Authors: Ali Ahani & Elshan Ahani
Source: Hybrid Advances, Volume 3, August 2023, 100063, ISSN 2773-207X, ScienceDirect, Elsevier B.V.
(https://www.sciencedirect.com/science/article/pii/S2773207X23000465)
DOI: https://doi.org/10.1016/j.hybadv.2023.100063
Abstract
The attachment of more than one glass layer through the polymeric interlayer results in the formation of laminated glass. In contrast to other glass types, laminated glass offers better breakage resistance, post-breakage safety, and protection against noise. The breakage resistance and post-breakage safety of laminated glass in residential and commercial buildings hold critical prominence and laminated glass sustainability is being investigated in academia and industry. This study conducts a survey of the literature to identify and discuss various materials and design approaches incorporated to augment the sustainability of laminated glass. The mechanical properties augmentation of the laminated glass through material incorporation has been studied. Similarly, the safety and sustainability augmentation through Finite Element (FE) analysis has also been reviewed. This study considers various simulations of the impact and blast loading on laminated glass through FE models. The material and FE design revelations of this study will impart practical insights into laminated glass sustainability augmentation approaches.
1. Introduction
The hypothesis of composite materials in the 1970s was nothing more than an engineering curiosity [1], the progress of which in the past half-century demonstrates the significance and importance of such materials that can introduce to engineering materials as well. The simplest definition for composite is refer to it as the amalgamation of two other materials in the macro scale to produce a third component with better anticipated mechanical characteristics [1,2]. Therefore, laminated composites consist of at least two bonded layers of different materials to acquire a component with more satisfactory quality. The prosperous uses of composites in various features of industry, are including but not limited to construction, electronics, aerospace, biomedical, automotive, energy, etc. [1,3,4]. Concrete is the simplest composite material in the building industry. However, the use of composites in the building industry is not limited to concrete. Various types of Fiber Reinforced Polymer (FRP) in retrofitting and rehabilitation industry, including but not limited to Polypropylene (PP) fibers, Plain Cementitious Composites (PCCs), Latex polymer Cementitious Composites (LCCs) in the production of High-Performance Concrete (HPC) industry, the compound of Aluminum Trihydroxide (ATH) and Poly Methyl Methacrylate (PMMA) acrylic resin in façade industry, and Polyacrylamide (PAM) synthesis of which may apply for stabilization of unstable soils are examples of the use of composites in civil industry [5].
1.1. Historical overview
However, the endeavors of Arthur T. Fullicks in mounting glass pieces together and John Crane Woods in using transparent cellulose between glasses sheets are praiseworthy Edouard Benedictus, a French chemist, was the first to introduce laminated safety glass by using gelatin in the interior layers of it [6,7]. Laminated glasses were produced regarding the concept of composite materials in which a layer is going to protect the rest of the layers. Various types of glasses, like heat-strengthened and annealed glasses due to their considerable post-failure load-bearing capacity, are used in external layers of laminated glasses. For the layer panels, fully tempered glasses are also utilized. The production process requires extra implementation, where concerning the using causes employed for secondary processes, including edge working, hole drilling, curving, coating, thermal treatment, insulating, etc., after production may also consider for laminated glass [8]. They are most often utilized in places subjected to human injuries [[9], [10], [11], [12]], or glass sheds may lead to further harm [7,13]. As an instance of sandwich composite, laminated glass is made from two high-strength external layers and a low-strength core layer. The outer layers foremost are undertaking the internal forces caused by bending while the shear stresses are imposing to the core layer that propagating them over a larger area [[14], [15], [16]]. In Fig. 1 schematics of laminated glass has been illustrated.
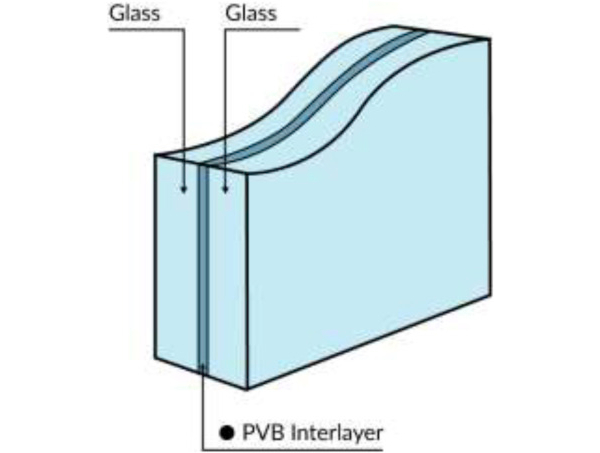
1.2. Interlayers
Because of its ability to barricade UV radiation, Polyvinyl Butyral (PVB) is the most commonly used material for the interlayers of laminated glasses [8,10]. However, because of its UV resistance content Ionoplast (SentryGlas (SG)) is also used as an interlayer element in laminated glasses, which provides more safety [17]. The nominal thickness of a single layer PVB is around 0.38 mm that may mostly use in 1, 2, or 4 layers as an interlayer for laminated glasses. The material is quite sensitive to the load duration and the temperature, where the elongation at room temperature could be around 200% and in the temperature below 0 °C could transfer shear stress completely. Liquid Crystal (LC) is an interlayer film that consists of two outer polyester layers and a polymer matrix, the combination of which is a voltage-sensitive substance that has also been used in the production of laminated glass interlayers [8]. Suspended Particle Devices (SPDs) and Photovoltaic (PV) cells that are used along with Ethylene Vinyl Acetate (EVA) are the other types of interlayer elements in laminated glasses [8,17].
