First presented at GPD 2019
However, due to the more stringent energy efficiency requirements imposed to buildings, efforts have been initiated by manufacturers to propose transparent insulating glass units. These new designs have a transparent spacer in the vertical visible glass edge whilst the horizontal edges are typically still using a conventional spacer, including the desiccant needed to guarantee a dry atmosphere within the cavity.
The result is a nearly seamless overall view with maximum transparency and the same technical characteristics of the IGU. Glass, PC or PMMA are typical materials used today as spacer, but they have the main disadvantage of being hard and rigid which makes manufacturing complex and time consuming and limits the freedom of shape design.
This paper discusses design possibilities and material properties offered by a clear silicone pre-casted in a rectangular spacer shape. The silicone transparent spacer is flexible and can be adhered to glass and several other substrates to ensure dimensional stability to the IGU and offer full flexibility in terms of design.
1. Introduction
The need for higher transparency in façades has led to the steady development of larger and larger glasses. The former ‘jumbo size’ - the maximum dimensions of a glass sheetglass was 6,000 x 3,210mm up to 2007 and has since then been drastically outdone.
Until recently, nearly seamless appearance of large-scale glass façades could only be reached with laminated safety glass since the edge of insulating glass units typically is non-transparent. However, due to the more stringent energy efficiency requirements imposed to buildings, efforts have been initiated by glass manufacturers to propose fully transparent insulating glass units [1, 2].
Instead of the conventional wide vertical black joints made of spacers and silicone, transparent spacers are used on two visible vertical edges. Transparent materials such as glass, polycarbonate (PC) or polymethylmethacrylate (PMMA) are rigid enough to guarantee dimensional stability of the IGU when bonded to the glass panes, typically using transparent two-sided tapes. This bonding process is however adding significant cost and implies a complex, manual and time-consuming production process.
The hard nature of the PC or PMMA spacers, typically around 80-100 on the D scale [3], results in difficult cutting to the required dimensions and furthermore hampers a good wetting onto the double-sided tape, leading to potential bubble formation and thus impaired IGU edge aesthetics. Furthermore, the rigidity of the spacer will add a lot of stress on the pressure sensitive adhesive used to bond the spacer to the glass during thermal cycles.
Finally, the rigidity limits the freedom of shape design to units with straight edges. As they are most often hidden, the horizontal edges will typically continue to use a conventional spacer, including the desiccant needed to guarantee a dry atmosphere within the cavity. To ensure long term durability, the use of a primary (typically black) polyisobutyl (PIB) barrier against moisture penetration is essential and additional design efforts are needed to include it in the IGU design in an invisible way.
Dow recently developed a new two-part condensation-cure technology, which enables bulk cure of silicone materials within a few days at room temperature. This new polymerization system leads to cured materials that exhibit a broad range of possible hardness, i.e. from very soft gels (Shore 00) to soft elastomers (Shore A). The new cure system can easily be formulated without fillers, to produce materials that exhibit a crystal-clear appearance.
Fillers are however useful to impart a non-sag rheology and to improve mechanical properties, such as tensile strength or tear resistance and in some case adhesion to substrates. Formulating crystal clear materials, i.e., without fillers, will therefore limit tensile properties. Moreover, before cure these materials are flowable and will be difficult to apply on vertical joints or in between substrates to be bonded together.
However, it is noteworthy that materials produced with the new two-part condensation cure technology can after cure of the product react with and develop durable adhesion on various substrates. In contrast to the new condensation curing silicones, post cure bonding cannot be obtained with standard condensation cure and addition cure silicone elastomers.
A new type of flexible, perfectly transparent molded elastomers having the capability to adhere can therefore be manufactured using this new chemistry. These cured articles can be bonded to many substrates using a reactive interlayer. This paper discusses the potential offered by these unique features to produce crystal clear IGU assemblies.
2. Technical properties of the cured crystal-clear silicone
a. Identification
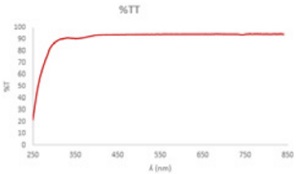
Clarity of the spacer is generally measured by visual inspection; no specific standards or specifications are set for spacer materials. The optical transmittance according to ASTM D1003 [4] demonstrates that the clear spacer has ≥90% of light transmittance for wavelengths between 380 and 760nm, see Figure 1.
