First presented at GPD 2017
Abstract
Architecture is the creation of space, which is (typically) defined and expressed by walls. Walls separate inside and outside. Openings in the walls expose and express their structural depth, which has been a major design feature in the evolution of facade design.
New materials and technology have ever been used for shaping a building’s face, defining its appearance as the walls do with space. Glass-Sandwich-Facades are not conceived with new materials but are a new and innovative combination of proven components and technology – glass, structural adhesive, sandwich panels and window systems. This is a precise response to the ever more challenging boundary conditions of today’s construction market.
1 Introduction
1. 1 Evolution of the wall
The theoretical and philosophical debate about shape, space and surface currently seems more intense than in recent years as the vanishing period of free-form extravaganza has led (and apparently mis-led many) to a sheer limitless vocabulary supported by new design and fabrication technologies. It‘s a kind of back to the roots movement, remembering the basic values of architecture and regaining the status of process owner in the design delivery.
Architecture is the creation of space, which is (typically) defined and expressed by walls. Walls separate inside and outside. Walls have always been a defining element, including or excluding. With great thickness if fortified or for structural reasons a wall can develop an inner life, incorporate (subtractive) space. In the German language there are even two distinct phrases for a wall – Wand (from weaving) and Mauer (from masonry).
Openings within the opaque walls, expressing the structural depth, have always been a key design feature, connecting spaces, public and private, inside and outside. New materials and technology have ever been used for shaping a building’s face, defining its appearance as the walls do with space.
Gottfried Semper is only one of the many sources to be mentioned here, that theoretically and practically dealt with a wall’s many different properties. A façade is a special wall, distinct from inner partitions by its special two and three dimensional treatment that provides for an expression radiating beyond its boundaries.
With the triumph of steel and glass the wall depth and amount of materials involved was reduced to a minimum, leaving such theories behind like Dom Hans van der Laan’s ‘Seven relationships of architectonic space’, that defined a wall’s thickness as a kind of DNA for a building [1]. The individual expression stood back for an aesthetic dominated by industrial products. No more technology leading to architecture, as Perret envisioned it.
In a video tour of his 2014 Venice Architecture Biennale with the Guardian Rem Koolhaas complained about architecture having become a fiction. What is left to the architects would be only the remnant of a real wall, a thin screen in front of all the services pointing out at an exhibit “this is us and that is them” [2].
1.2 Designing with industrial products
In the early 1990s in response to the sheer unmanageable supply of industrial building products that focused on technology and market but not their design potential a studio for Constructive Design was established at the ETH Zurich by Hans Kollhoff. Its goal was to explore design options with industrial products in an experimental approach. For Kollhoff it was not about finding the right construction, that does not exist, but the interrelationship of architectural intent and constructive solution.
Archithese, the Swiss journal, dedicated its May 1993 issue with the title ‘ready-made. Designing with Industrial products’ to that challenge [3]. It was about fighting the loss of architectural expression with the rise of technical perfection. As a main problem the distance between the building industry and the architectural world was identified.
The Constructive Design studio’s first highly influential designs, a series of experimental pavilions, ultimately resulted in a focus on the façade’s surface, corners, openings and joints. The conclusion was that industrial products were semi-finished components that are not ready for an instant application. In Kollhoff’s view it is important that building products are not simply made for an individual styling but that develop their quality in an architectural application.
Per Swiss architect Erwin Mühlenstein working with industrial or standard products will never create a short lived trend as designing and building with them requires a certain intellectual discipline and adaptation of the architectural expression to the respective technology [4].
1.3 Today’s construction environment
From bid to building a design has to sustain many influences in the course of multiple developmental stages. Budgets are tighter than ever, thus decision making is delayed and bid processes are likewise lengthy and often involve several rounds. Too often building envelopes are the first target of a value engineering processes and this applies not only to challenging projects including innovations and exceptional design or construction elements.
For a successful delivery of projects it has become paramount to look beyond scope boundaries and to consider market and feasibility at the very early design stage [5]. Once a design has finally evolved other challenges such as quality issues caused by price and time pressure as well as unskilled workforce must be coped with. That are all aspects that also a highly digitalised delivery process so many have become dependent on cannot resolve.