General expression and their features for the most widely used interlayer elements have been illustrated inTable 1. By employing different interlayers, laminated glasses may be used in fire protection glass, bullet-resistant glass, blast-resistant glass, etc. [8,10]. Apart from its uses in gas masks and windows during World War I and using various interlayer elements from Canadian balsam and gelatin to the transparent cellulose nitrate and PVB, laminated glass has a wide variety of applications in wide ranges of industries. Because of their high shock-resistance, break-resistance, and sound-insolating content, in Europe and America, laminated glasses are widely used in residential areas and touchy structures [10]. As a decorative, nonstructural, and structural element, laminated glasses are also used in household decorations, surface partitions, skylights, storefronts, and building façades [8,10,18].
Table 1. Most widely used interlayer elements their commercially available thickness and general application.
1.3. Simulation
In this regard, various pieces of research related to the performance of laminated glasses in façades have been performed [19]. in a numerical study, via LS-DYNA FEM software, assessed the performance of laminated glass windows under blast loads. According to the results, the outcomes may lead to an approach to obtain the better performance of laminated glass windows due to blast loads. According to Ref. [20]; façades are the first defensive element against external excitations, and even though glass elements have a high-pressure resistance, their tensile strength is limited that leads to detrimental consequences due to external events. In the study, the interlayer element of the laminated glass has to adjust to the demanded level for obtaining desirable safety. In an experimental study [21], have evaluated the in-plane behavioral content of non-structural façade glasses due to seismic excitations. Accordingly, the result demonstrates the in-plane displacement of the façade leads to high-stress concentration and premature failure.
Accurate structural analyses such as Finite Element Methods (FEM) for laminated glasses in the structures have increased the pace of their uses in the building industry. The FEM has been used to determine the buckling behavior, blast behavior, post-failure behavior, etc., of the laminated glasses [8,20,22]. For instance, outcomes of the numerical studies performed by the DYNA-2D FEM code demonstrate that the Hertzian cone is the main failure mode of laminated architectural glass due to windborne debris impacts [23,24]. [25] implemented the discrete element modeling (DEM) for behavior prediction of broken LG. There is a convergence between the empirical study and the numerical approach. Regarding the outcomes, the post-failure behavior of the LGs due to the formation of large pointy ends won't confer safety. Phase field strategy has been proposed for the failure mechanism for in-plane loaded Glass [26]. The aforementioned predicts crack distribution and density with acceptable precision. Load transfer between layers is considerably dependent on the interface fracture energy.
The load transferring mechanism for laminated glass before the damage initiation is similar to other materials in the elastic region. The load path changes after the formation of the early failure mechanism in one layer. Load redistribution continues till the fracture pattern forms in the undamaged layer. In other words, initially, the loading procedure is ongoing till the formation of a crack at one of the layers. At this point, the interlayer retains the integrity of the laminated glass and redistributes the loads to the other layer(s). The new path for loading is temporary and last till the failure in the damaged layer completely transfers to the other layers, and the overburdened layer(s) won't bear any extra load. This latter step coincides with the collapse of the load-bearing system [8,17]. However, to deal with this failure [27], introduced two limit states reflecting the additional design situations during and after breakage, namely the “Fracture Limit State” (FLS) and the “Post Fracture Limit State” (PFLS) at the new CEN/TS 19100, Design of glass structures. An experimental study on the tensile behavior of cracked glass has been carried out, and theoretical formulas for the prediction of the behavior proposed by Ref. [28].
Results were indicative that the force-displacement curve for the cracked glass under tensile loading is highly dependent on the finite strains and cohesive zone size. Increased adhesion also results in poorer energy absorption capability in LG. Post-breakage stiffness of laminated glass subjected to uniaxial in-plane loading measured by the use of a homogenized model. Results from both numerical and modeling were almost the same, which was indicative of the accuracy of the proposed method [29]. Two different strategies for the post-breakage response of undamaged and damaged 2-ply Laminated Glass (LG) plates with different interlayers namely, the equivalent temperature variation and elastic-brittle constitutive law have been proposed by Ref. [30]. They observed that the size effect plays an important role in the mechanical response of LG plates, and it should be considered in the design and utilizing the numerical findings of a critical length from which the plates behave as monolithic, independently of the stiffness of the interlayer defined. In a review research carried out by Ref. [31]; They observed the post-breakage tensile stiffness depends on the thickness, the mechanical properties of the interlayer, the size of the glass shards, and the delamination length. Indeed, the tension stiffening is strongly affected by a stress diffusion phenomenon from the regions where the fragments are detached from the interlayer to the bonded zones.