The hardness was measured by texture analyzer at 50 (shore 00 scale) according to ASTM D-2240 [5] and the tack strength at 13g. The specific gravity was measured at 0.97 g/ml. The thermal conductivity, thanks to the absence of filler material, was measured at 0.16W/mK according to EN ISO 12667 [6].
b. Adhesion development
A unique feature of the technology is the ability to chemically bond the silicone elastomer to a substrate by applying a common primer onto the substrate. This process is relatively straightforward and fast. Float glass substrates should be treated with DOWSIL™ 1200 OS Primer a commercial Primer from Dow which has been used according to the manufacturer’s instructions.
Strips of the new silicone should be left to cure for about 7 days at 23ºC and 50% relative humidity in a mold of the appropriate shape. to obtain dimensions suitable for a spacer. Dimensions of the cured strips are 2 meters long with a section of either about 14x10 mm or 12x12 mm. This process is illustrated on Figure2.
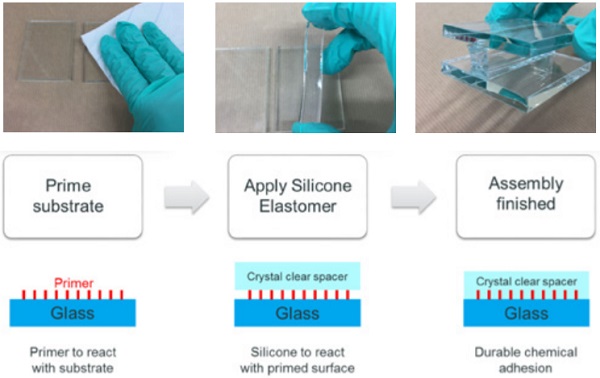
About 10 cm in length strips were cut after full cure of the product. They were applied to the substrates at different times after the application of DOWSIL™ 1200 OS Primer. The adhesion of the strips to the float glass substrate was examined after a determined time using peel testing as shown on Figure 3.
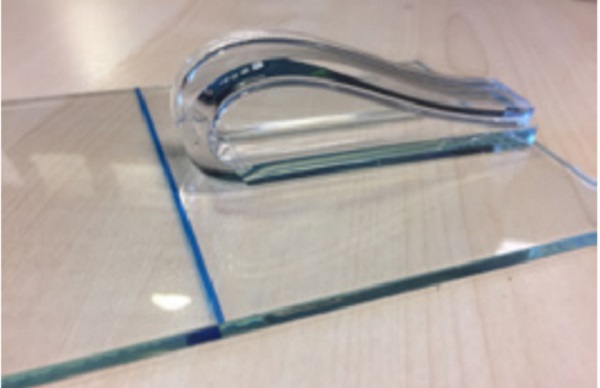
“Primer time” is defined as the time between the primer application and the assembly After the primer time, parts are assembled by simple contact between the silicone and the substrates. A few minutes (2-5 minutes) after contacting parts they have enough green strength to be moved. The time between the contact of parts and the testing is referred to as the “Testing time” or “Contact time”.
Adhesion build-up is extremely fast considering that the material applied is a solid cured elastomer. After about 3 minutes of Primer time and about 3 minutes of Testing time, chemical adhesion is achieved between the silicone and the glass. It is interesting to note that a minimum time is required prior to application of the strip on the primer. Before this critical moment, adhesion will not occur even after a long period of contact.
When the primer is applied directly on the silicone strip, no adhesion will be developed even after long contact time with the substrate. These observations suggest that the minimum primer time is the time required for the primer to bond chemically to the substrate. If applied before this critical period, the strip will react with the primer and bonding with the substrate will not occur. After the critical time the primer is attached to the glass. The strip in contact with the substrate will require a minimum period to react with the primed surface.
At low humidity, both critical primer time and contact time are increased before cohesive failure can be observed. At higher temperature, the adhesion build-up is reduced to 1 min critical primer time and 1 min critical contact time, which can be short for assembling units together.
From 3 to 10 minutes, a general rule is: x minutes primer time leads to x minutes contact time. After 10 minutes contact time is much longer to achieve adhesion.
Good adhesion can also be obtained on other substrates than glass. Adhesion will be developed on many plastics and even PMMA if the contact time is longer (30 min). Peel testing was carried out on additional substrates such as stainless steel, copper, and more difficult substrates such as leather, silicones, highlighting that adhesion on these primed surfaces is obtained.
c. Mechanical strength
To quantify the bonding strength of the silicone strip, glass H-pieces were produced using the priming technique described above. The strip dimensions were approximately 12.5 x 10 x 50 mm³. Three H-pieces were assembled for each testing carried out and the average of the three values are reported.