As a consequence of that situation and based on more than 30 years of experience with the most challenging building envelopes and structures, iconic skin GmbH, which is part of the seele group, has developed a building product that helps overcome these issues - the Glass Sandwich Panel GSP®.
2 Status Quo of GSP® and the Glass-Sandwich-Façade GSF
2.1 GSP® Conception
The GSP® development was not about reinventing the wheel but it is a new and innovative combination of proven components and technology – glass, structural adhesive and sandwich panels [6].
6mm HS glass panels with full ceramic print are structurally bonded to lightweight and easy to handle sandwich panels. The bonding is carried out with strips of adhesive. Elements can be produced as long as 16,0m, with a width of up to 1,50m. The sandwich panel is the load bearing component and provides for impermeability as well as the excellent thermal and acoustical properties. However, the tremendous design potential lies within the glass panel with its perfect surface that provides for much more metaphysical depth than its physical 6mm thickness.
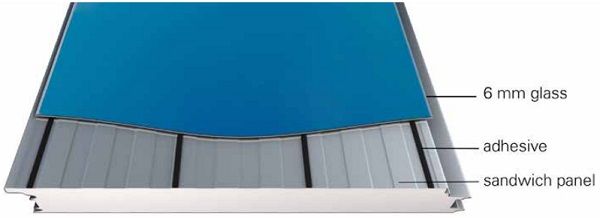
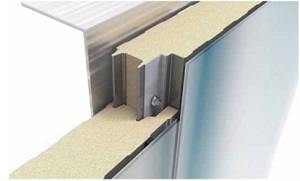
The unit can be fixed to frameworks or solid walls, the latter e.g. for renovations or upgrades. Because of the glass panel’s opacity no bonding or other means of fixing are visible as the screws are concealed within the joints (Figure 2-2).
If aesthetically or functionally required, the GSP® panels receive on their backside facing the interior a drywall system. In front of a solid wall the cavity between the two components is warm, as it is closed at the upper and lower perimeter with a permeable insulation.
2.2 Glass-Sandwich-Façade GSF
In combination with window systems GSP® becomes the Glass-Sandwich-Façade (Figure 2-3). As a warm system it provides for a near seamless and dry transition between the two main components, omitting problematic interfaces or connections requiring attention and maintenance throughout their life-span. The window profiles are fixed to GSP® with system compatible transfer profiles, which also take the loads of the windows (Figure 2-4).
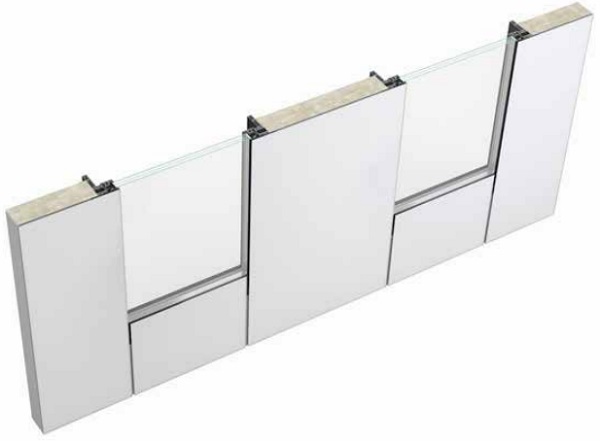
That principle allows for new applications as a secondary back-up structure is typically not necessary. In horizontal applications windows can span the full length of a panel. [7]
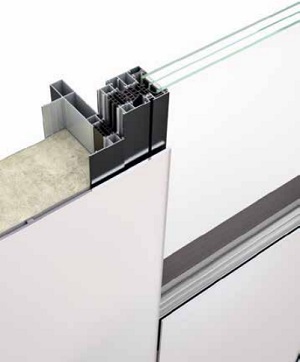
Unlike a cold façade system that involves many layers and interfaces that need to be well coordinated from design to completion, the Glass-Sandwich-Façade is basically one element and layer that can be easily managed during design, bidding, fabrication and installation. With all components being pre-fabricated high levels of precision and quality are achieved and thus errors during the efficient installation period on site can be prevented.