According to various performed experimental studies [[32], [33], [34]] proffered drift-related equations corresponding to the cracking failure of storefronts and curtain walls. Several studies categorized interlayer failure, which happens due to rupture, cut by sharp points of the broken glass, and boundary failure. The process takes place when the interlayer is partially or thoroughly pulled out of the boundary [[35], [36], [37]].
1.4. Sustainability
The most widespread ideas about augmenting various types of glass elements were categorized into three major parts of energy-conserving, load-bearing, and recycling elements, according to which sustainability requirements of expected structures will be obtained [6,18,38]. Because of its transparent content, it can let the light pass through and absorb the solar energy for household appliances along with protecting the environment by barricading extra uses of fossil fuels for electricity production and decreasing the carbon footprints. Accordingly, smart glass panels with authenticated energy-efficient values if have been used in building façades, would actively control solar gain, daylight, thermal emission, etc., which finally leads to lowering the total energy consumption of the structure. The use of smart laminated glass with PVB interlayer and PV cells could respectively barricade the UV radiation and electricity production. By employing the other type of interlayer element or their combination inside the laminated glass, the required energy and service demands of the structure through their façades may be achievable.
Recycling any substance is an effective way to reduce the consumption of earth's resources. Because of its simple structure and accessibility, the root substance of which is silicon dioxide (SiO2), the incipient production component of glass, is widely available. Fortunately, the availability leads to ease in the production of glass almost in every place on the earth. However, it may affect the environment by consuming the substance from the soil sources and leaving the remnants in waste disposal at best. This process may affect the ecosystem and livings through time. The glass remnants from demolished structures, derelicts, etc., could have proper performance as an aggregate in concrete admixtures. Because of their most desirable shapes for use, they could also have some uses as aggregates in asphalt concrete.
Transcendences in technology and numerical evaluation of engineering concepts along with new material discoveries facilitate the use of glass elements in the building industry. The augmentations also lead to the production of structural glasses, which are mostly used in secondary load-bearing elements. Since the utilization of glass as a structural element has had a very shallow background, the reliability of its use as a structural element is not that convenient. However, the mechanical behavior of the element demonstrates that there is a possibility to utilize glasses as primary load-bearing elements inside the structure. According to the provided explanations, using laminated glass as the structural elements in low-rise and high-rise is mostly expectable. The production of structural glass in shaped forms to use in façade elements in exoskeleton structures is also anticipated.
2. Characterization of interlayer materials
It is necessary to characterize the interlayer materials utilized in laminated glass building applications. Resultantly, an interlayer material characterization is supplied, which is centered upon the literature and clustered into three categories: Types and applications, mechanical aspects, and environmental features.
2.1. Types and applications
2.1.1. PVB
Nonlinear strain hardening is the material behavior attributed to the PVB in the state of the art. For modest deformations, linear viscoelasticity is referred as a good model to represent the mechanics, because pressure amplifies exponentially as an aspect of strain functionality. PVB strain rate-dependent tendency was established by Ref. [39] in both tensile and compression testing. PVB is found behaving elastoplastic material in a situation of dynamic tensile loading, yet its functionality tendency is recorded viscoelastic under tensile quasi-static stress. In consideration of both the dynamic and quasi-static loadings, it exhibits viscoelastic behaviour in the compression situation. In addition, the constitution PVB model was carried under the classification of three phases: linear-elastic, bi-exponent-like, and failure.
Several vibrant studies, like the one conducted by Ref. [40] with a rheometer, helped to better comprehend PVB mechanical reaction. The DMA (Dynamic Mechanic Analysis), on the other hand, is a widely acknowledged method for studying polymer mechanical behaviour as a function of time and temperature. PVB is in the glass transition area between 0 and 50 degrees Celsius, according to this methodology. As a result, its dynamic modulus varies dramatically according to temperature and frequency. PVB, on the other hand, exhibits brittleness along small fluctuations representing functionality factors in the dynamic modulus with respect to glassy states [41]. [42] depicted the storage and complex modulus along offset angles of PVB through DMA and time master curves.
PVB's temperature for glass transition and the inflexibility at a specified temperature are affected by the amount of plasticizer it contains. The increase in temperature accordingly amplifies the mobility of polymer chains. This changeover towards free mobility of polymer chains occurs most prominently in the domain glass transition. By raising the plasticizer application, the mobility between chains improves and begins at lesser temperatures resulting into lowering the glass transition temperature. Structural PVB, such as Kuraray's PVB Extra Stiff, has less plasticizer than ordinary PVB. The relaxation curves of standard and structural PVB are shown in Fig. 2. These findings reveal that structural PVB has a higher rigidity than ordinary PVB for a certain particular period, functionality and temperature. The master curves through the utilization of time-temperature shifting CFS algorithm [43] and reference temperature of 10 °C were attained. The change in tendency from glassy to a rubbery causes the most dramatic loss in stiffness, which occurs sooner in conventional PVB than in structural PVB. The shear relocation coefficient, which calculates the sum of horizontal shear force through interlayer towards the glass plies, is another significant mechanical component that must be considered, according to prEN13474-3 (2008). It is a coefficient with a value ranging from 1 to 0, with 1 indicating full shear transfer and 0 indicating no shear transfer [44]. asserted that under short-term loadings, shear transfer coefficient x 14 0:5 should be used instead of x 14 0:25, as specified by the standard [45].