The tensile properties of the produced H-pieces were determined using a Zwick tensiometer at a speed of about 5 mm/min according to EN ISO 8339 [7]. Table 2 shows results obtained with glass substrates with the strip applied on the non-tin side. Adhesion is excellent before and after accelerated ageing in various environments.
There is some variability in the tensile strength, which is related to the variability in the tear resistance of the strips produced. Any defect in the strip can induce early failure in the H-piece. Considering this impact, results obtained are very consistent. Tensile strength of 40kPa (5.6psi) is obtained at break for an elongation at break of 90%. This is equivalent to 40kg load per linear meter with a 10mm bondline. Similar results were obtained on the tin side of the glass.
One of the most severe accelerated ageing test environments is in hot water immersion, like outlined in the ETAG002 standard [8]. On both sides of the glass very consistent results were obtained, which demonstrate the longterm durability of the chemical bond formed between the spacer and the glass. In comparison, some conventional filled twopart tin-based silicone formulations applied uncured onto the primed glass do not exhibit this level of adhesion durability.
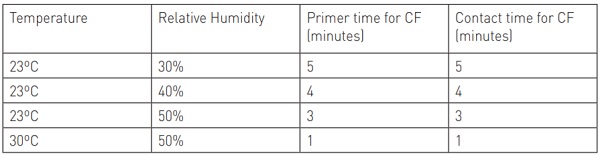
3. Application as spacer in transparent IGU
As mentioned before, the new clear silicone combines low hardness, excellent adhesion and durability. These properties ensure efficient and quick production process as it eases the cutting to the required dimensions, as well as the wetting and adhesion of the spacer onto the glass surface. The flexibility of the spacer allows for complex shapes.
To prove the potential offered by the technology as transparent spacer for IGU, three designs concepts were defined and for each concept, and for each concept three IGUs were manufactured and tested through a specifically developed procedure to determine their durability and lifetime expectancy.
Dimensions of tested IGU correspond with the conventional size for EN1279-2 [9] testing, i.e. 350x500mm. Annealed glass panes of 3mm thickness were bonded using a transparent spacer of width g= 12mm, and height b = 12mm. A plastic bag containing 60 g of desiccant was enclosed in the cavity of each manufactured unit to monitor the moisture pick-up, the plastic bag was punctured to allow for moisture ingress.
A bag of desiccant, identical to the bag enclosed in the cavity, was directly exposed in the climate chambers with the IGU to serve as a reference.
The units were manufactured and immediately exposed in a climate chamber to various conditions of temperature and relative humidity: 23°C and 50% RH and 50°C and 80% RH. These conditions were maintained throughout the test, i.e. without cycling and therefore the test procedure deviates from the EN1279-2.
a. Design option 1: no edge protection
The first design option would not be suitable for outdoor exposure since it is limited to sealing the full perimeter of the IGU using the transparent spacer. No primary and no secondary seal were used. The goal of this system is to act as a reference for the performance of the silicone alone. Figure 4 shows the concept and figure 5 the realized IGU. The edges of the spacers were bonded using a conventional bi-component silicone DOWSIL ™ 3362 Insulating Glass Sealant. However, transparent silicones could as well be used for the bonds.
