First presented at GPD 2017
The technology creates a very stable and uniform ceramic surface. This new process opens up opportunities to provide high performance coated glass for a number of different applications such as structural glazing, all-glass corners, glass roofs or louvre windows.
The process involves the enamel being applied directly onto the coating. During subsequent heating, the enamel dissolves the sputter coating and fuses with the glass to create a very strong bond – comparable to standard enamel on float glass. After cooling, the coating is fully embedded in the enamel.
Introduction
The introduction of heat-treatable thermal insulating and solar control coated glass was a big step towards the improvement of customer service and flexibility in the realization of architectural glass projects. This led not only to new possibilities for the provision of tempered and heat-strengthened glass, but also to the possibility to bend coated glass and, depending on the type of coating, even to print on glass with suitable ceramic paints.
Printing took place either over the entire surface in order to manufacture reflecting spandrel glass, or at the edge of the glass panes in order to conceal structural elements or to create suitable surfaces for structural bonding.
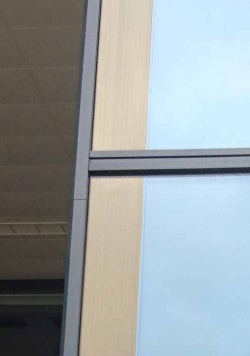
However, the available ceramic paints are compatible only with a few types of coating. In addition to that a change of colour, in some cases clearly noticeable, is seen in particular with very transparent or silver-containing coatings; see fig. 1.
On the other hand, new generations of coated glass (e.g. the so-called double and triple silver coatings) are not usually compatible with ceramic paints. The consequence of this is that many applications can be realized only with a great deal of effort using conventional processing methods. These applications include:
- structural bonding
- all-glass corners
- overhanging roof glazings
- glass louvre windows
- turn and tilt windows in all-glass facades.
The usual cut-to-size tempered and heatstrengthened glass necessary for this often also have to be elaborately coated, which is usually connected with long and unpredictable delivery times, quality risks and not least, high logistics expenditure.
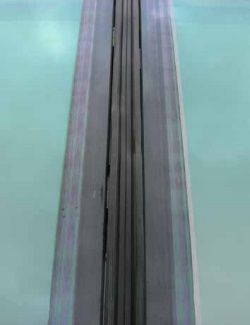
The removal of the coating at the edges of the glass by conventional grinding, either automatically directly on the cutting table or manually with the appropriate equipment, also usually leads to unsatisfactory results with regard to aesthetics and surface quality; see fig. 2. The amount of work necessary to remove the coating from large areas also incurs costs that are frequently significant.
New processing technology
The “System TEA” technology (TEA = True Edge Application), developed in collaboration with Ferro, a leading manufacturer of ceramic paints for architecture, allows direct printing on coatings, including those of the latest generation. This method makes use of a completely new type of material-dissolving ceramic paint (enamel), which was conceived for use in combination with heat-treatable sputter coatings.
During the firing process the coating is completely dissolved in the enamel. The System TEA enamel fuses with the glass and adheres very strongly – comparable to conventional ceramic paint on glass. After cooling, all constituents of the coating are chemically passivated, similar to colour pigments, and completely embedded in the enameling.
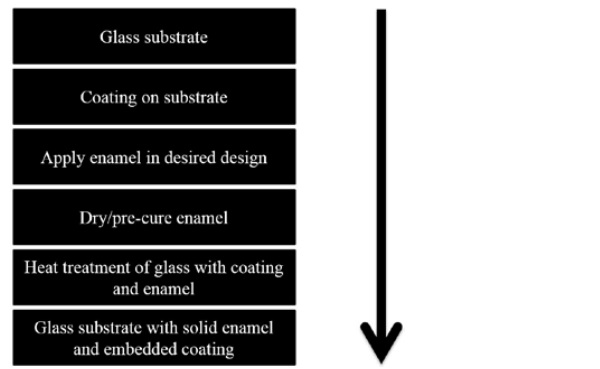
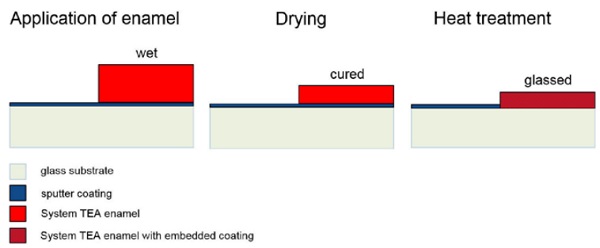
Due to the efficiency of the process, the number of processing steps is considerably reduced. The complete dissolving of the coating constituents by the ceramic paint makes it unnecessary to grind off the coating before enameling. This allows the omission of the work step that is most critical for the final product and which is frequently responsible for an inacceptable appearance and an inhomogeneous surface. At the same time, the technical risk for intended structural bonding is lowered.