![Fig. 2. Depiction of PVB clear and extra stiff relaxation curves at various temperatures [43].](/sites/default/files/inline-images/Fig2_319.jpg)
2.1.2. Ionoplast
The ionomer is a polymer composed of repeat units, that was designed for inflated demand purposes like laminated glass uncovered to bomb blasts, burglaries, or hurricanes. Even at high temperatures, this interlayer outperforms conventional interlayers in terms of strength and inflexibility. As a result, it's a popular interlayer for systemic laminated glass. Ionoplast’ relaxation master curve vs a structural PVB is shown in Fig. 3. Ionoplast and the same structural PVB are shown in isochronal curves in Fig. 4. The findings reveal that both materials have a similar mechanical reaction at low temperatures and for long periods of time [43].
![Fig. 3. Depiction of Master relaxation curve of PVB extra stiff and sentry glass through shifting CFS algorithm [43].](/sites/default/files/inline-images/Fig3_302.jpg)
![Fig. 4. 60 s duration PVB extra stiff and Ionoplast Isochronal curves [46].](/sites/default/files/inline-images/Fig4_292.jpg)
The systemic connectivity created involving glass plies is a significant advantage of Ionoplast [47]. used Ionoplast in tensile tests and found that it had an elasto-plastic behavior that received impact through strain rate. Excessive strain rates result in more dramatic elongations and advanced capitulated stresses. The ratio of strain, on the other hand, had no discernible effect on the failure strength (above 32 MPa). Ionoplast has a preliminary modulus of elasticity of 200–300 MPa at moderate strain rates and 150 MPa at accordingly higher strain ratio, according to this study. Additionally, the amplification in strain rate decrease the recoverable deformation.
When balanced to alternative interlayers [44], found that Ionoplast laminates have little sliding displacement (PVB and EVA). Furthermore, the usage of shear transfers coefficient x = 1.0 is advised in the case of Ionoplast, which is the interlayer with the greatest value).
2.1.3. EVA
EVA mechanical behavior asserts an imperative dependence with VA substance. Characteristically, elevated VA content is directed in to further rubber-like tendency. As a result, materials with low VA concentration are elastic and pliable. EVA interlayers typically includes and ranges between 32 and 34 percent VA, resulting in a performance that is halfway between the two mentioned behaviors. However, after being laminated with glass, EVA's mechanical characteristics may be considerably altered [48]. used tensile testing on EVA specimens treated to various lamination techniques to investigate this phenomenon. Samples given heat for 3 h at 120 _C, following a process comparable to that used in industrialized degree production, had better mechanical properties: 400 percent failure strain and 12 MPa failure strength. It's also worth noting that the linear portion symbolizes the same approach for all of the procedures under consideration. In laminated glass mechanism, EVA has a higher shear transmission than PVB. In small loadings [44,49], suggested using a shear transfer coefficient of x = 0.7. The value of shear transfer coefficient represents the amount of shear transfer from the interlayer to the glass layers that ranges from 0 to 1. No shear transfer at a joint surface respects with 0 and full shear transfer reflects by 1. Furthermore, the eventual loads of laminates for both EVA and PVB interlayers were found to be equivalent in this investigation.
2.2. Mechanical aspects
2.2.1. Influence of the interlayer
[50] discussed the out-of-plane flexural behavior of laminated glass. The shear pairing connecting glass layers with the polymeric interlayer, which establishes the flexural performance of laminated glass. The special behaviour of laminated glass is based on the layered and monolithic limits, where the stress is not transferred between the layers of glass. Accordingly, the similar tendency is traceable in misplaced layers of laminated glass. The closer association of the interlayer with monolithic limit makes its interlay stronger. The shear stress transmission capability of the interlayer may be affected by its depth [51].
The deformability of the interlayer determines the mechanical behaviour of laminated glass [52]. Hence the mechanical analysis is focused on pairing aptitude of interlayers. Interlayer materials for laminated glass are exposed to a variety of load situations. The range may vary from seconds to several years, which represents the wind pressure and permanent loads, respectively; as well as a variety of heat extremes. The consideration of the viscoelastic behavior of interlayer materials strongly affects their performance in both load duration and temperature.