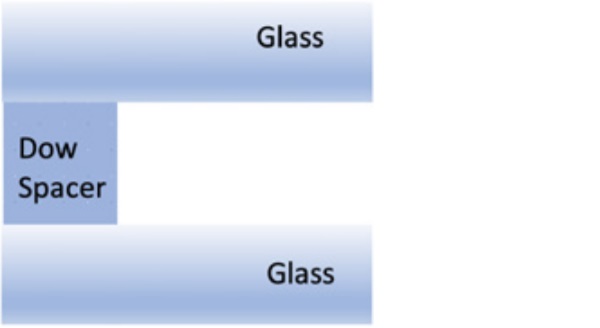
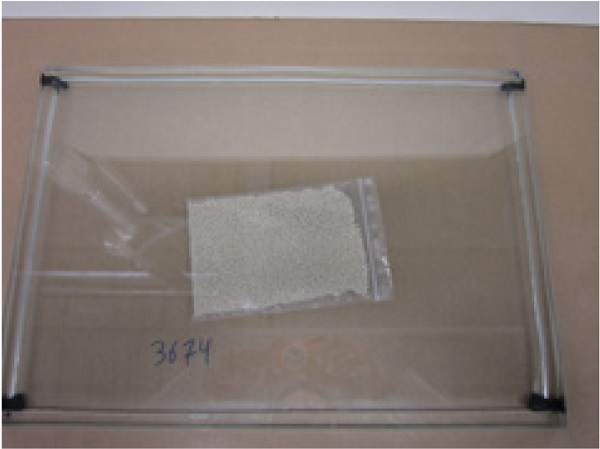
b. Design option 2: aluminum foil protection
In the second concept, the transparent spacer edge is protected using an aluminum foil of thickness 20µm. The goal is to ensure physical protection of the spacer but as well to act as a potential barrier for moisture ingress. The spacer edge is slightly misaligned by 1 mm versus the edge of the glass panes of the IGU.
Adhesion of the aluminum foil on the spacer is obtained with DOWSIL™ 1200 OS Primer. The primer should be applied on the substrates before the substrate is pressed on the spacer. The foil does not adhere to the edges of the glass panes. The spacer is closed using DOWSIL ™3362 Insulating Glass Sealant.
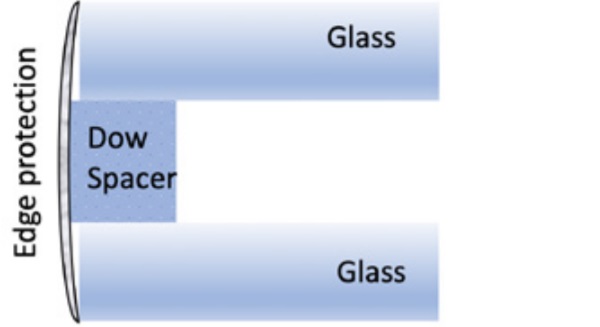
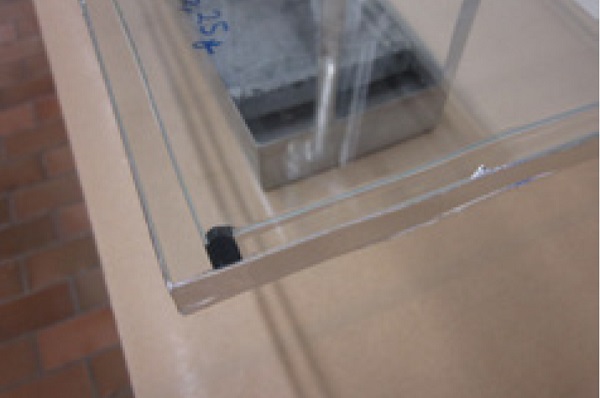
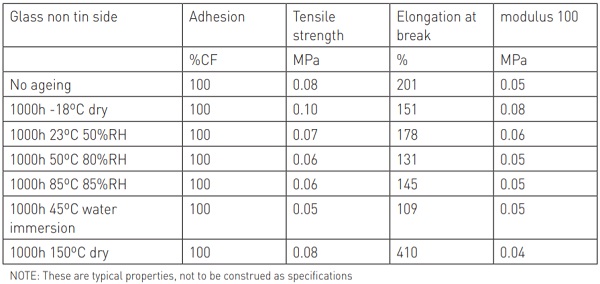
c. Design option 3: aluminum foil and PIB
In the third concept, PIB is applied on the edge of the glass underneath the aluminum foil, to add an extra barrier to the moisture ingress. Doing this, the edge is now perfectly flat. The PIB used is from Kömmerling (GD117) [10]. A thickness of 1 was used which results in a perfectly flat edge thanks to the original displacement of 1mm between spacer and glass edges. The transparency remains very high despite the use of the black PIB.
