This paper was first presented at GPD 2023.
Link to the full GPD 2023 conference book: https://www.gpd.fi/GPD2023_proceedings_book/
Authors: Vicente Montes-Amoros, CDC, Inc.
Abstract
It is a widely studied topic and well known in the industry that tempered glass can be subjected to spontaneous glass breakage caused by Nickel Sulfide (NiS) inclusions. It is also known that safety glass is required by code at certain locations and applications and that tempered glass is widely used to fulfill this safety requirement. Certain projects and/ or conditions do not allow the use of laminated glass, and tempered glass has to be utilized. Heat soaking glass is an additional step in the glass making process that has been utilized for years in order to minimize the potential for spontaneous glass breakage caused by NiS inclusions on installed glass. But what are some of the implications? What is the risk? Is there a risk?
The economic impact for heat soaking glass cannot be afforded on certain projects and a (reduced) risk would remain for NiS spontaneous breakages even after heat soaking. Therefore, what is the risk/benefit for heat soaking glass? What are the glass characteristics after heat soaking glass? What is the remaining risk after heat soaking glass? This paper explores the requirements of the US versus European markets and provides examples of projects where heat-soaked glass has been utilized and the data gathered thus far regarding the effectiveness of this measure.
Introduction
First of all, one must know that the US currently has no standard for heat soaking and the European Standard has been widely specified when heat-soaked glass is required. When specifying this European standard in the US, the question arises weather the specified standard is meant only for the process or the entire standard. One could argue that if specified, it should be the whole document. However, when issues start occurring on installed projects, this question could become a litigious fight.
The audience reading this paper or attending this presentation understand the reason why heat-soaked tested glass is specified. Therefore, the scope of this paper is not to cover any of those topics. We are going to cover instances where heat-soaked glass has become a discussion topic on different projects. These instances deal with requirements set forth in the International Building Code.
The International Building Code, which has been adopted statewide by the majority of the United States with the exception of Arizona, Colorado, Delaware, Kansas and Nevada; provides information regarding areas and conditions that are classified as hazardous locations which require the use of safety glass. Section 2406.3 from 2015 IBC (this paper utilizes references from the 2015 IBC version), lists four criterion that need to be met for glazing in windows to be considered a hazardous location:
- Exposed area is greater than 9 square feet.
- Bottom edge of glass is less than 18 inches above the floor
- Top edge of glass is greater than 36 inches above the floor
- One or more walking surface(s) are within 36 inches, measured horizontally and in a straight line, of the plane of the glazing.
Additional conditions and areas that are classified as hazardous locations per IBC are: glazing in doors, glazing adjacent to doors, glazing in guards and railings, glazing at/ around wet surfaces applications such as hot tubs, glazing adjacent to stairways and ramps, and glazing adjacent to the bottom stairway landing (Montes-Amoros, 2019).
If the Building Code in the US requires safety glass, it means that tempered glass or laminated glass could be utilized to meet this requirement. We know that the potential for glass breakage due to NiS exists if tempered glass is utilized. We also know that heat soaking would reduce this potential, but it would not completely eliminate it.
If the risk is not completely mitigated, what is the remaining risk? What is the probability of breakage after heat soaking? Is there a premium associated with this test? Can all projects afford the premium (if any)? Is it possible to verify if heat soak testing was carried out? Should projects heat soak tempered glass?