Experiments to test the mechanical reaction of the interlayer material alone and in combination with laminated glass have been created in a variety of ways. A range of mechanical characterization approaches has been employed in the literature. The considered loads and displacements are linked through the application of various approaches with the associated stress in the domain of laminated glass. In bending tests, the principal resisting material is glass, while the interlayer donates to the compound laminate's cohesiveness. Generally, the interlayer may retain the post-failure integrity of the laminated glass, whereas due to the brittle content of the glass, the interlayer keeps the fragmented particles together via its adhesion.
Therefore, the ductility and toughness of interlayers may also take into account. The interlayers may be affected by environmental parameters, i.e., temperature, moisture and sun radiation. Higher temperatures may increase the deformation content of the interlayer and lowering the temperature could increase the strength. According to its application, one or more layers of interlayers may employ between glass sheets. Since its presence may increase the eventual thickness of composite glasses and the difference between the behavior with that of the glass, the term effective thickness has been introduced. This value provides an alternative thickness for laminated glass by considering the thickness of interlayer/s and the glass elements. Extra information around the effective thickness may be available in Ref. [53] and CEN/TS 19100 [27].
2.2.2. Load duration and temperature impact
The concept around the effect of the temperature were discussed for the better understanding of the interlayers' behavior. E.g. Ref. [44], tested laminated glass specimens with three distinct interlayer materials: Trosifol (PVB), EVASAFE, and Ionoplast, in a four-point bending test. They tested a continued load at three temperatures: 20 °C, 30 °C, and 40 °C. Outcomes show that specimens with PVB, which has up to 100 time's poorer stiffness qualities than Ionoplast, had a larger mid span deflection. Ionoplast -coated specimens had the lowest deflection, followed by EVASAFE-coated specimens. Ionoplast and EVASAFE showed enhanced stealthily resistance at low temperatures, although creep was still present at elevated temperatures, particularly at 40 °C. The findings reveal how the interlayer material's viscoelastic behavior impacts the cohesive behaviour of laminated glass.
The approach of viscoelastic materials is managed by a mixture of elastic and viscous responses, as defined by Hooke's law as in (Eq. (1)) and Newton's law (Eq. (2)). The Maxwell model in which a series joins the elastic element to a viscous component (Eq. (3)) and the Kelvin-Voigt model; where an elastic component is coupled in correspondence with a viscous element (Eq. (4)), are the two most basic models for defining a material's viscoelastic behaviors. A number of Maxwell models are associated as equivalent in the comprehensive Maxwell model (Fig. 5), allocating the better model modification to real viscoelastic behavior.
Where.
![Fig. 5. Depiction of the Maxwell-Wiechert model [54].](/sites/default/files/inline-images/Fig5_285.jpg)
The complex dynamic modulus (E* or G*), with its two prominent components (E0 or G0) are generally adopted to evaluate the mechanical behavior of viscoelastic materials. The mentioned components (E0 or G0) respectively represent the elastic energy that is stowed by the material and loss modulus that refers to the energy vanished by the element in its functionality process. The energy is generally lost as heat resultant of its viscous part. The component referred as elastic is found dominant at low temperature for short-term loading whereas for greater heats and extended loading the viscous component becomes dominant (Fig. 6).
![Fig. 6. Depiction of storage and complex modulus along offset angles of PVB through DMA [42].](/sites/default/files/inline-images/Fig6_259.jpg)
To depict viscoelastic behavior of polymers at various time intervals, the time–temperature superposition principle (TTSP) is mostly implemented. This principle determines temperature-dependent mechanical properties of viscoelastic materials at a reference temperature. Extending the operational temperature and escalating the load extent exert parallel outcome on viscoelastic materials' mechanical response: both decrease the storage space modulus and the complex modulus. This approach is usually found in practice at relaxation curves of the material. The master curve is attained by associating the relaxation curves at diverse temperatures through the adaptation of temperature superposition method which further classifies the perfunctory conduct of a substance at a certain temperature (Fig. 7).
![Fig. 7. Depiction of relaxation curves at various temperatures [55].](/sites/default/files/inline-images/Fig7_241.jpg)
The experimental methodologies which are often adopted for the analysis of viscoelastic properties are described in many international standards. For example, the [56] standard includes dynamic methods for determining polymer mechanical characteristics experimentally. The draught standard [57] is concerned with the determination of interlayer mechanical characteristics and offers a variety of approaches to address specific interlayer challenges.
[58] examined the tests methods utilized in available literature for the assessment of viscoelastic properties of interlayer materials. Through the adaptation of limited tests, the study found attaining the comparative results through experimental approach; despite the strengths and weaknesses of each method. According to the assessment, the tentative campaigns were likely determined by the availability of a range of equipments in research laboratories. Mechanical tests, on the other hand, can be divided into two categories: those that involve impressive loads or displacements, and those that involve dynamic transients. Tests that apply loads or displacements at a set pace allocates your approach of comparing diverse materials or spoiled specimens rapidly, while the dynamic or transitory tests, particularly creep and stress relaxation tests, are better for characterizing time-dependent behaviour. The behaviour of laminated glass after fracture and the functionality aspect of interlayer simultaneously are other significant factors to consider.