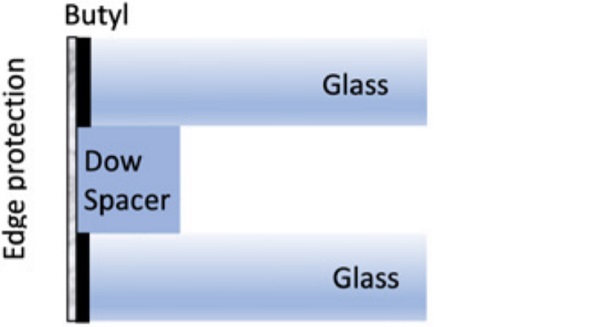
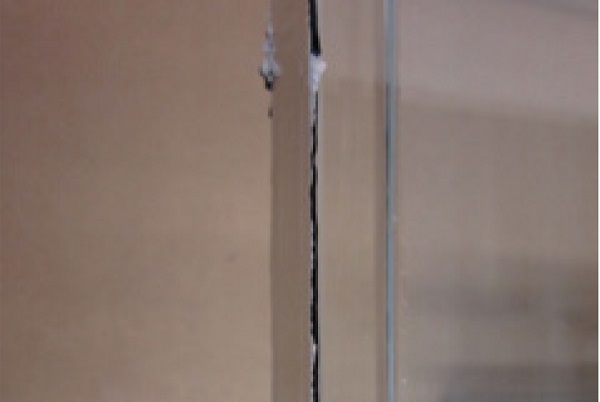
d. Performance
Exposure of the units at room temperature and RH conditions results in a rapid increase of the weight of the molecular sieve bag, as the moisture penetrates the bag. Saturation is reached after 100days whereby the weight does not increase anymore. Consequently, whenever this value is reached signifies the IGU has reached the end of its lifetime expectancy. The different IGU concepts show a more progressive linear moisture uptake. Saturation is reached around 350days for all concepts except the combination 3.
This can be explained for the other concepts by the absence of a primary barrier with low permeability to moisture. Moisture permeability is governed by the diffusion coefficient and for unfilled silicones, like the new spacer, the moisture vapor transmission rate was measured at 19.4 g/m² according to EN1279-4 [11], which is higher than filled silicones used for secondary sealing of IGU. Elevated temperature and high relative humidity lead to a significant increase in the speed of saturation.
Based on these test results, the service life for the different concepts was predicted as a function of the content of desiccant for concept 3 whereby a primary barrier is integrated in the system and systems without primary seal. Based on the data from the figure 11, a linear fit was used as a model to predict the service life of an IG unit in function of the amount of desiccant present in the system. This is expressed per linear meter of the crystal-clear spacer used in the IG unit.
The use of the PIB allows as expected to increase drastically the lifetime expectancy for the typical desiccant amounts used. A possible strategy to avoid the use of the butyl primary seal is to add more desiccant or to use a replace-able desiccant device connected to the inner cavity [12].
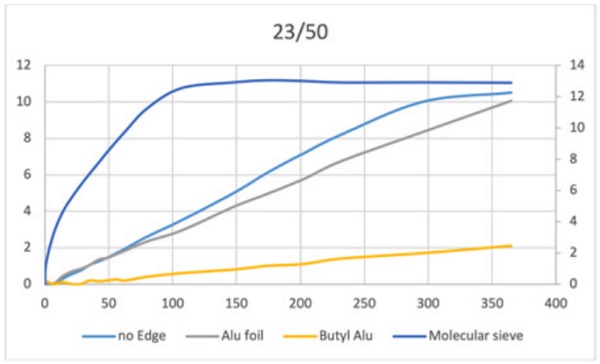
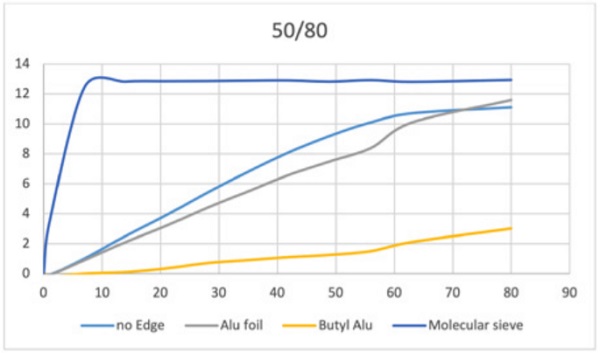
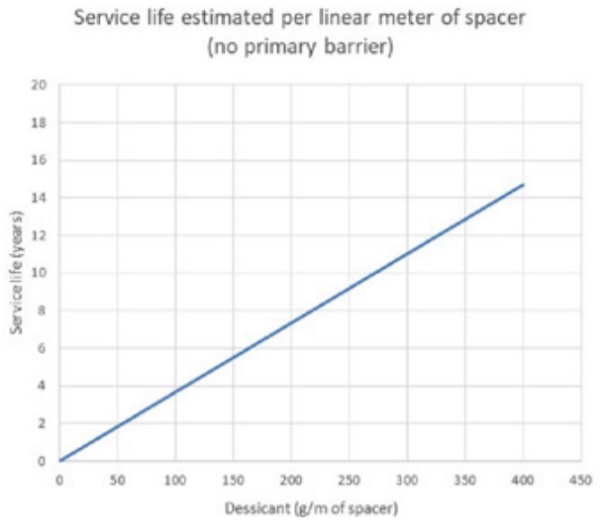
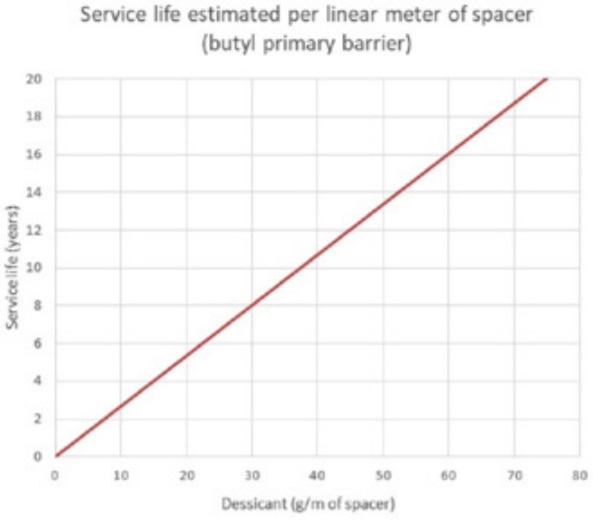
4. Conclusions
A new crystal-clear silicone adhesive technology allowing on-demand adhesion on various substrates has been developed. As far as assembling of parts is concerned the curing system brings a new perspective in the industry. For the first time, a pre-cured silicone part can be glued to various substrates with the use of a primer forming a covalent bond. The durability of this bond is excellent with reactive substrates, such as glass and metal while it does not resist water immersion for unreactive