First presented at GPD 2019
Two concepts are mainly discussed especially in high-profile markets like London or Switzerland: Closed Cavity Façades (CCF) adopting the concept of pressurized multilayer ETFE-foil cushion constructions and Self-Conditioning Façades (SCF) using the concept of pressure relaxed insulated glass.
Both concepts were formed by available technological solutions. The necessary technological effort for CCF and the extended design efforts for SCF can be avoided by relying on a simpler and modular glazing typology, which is the result of current developments for the next generation of double-skin façades, called ISOshade®. The paper will explain the element itself, its advantages and various installation possibilities.
Introduction
The double-skin façade is the result of a global demand for new ways to save and use energy sustainably, in conjunction with the financial running costs of the façade.
The advantages of double-skin façades lay in an increased performance of the skin regarding acoustics, individual ventilation and conditioning concepts. An additional benefit is the protection of sunscreens, improving the user comfort especially in high-rise buildings.
Double-skin façades are categorized by three separation concepts between cavity and interior. The concepts differ in a pressuredependent exchange of the interior and cavity air (exchange systems), an outflow of interior air into the cavity (extract systems) and a complete separation of the air streams (buffer systems). The air streams within the different separation concepts are driven either mechanically or naturally.
This technical contribution examines the characteristics of Closed Cavity Façades (CCF), Self-Conditioning Façades (SCF) and ISOshade® as the latest development of double-skin façades.
Limiting Cases and Challenges for Closed Cavity Façades
The development of closed cavity façades was driven by the need of an easy to handle doubleskin solution for high-rise buildings with office use. Typical predecessors used much more floor space and required a lot of maintenance. The unitized CCF concept simplified the glazing element in order to provide shading, light control and regulation functions as well as climate load management in one system. [1-3] Realized projects are mostly high-rise buildings with office use.
Closed cavity façades use pressurized air supply or a ventilation system known from the concept of pressurized multilayer ETFEfoil cushion constructions. Dried, filtered and sometimes tempered air enables to manage condensation for the cushion constructions.
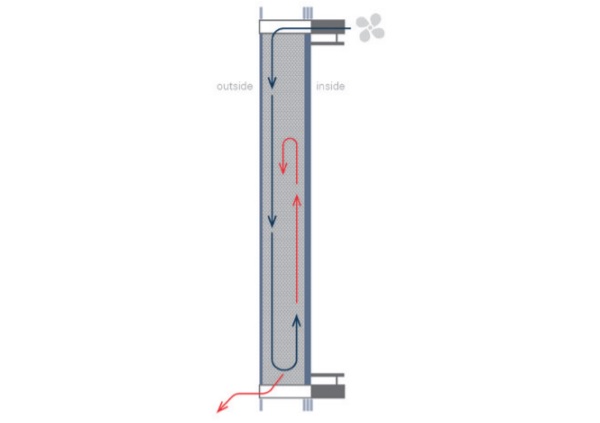
Mechanically driven vents or compressors, stainless steel pipework and valves are used as an air supply system. Filtration and exclusion of any contaminations of the supply air is essential in order to ensure a performing cavity condition.
The design needs to configure a system with an appropriate air flow rate in order to avoid condensation under almost every environmental condition, to handle climatic and other pressure induced loads, and to minimize energy consumption. The challenge of the development laid in understanding the influences of heating and cooling on the special geometry and in the development of a defined flow process in order to avoid congestion as well as heating.
Special challenges for closed cavity façade solutions arose in material compatibility due to the used, dried air and the interdependencies between plastic materials, hydrofluorocarbons and the fogging of glass. This makes developments and individual use in projects both complex and expensive, as very high-quality and tested components have to be used.
In addition, the planning effort for the mechanical systems is laborious and requires a great amount of detailed coordination. The unitized glazed elements must also be manufactured in ultra-clean rooms and need a conditioning over the entire further processing and supply chain. This is particularly important when CCF technology is used i.e. in North America or Asia, in order to coordinate the delivery and assembly process accordingly.