2.3. Ageing resistance and weathering
The phenomenon of “ageing” refers to any irreversible material or chemical process that causes alteration in material qualities and, as a result, a reduction in the material's application over time. The interlayer material's clearness, mechanical characteristics, and adherence to glass or added materials may get affected by degradation.
Weathering circumstances promote polymer early breakdown, which has a significant impact on its major properties [59,60]. As a result, the resistance of laminated glass qualities to weathering agents leads to be critical component in determining appropriateness for protection and safety proposes. UV radiation undoubtedly is prominent weathering agent for polymers, while it is frequently accompanied for effects with other means like temperature, humidity, and oxidation. To understand the functionality of each agent with regard to affecting polymers; accelerated testing is usually performed. Weathering agents are combined in a practical speeded up ageing procedure in climatic experimentations. The surface value of glass, stress sort and time-span, and temperature impacts are all included and analyzed in contemporary laminated glass systematic standards. In addition, international regulations are take into account like humidity, UV light, and temperature. However, this systematic procedure is only concerned with predicting the formation of flaws (delamination, bubbles, etc.) which are observed by visual assessment, not with predicting possible changes in the interlayer stuff characteristics.
As a result, various writers, including [40,44,49,61,62], set out to investigate the weathering outcome in polymeric resources, based on typically adopted ageing tests. Various ageing procedures might cause unusual modifications in material qualities, which is why it's critical to utilize standardized methodologies so that results can be compared.
3. Evaluation of laminated glass
3.1. Experimental approach
Laminated glass is a common form of glass that is used in building structural elements. Similar to building materials, LG plates are expected to have adequate stiffness and resistance to breakage so they can withstand the loads subjected to them. Different LG plates resting on four simple or bolted support at the corner in subjection to static and impulse load at the center of the plate were investigated by Ref. [63]. Supports condition is the main parameter for determining the ‘yield line’ pattern and the post-breakage behavior. An experimental study also illustrated that the initial stiffness of the cracked LG plate with the simple support is approximately four times that of the cracked LG plates with the bolted support.
[64] investigated a glass specimen with a dimension of 1600 x 1300 mm and two 4 mm thick glasses at the top and bottom with 0.76 mm thick PVB interlayer. Impulse load impact on the glass plates was investigated and their behavior has been captured by high-speed cameras. Different failure modes have been observed, however, three of them were most common namely, global flexure failure, mixed failure, and punching failure. Their study showed that ASTM design criteria overestimate the glass strength and revisions required in favor of safety.
3.2. FE modelling
In order to forecast spoilage in a laminate, practical calculations are used to determine the allocation of configurational stresses. These equations, however, are not handled directly when it comes to intricate structures and stress distributions. Finite-element modeling solves this challenge by approximating basic, intimately related forms instead of the intricate structure. In laminate structural creation, certain conceivable modifications, the most notable are layers associated with thickness and ingredients, can have a significant impact on ballistic executions.
Numerical modeling in combination with tests is shown having excessively efficient technique of evaluating the spoiled distinctiveness of laminated glasses [[65], [66], [67]]. Numerical modelling allows for a quick and inexpensive examination of a wide number of alternative armour formats. It aids in understanding the nature of laminate reactions impacting the failure procedures towards positive management. Numerical models facilitate the designs of ordinary and simple laminates and further adjust them to efficiently eliminate some incidental and interferential variables.
A numerical model was designed through the adoption of AUTODYN software for facilitating the response of glass designed for soda lime by further utilizing the Polycarbonate translucent laminates [68]. A short ballistic test program was carried out to sustain the development of numerical modeling by intimating substantial numerical reproduction. The Lagrange and SPH processors [69,70] are the best appropriate modeling aspects for the effect of glass lamination among AUTODYN's numerical processor approaches. DERA (Defense Evaluation and Research Agency) used this computational model to assess a large variety of alternative armor schemes and gain a better knowledge of how laminate mechanism interrelates in a ballistic impact situation. DERA is a long-term research project aimed at finding better insubstantial armor alternatives.
The bending inflexibility of both components with identical width and elasticity modulus was recorded similar to that of the PVB laminated varnishing. The term inflexibility is referred to behavior generally attributed to viscoelastic materials, such as interlayer elements, which measure their capability not to show loose behavior. The authors further asserted to replicate glass failure by wearing away shell parts, which allowed them to calculate the Young's modulus of the lasting shell constituent, which formulates the presentation of interlayer glass on windscreen. This change allows the replication of impactor shot speeding up on a windscreen along the aspect of compound effectiveness of glass laminate. In the instance of liberated linear vibrations [71], engaged with the predetermined constituent approach to compute the features of the glass's modal. The viscoelastic material and the composite Eigen value problem were adopted to support and sustain laminated beam at both edges. Problem Eq. (5) was explained with MATLAB software to acquire the natural frequencies (ω) and related loss factor (ƞ) using Eq. (6), where [K] and [M] respectively represented element rigidity and mass matrices, Ω is complex frequency, and {q} is nodal displacement vector. This research aids valuable output in designing supports of laminated beams to better sustain passive vibration control.
