This paper was first presented at GPD 2019 by Univ.-Prof. Dr.-Ing. Thorsten Weimar and M.Sc. Sebastián Andrés López from Universität Siegen.
For this reason, laminated safety glass with a resistance against manual attack results in heavy and thick cross-sections. General attributes of security glazing can be optimised by using benefits of different materials. In this case, the lamination of thin glass with polycarbonate enables innovative composite panels with improved properties in contrast to common laminated safety glass. Two outer thin glass panes and one or more inner polycarbonate sheet laminated by thermoplastic interlayers define the cross-section.
Nevertheless, thin glass-polycarbonate composite panels as a more efficient alternative to laminated safety glass as security glazing results in slighter cross-sections by achieving the highest resistance class P8B against manual attack. Several options for using annealed and chemically strengthened thin glass by laminating with polycarbonate are described as well as the results of the four point bending test as set-up for the structural behaviour. Thus, deformations of the bending tests are compared with numerical and analytic analyses to specify the capacity of shear connection. Finally, test results for a resistance against manual attack complete this study.
1 Introduction
Smart buildings can adjust themselves to different climatic conditions. Focused on building envelopes, it might be better to speak about adaptive façades or polyvalent walls. This element is a kind of building controlled element which reacts independently to changing boundary conditions. Instead of encapsulate itself from the outer space, an adaptive façade utilises the environment for comfort, usability and energy consumption [1].
Mike Davies already introduced in 1981 the vision of a polyvalent wall which adjusts adaptively to the respective requirements. Only with self-produced energy, the element can arrange itself with aspects like fire, heat, noise, weather and sun protection as well as design, energy, media and security. Up today the idea of a polyvalent wall is an unachieved ideal of multifunctional glazing in façades [2].
EN 13830 [3] defines characteristics of a curtain wall in terms of weather, sound, fire and heat protection in combination with a resistance against external loads. These requirements in accordance to Davies are often not met by a single glass pane. Therefore, laminated glass is used primarily on multifunctional glazing. The interlayer or gas space should regulate several properties independently. According to EN ISO 12543-1 [4] and EN ISO 12543-2 [5], a laminated glass consists of at least one or more glass panes or plastic glazing material laminated by an interlayer.
Referring to the requirements of a laminated safety glass with enhanced demands on the interlayer, a composite of ductile polycarbonate with brittle thin glass enables innovative composite panels which achieve the possibility to be an alternative to conventional laminated safety glass. Furthermore, the impact-resistant polycarbonate in combination with the high surface strength of thin glass reduces significantly the cross-section and the dead load in comparison to conventional laminated safety glass as security glazing [6] [7].
The manufacturing in a cast resin process leads to the research on the structural behaviour with the four point bending test. This paper focuses on the experimental and analytic investigation of the lamination of thin glass and polycarbonate. The analytic method of sandwich beams is implemented for thin glass-polycarbonate composite panels tested in the four point bending test and compared to numerical analysis with the finite element program SJ Mepla 5.0.0. Furthermore, the research on the lamination with the ball drop test and against climatic stress as well as the resistance against manual attack complete the investigation.
2 Bulk Materials of a Thin GlassPolycarbonate-Composite Panel
A thin glass-polycarbonate composite panel consists of two outer thin glass panes, and at least one inner polycarbonate sheet which are laminated by a transparent polymeric interlayer. Figure 1 shows the cross-section of a thin glass-polycarbonate composite panel and table 1 the bulk material properties.
