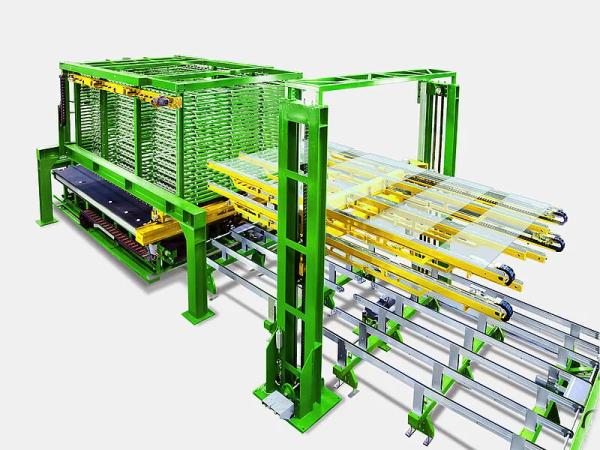
Date: 8 June 2023
To begin with, however, the objective is to reduce costs and improve or automate processes. The big solution doesn’t have to come all at once. It often pays to take a closer look at individual steps, according to Dr Jan Schäpers, Managing Director of HEGLA-HANIC, the specialist for software for the glass industry.
Where is paper being used?
If prioritisation or analysis is difficult at the beginning, Jan Schäpers recommends a topic for initial reflection that regularly proves its worth: “Where are we still working with paper? Which processes are being controlled without software or manually triggered?”. Jan Schäpers explains the reason as follows: “The work steps where information is transferred manually or by routing slip are more prone to error and typically slower than system-controlled sequences.” In the ideal case, the data required can be integrated into the MES and production planning software via an interface – or even better, input centrally there for all needs. Making the data automatically available from a central location excludes errors and enables companies to leverage their entire potential. If the technical effort required to compile the data is too great, transferring information via scan is a viable alternative. When a machine-readable sticker or laser marking is used for scanning, the processing step can be documented for product traceability or evaluated for production planning at the same time. Depending on the extent to which the company drives its data integration, the ID or code from the marking can be used to trigger processing steps without the risk of any mix-ups. The data for processing a previously set-up pane are directly available to a double edger, for example. And the information as to whether RF-transparent or bird protection glass is to be produced can be transferred to a laser processing system as well. If the end of a process is also acknowledged via scan, this creates valuable production data and makes these available for capacity and production planning.
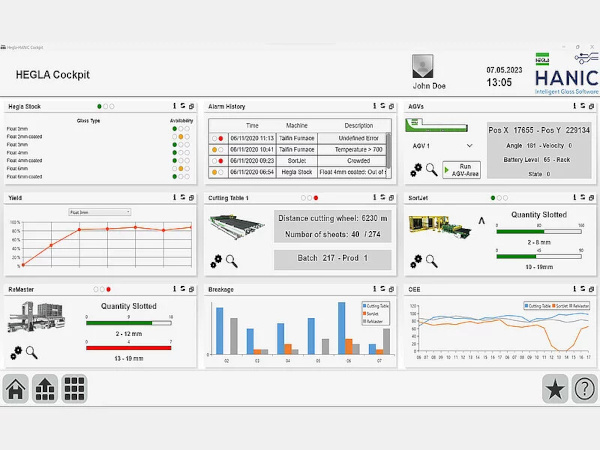
Reduce offcut costs with dynamic continuous optimisation
Offcut optimisation is certainly one of the perennial concerns of glass processing companies. But the increasing cost of glass today has made the topic even more relevant. Depending on the product portfolio and level of automation in handling, the use of dynamic continuous optimisation holds the promise of additional benefits. “With this approach, optimisation is applied to multiple batches and is continuously adjusted: for example, when panes are remade or new orders are created in the ERP,” explains Jan Schäpers. This increases the utilisation rate and reduces resource consumption. Additional potential can be created by an automatic remnant system that is linked to the optimisation software and holds usable panes ready for access by the cutting system.