Application of the glass enamel and firing
A decisive criterion for the application of the paint is the most homogeneous enameling possible. The wet film thickness (measured directly after printing) should be at least 44 µm (see also System TEA data sheet from Ferro) in order to ensure the complete dissolving of the coating material. The wet film thickness should be checked my means of suitable measurements.
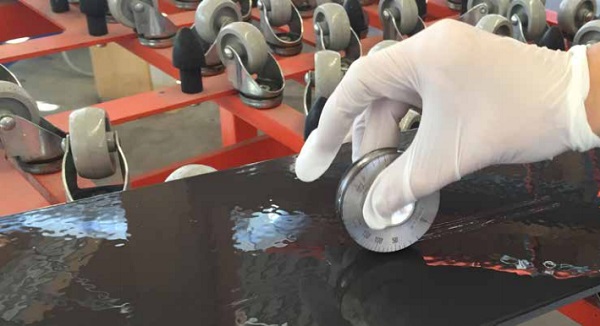
The coated surface can be printed on using various methods. The best results are achieved with the so-called roller coating technique. Wet film thicknesses > 70 µm are easily achievable here and the homogeneity of the enameling is typically very good. Another option is ceramic screen printing. Here the minimum wet film thickness must be ensured through the selection of an appropriate screen. Manual paint application using a hand roller is possible, but not recommended, since the uniformity of the enameling is very difficult to maintain.
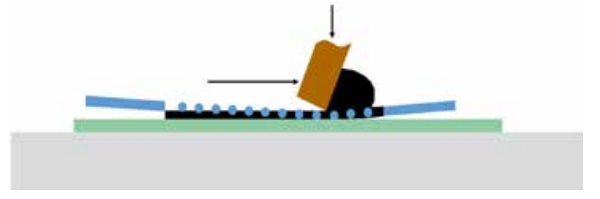
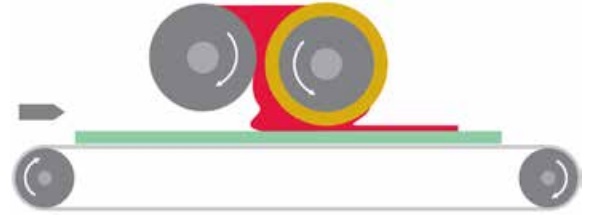
The subsequent drying process is equally decisive for an optimum result. Infrared or convection dryers are recommended for this. The glass temperature should be > 130 °C. It is important that the paint dries homogeneously and completely. The paint is fired during the normal heat treatment of the glass to make tempered or heat-strengthened glass.
On account of the differing degrees of reflection for long-wave thermal radiation exhibited by the ceramic printed surface and the lowemission coating, the glass may warp during heating in the furnace and in the cooling area due to lateral temperature differences. These deformations depend on the width of the printed surface and the number of printed edges. A circumferential edge print in particular can lead to strong “bulging” of the glass in the furnace. The furnace parameters must therefore be adapted accordingly.
![Fig. 8: SEM photo of glass with a SunGuard SNX triple-silver-coating and System TEA [2]](/sites/default/files/inline-images/Fig8_33.jpg)
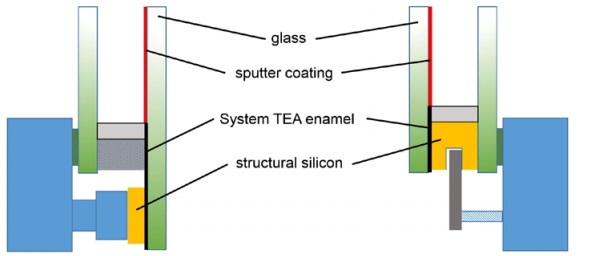
Tests and analyses
Various tests were carried out on the end product. The aim was, firstly, to prove the coating-dissolving properties of the ceramic paint and, secondly, to test the properties of the enameled surface with respect to its suitability for the corresponding applications.
Proof of the coating-dissolving properties
In order to prove the coating-dissolving properties, samples were analytically examined by means of SEM (Scanning Electron Microscopy) / EDX (Energy-Dispersive X-ray spectroscopy) or WDX (Wavelength-Dispersive X-ray spectroscopy). In the process, all materials and material combinations used in the Guardian coatings had to be accounted for. Therefore, different coatings were printed on and analyzed accordingly. The aim was to prove the complete removal of the coating constituents at the interface.
In other words, the composition of the glass/enamel interface remains independent of the dissolved coating. In fact, relevant coating constituents such as silver (Ag) or dielectric coating elements could no longer be found at the interface using the methods described above. That applies both to the coated surface and to the cross section through to the glass surface. Amongst others, the coating SunGuard SNX 50/23-HT, consisting of a series of over 20 individual layers, was examined as an example.