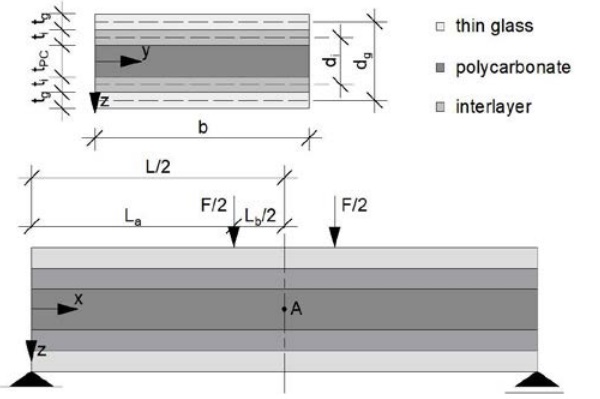
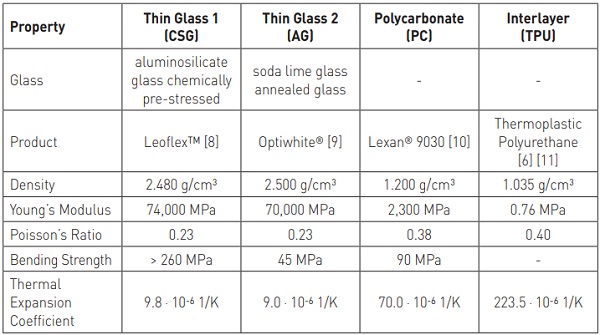
3 Theory of Sandwich Beams
Common sandwich constructions consist of two thin, stiff and strong layers separated by a foam core with a low density. The adhesion or lamination of the faces with the shearresistant core results in a high structural behaviour and high flexural rigidity [12]. A thin glass-polycarbonate composite panel with more than 3 layers, seen in figure 1, can also be calculated with the sandwich theory next to conventional analytic methods. The four point bending test according to EN 1288-3 [13] is approximated with the beam theory.
Analogously, the theory of wide sandwich beams fits as well for laminated safety glass and glass-polycarbonate composite panels [6] [14]. Figure 1 shows the composite panel in the four point bending test. The flexural rigidity results as the sum of the bending stiffness of each layer about the global centroidal axis and the local bending stiffness about its own centroidal axis. The following simplifications are made for the analysis of thin glasspolycarbonate composite panels as sandwich beams in this study.
• Eg and EPC ›› Ei, where Eg is the Young’s modulus of thin glass, EPC the Young’s modulus of polycarbonate and Ei the Young’s modulus of the interlayer. The local bending stiffness as well as the bending stiffness about the global axis of the interlayer are neglected. Furthermore, the assumption of the thermoplastic polyurethane constitutive law has no time dependence due to a short time test. This results in a homogenous and isotropic material.
• The glass faces of the sandwich panel possess a linear elastic material behaviour with a validation of Hooke’s law.
• The cross-section is constant, independent of the load and leads to a symmetrical structure of the laminate.
• If the bending stiffness of the faces about their own axis related to the bending stiffness of the faces about the middle axis is lower than 1 %, the bending stiffness of the faces about their own axis is insignificant. The faces of the sandwich beam are thin. Equation (1) shows the two conditions for the thin face approximation. [15]
• If the bending stiffness of the core related to the bending stiffness of the faces about the middle axis is lower than 1 %, the bending stiffness of the core is insignificant as well. Equation (2) shows the condition for the weak core approximation. [15]
Based on the simplifications, the flexural rigidity B of the sandwich beam describes equation (3). Equation (1) and (2) depends on the cross-section of the sandwich. An analysis of the conditions for the thin face or weak core approximation is given in chapter 4.
The total deformation w of the sandwich beam is divided in a bending deformation w1 and a shear deformation w2. The bending deformation w1 depends of the load F and results from the simple bending theory. The shear deformation has to be shared between the faces and the core. By integration of the basic equations, the total deformation in the centre of the beam at A results with equation (4) for the unfractured state of a sandwich beam. [14]
Further information about the analysis and design of sandwich elements can be found in literature like [6], [12], [14] and [16].
4 Structural Behaviour
First, the theoretical investigation of the structural behaviour of thin glasspolycarbonate composite panels implies the analysis of the thin face or weak core approximation. Referring to equation (1) and (2), figure 2 and figure 3 shows the results of the condition analysis in equation (1) and (2). The bending stiffness of the faces are insignificant for the composite panels made of thin glass Leoflex. By using a thicker top layer, the bending stiffness of its own axis has an influence on the total flexural rigidity of the sandwich.