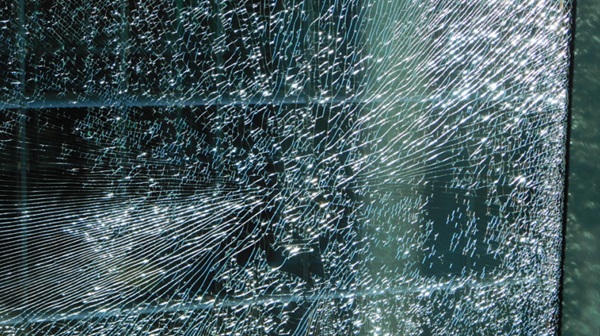
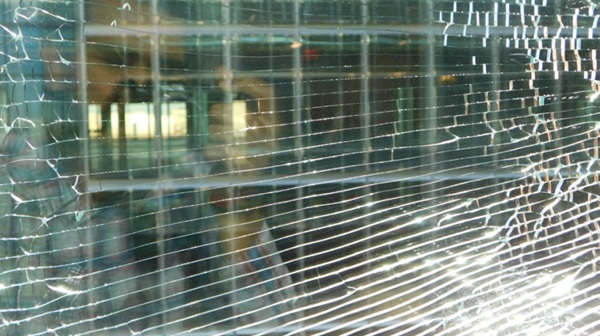
Background
Several papers and research studies have been conducted trying to answer the questions above. Unfortunately, glass has continued to break causing personal and material damages. Sometimes it is because heat soaking has been excluded from the projects due to cost. Several projects in the US have experienced an alarming number of breakages even when glass has been heat soaked, which begs the question of whether it was really heat soaked or not.
Without going into detail of the history of how the first heat soak test was carried out in the 1970’s and then how the European standard was created in the 1990’s, we can say that embedded in the European Standard, EN 14179, glass can have one NiS inclusion in 4 metric tons (CWCT, 2008). Some other researchers have stated that the number is one inclusion in 6.2 metric tons. For the purposes of this paper, we are going to use the more conservative value of one in 4 metric tons. Furthermore, EN 14179 states that the process of heat soaking reduces the risk of an active NiS particle to one in 400 metric tons. Other researchers have stated that the number is closer to 1 in 6,000 metric tons based on their historical results (Kasper, 2019). But again, for purpose of this paper, we are going to use the EN 14179 value.
Depending on the glass manufacturer, the cost associated with heat soaking of the glass varies. It is dependent on factors such as glass size and in some cases if a certain threshold of breakages is exceeded during the test, an additional premium or cost could be charged. Therefore, it is recommended that all of these factors get specified ahead of embarking on this task.
Breakage patterns and crack propagation has been studied and proven by many researchers. It has been demonstrated that the greater the magnitude of the compressive and tensile zones in the glass, the higher the strength and, the smaller and more numerous the fragments of glass in the fracture. (Kocer, 2015). Hence, at a greater strength capacity with a surface compression of not less than 10,000 psi (69 MPa) per ASTM C1048, tempered glass provides a breakage pattern that meets safety standards. In annealed and heat-strengthened glass, the residual stress profile is respectively one quarter and one half less than tempered glass. Hence, the available strain energy for crack propagation is less and their breakage pattern exhibits larger shards.
Project examples
In the US, the European Standard for Heat Soak Testing EN 14179 has been specified and utilized for several years now. But, in some cases, developers and building owners have opposed this recommendation due to the added cost.
To make matters worse, “Developer A” opted to accept heat soaking of all tempered glass on Project Alpha to later find out that glass was breaking at alarming rates. Studies were conducted and the evidence of NiS was only found in less than 12% of Project Alpha’s specimens. The rest of the breakages were either found to be caused by impact or the specimen could not be captured for laboratory testing. Developer A decided to not heat soak their glass on their next project since it made no difference on Project Alpha.
The glass in Project Alpha was procured from outside the US and when the glass manufacturer was questioned, they did produce data showing that heat soak testing was carried out. However, with the information provided there was no straightforward correlation between the glass sheets that went into the heat-soaking oven vs. the sheets that were utilized for the project’s IGU’s. There was no other information provided for heat-soaking verification.
Following the figures presented in the previous section regarding the probability of NiS inclusions in glass, Project Alpha had nearly 1.5 million pounds (641 metric tons) of tempered glass. This equates to 160 potential inclusions or nearly 2 inclusions if the glass had actually been heat soaked. Laboratory testing on this project found 3 confirmed cases of NiS inclusions which exceeds the anticipated number of potential inclusions.
Developer Beta decided to heat soak their triple glazed project, Project Beta, and a very high number of glass breakages occurred within five years of substantial completion. With nearly 1.5 million pounds (638 metric tons) of heat-soaked tempered glass, not more than 2 inclusions should have been expected. However, laboratory testing confirmed NiS on more than 2 specimens. When requested, no records were produced to be able to corroborate heat soak testing by the glass manufacturer.
