Motivation
Curved building envelopes are highly coveted by architects and their clients who are striving for demanding esthetics of their constructions as a mutually satisfactory result. Particularly with regard to not only curved - but also large-sized glass panes - the complexity in the manufacture and design process is challenging [1]. In addition, no standardization of curved glass has been achieved yet in Europe [2] [3]. Hence, these architectural demands and challenges are a stimulating factor for the research on curved glass and related product development.
Cold-bent glass
Cold-bent glass is obtained by imposing a deformation on a flat glass (either monolithic glass or laminated safety glass) or an IG by fixing the flat glass permanently to a curved substructure. Cold-bent glass is experiencing permanent internal stresses therefore pre-stressed glass must be used instead of float glass. Limitations of cold-bent glass are particularly given through the bending strength, geometric conditions, and - regarding laminated glass - the partial shear rate of the intermediate layers [4]. Cold-bent glass is superior to warm-bent glass for applications in building construction because it gives better optical quality at a lower cost, unlike hot-bent glass where local warping can occur [5]. Surface coating, pre-stressing, and other processing steps can be carried out in the plane configuration which is very like for float glass therefore no further expenses need to be considered [6].
Cold-lamination bending of glass
Cold-lamination bending is convenient for pre-stressed thin glass with big bending radii [7]. Cold-lamination bent glass is made from flat glass which has to be pre-stressed like cold-bent glass and gives a curved laminated safety glass as a final product. After stacking the single float glass panes and the interlayer on top of each other, they get cold-bent on an auxiliary scaffold under autoclave conditions. It is important to understand the difference between cold-lamination bending and cold-bending of glass. This article focuses on cold-bent insulating glass units only.
Cold bending of a single-bent IGU
The numerical investigation [8] was carried out in the software Abaqus. The reference model of a single-bent IGU (insulated glass unit), as well as all other models, are bent displacement controlled onto an underlying sub-construction.
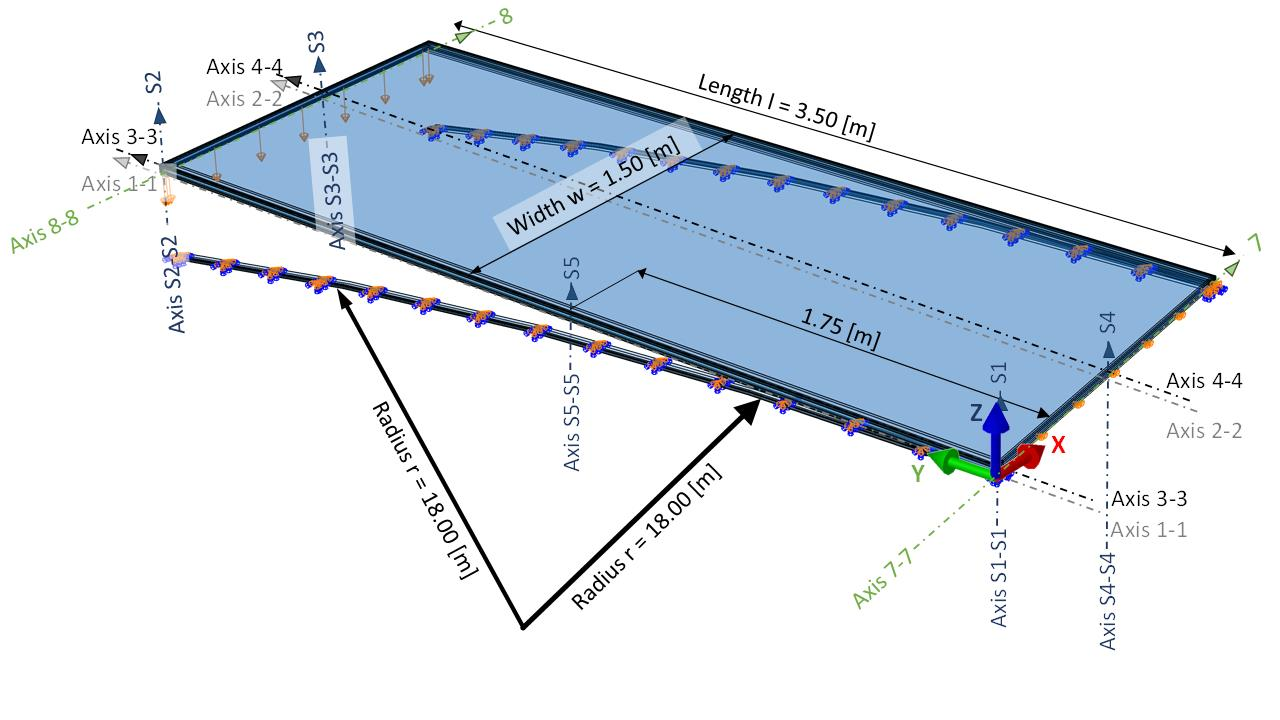
The FE (finite element) model consists of several parts, which are two longitudinal spacers parallel to the y-axis, two spacers along the width parallel to the x-axis, a circumferential secondary seal, two glass panes, and two rectangular-shaped steel arcs for the sub-construction.