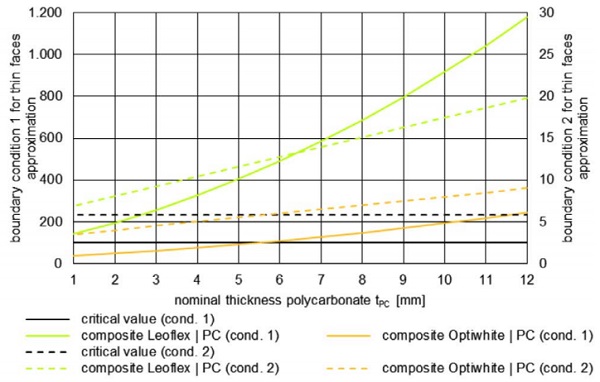
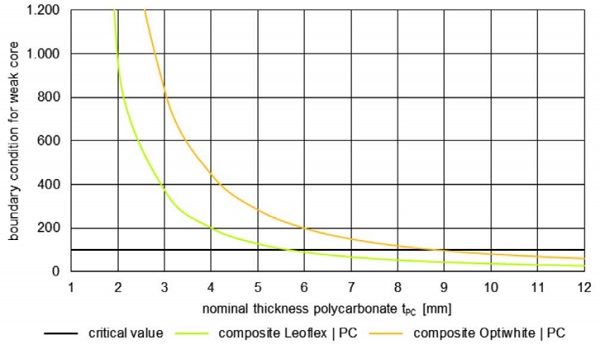
Nevertheless, by increasing the polycarbonate core, the glass influence decreases and for polycarbonate sheets thicker than 5 mm the local bending stiffness of the core material is negligible. Furthermore, a weak core sandwich beam does not consider the local bending stiffness of the inner polycarbonate core. Due to the outer glass panes, a weak core approximation results for polycarbonate sheets lower than 6 mm for a composite panel with Leoflex and lower than 9 mm with Optiwhite faces.
The structural behaviour of thin glasspolycarbonate composite panels is tested by the four point bending test according to EN 1288-3 [13] with short load duration. The specimens with dimensions of 1,100 mm in length and 360 mm in width lie on two support rollers and are symmetrically loaded to the centre by two load rollers. Biaxial strain gauges are implemented on each layer and measure the elongation in the centre of the composite panel as well as along the longer edge. Linear variable differential transformers detect the deformation of the laminates. Figure 4 shows the experimental set-up for the shorttime test.
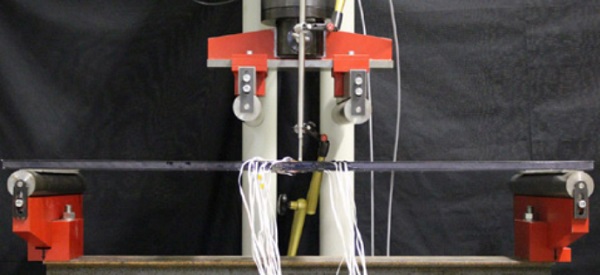
The specimens consist of one inner polycarbonate sheet and two outer thin glass panes laminated by a 2 mm thick polyurethane interlayer. The nominal thickness of the inner polycarbonate sheet varies, so that the nominal thickness increases from 9.7 mm to 20.0 mm. Overall, 18 specimens with 6 different cross sections are analysed. Table 2 illustrates the cross-section, nominal and real thickness.
The study also considers the analysis of the shear transfer of the interlayer. Related to DIN 18008-1 [17], a favourable shear transfer may not be used except under constraining conditions. The two limit states »no composite« and »full composite« can be determined easily by analytical or numerical calculations. In reality, there is a »partial composite« which transmits the shear forces [18].
The tests are performed at (22 ± 1) °C and (38 ± 5) % rH. Table 2 shows also the mean values of the load and deformation. The deformation of the composite panels under a constant load can be reduced by increasing the inner polycarbonate thickness. This leads to a stiffer laminate. Furthermore, by increasing the polycarbonate thickness in the core, the standard deviation is reduced due to the thicker core which is more responsible for the load transfer.