3.2.1. Simulations resembling experimental assessments
[72] tested glass plates subjected to the four-point bending test relying on continuous simple support at two sides. Four different series of plates with varying thickness and various interlayer material has been experimentally studied, and load-displacement curves were obtained. Yield lines and failure modes have been compared with FE built model. FE model results were in good agreement with the outcomes achieved from the experimental model. Results indicate that sentry glass and plates with PVB interlayer have better post-failure behavior and higher shape deformation compared to XLAB glass laminated specimens.
An experimental test and a numerical simulation by FE for vehicle windshield failure behavior have been carried out by Ref. [73]. A windshield is composed of a PVB interlayer at the center. LS-DYNA as FE software is used to predict the behavior of the windshield under 50-MPa impact stress. Two different mesh sizes of 5 and 10 mm have implemented during the numerical simulation. It has been observed that a 10-mm mesh size has unrealistic results with lower stiffness, while a 5-mm size was more realistic and in agreement with the experimental result.
3.2.2. Laminated glasses due to impact load
Numerical simulations to greater extent facilitate safety engineers. Accordingly, the information gathered from windows and windshield simulation help out the manufacturers and accident researchers to devise stratagem for inhabitant's protection [74,75]. A number of academics have done broader study on finite element modeling of laminated windows and facades mechanical behavior throughout impact loading in the past. Prior to failing of laminated glass plate, the speed and impact were tested through various speeds and laminate combinations. Improvements have been brought by using a finite element code to simulate glass plies, aluminum spheres, and PVB interlayers as linear elastic materials. The fracture commencement time and position are calculated using the strain energy discharge rate criterion (g) [76].
Where, γ represents the energy consumed in surface fracture and Ws stands for the demanded work for the creation of new surface, A stands for linear elastic material and is free of channel restriction and its value is determined as 7.8 J/m2. Through the adoption of global modeling; impact was calculated as 2D axisymmetric FEM consisting bilinear axisymmetric element CAX4R in quantity of four. The dynamic analysis was adopted using ABAQUS for running the global model where the gathered results were interpolated on margin line of sub model. The authors additionally looked at the influence of PVB thickness, glass ply thickness, and evaluated laminated and monolithic glass, discovering that the simulated impact generally leads into cracks.
The process of crack promulgation in windows under impact contact was examined by Ref. [77] using new breakthroughs in mathematical modelling. Reverse study of the crack outline may also be used to determine the impact momentum, which demonstrated good concurrence with real-world accidents. This study discovered the growth of radical cracks at first while circumferential cracks appearance at point of junction and around the system boundary of the fracture to relieve radial tension.
Researchers have used an experimentally validated FE model for laminated side glazing to examine mechanical tendency under the situation of impact loading. Various hybrid impacts with various rages of ultimate weights have been adopted as impact. Shell was made up of three distinct layers of laminated glass, each of which pursued the elastic brittle law and the elastoplastic law of the PVB interlayer (Fig. 8).
![Fig. 8. Different laminated glass FEM simulations [73,78].](/sites/default/files/inline-images/Fig8_208.jpg)
Three options for modeling the windows were explored in the earlier reference [79]. [73] published five windscreen finite element models. The analysis process covered two shell for the exterior or outer glasses while one PVB layer was analyzed in the overall three-layer model with each joint node or linked element connections. Accordingly, concerning the impact linear acceleration and rupture, the optimal model of 5 mm was discovered to be the double-layered model with associated links. Research experiments were carried out with standard and varying specifications on the impact load effects on laminated glass windows, facades and windshields under various loading conditions and the speed of impact. To report for the complex effectiveness of windows, Timmel's notion about smearing modelling methodology was used [78]. The tendency of the window panels is managed through the glass shell prior to fracture and by the PVB shell subsequent to fracture, the glass shell and connected parts being erased, parting only the density stress in the fragmented glass.
3.2.3. Laminated glasses subjected to blast loading
Considering the increasing danger of bomb detonations, gaseous blasts, windborne debris, earthquakes, and further intense loading circumstances, structural study and design for laminated glass is becoming increasingly critical [80]. evaluated blast loading and consequences and summarized different computer codes, such as ABAQUS AUTODYN, DYNA3D, and LSDYNA, that can reproduce blast effects on structures and stand for structural movement while calculations are being performed. The researchers have employed FEM investigation comprehensively to anticipate the collapse of laminated architectural glass when situated under certain blast pressure [81]. adopted a 3D nonlinear finite element mold to envisage laminated glass failure and explain the collective damage likelihood of inner glass panes of architectural glazing when a grounded explosion of bomb occurred. Although the shock wave's pressure is comprised of both the positive and negative pressure phases; structural damage was considered and emphasized greatly by the authors to conclude on positive phase through an experimental quasi exponential structure.