The easy handling throughout the whole delivery process is only one of the many sustainable and commercial advantages that continue beyond the completion date. The glass panels of GSP® can be e.g. exchanged in situ, without opening the building’s physical barrier.
And at the end of the life cycle GSP® can be more or less completely recycled. Whether a client looks for cost conscious aesthetics, the designers for aesthetics and individuality, a system processor or building operator look for a hassle free product – they all will find their objectives met with a GlassSandwich-Façade.
2.3 Configurations
GSP® panels are applied in either vertical or horizontal direction, creating a basic linear joint system. The joints can vary per floor or express the full building height. No other highend cladding panel is available in that length.
Adaptations and creation of movement can be achieved via the following design options that were initially presented at the BAU 2017 in Munich this year:
• 2D Print GSP®
• 2D Pattern GSP®
• 2D Light GSP® lumen
• 3D Embrasure GSP®
• 3D Shingles GSP®multilam
• 3D Rotation GSP®
• 3D Material switch GSP®
The prime design feature is the glass panels’ individualisation via ceramic printing – digitally, by roller or screen print. Or in a combination of them e.g. if signage or special imagery are desired. The advanced technology creates long lasting and colour-fast treatment that makes the product look the same all throughout the life cycle. Later changes or add-ons will match the other panels.
A recent completion of a commercial project in Dortmund, Germany, involved a special dynamic design called ‘Dortmund Crossing’ conceived by artist Joerg Maxzin (Figure 2-5). 60 GSP® panels received illusory images with digital printing. Another 150 GSP® panels completing the curved glass ribbon surrounding the volume on the ground floor level were screen printed. A standard product became a case specific and identity creating application solely by treating the glass surface on one side.
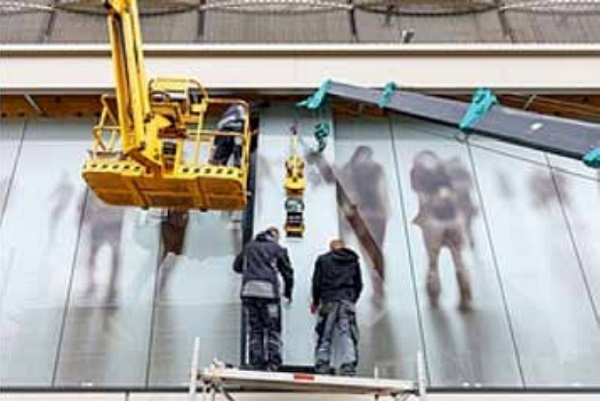
3 Summary
The presented product development is a precise response to the ever more challenging boundary conditions of today’s construction market, budget conscious without compromising aesthetics. It shows that glass remains also in an opaque application an important enclosure material. GSP® is an all-in-one product with an easy to individualise surface that with or without plug-ins provides for a multitude of architectural expressions. It shows that industrial building products do not necessarily limit design options, but rather open a whole range of new opportunities if their basic properties are understood and reflected in the design concept from the beginning.
4 Literature
[1] Van den Bergh, W.: Wand und Raum. In: der architekt, Düsseldorf: Bund Deutscher Architekten, 2016 (04), 35-40
[2] Wainwright, O., Levene, D.: https://www.theguardian.com/artanddesign/video/2014/jun/06/rem-koolhaas-fundamentals-venice-architecturebiennale-video
[3] Kollhoff, H., Baumann, D.: Experimentelles Entwerfen mit Industriebauprodukten. In: archithese 5.93, Zürich: archithese 1993, 46-47
[4] Maurer, B.: Eternitgerecht Bauen. In: archithese 5.93, Zürich: archithese 1993, 24
[5] Frey, H.: From bid to building. In: Glasbau 2016, Weller B., Tasche S. (eds.), Berlin: Ernst & Sohn, 2016, 33-45.
[6] Teich, M., Mertel, H.: iconic skin glass sandwich panel. In: gpd proceedings book 2015, 13-15
[7] Teich, M., Radner, W.: Glass Sandwich Facade – development of a new façade typology. In: Glasbau 2017, Weller B., Tasche S. (eds.), Berlin: Ernst & Sohn, 2017