The partial composite of the laminate depends on the Young’s modulus Ei and the shear stiffness A·G(t) of the interlayer. For the short time tests of this study, A·G(t) is independent of the time t, so time effects of the interlayer are insignificant. Due to the five layered sandwich beam, the geometrical non-linear calculation with SJ Mepla determines the Young’s modulus of the thermoplastic polyurethane for each specimen. Generally, a geometrical non-linear calculation of the deformation and stresses is required for glazing with deformations thicker than the cross-section.
PK_12 Leo and PK 12_Opti show deformation smaller than the thickness. This fact causes in the approximation of the specimens with the linear sandwich beam theory. According to figure 2 and figure 3, the specimens possesses thin faces and a stiff core. The bending stiffness on its own axis of the faces as well as of the core are insignificant. For each specimen, the linear sandwich theory calculates the deformation.
Table 3 shows the difference between the deformation of the sandwich theory and the measurement values. The differences are up to 12.8 %. Under consideration of geometrical non-linear effects of the structural behaviour as well as a physical non-linear material behaviour of the interlayer, the differences can be reduced. The deviation between the measured deformation and the analytical calculated deformation of PK_12 Leo are smaller than of PK_12 Opti.
5 Additional Properties of Thin GlassPolycarbonate Composite Panels
5.1 Investigation of the Laminate as Laminated Safety Glass
Due to the manufacturing process a thin glass-polycarbonate composite panel is more expensive than common laminated glass with a PVB interlayer. Hence, additional benefits has to be specified for the laminate. First of all, the test methods at high temperature, in humidity and under radiation according to EN ISO 12543-4 [19] are investigated to verify the durability of the interlayer.
The test at high temperature analyses the temperature influence of +100 °C over a period of 16 h on the composite panels. Testing in humidity determines the influence of the air humidity of 80 % rH and a temperature of +50 °C over a period of 2 weeks. The radiation test proves the effects of radiation in a sun-like spectrum on the thin glass-polycarbonate composite panel. Additionally, the light transmission value of the specimens is detected before and after the radiation.
Due to the tests, the interlayer should not change in a visual rating by the appearance of blisters, delamination or clouding. All tests methods for durability are performed with the normative arranged quantity and minimal dimensions with an inner polycarbonate sheet of 2 mm. The specimens pass the tests without any appearance of defects.
Furthermore, the resistance against mechanical loads with the analysis of the bonding strength of the interlayer is based on the ball drop test [20] A steel ball with a diameter of 63.5 mm and a mass of 1,030 g falls from a height of 4 m without any initial pulse centrally on the specimen. The composite panel with the dimensions of 500 mm by 500 mm is clamped four sided lineshaped on a steel frame. The steel ball does not penetrate any specimen.
Both glass panes of the laminate made with annealed glass break and show damage and crack formation. By using chemically strengthened thin glass only the upper pane breaks. After the impact, no fragments of glass above the critical size of 40 mm detaches from the bottom side or the top side. Additionally, the splitter mass of the bottom thin glass pane is under 1.4 g for annealed thin glass and 0.0 g for chemically strengthened thin glass. The analysed specimens comply with the requirements for the mechanical load by a hard impact and ensure a sufficient adhesion of the interlayer.