In order to choose the best numerical interaction property, it is vital to understand the interplay between the different parts of the IGU model. Because structural silicone sticks to the glass and to the spacer like an adhesive, it is reasonable to "tie" the finite element surfaces of the adjacent parts together. The mechanical contribution of the primary seal is nearly zero but its shear distortion becomes rather huge. This leads to serious numerical instabilities in the model and hence a slip-free interaction represents the butyl strip.
Therefore, the spacers in the model are interacting with the underlying and overlying glass panes. In order to represent the interaction spacer – primary seal – glass pane, the spacers, and the glass panes are allocated to a surface to surface interaction with a frictionless and hard contact, whereby the glass is the master because the spacer is deformed easier due to its thin sheet thickness.
Because the sub-construction is embedded rigidly, in order to avoid result interpretation difficulties, it is the master for glass pane 1. A frictionless and hard contact seemed to be sensible because the results compared to a soft contact were the same. Furthermore, the friction between steel and glass, in this case, is negligible. It is assumed that the cavity is filled up fully with the noble gas argon which was modeled with pneumatic elements.

Required bending force
The required force 𝐹 for the cold-bending process is shown as a function of the enforced displacement. It takes just 100 [𝑁] to bent the IGU 0.15 [𝑚], for the next 0.15 [𝑚] it takes another 200 [𝑁]. The total required force to bent it 0.3 [𝑚] is 300 [𝑁]. For the last few centimeters, it takes over 1100 [𝑁] which means that almost 80% of the total force is required for the last 12% of enforced displacement. The reason for this is that most of the contact between the sub-construction and the IGU is realized mainly in the last centimeters.
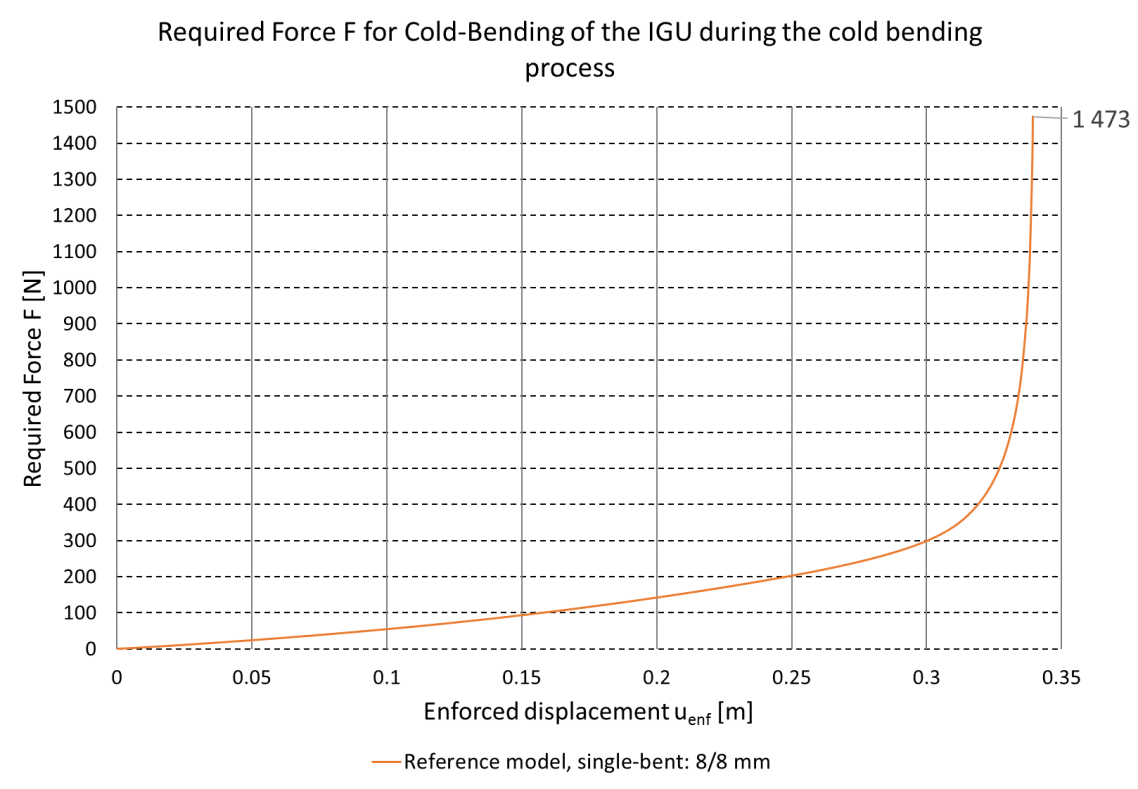
Results of the single-bent IGU
A parameter study about the influence of the thickness of the glass pane on the overall IGU system is carried out. The following glass thicknesses are considered: 6 [𝑚𝑚], 8 [𝑚𝑚] and 10 [𝑚𝑚]. Because the IGU is double-glazed, there are 9 possibilities to combine the glass pane thicknesses. As it can be seen from the depiction below, the maximum glass pane thickness determines the maximum principal stresses in both glass panes. Recalling Barlow's formula, and comparing the maximum principal stress with the analytical Barlow equation, the valuescan be up to 40% higher in reality and shall therefore not be used to predict stresses.
