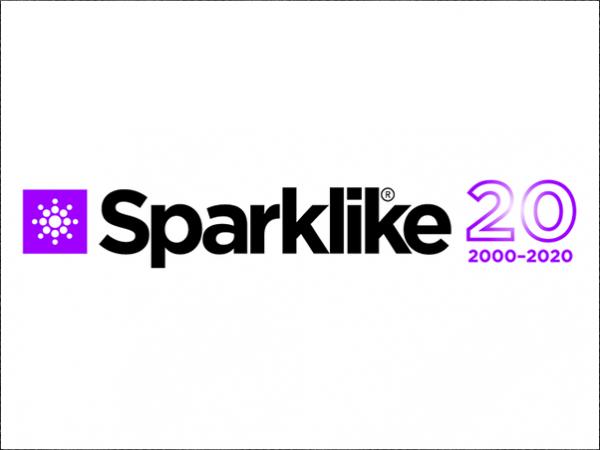
Date: 27 January 2020
Sparklike is the developer of the world's first non-invasive gas analyser for insulating glass. Our Sparklike Handheld™ and Sparklike Laser™ devices has become the de facto world standard for gas fill measurement of IGUs. Sparklike products are used on a daily basis by the leading insulated glass manufacturers, testing laboratories and window processors world-wide.
To meet tightening industry standards and keep pace with the fast developments of state-of-the-art glass manufacturing, Sparklike has developed a new laser based technology for IG line integrated solutions for gas fill measuring, Sparklike Online™.
Alongside the technology, this article discusses the advantages of gas fill for thermal performance and the developments in gas fill measurement. This is the first article of the Sparklike 20 year anniversary series, detailing the history of Sparklike, development of the products as well as the technology development generally.
Insulating enhancement in modern IGUs
A common insulating enhancement in modern IGUs is filling it with argon, krypton or xenon gas to increase the energy efficiency, slow the transfer of heat as well as improve the general performance of the glass. The insulating gas is applied to the cavity, either during the manufacturing process at a gas press station or manually to the ready-made units.
As product liability for the insulating glass often lasts several years after initial delivery, window suppliers are constantly looking at new ways to increase the security of the gas fill. The challenge usually lies in confirming the correct filling degree and ensuring that the initial gas concentration remains inside the insulating glass unit (IGU).
Glazing & Energy-efficiency
Today’s architectural design favours the use of glass both as a structural element as well as a way to improve lighting inside. At the same time, glass windows are one of the most sensitive building components when it comes to assuring energy-efficiency in construction.
Energy flows in and out of buildings – depending on their location and prevailing weather conditions – has been a traditional focus of attention for building owners and their suppliers particularly in view of increasing energy costs. The window industry has responded to the energy-efficiency requirement by developing different types of insulated glass structures.
Multiple layer glazing, double or triple-pane solutions and insulated glass units (IGUs) utilize advanced insulation materials ranging from glass types, frames, sealants and cavity fills to maximize the thermal performance and minimize the U-factor – energy penetration through the glass. Double and triple glazing, gas fill and specific coatings have contributed immensely to the energy-efficiency of windows and become the best solution and state-of-the-art choice for high-performance IGUs.
Views on gas fill
Glass manufacturers of today are looking to maximize resistance to heat conductivity, and thus minimize the outflow of energy through the window. To date, this is best done by noble gas between the glass layers of an IGU. A vacuum solution between the glass panes (vacuum insulated glass) provides great temperature insulation performance, but due to price as well as technical limitations, these are seldom used in window designs of today.
Air fill is an option but the use of noble gases provides superior resistance to heat conductivity in comparison with air. While air has a thermal conductivity of 0.024, argon with 0.016 is only 67 % of that, and krypton at 0.0088, is just half the conductivity of argon (Thermal conductivities).
The favoured gas is, however, argon because it is the most cost-effective noble gas to use. Compared to Argon, krypton is typically 200-300 times more expensive and xenon even more so. Estimates show that the raw material costs of producing well-sealed argon-filled IGUs, compared to air-filled ones, will go up by only 1 %. Regardless of the choice of fill, the gas content of an IGU is generally considered to be adequate when exceeding 90 %.
Different markets have different standards for gas content, but generally the gas content is to exceed 90 % with a margin, although some regions have approved lower standards that match the quality performance of their local IGU- manufacturing closer. The challenge for IGU suppliers is verifying this figure by reliable measurement as solid evidence of consistent product quality. (EN 1279-3: 2002; Standard test method for determining argon concentration in sealed insulating glass units using gas chromatography.)
Insulating glass performance – the reason for quality control
For IGU producers, the key high quality and energy-efficient solutions lie in proper processing of advanced glass products, such as tempered, laminated and coated glass as well as skilful sealing of the gas-filled IGUs. Yearly gas fill escape due to the pressure difference between outside conditions and the gas-filled cavity is maximum 1%.
This escape is considered normal and acceptable. The requirement for manufacturing quality naturally includes ensuring successful and adequate gas-fill. If the processing quality is not on a high enough level, the gas escape could be much higher than this, leading to quality problems in the glass, and at worst, it could cause the collapsing of an entire glass structure.
Adequate measurement
The difficulty for IGU manufacturers has been ensuring that the performance quality of the product is adequate and the inert gas-fill up to standards. Traditionally insulation gas fill was tested by taking random samples off the production line and drilling holes in the glass to measure gas fill and thus the insulation performance of the IG-unit (Argon gas fill and insulated glass units).
This was a functioning, though costly method that involved breaking the glass and destroying the expensive product either on the processing line as part of manufacturing quality control or doing the same to an already installed IGU in the field. In other words, there was no available method to measure the gas fill without tampering with the product.
In the past, no method to measure gas fill in the production line as part of manufacturing on-line quality control was available. Thus, leaving out the possibility to gain gas content information from every piece produced, impairing the possibility to efficiently control the quality of the production line. For more information on insulating glass manufacturing and quality control, see our web page.
The world´s first and only non-destructive insulating gas analyzers
Controlling and determining the gas concentration inside the insulating glass units requires effective and reliable tools to meet the increasing and tightening industry requirements. The Sparklike IG gas analyzers allows non-destructive and IG-line integrated measurement of IGUs.
THE SPARKLIKE PRODUCT RANGE CONSISTS OF:
- Sparklike Handheld™ – Portable and battery operated gas fill measurement of standard double glazed IGUs
- Sparklike Lasers™ - Measuring IG gas fill of triple and double glazed units
- Sparklike Line Integrated Solutions™ - Sparklike Online(™)
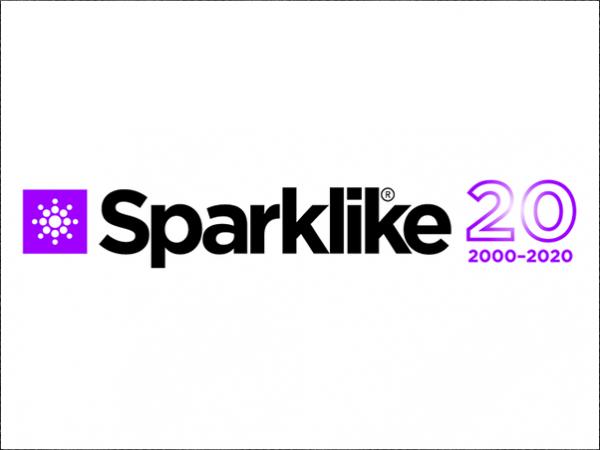

Add new comment