This paper was first presented at GPD 2015 by Saverio Pasetto from Skanska Construction UK Ltd.
Abstract
Anisotropy, or leopard spots, are the terms used in the façade and glass industry to describe the manifestation of patterns and colourful areas in heat-treated glass, under certain light and viewing conditions. The phenomenon is often the subject of disagreements that may eventually lead to disputes, between the cladding supply chain and designers/specifiers and their clients [1].
The causes of anisotropy and the conditions that may affect it were reviewed through the literature and the current state of the art production and measurement processes that aim to minimise its visibility. This revealed that the visibility of this phenomenon is dependent on polarised light, viewing angle and stresses in the glass plate, the latter being a function of the temperature distribution during the heat treatment process.
A limited number of specialist glass suppliers appeared to have altered their tempering equipment and processes to reduce the phenomenon. State of the art scanners may be able to measure and analyse anisotropy patterns and enable the dedicated design and operation of the tempering ovens to reduce the visibility of anisotropic phenomena. This is an important step for the glass industry that have historically maintained that this unavoidable issue could not be mitigated.
The on-going development of measuring equipment is also crucial to objectively define acceptance and rejection parameters. These may be incorporated in future revisions of regulatory Standards and guidelines, in which anisotropy is currently not considered a defect but a visible effect. This is in contrast to a number of specifications that demand glass with reduced anisotropy or with no anisotropy
The results of a detailed survey administered to 35 key stakeholders (architects, glass suppliers, specialist façade contractors and façade consultants) highlighted the division between the supply chain, that accepted the phenomenon, and designers and their clients, who aspired to have glass with reduced anisotropy.
It also highlighted the need for a detailed explanation of anisotropy and the inadequacy of current standards, which lack objective acceptance parameters as much as specifications, thus attracting protracted qualifications and the potential for disputes. Anisotropy is an important matter for the stakeholders who would like to receive updated information on what causes the phenomenon, what the industry status is and what can be done to reduce its visibility. This study may be used to support such action and inform further research.
Introduction
Anisotropy is the term used in the façade industry to describe the manifestation of patterns and colourful areas in heat-treated glass under certain light and viewing conditions. The phenomenon is caused by stresses embedded in the glass plate as a result of the heat treatment process. The level and distribution of the stresses, which make the glass bi-refringent or doubly-refractive, is a function of the (non-uniform) temperature distribution and heat transfer which are affected by, for example and without limitation, the contact of the glass plate on supporting rollers, the oscillation of the glass plate, the layout and operation of heating pipes and quenching nozzles (note that tempering by air floatation technology was not reviewed during this study).
An earlier study by Redner and Bhat [2] highlighted the non-uniform distribution of the stresses as a result of the tempering process. This results in a complex thermodynamic process and an intricate layout of areas of glass that alter the behaviour of (polarised) light in a relatively different manner, thus resulting in a particular (anisotropic) pattern.
Polarised light, i.e. light that oscillates only in one plane, is a naturally occurring and unavoidable phenomenon that results from natural light reflection and scattering. A detailed explanation of these optical phenomena is provided by Illguth et al. [3] that also proposes a method to measure the anisotropies, and by Henriksen and Leosson [4], that also discuss the reasons and presented examples of certain specific anisotropy patterns and suggested a way to quantify the phenomenon.
Technologies and equipment that promise to measure and reduce visible iridescence have been marketed in the last couple of years. Conversely, a more homogenous distribution of the temperatures throughout the entire heat treatment process results in a more uniform stress distribution and in turn a less disturbing anisotropy pattern.
Figure 1 and Figure 2 show an example of an in-house alteration of the tempering oven carried out by a leading glass supplier in his quest to minimise the visibility of anisotropy. The alteration of the rollers’ design created a more uniform heat distribution that eliminated the central longitudinal band (indicated by the red arrow in Figure 1) and in turn resulted in a more homogeneous and, crucially, less disturbing anisotropy pattern (Figure 2).