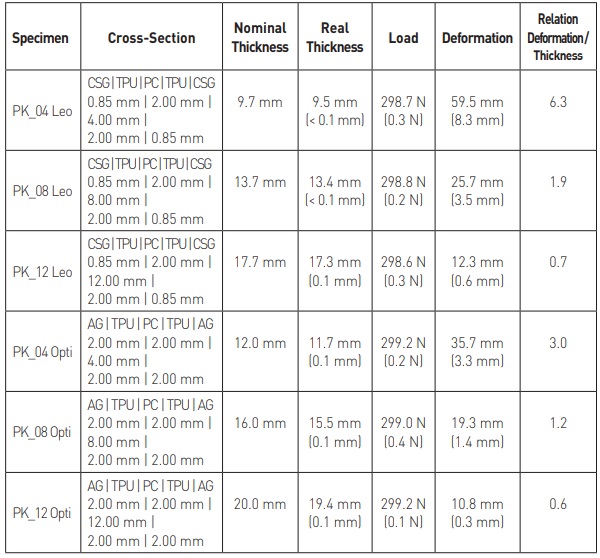
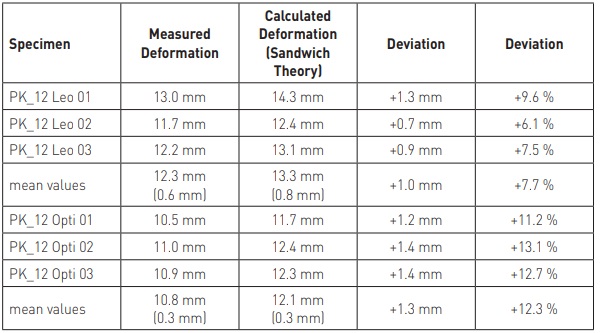
5.2 Applications of Thin Glass-Polycarbonate Composite Panels and Investigation as Security Glazing
The results of the structural behaviour and the enhanced properties as laminated safety glass show the possibility of thin glass-polycarbonate composite panels as an innovative alternative to conventional laminated safety glass. The basic function as passive safety of a laminated safety glass can be verified by the innovative laminate.
Additional requirements on laminated safety glass leads to security glazing with an active safety which violent exterior attacks like manual attack, bullet attack or explosion resists. In this case, the composite panel is tested for a resistance against manual attack. EN 356 [21] describes the test method for a specimen with a dimension of 1,100 mm by 900 mm. The test results are independent of the already realised investigation.
Subsequently, the minimum cross-section may be modified with additional glass panes, polycarbonate sheets or with sheets of a higher nominal thickness. The resistance class for a break-through glazing depends on the number of loosening and axe strikes until the formation of a 400 mm by 400 mm opening in the middle of the specimen. The nominal thickness of the laminate can be reduced for each resistance class by using thin glass panes. Furthermore, the chemically strengthened thin glass reduces significantly the dead load. Figure 5 shows the results of the highest resistance class P8B in comparison to common security glazing made of laminated safety glass.
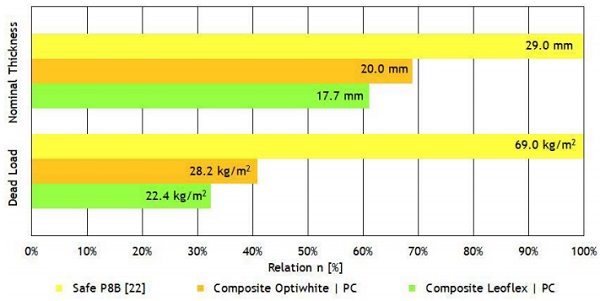
6 Conclusion
The combination of thin glass and polycarbonate enables a laminated safety glass with high performance to security glazing. The structural behaviour of thin glasspolycarbonate composite panels is analysed with the four point bending test in comparison to the theory of sandwich beams. For validation of the sandwich theory, the Young’s modulus used in the analytic method is calculated by the numerical non-linear method with the finite element program SJ Mepla 5.0.0.
The results of specimens with a 12 mm polycarbonate core from the sandwich theory are compared to the measurement results. The mean value differences are smaller than 12.3 %. The application of the sandwich beam theory under consideration of the Young’s modulus from the numeric results leads to a weaker model with conservative results. Under consideration of a time-dependent non-linear material law of the interlayer, the differences could be reduced further. For the tested thin glass Leoflex the local bending stiffness is insignificant.