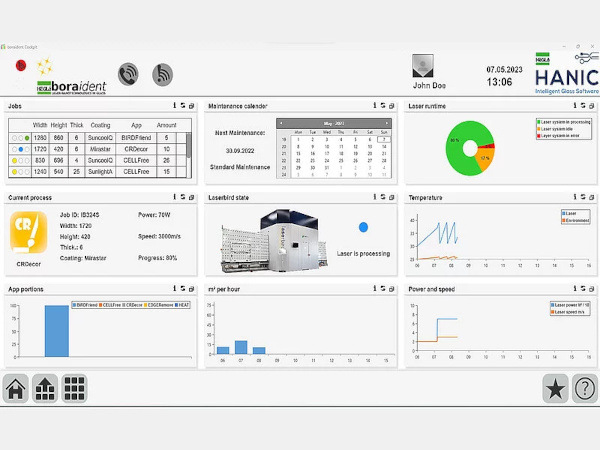
Transparent information
The large quantity of data made available as a consequence of digitalising and automating systems and process steps offers a starting point for getting employees even more involved and on board with regard to their daily tasks. First, collecting this information improves their knowledge of production. Second, it has often been shown that implementing a cockpit in a company improves communication and understanding among employees. Depending on the data selection and storage mode, monitors in the production area display the current stock levels and indicate whether or not cutting or insulated glass production is still on schedule and which batches should be prioritised on a given day. If desired, an intuitive traffic light system with a target/actual comparison can provide information as to whether or not production is still in sync or action is required.
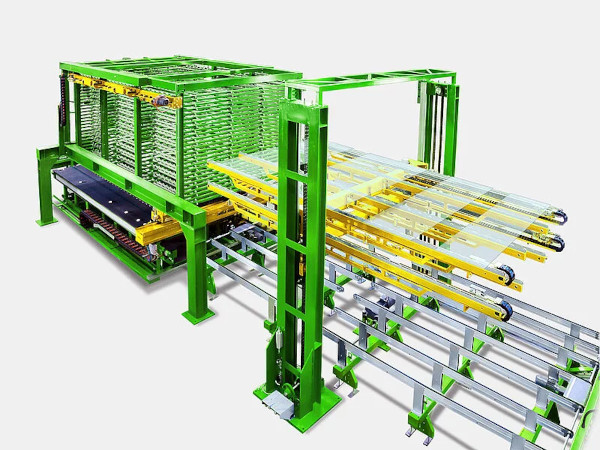
The shop floor as the sum of the parts
Alongside the many small and medium options, the comprehensive networking and digitalisation of the ERP to production planning software and the machines ultimately offer further starting points. Here as well, Dr Schäpers recommends first looking at areas that are not directly integrated into a process or are manually controlled via paper. Depending on the portfolio, optimisation of the ordering process in the ERP can be worth considering in order to automatically import the customer order and run a plausibility check or request missing information. And depending on the configuration, the stock level is immediately checked and a control code for the various systems is generated. For some companies, triggering shipping document creation via automatic or manual scan at the system is ideal. The more the various systems and departments communicate with each other directly or are controlled by software, the less prone the overall system is to errors and delays. “In recent years, the dynamics within the economy have shown that alongside the major goal of Industry 4.0, the smaller intermediate steps are also valuable when the aim is to improve processes, minimise errors or flexibly adjust to changing requirements,” says Jan Schäpers.
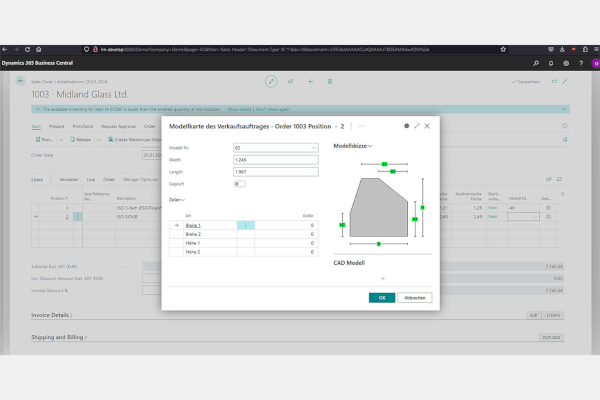
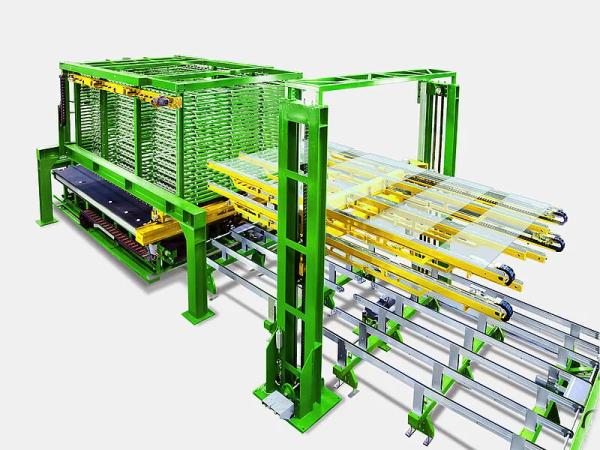

Add new comment