Special attention should be given to the secondary seal's shear deformation in the case of cold-bent IGUs. This can be solved with high performing silicones, however elaborate approval procedures shall ensure the airtightness of the cavity. In the depiction below, the shear deformation of the secondary seal of an IGU with different lengths is compared. All other parameters are as desribed in the reference model above. The shear displacement of the secondary seal increases as the IGU gets longer. For an IGU with the dimensions of 1.5x3.5 meters, the shear displacement is 12.5% which is pushing the boundary of what is feasible with today's silicones.
Aluminum spacers are preferred over stainless steel spacers for IGUs. A variation of the spacer materials shows, that the stainless steel spacer is more suitable than the aluminum spacer because of it's higher ductility. Besides the high material utilization, a further problem shows up when looking at the local deformation of the spacer in the x-direction, which is also illustrated in the figure below.
Conclusions
In general, single-bent IGUs are not sensitive to different boundary conditions (BCs) and do not undergo local stability problems. Spacers which are made out of stainless steel show to be suitable because of the high ductility of the material. During the cold bending process, an onset of yielding can be observed in the corner region of the spacers. The plasticizing in the corners stay locally limited if the deformation is increased further. At a certain deformation value, the plasticizing area starts to expand.
Therefore, the spacers limit the feasible deformation of IGUs. Aluminum spacers are not ductile enough because they are reaching their ultimate strength in the corner region already for small deformations. In the corner region, high strains and pressures must be endured by the spacers and the secondary seal. This can also lead to local buckling of aluminum spacers. Outside the corner region, the spacers' stress is - as a general rule - below half of the yield stress. Because the spacer reaches first a crucial stress level, it limits the possible deformation.
Based on the limitation of metallic spacers, the critical values in the glass panes stay below the material resistance. Low material utilization is indispensable in order to bear variable loads during the service life. However, if it is necessary to reduce the stress in the glass for a given deformation, then the pane thickness has to be reduced. The primary seal has no mechanical contribution to the IGU and hence is neglected in numerical simulations. The circumferential secondary seal, which is made out of structural silicone, ensures airtightness of the IGU.
Structural silicones are able to withstand high deformations
which makes them a suitable material for cold bending. The shear displacement of the secondary seal usually exceeds 10% before the maximum feasible deformation due to yielding of the spacer is reached. For the single-bent model with a length of 3.50 [𝑚] and a width of 1.50 [𝑚], the shear deformation can be as high as 17% if both glass panes have a thickness of 10 [𝑚𝑚]. A stiffer silicone can reduce the strain outside the corner regions but is not able to reduce the shear displacement to an appreciable level.
References
[1] J. Salo, „Modern safety glazing - demand, challenge and opportunity,“ Tamglass Singapore Pte. Ltd., Singapore, 2005
[2] Steffen Schäfer, Michael Elstner, „Starke Kurven,“ Deutsches Architektenblatt, 31 8 2010.
[3] Eva Scheideler, Markus Broich, Michael Elstner, „Anwendung von thermisch gebogenem Glas im Bauwesen,“ Ernst & Sohn, Berlin, 2012
[4] Ömer Bucak, Markus Feldmann, Ruth Kasper, Martin Bues, Marcus Illguth, „Das Bauprodukt "warm gebogenes Glas" - Prüfverfahren, Festigkeiten und Qualitätssicherung,“ Stahlbau Spezial, Bd. Konstruktiver Glasbau, pp. 23-28, 2009.
[5] Stefan Peters, Stephan Engelsmann, Christoph Dengler, „seele Glasbrücke: Eine gläserne Brückenkonstruktion aus kaltverformten Glas,“ Bautechnik, Bd. 91, Nr. 12, 2014.
[6] Tihemo Fildhuth, Jan Knippers, „Geometrie und Tragverhalten von doppelt gekrümmten Ganzglasschalen aus kalt verformten Glaslaminaten,“ Stahlbau Spezial, pp. 31-44, 2011.
[7] Christian Schuler, Michael Elstner, Marcus Illguth, Sonja Stief, Alexander Lorenz, „Einsatz von gebogenem Glas im Bauwesen,“ Stahlbau, Bd. 81, Nr. 3, pp. 190-196, 2012.
[8] Franz Nikolaus Pölzl, "Mechanical Behavior of Cold-Bent Insulating Glass Units", Technical University of Graz, 2016