substrates such as plastics. whereas the initial potential offered by this bonding technique to produce crystal-clear components has been partially demonstrated, several design elements still need clarification, for example regarding the integration of the desiccant in an elegant way. Different options already used by the industry (conventionally built horizontal edges or integration of the desiccant in the bottom of the IGU) could be applied to this clear technology.
References
1. AGC Thermobel Scena: http://www.agc-glass.eu/en/news/press-release/discover-beauty-framelesswindow-thermobel-scena-agc , accessed 30/04/2019
2. Sedak Isopure® for more transparency, https://www.sedak.com/fileadmin/user_upload/pdf/Englisch/Brochures/190328_sedak_isopure_EN.pdf, accessed 12/04/2019
3. Matweb http://www.matweb.com/
4. ASTM D1003-13, Standard Test Method for Haze and Luminous Transmittance of Transparent Plastics
5. ASTM D2240-15, Standard Test Method for Rubber Property—Durometer Hardness
6. EN 12667-2001, Thermal performance of building materials and products. Determination of thermal resistance by means of guarded hot plate and heat flow meter methods. Products of high and medium thermal resistance
7. ISO 8339, Building construction -- Sealants -- Determination of tensile properties (Extension to break)
8. EOTA, ETAG002, Structural Sealant Glazing Systems Part 1: Supported and Unsupported Systems
9. EN1279-2, Glass in building. Insulating glass units. Long term test method and requirements for moisture penetration
10. GD115, Kömmerling
11. EN1279-4, Glass in Building. Insulating Glass Units. Methods of test for the physical attributes of edge seal components and inserts
12. Dodd G., Structural Glass Sandwich Panels, GPD 2017, Tampere
NOTICE: No freedom from infringement of any patent owned by Dow or others is to be inferred. Because use conditions and applicable laws may differ from one location to another and may change with time, Customer is responsible for determining whether products and the information in this document are appropriate for Customer’s use. The product described in this literature may not be available for sale and/or available in all geographies where Dow is represented. The claims made may not have been approved for use in all countries. Dow assumes no obligation or liability for the information in this document. NO WARRANTIES ARE GIVEN; ALL IMPLIED WARRANTIES OR MERCHANTABILITY OR FITNESS FOR A PARTICULAR PURPOSE ARE EXPRESSLY EXCLUDED. ™® Trademark of The Dow Chemical Company (“Dow”) or an affiliated company of Dow.