A façade for a museum in Hong Kong, for example, was equipped with up to 9 m long glass tubes using CCF technology to operate them all year round in a humid climate. The setup enables to use completely glazed tubes with minimal joining details while keeping them conditioned properly.
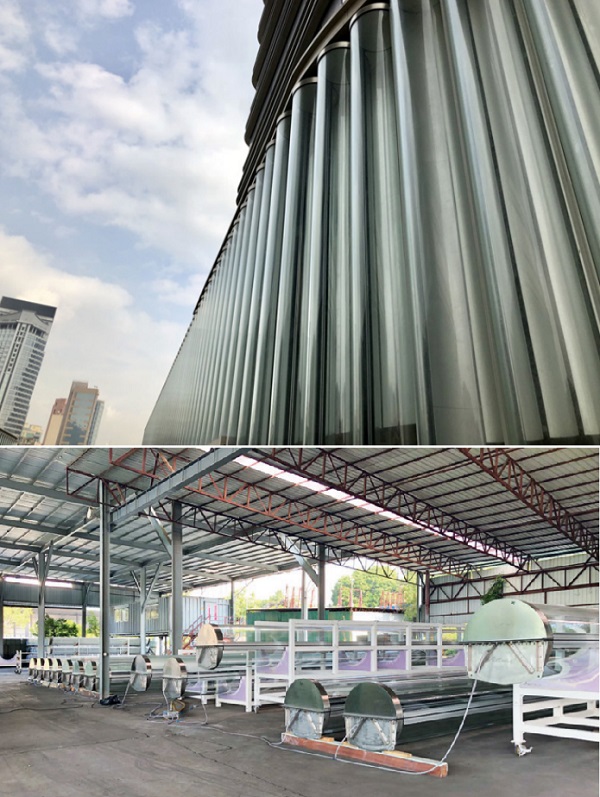
Limiting Cases and Challenges for Self-Conditioning Façades
Self-conditioning façades adopt the concept of pressure equalized insulated glass, using natural ventilation without mechanical aid. Pressure compensation and air exchange is achieved by coupling the cavity to the exterior. The air exchange is necessary to balance the vapor conditions and control condensation. The conditioning of the cavity is self-regulating during its entire service life.
It is balanced by the coordinated interaction between the thermal properties of the façade and fluidmechanical effects in the cavity and outside. The conditioning takes place with a minimal exchange of air not affecting the thermal performance significantly.
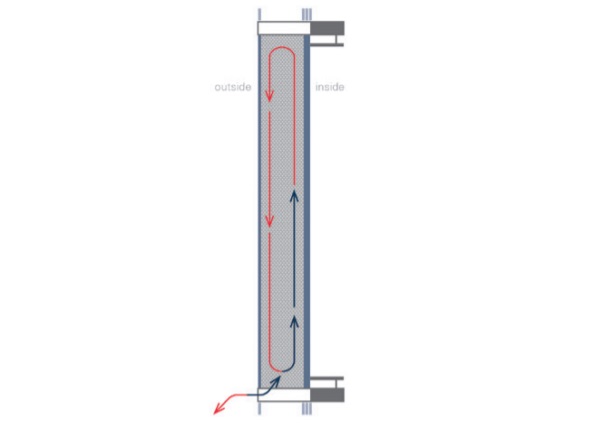
The design of a passive façade requires a precise understanding of the prevailing conditions regarding climate, micro-climate and site conditions. Relevant parameters are interior, exterior and cavity air temperatures as well as surface temperatures including their dew point temperatures. The exterior and cavity humidity are relevant for the hydrothermal conditions, the resulting dew point and the surface temperatures. [4, 5]
Designing for these parameters lead to a reliable and autonomous system. Critical situations for these systems are cooling phases during clear summer nights. High temperatures and high levels of humidity over the course of the day and a steep temperature drop overnight due to clear sky radiation define the most relevant threshold.