The current glass industry standards and guidelines recognise anisotropy as an unavoidable characteristic of heat-treated glass when exposed to certain light conditions, see for example CWCT Technical Note 35 (Assessing the appearance of glass [5]) and the British standard regulating the heat strengthened glass process (BS EN 1863:2011 [6]).
Façade specifications have always been aligned with such standards, however specifications have become, in recent years, increasingly stringent by frequently demanding glass with reduced anisotropy or anisotropy-free glass and by effectively redefining the phenomenon a defect for which glass may be rejected. Conversely the façade industry is struggling to meet such demands due to the limitations of the glass processing that limits what the industry can actually produce.
In addition, factory and on-site glass acceptance and rejection due to anisotropy are essentially based on subjective inspection criteria and supported by extensive sampling, as it is not clear if, and how, the anisotropy can be measured or controlled. The phenomenon is often the subject of disagreements that may eventually lead to disputes between the cladding supply chain, who do not consider it a defect, and designers/specifiers and their clients, who consider it a flaw and want to avoid it.
Objective
This work seeks to identify the extent to which anisotropy in heat-treated glass is perceived as a defect by architects, glass suppliers, specialist façade contractors and façade consultants, and how this affects the U.K. façade industry as a whole. It presents the main results of a survey administered to the stakeholders and seeks to identify the level of clarification required, what the industry state of the art is while examining future challenges and possible ways forward.
Methodology
The background to this research seeks a more explicit yet simple definition of anisotropy, as a phenomenon, and its causes. To accomplish this a comprehensive review of glass as an architectural product and the relevant literature was conducted, with particular focus on the processes that contribute to anisotropy. This was supported by an appraisal of the current state of the art glass manufacture and, crucially, if and how visually disturbing anisotropy in architectural glass was measured and controlled. The resulting industry context was compared to existing industry standards, guidelines and specifications.
An initial pilot survey highlighted the tension between the demand for anisotropy-free glass in current specifications and the challenges faced by the façade industry that relies on the glass industry to meet such demands. The outputs of this initial pilot survey were used to inform a more detailed survey designed to assess the knowledge and perception as it relates to anisotropy in glass of key façade industry stakeholders. The results established the magnitude of the problem, highlighted any associated shortcomings and showed how the different stakeholders currently dealt with anisotropy. This was used to identify possible and sustainable ways forward, potentially improving the standards and guidelines related to anisotropy in architectural glass.
Results
The survey was administered in March/April 2014 to 37 industry stakeholders including architects (10 no.), façade consultants (9 no.), glass suppliers (8 no.) and specialist façade contractors (10 no.). 35 questionnaires were returned giving an overall response rate of 95%, demonstrating considerable industry interest on the phenomenon. All but one respondent expressed their interest in receiving more information about the phenomenon and its effect(s) on the façade and glass industry. Notably, six respondents wished to remain anonymous: four of these were suppliers who were perhaps less inclined to openly share their views.
At least 60% of the participants considered the phenomenon either critical or important at tender, production and handover stages: it would appear that it is slightly less of an issue (43%) after the project completion (Figure 3).
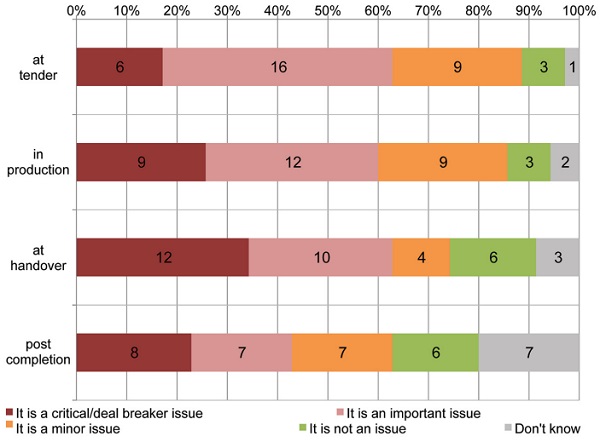
While the majority of the survey respondents (43%) believed that anisotropy in glass could be addressed, there was also considerable uncertainty as over a third were not sure that this was the case, while 20% believed that it could not be addressed (Figure 4). These responses confirm the industry confusion, and division, as it relates to this phenomenon.
