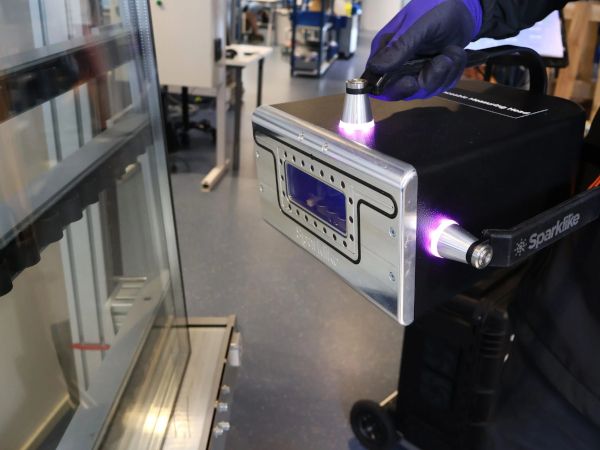
Date: 8 July 2025
The Sparklike Laser devices measure the insulating gas concentration in Insulating Glass Units (IGUs). Its non-invasive technology ensures accuracy while preserving the integrity of the units. In this blog, we will provide an overview of the critical steps for effective Sparklike Laser usage, based on the official user guide, and highlight tips to achieve accurate measurements every time.
Download Guide for Sparklike Laser Users
Understanding the Science Behind Sparklike Laser
The Sparklike Laser operates on a technology called Tunable Diode Laser Spectroscopy (TDLAS). By emitting near-infrared light at a wavelength of 760 nm, it detects the oxygen content in IGUs, which is then converted to the insulating gas concentration. This wavelength is chosen for its specificity to oxygen molecules, ensuring precise readings.
The Importance of Preparation
Before starting measurements, consider these preparatory steps:
- Identify Coatings: Coated glass panes can reflect the laser beam and distort results. Always identify coating types and locations using visual inspections or coating detectors.
- Clean Surfaces: Ensure the measuring head and the glass surface are clean and free of debris or scratches, which can scatter light.
- Secure Attachment: Attach the measuring head tightly to avoid air leakage or misalignment, which can introduce errors.
Step-by-Step Measurement Procedure
- Determine the Type of IGU: Identify whether the unit is double or triple glazed, as the measurement approach varies.
- Positioning: Select the preferred side for measurement. If the unit has coatings, measure from the uncoated side whenever possible.
- Use Preset Modes: For laminated or toughened glass, utilize the device’s preset modes to account for thickness variations.
- Repeat Measurements: Conduct at least two measurements per IGU to ensure accuracy and identify anomalies.
Test Laser Compatibility tool to see how to test your IGU configuration
Best Practices for Accurate Results
- Regular Calibration: Annually calibrate the device to maintain precision.
- Minimize Measuring Through Coatings: Coatings with low transmission at 760 nm can reflect the laser beam, so avoid measuring through these layers if possible.
- Controlled Environment: Perform measurements in environments with stable temperature and humidity levels to reduce variability.
- Documentation: Record measurements in a standardized template to monitor trends and ensure traceability.
Common Challenges and Solutions
- Dirty or Scratched Measuring Head: Regularly clean and inspect the device to maintain optimal performance.
- Low Transmission Glass: For glass panes with transmission below 35%, consider alternative sides or repeat measurements to improve reliability.
- Operator Errors: Provide thorough training to ensure consistent handling and understanding of the device.
Why Repeated Measurements Matter
In quality assurance, repeated measurements help reduce errors and provide confidence in the results. This practice is essential for:
- Ensuring production processes meet specified tolerances.
- Supporting informed decision-making in production adjustments.
- Meeting customer expectations by delivering high-quality IGUs.
Validation and Documentation
Proper documentation is the cornerstone of reliable measurement results. Use standardized templates to:
- Track measurement trends over time.
- Validate the preferred measurement side for consistency.
- Support quality control initiatives.
Conclusion
The Sparklike Laser devices are a powerful tool for ensuring the quality of IGUs, but its effectiveness also relies on proper usage. By following these guidelines, users can achieve accurate, consistent results that support manufacturing excellence and customer satisfaction.
For further information, consult the Sparklike Laser User Guide or contact our support team for assistance.
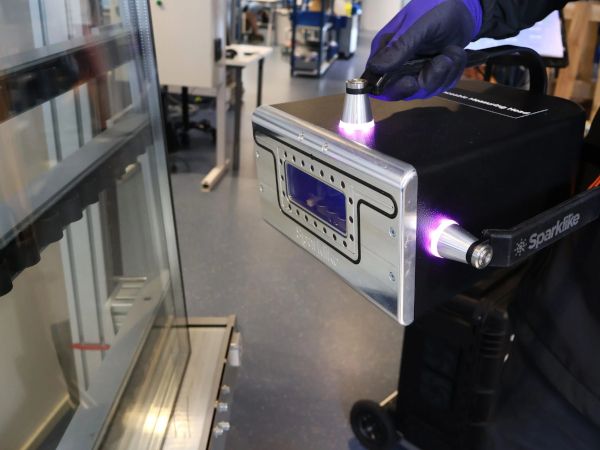

Add new comment