Tests showed that the effect of the temperature drops can be influenced through system design. A continuous offset between surface temperature of the inner glass panes and the dew point is necessary. [4, 5] Closed cavity systems realize this offset between surface temperature and dew point through a flow rate with dried air.
Realized projects are multiple story buildings with office or residential use. Each project requires an exact design of the thermal properties of the individual glass layers, their coatings and consideration of the façade orientation and external influences.
For a multistory office building at Principal Place, London/UK extensive research and testing on boundary conditions were realized to use the SCF typology with coating-free, ultra-transparent elements with sizes up to 3 x 7 m. The challenge for the application was the realization of the sunscreen for the element sizes with certified materials. [6] Another challenge for self-conditioned façade solutions is the adjustment and monitoring of climatic conditions during transport and the construction stages.
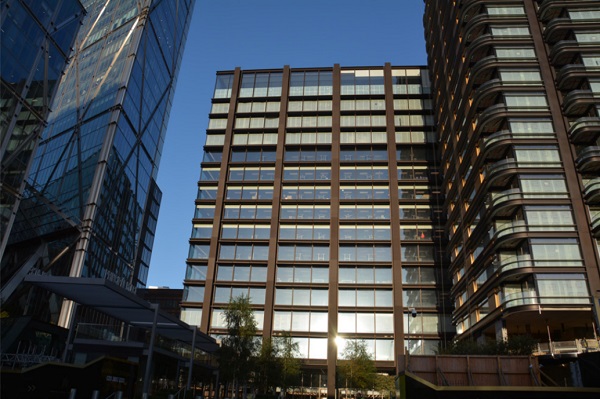
Unitized buffer systems – ISOshade®
In addition to the specific challenges for unitized buffer systems, there are common difficulties that need to be solved through further developments with additional marketable technological solutions. A general issue is its material usage especially when designing for integrated sunscreens. [6]
The influence of elevated temperatures on used components and the compatibility of materials especially the used plastics needs to be considered during design. Close cooperation between component manufacturers for sunscreens and façade manufacturers as well as chemical investigations at certification and research facilities enable customers and manufacturers to gain greater certainty in using these buffer façades.
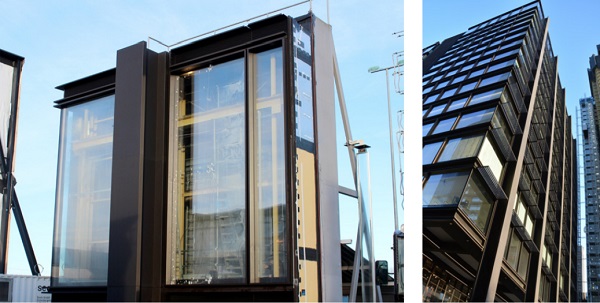
On the one hand the concept of closed cavity systems would be strengthened greatly by avoiding mechanical ventilation and pipework. The required design of selfconditioning façades on the other hand is costly and complex. Two reasons, why buffer technologies using drying agents for humidity and phase change materials for temperature management are investigated in order to establish a natural ventilated but robust alternative.
The necessary technological effort for CCF and the extended design efforts for SCF can be avoided with a simpler and more modular glazing typology. An insulating glass unit with triple glazing and a sunblind in a cavity using a newly developed, micrometer-sized, filtered pressure compensation technology and buffer technologies for heat and humidity is called ISOshade® from iconic skin GmbH.
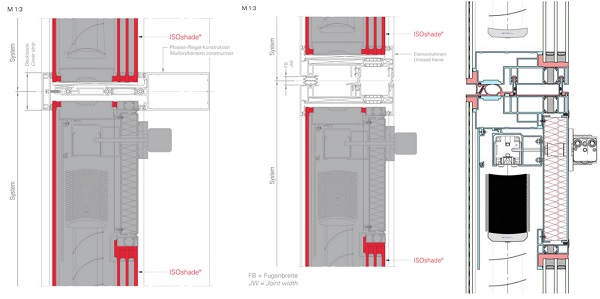
This product offers a new generation of selfconditioning insulating glass units and fills the gap between CCF as an operational system with flexibility integrating it into existing stick or unitized systems, offering a wide field of application independent of a complex climaterelated design.