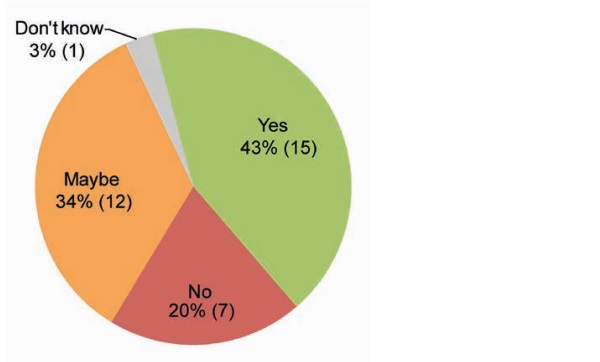
One major glass supplier is currently marketing glass with reduced anisotropy and the R&D efforts of at least another one as previously shown have given satisfactory results. Private communications with the supply chain confirmed that operation, knowhow and maintenance are crucial to obtain the best results. Contrary to the historical position of the glass industry, it would therefore appear possible to influence the visual impact of this phenomenon.
For 69% of the respondents, the current industry standards and guidelines were not adequate to regulate anisotropy and only four respondents believed that they were. Anisotropy is recognised as an inevitable effect of the heat treatment processes by current British Standards regulating such processes (i.e. BS EN 1863:2011 [6], BS EN 12150:2000 [7], BS EN 14179:2005 [8]) and glass industry guidelines.
The reviewed documents appear to be consistent in terms of explanations for the phenomenon, also referred therein as leopard spots, iridescence, quench marks or strain patterns. Four of the reviewed documents, only one of which is a British Standard (BS EN 1863:2011), clearly state that anisotropy is not a defect. However, this important statement is expected to appear in the next revision of the British Standard for toughened glass (BS EN 12150) and may contribute to improved clarity of the standards.
This appears to be in contrast with the current aspirations by clients and their designers to procure glass without visible anisotropy. Further revisions to glass standards may also need to consider the progress currently being made by the glass industry to assess and reduce the phenomenon, and ideally list measurement processes along with anisotropy acceptance and rejection criteria and parameters.
In addition, it should be noticed that glass is hardly used as a monolithic product these days. Heat-treated glass may be coated, fritted, laminated and used in combinations to form complex products that in turn can be used to form complicated double and triple insulated glass units. These numerous and varied configurations may influence the visibility of anisotropy, and therefore should be referred to in the relevant standards, that currently do not, alongside comprehensive guidelines. The detailed assessment of such influence may require dedicated research, however this lies outside the remit of this study.
Despite not being defined a defect by glass industry standards and guidelines, anisotropy is perceived as a fault by 26% of those interviewed. Perhaps not surprisingly, further analysis of the data as shown in Figure 5 revealed that Architects and Façade Consultants account for 78% of those who stated that the phenomenon is a defect. For these two groups building aesthetics are paramount hence a higher demand for quality is expected. Conversely, the position of the remainder is consistent with that of the current glass regulating standards.
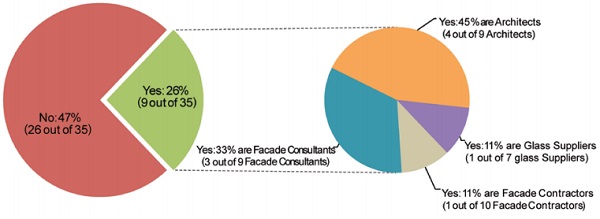
The majority of the respondents (51%) confirmed that their clients were not prepared to pay more to avoid issues, or take the risk, associated with anisotropy. Depending on the type of contract and specifications, the risk was, in this case, conveniently transferred “free-of-charge” to the supply chain. On the other hand, just over a quarter of the participants (26%) stated that clients may be prepared to pay more to reduce risks associated with anisotropy, while 23% did not know.
