essential that the step is supported throughout the entire production process. Aligning the larger glass towards the back wall allows for risk-free production of larger and heavier units, among other benefits.
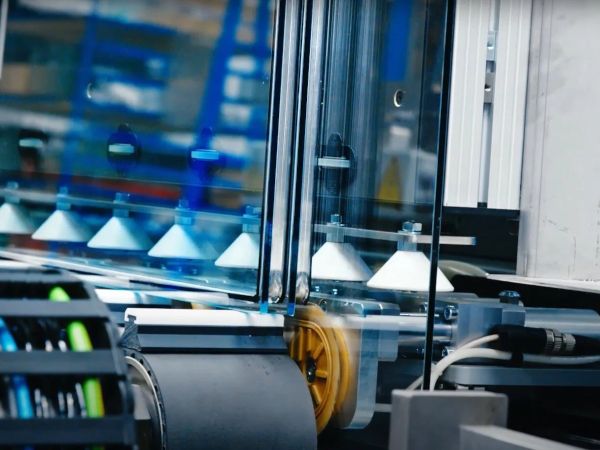

Add new comment