The concept of ISOshade® is based on a hermetically sealed cavity fabricated in a clean room. A special pressure compensation system maintains the permissible climate loads in the cavity. This system ensures that, as temperatures fluctuate, the pressure in the cavity is kept at a permissible level. For further protection against condensation, the spacers are filled with a desiccant. The cavity conditions itself via a volume-dependent system.
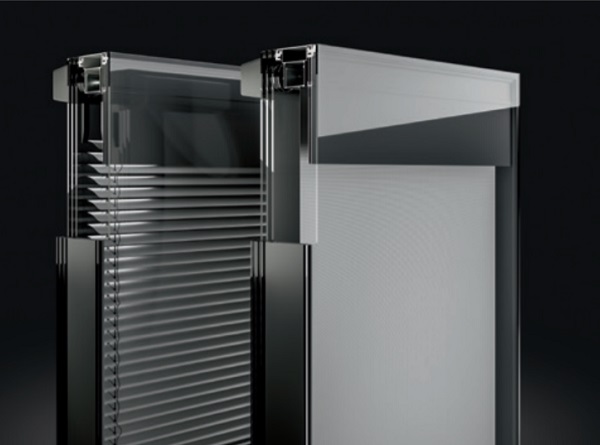
To analyze and determine characteristics of modern façade concepts the Fraunhofer Institute for Building Physics offers the possibility to install façade units in a laboratory test building (VERU) in Holzkirchen, Germany (see Figure 6). This enables to conduct longterm observations and measurements of the building envelope with respect to realistic climate conditions.
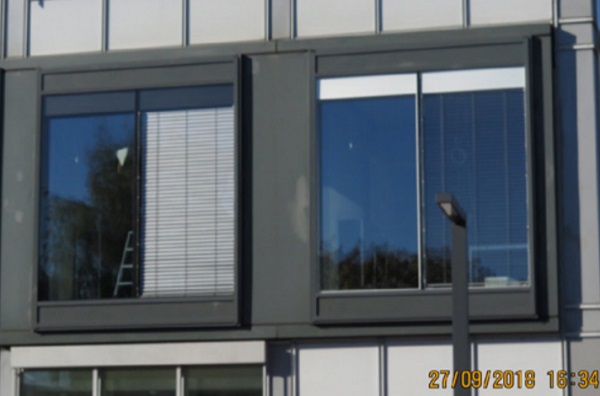
Within the development of the ISOshade® concept, long-term measurements have been performed on a ISOshade® sample unit to monitor climate situation within the cavity. Air / surface temperatures and humidity levels were analyzed to evaluate the functionality of the concept and confirm the theoretical ideas and thermal relations (as shown in Figure 7).
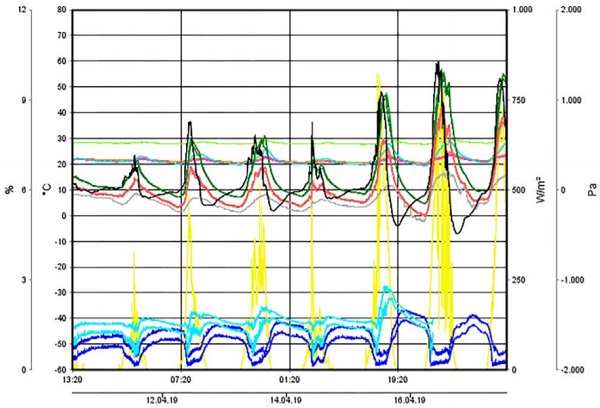
A façade for a museum in Augsburg, for example, has been realized with ISOshade® elements (figure 8). The museum’s new glass façade is made up of three elements each nearly 7m high. The exposed, frameless façade in structural glazing look fulfils the highest demands in terms of design and transparency. At the same time, the ISOshade® elements satisfy thermal and sound insulation requirements and provide sun shading that can be varied to protect the sensitive exhibits against UV light.