There currently is a trend to avoid the use of heat-treated glass so as to avoid issues with anisotropy and this was confirmed by 40% of the respondents. Avoiding heat-treated glass altogether is not always possible due to the variety of applications that the product is suitable for (e.g. increased strength, safety breakage in the case of fully toughened glass, fritting/enamel panel processing, holes and notches) and is therefore not a sustainable way to resolve the anisotropy issue.
Conclusions and Summary
Specific investments and research by some industry players appear to confirm that the degree of visibility of the phenomenon, which remains unavoidable, can be altered and minimised to produce glass with less disturbing anisotropy. However, the magnitude of the associated cost remains unclear and may require a dedicated market study. The design of the tempering oven, and in turn temperature and stress distributions, is critical to address the visibility of the pattern, as are its operation and maintenance.
The development of anisotropy measurement equipment is critical to analyse the stresses and their distribution, and in turn optimise tempering oven design and heat treatment temperature distribution to reduce anisotropy visibility. The measuring equipment is also fundamental to defining objective acceptance and rejection parameters. These can be used not only for benchmarking, sampling and quality control but also, if and when agreed by the industry as a whole, to redefine the regulating standards.
The current standards are being revised to clarify that anisotropy is not a defect. On the other hand, the glass industry, or rather some of its key players, are making good progress to quantify and minimise the phenomenon and its effects, and are therefore potentially moving toward meeting clients and designer aspirations. This may create an impasse that could be resolved ad-interim by guidelines and technical notes, but ultimately require future revisions of the standards. Unfortunately this may be a lengthy process due to the natural latency in revised document consultation periods prior to ratification and final publication.
The results of the survey confirmed that the façade industry is divided between the supply chain accepting anisotropy, and designers/ specifiers seeking to have glass with reduced anisotropy. This matter is important for the stakeholders and while progress and products from a limited number of suppliers appear to be able to satisfy their glazing aspirations, clients appear not to be willing to pay the additional cost. The survey responses confirmed that there is a trend towards not specifying heat-treated glass to avoid issues with anisotropy. Regulating standards are currently inadequate and may need to be updated to reflect current industry progress and include objective acceptance and rejection criteria for use in specifications if anisotropy is to be considered a defect.
If the anisotropy issue is not resolved to the satisfaction of all parties then the current situation will only get worse and more confused, as demands for virtually fault-free glass become ever more prevalent. Conversely, it may be possible for the tempering oven supply chain industry to translate the issue into an innovation opportunity
References
[1] Pasetto, S., 2014 Anisotropy as a defect in U.K. architectural float heat-treated glass, Dissertation for MSc in Façade Engineering University of Bath, U.K.
[2] Redner, A.S. and Bhat, G.K., 1999 Advanced method of measuring surface stress using digital image analysis based readout Proceedings of the Glass Processing Days, 13-16 June 1999, Tampere (Finland): Glass Processing Days, pp. 671-673
[3] Illguth, M., et al. The effect of optical anisotropies on building glass façades and its measurement methods Frontiers of Architectural Research (2015), http://dx.doi.org/10.1016/j.foar.2015.01.004
[4] Henriksen, T. and Leosson, K., 2009 Anisotropy and Optical distortion in architectural glass, can it be controlled Proceedings of the Glass Performance Days, 12-15 June 2009, Tampere (Finland): Glass Performance Days, pp. 834-839
[5] CWCT Technical Note No. 35, 2003 Assessing the appearance of glass. December 2003 CWCT, U.K.
[6] BS EN 1863 Part 1:2011 and Part 2:2004 Glass in building - Heat strengthened soda lime silicate glass BSI
[7] BS EN 12150 Part 1:2000 and Part 2:2004 and prEN 12150-1:2012 Glass in building - Thermally toughened soda lime silicate safety glass BSI
[8] BS EN 14179 (Parts 1 and 2): 2005 Glass in building - Heat soaked thermally toughened soda lime silicate safety glass BSI
Acknowledgements
This work was supported by Skanska Construction UK Ltd.
The author would like to thank all the survey participants and in particular Dr. Steve Lo of the University of Bath.
A particular thank also goes to Arcon and Glaston for their invited workshops, private communications and support.