Where p(t) refers to the immediate free air overpressure at time t, p0 stands for the climax overpressure at time t = 0, td is the interval of positive pressure, and α is the shape parameter [82]. tabular values of these factors were adjusted to the equation for proficient numerical modeling. The vibrant problem was coped with by means of a dynamic nonlinear 3D FEM, LS DYNA, using fundamental leading equations offered by Ref. [83]. For the laminated glass, stresses were estimated through the adoption of, method of finite element with 8 node solid elements via the subsequent equation:
Where,
The further utilization of the model characterized the stress allocations in laminated architectural glazing and the effects of blast loading outlines and PVB interlayer viscoelastic factors on dynamic reaction [11]. To model the glass, ten 3D 8 node solid components were engaged for a pane of four glasses while PVB application was done through two panes with 4040 meshes in the x-y plane. The utmost primary stress and innermost deflection predicted while using static solutions in good accord with previous studies. The suggested model correctly envisaged the glass's dynamic reaction, and no effects of PVB bulk modulus in levels 0.3–200 GPa were detected. The researchers however concluded that small time shear modulus has a considerable impact on dynamic responsiveness. The usefulness of calculating endeavors in numerical modeling of multifaceted laminated glass tendency was enhanced in this study.
Conditionally, if the positive stage concerning blast load is insufficiently cruel for failure, the breakage of laminated glass can also occur through the negative phase. Von Karman big deflection equation was used to construct a failure condition for predicting glass failure. The results were confirmed using a three-dimensional finite element model that treated PVB as both viscoelastic and elastic. A rectangle laminated panel was found more resistant to blast in comparison to that square panel. The influence of glass panel thickness for both PVB and interlayer was studied with researchers recommending the excessive thickness of inner glass ply with arrange varying from 0.76 to 1.52 mm for PVB for cost-effective and reliable blast resistance.
[84]; evaluated 2D shell element and 3D solid element models for studying laminated glass panels subjected to blast stresses and discovered that both models can accurately predict experimental results [85]. published a new finite element model in the ABAQUS finite element software package for estimating blast opposition of laminated glasses the further confirmation was done through laboratory experiments. To speed up the dynamic reaction of laminated glass with blast loadings [19], ran mathematical simulations and built pressure-impulse diagrams. Solid continuum elements with mesh sizes of 5mm5mm3mm for glass and 5mm5mm1.52 mm for interlayer were used in the FE model produced in LS-DYNA.
The greatest deflection in numerical replication for tough impulse was recorded 13.884 mm, which was extremely close to the investigational value of 14.583 mm, although there were minor deviations for weak impulse values. The failure criteria based on interlayer breakage were utilized to create unified P-I diagrams of laminated glass with bending and shear failure modes. The equation gives the P-I diagrams of laminated glasses:
Where.
P0 and I0 are respectively studied as pressure and impulse asymptote. Because A was read as unaffected by changes in PVB thickness, they were used as invariable to diminish the numeral of parameters (2.4 and 1.2 correspondingly). The influence of certain factors like interlayer and glass thickness, window proportions, periphery conditions, and glass strength on P-I diagrams has been premeditated, and the mathematical consequences are adopted to establish an experiential formula for P-I diagrams, which is given by the Eqs. (11), (12), respectively:
Where,
4. Conclusion
The conducted review reveals that PVB is the most extensively employed interlayer material, however, its incorporation does not suit every intended use of the laminated glass. PVB offers better glass adhesion and transparency, however, it is outperformed by Ionoplast through its multilayer adhesion capacity and resistance against high temperatures. Hence, Ionoplast is revealed as expensive but safer, durable and of high utility in comparison to PVB. However, recent works indicate that advanced versions of PVB offers higher transparency, strength, stiffness and sound proofing in comparison to the conventional PVB. Likewise, effective and productive estimation of the laminated glass failure scenarios have been conducted through FE modelling. The numerical revelations obtained impart better design capacities against specific failure and impairment physiognomies. Various approaches and models have been implemented for the effective characterization and numerical estimation of the impact.
The accuracy and reach of the FE models have advanced with the passage of time and covers 3D and quadrilateral high accuracy models encompassing crack initiation and propagation analysis. Extensive work has been conducted on the negative and positive phases of the laminated glass failures under the blast loading recognizing layered model is the most effective model. The impact of blast loading has been analyzed through pressure-impulse diagrams and dynamic response. The impact of different thicknesses and dimensions on the strength parameters of laminated glass has been analyzed under various scenarios. The numerical FE models are revealed to be more accurate, productive and effective models for consistent forecasts of pressure-impulse diagrams under a range of blast loading scenarios. The enhancement of both crack and breakage resistance and the post-breakage safety are of utmost prominence with regards to the sustainable performance optimization of laminated glass.
Declaration of competing interest
The authors declare that they have no known competing financial interests or personal relationships that could have appeared to influence the work reported in this paper.
Acknowledgement
The authors are grateful for the financial support of LPA Science Inc., a technology business Co. for supplying the outfits of performing successful research around the glass structures. The project was carried out in the facilities provided by the same incubator at the University of Tabriz.