From the analyses, the conclusion can be drawn that no change is detectable in the composition of the enamel paint in the System TEA due to the dissolved coating constituents. That applies both to the surface of the printed areas and to the profile cross-section. All elements of the various coatings were fully dissolved. The SEM photo in fig. 8 shows a typical interface between glass and System TEA enamel. The EDX analyses prove that there is a sliding transition of the Si concentration between the float glass and the enamel, which indicates good fusion. [2]
Adhesive behavior of structural silicone
An important reason for the development of the System TEA technology was the problem of undefined surfaces following the mechanical grinding off of sputter coatings. This can lead to unforeseen risks, especially for structurally bonded surfaces. Therefore, the following silicones were tested for structural bonding to the System TEA surface according to ETAG 002-1:
- Dow Corning DC 993 (passed)
- Dow Corning DC 3363 (passed)
- Sika SG 500 (passed)
- Sika IG-25 HM+ (test is still running)
The test specimens according to ETAG 002-1 were stored under changing temperatures and subjected to tension until failure. Moreover, the residual strength was tested after storage in water at a high temperature and UV exposure, after storage in moisture and NaCl environment, after storage in moisture and SO2 environment and after storage in a cleaning agent solution. The requirements were met in each case.
In addition, the System TEA was adopted into the General Type Approval (AbZ) issued by the DIBt (Germany building authority) for the use of Dow Corning DC 993 in combination with tempered, tempered heat-soaked and heat-strengthened glass in structural facade applications. The sputter coatings covered by the General Type Approval AbZ (Z-70.1-75) are listed there in the appendix. In order to obtain the data for a suitable production control within the scope of the General Type Approval, the following properties of the ceramic-printed surfaces were also determined:
- Scratch hardness (ISO 1518): no scratches detectable with adhesion test rod at ≤ 16 N pressure
- Porosity (ASTM C 1048-92): no penetration with isopropanol
- Degree of glass (DIN 67530): measured 126,7 (required: min. 110 at 60° angle) [3]
Proof of the properties of tempered heat-soaked glass
The objective was to prove that tempered, heat-soaked glass printed with glass enamel of the type System TEA with correspondingly dissolved sputter coatings conforms to the standard DIN EN 14179-1. The types of coated glass selected as examples were the SunGuard HD Neutral 67, a relatively simple solar protection glass, and the SunGuard SNX 50/23 HT, which is equipped with an extremely complex coating. Panes of glass in the thicknesses 6 and 8 mm were tested in each case.
All panes tested met the requirements of the standard.
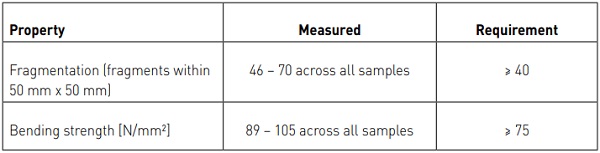
Summary and outlook
Today, glass enamel printing is used more and more frequently wherever structural elements have to be concealed, for example in the case of all-glass corners or louvre windows. The “System TEA” opens up opportunities for the use of edge-enameled, coated architectural glass. Using this new technology, visually homogeneous glass enamel surfaces can be created that are both mechanically and chemically stable.
The surfaces of the System TEA always offer reliable and tested adhesive characteristics for the structural bonding of facade elements. At the same time an attractive, visually uniform outside appearance is achieved. The new method reduces the expenditure for production and logistics.
On one hand it is possible to eliminate the laborious grinding off of the coating, which is often associated with poor quality while on the other hand heat-treatable coatings can be used instead of a logistically elaborate coating onto cut-to-size heat treated glass. All in all, it can be expected that the use of this technology will make a very big contribution to the improvement of the quality of enameled architectural glass in the future.
It is planned in the future to supplement the currently available colour black grey shades, amongst others. These would be used especially with grey structural sealants.
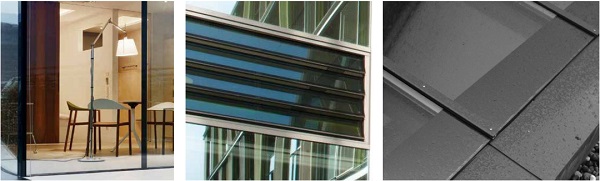
Literature
[1] Internat. Patent Application, Int. Publication Number: WO 2014/133929 A2 (24.02.2014) Title: “Window units made using ceramic frit that dissolves physical vapor deposition (PVD) deposited coatings, and/or associated methods”
[2] Bahn, M.: Charakterisierung von Guardian Magnetronbeschichtungen bei Emaillierung mit einem neuartigen schichtauflösenden Email (CFDPC)“, Bachelorarbeit, Köthen, May 2014
[3] Ferro, Technical datasheet GSGF TEA Black 14 4400AL