Developer Gamma chose not to heat soak all tempered glass in their 38 floors tall project, Project Gamma. The IGU’s at Project Gamma only have tempered glass where required by code and the rest of the glass is heatstrengthened. With over 1.55 million pounds (705 metric tons) of heat-strengthened glass and nearly 600,000 pounds (259 metric tons) of tempered glass, the number of potential inclusions in tempered glass is 65. Within three years of substantial completion, almost one dozen pieces of glass had broken and only three exhibited the butterfly pattern characteristic of NiS. However, only one of the three was confirmed to be NiS.
All others breakages were confirmed impact breakages. In one of these projects, a unique breakage pattern on an allegedly heat-soaked glass was found, refer to Figure 1. As can be seen on a close-up image, Figure 2, the shards are rather large. This finding poses the question of whether this pane meets safety standards or not. We will review these images in this paper through the eyes of the safety standards adopted in Europe and the United States.
Heat soaking verification
Projects Alpha and Beta elected to heat soak their tempered glass but unfortunately, the NiS confirmed cases exceeded what was calculated based on the figures presented in EN 14179. Keep in mind that in order to produce glass breakage, a NiS particle present in tempered glass needs to be of certain size and be located within the tension zone. Therefore, it is possible that even with a simply calculated probability based on EN 14179, the two particles in both Project Alpha and Project Beta would not necessarily lead to glass breakage.
That leads up to question, how can heat soak testing be verified? And how can it be enforced in the US when there is no standard for this procedure??
Ignatius Calderone (Calderone, 2019), proposed a method for verifying heat soaking. His proposed method is based on the hypothesis that glass stress distribution at the center is flatter after heat soaking. In other words, there is some rate of annealing that takes place at the different glass layers. His method can be used to calculate this rate at different glass temperatures and provides a baseline for this verification. However, when the majority of the variables are unknown or have to be assumed, this method cannot be utilized with absolute certainty to determine if heat soaking was performed or not. This method does explain the increase in particle count after heat soaking, since the glass’ residual stress is reduced. On a project where all glass has been allegedly heat-soaked and there is no means for determining with certainty what the depth of the compressive layer is, this method could be challenged by some professionals.
Per EN 14179, fragmentation needs to be verified after the heat soaking process and glass still needs to meet fragmentation requirements per EN 12150. By the way, please note that those two standards are identical as it relates to fragmentation. This requirement brings us to the next challenge which deals with breakage pattern/fragmentation. If by heat soaking the glass there is some stress relaxation within the glass layers and some level of annealing does occur, then there would be less residual stress and therefore larger glass fragments (or less fragments) than if it hadn’t been heat soaked. Therefore, safety glazing requirements also need to be met and verified.
Safety glazing standards as it relates to fragmentation
In the United States, per Section 2406.1 of the building code, safety glazing must meet human impact loads. All safety glazing is required to pass the prescribed impact test per Section 2406.2 which references CPSC 16 CFR Part 1201 for Category II glazing. ANSI Z97.1 is the document published by the American National Standard Institute (ANSI) and it addresses “safety glazing materials used in buildings and safety performance specifications and methods of test”. In this standard, it is stated that tempered glass needs to be tested for impact and for center punch fragmentation, however, center punch fragmentation testing is not referenced in IBC.
In Europe, EN 12600 is identified as the Pendulum test – Impact test method and classification for flat glass. For glazing to be classified as Class 1, it needs to be impacted at different drop heights and it provides criterion for cases where glass breaks during testing. The table below summarizes the information stated on ANSI Z97.1 and EN 12600 as it relates to requirements specified for safety glazing.
In principle, EN 12150, EN 12600 and EN 14179 are similar as it relates to meeting safety glass requirements and fragmentation count. These three European standards are comparable to the safety glass requirements in US standards. The difference however, is that there is no US standard equivalent to EN 14179, which deals with heat soaking.
Fragmentation count
As stated before, different standards exist in Europe and the US as it relates to meeting particle/fragmentation count for tempered glass. The section above states glass breakage characteristics as a result of impact testing, but in EN 12150 and EN 14179 fragmentation count requirements are included and it states that for a ¼” (6mm) thick glass, the minimum number of fragments is 40. In summary, the count should be done over the coarsest section on a 2in x 2in (50mm x 50mm) area. In the US ANSI Z97.1 is the equivalent standard and the figures shown in the section above are the required threshold for meeting the fragmentation requirement.