Focus on environmental, architectural and social quality is needed in addition to the insulation properties of an assembly. A major issue is resource consumption. A typical SCF emits two times and a CCF three times more greenhouse gas equivalents than a spandrel and double-glazing curtain wall reference over its lifetime. [7]
Therefore, ISOshade® is designed much more consciously with regard to the reduction of resource consumption and the possibilities for prolonging the lifetime were consistently considered. Each unit is developed to be able to overhaul it several times and extend the lifetime of the energy consuming parts. A continuous monitoring of production steps offers valuable information for a product, material supply and production process optimization. In addition, optional monitoring of the condition of the elements during operation enables maintenance and service to be carried out as required.
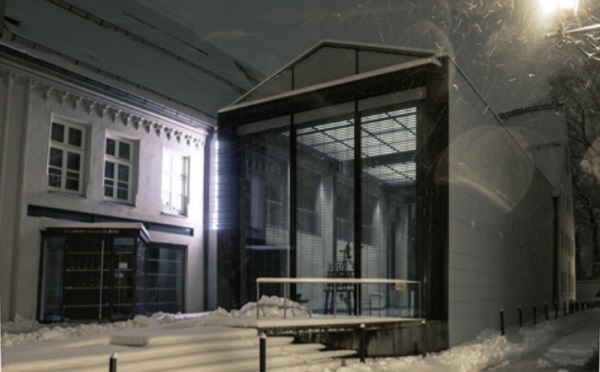
Conclusion
The necessary technological effort for CCF and the extended design efforts for SCF can be avoided with easy to handle, multilayer glazing typology like ISOshade®. Buffer technologies for humidity as well as enhanced pressure equalizers are used to solve the basic physical challenges.
Nevertheless, local conditions and project demands are specific. Therefore, the methods for the façade design process are improved in industry as well. Product simulations and processed monitoring data are integrated into digital planning tools to support the professional team. Next generations of such planning tools will help to develop the appropriate and most suitable design alternative faster and more profound. [8] This requires functional models and an interoperability of the essential data between project developers, professional team, specialized contractors and building operators.
These trends influenced the development of ISOshade® in two ways. On the one hand, the product was engineered with the systematic of insulating glass panes. The easily configurable product is suitable for stick system or unitized façades and can be used by every metal construction company. These low entry requirements for product installers will also provide to planners, customers and operators through digital tools such as configuration assistants or monitoring services and digital lifecycle information.
The end-to-end support of the different lifecycle phases of a product is already in use in other industries such as automation engineering. It thus represents a valuable influence for reviewing the processes in the construction industry and for improving them with digital services and tools as well.
References
[1] Herzog, T.; Krippner, R.; Lang,W. (2004): façade manual, Birkhäuser.
[2] Knaack, U.; Klein, T.; Bilow, M. et al. (2014): Façades: Construction Principals, Birkhäuser.
[3] Crosbie, M. (2005): Curtain Walls: Recent Developments by Cesar Pelli, Birkhäuser.
[4] Cseh, X. (2013): Numerical Modelling of Unpressurized Double-Skin Façades, BauhausUniversität Weimar.
[5] Fraunhofer Institut für Bauphysik (2014): Research Report.
[6] Rehner, C. (2014): Bauphysikalische Betrachtung von textilen Sonnenschutzelementen in einem geschlossenen, druckentspannten Fassadensystem, Augsburg: Hochschule Augsburg.
[7] Souviron, J. (2016): Producing Transparency: An Energy and Material Flows Analysis of Glazing and Membrane Façades and their Potential of Hybridisationean, Ecole Nationale des Ponts et Chaussées Paris.
[8] Schmid, Fabian C. (2015): Methodological and Systematic Design of Future Façade Solutions, Springer.