Optiwhite laminated with polycarbonate shows a neglect of the face bending stiffness with an inner polycarbonate core thicker than 5 mm and a consideration of a stiff core by the local bending stiffness with thicknesses larger than 8 mm. Nevertheless, the linear theory of sandwich beams possesses an acceptable conservative approximation for thin glasspolycarbonate composite panels. Due to the large deformation, a thin glass-polycarbonate composite panel should be used as vertical glazing.
Additional research on the lamination and the durability demonstrate an application as laminated safety glass. Furthermore, the lamination of the strong thin glass and the impact resisting polycarbonate provides a high resistance class against manual attack with slight cross-sections. The innovative laminate is up to 39 % thinner and 68 % lighter than common security glazing. This enables a thinner design for frames and support structures. Retrofitting into existing buildings and further processing to insulation glass will be more simply.
7 Acknowledgements
The research project was part of the research initiative Zukunft Bau and financially supported by the German Federal Ministry of Environment, Nature Conservation, Building and Nuclear Safety. Special thanks go to the co-operation partner SiLATEC Sicherheits- und Laminatglastechnik GmbH for providing of numerous specimens.
8 Literature
[1] Knaack, U.; Klein, T.; Bilow, M.; Auer, T.: Façades: Principles of Construction. Birkhauser, 2014.
[2] Davies, M.: A Wall for All Seasons. In: RIBA Journal 88, pp. 55-57. London, 1981.
[3] EN 13830: Curtain walling - Product standard. Berlin: Beuth, 2015.
[4] EN ISO 12543-1: Glass in building - Laminated glass and laminated safety glass - Part 1: Definitions and description of component parts. Berlin: Beuth, 2011.
[5] EN ISO 12543-2: Glass in building - Laminated glass and laminated safety glass - Part 2: Laminated safety glass. Berlin: Beuth, 2011.
[6] Weimar, T.: Research on Glass-Polycarbonate Composite Panels. Dissertation. Technische Universität Dresden, 2011.
[7] Weimar, T., Hahn, C., Andrés López, S.: Entwicklung von Verbundtafeln aus innovativem Dünnglas und Polycarbonat. Report. Fraunhofer IRB, 2018.
[8] LeoflexTM. Datasheet. Asahi Flass Co., Ltd., 2015.
[9] Optiwhite®. Datasheet. Pilkington Deutschland AG, 2011.
[10] Lexan® 9030. Datasheet. SABIC Deutschland GmbH, 2014.
[11] TPU. Datasheet. SiLATEC Sicherheits- und Laminatglastechnik GmbH, 2017.
[12] Allen, H.G.: Analysis and design of structural sandwich panels. London: Pergmon, 1969.
[13] EN 1288-3: Glass in building - Determination of the bending strength of glass - Part 3: Test with specimen supported at two points (four point bending). Berlin: Beuth, 2000.
[14] Overend, M., Butchart, C., Lambert, H., Prassas, M.: The mechanical performance of laminated hybrid-glass units. Composite Structures 110, pp. 163-173. Elsevier Ltd., 2014.
[15] Zenkert, D.: The Handbook of Sandwich Construction. EMA Publishing. United Kingdom, 1997.
[16] Stamm, K., Witte, H.: Sandwichkonstruktionen – Berechnung, Fertigung, Ausführung. Dortmund: Springer-Verlag, 1974.
[17] DIN 18008-1: Glass in Building - Design and construction rules - Part 1: Terms and general bases. Berlin: Beuth, 2010.
[18] Weimar, T., Andrés López, S.: Development of Thin Glass-Polycarbonate Composite Panels. Engineered Transparency 2018. Düsseldorf, 2018.
[19] EN ISO 12543-4: Glass in building - Laminated glass and laminated safety glass - Part 4: Test methods for durability. Berlin: Beuth, 2011.
[20] EN 14449: Glass in building - Laminated glass and laminated safety glass – Evaluation of conformity/Product standard. Berlin: Beuth, 2005.
[21] EN 356: Glass in building - Security glazing - Testing and classification of resistance against manual attack. Berlin: Beuth, 2000.
[22] SAFE P8B. Datasheet. Glas Trösch BeratungsGmbH, 2018.