The breakage pattern shown on Figure 1 was captured on trace paper and area calculations were performed. The area calculations are shown on Figure 3 as well as a 2 in. x 2 in. square over the coarsest section. As can be seen, there are less than 10 particles within the square which means that it does not meet EN 12150 or EN 14179. The 10 largest crack free particles on Figure 3, add up to 25 in2 (161 cm2) which is 2.5 times greater than the threshold stated in ANSI Z97.1. This specimen does not meet the safety glass standards, which means that it is not code compliant.
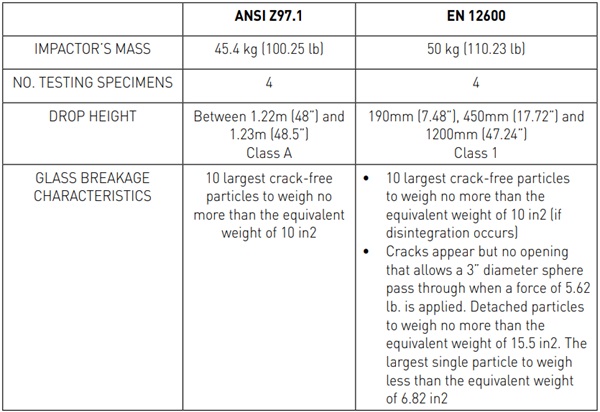
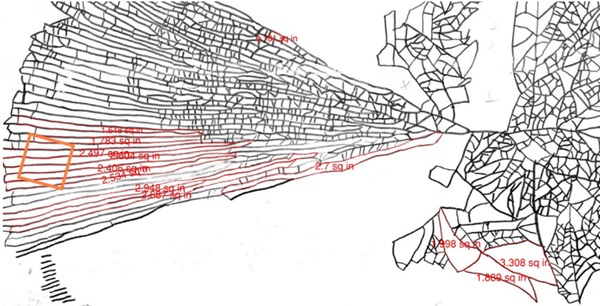
Discussion
Is it possible that due to the fact that heat soak testing is not a US standard yet, the International Building Code widely used in the US, is silent regarding heat soaking tempered glass as far as making it a requirement? In Australia, standard AS1288 requires that tempered glass is heat soaked if certain conditions are met to minimize the risk to pedestrians and users.
Should the US officially adopt EN 14179 or create a heat soaking standard? How can the risk of glass breakage be enforced without having an actual standard? How can heat soaking be verified in the field without having to rely on reports or witnessing the glass assembly?
Conclusion
In the US, many industry leaders and manufacturers are well aware of the heat soaking process and are knowledgeable of the limits and remaining risks. Unfortunately, a few professionals have misguided some developers and stakeholders regarding what heat soaking can do for their buildings and the limits of this test. In addition, some glass manufacturers do not have a good record keeping process in place to be able to corroborate that heat soaking was actually performed.
With the lack of a heat soaking standard or a code-enforced adoption of one, it leaves the door open to dishonest practices that charge for the test when the test is never conducted. This dishonest practice exacerbates developers’ reservations regarding the effectiveness of the heat soaking process. At the end of the day, tempered glass is still being widely used in the US for many different purposes and requirements, but the latent risk of breakage remains there. And with no heat soaking standard, the risk is even greater
References
Calderone, I. (2019). Checking if Heat Soak Testing was carried out. GPD, (pp. 199-204). Tampere.
CWCT. (2008). Lectures. Glass. Bath, England.
Kasper, A. (2019). Spontaneous Breakages of Toughened Glass: The H.S.T. is better than Presumed. GPD, (pp. 205-211). Tampere.
Kocer, D. A. (2015). The mechanical failure of tempered glass; a comparison of testing standards and in-service catastrophic failure. . GPD , (pp. 388-391). Tampere.
Montes-Amoros, V. (2019). Does Safety Glass Manufactured Abroad, Meet US Building Code? GPD, (pp. 362-363). Tampere.