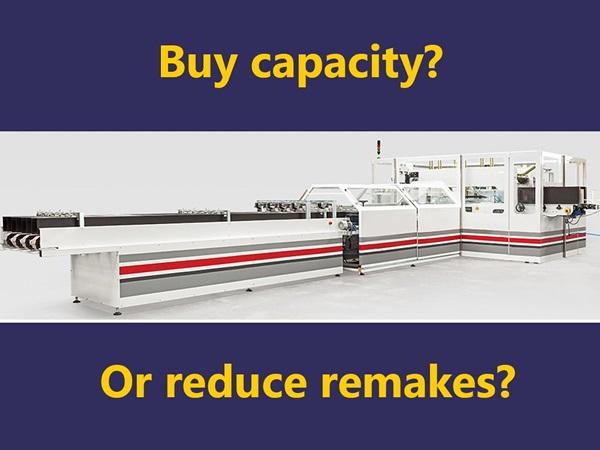
Date: 30 August 2019
It’s possible, even likely, you’re unaware how much rework is costing your business. It’s much more than just direct time and materials.
In fact, if you’re considering investing in equipment or adding workers, instead reduce costs while improving quality and efficiency.
At one manufacturer, the plant pretended rework did not exist and went into chaos every single day to handle it. This was classic firefighting mode.
Worse, no one was monitoring rework requirements or prioritizing resolving the issues. Management saw the daily hours versus throughput and thought the team was slow or slacking off.
Yikes!
Rework symptoms
Is your plant floor in reactive mode every day? How often is production stopped for rework on a task?
Operating in reactive mode impacts on-time performance. How often do you tell (or hide from) customers that their order didn’t make it on the truck because of rework?
A chaotic work environment also takes a toll on workers. If turnover is higher than normal, the cause could be rework.
Are job margins good but profits lower than expected? Estimates are that high-performing companies spend fewer than one percent of profits on rework. Lower-performing customers are in the two to three percent range, while others can be even higher.
More on rework’s financial costs
Do you incorporate material costs for rework into your job costing analysis? How about the extra labor dedicated to the job?
Or the lost opportunity to be manufacturing another job with that same labor?
Again, if you don’t recognize and correct rework issues, you may be investing in equipment or hiring workers to increase throughput.
As rework is essentially a quality issue, you will likely be experiencing field replacement costs and reputation damage if high remake rates are left unaddressed.
Is rework costing you? A simple test.
Each manufacturer is different. To determine if rework is reducing productivity and cutting into your profits, you can run a simple test.
1. Identify ideal throughput
Run a full shift without any rework introduced and eliminate distractions from the front office, e.g., no questions about jobs; no interruptions.
Record the following:
- Quantity of products manufactured
- Revenue generated
2. Identify the cost of rework
Run a full shift allowing rework, but eliminate distractions from the front office, e.g., no questions about jobs; no interruptions.
Record the following:
- Quantity of new products manufactured
- Revenue generated on non-rework products
- Quantity of products reworked
- Time spent on rework (labor cost)
- Quantity and cost of extra material used on reworked products
3. Analyze the results
Monetizing the impact of errors causing rework while excluding any other causes of lower production efforts allows you to better understand the full impact rework has on your current jobs.
What if there were no rework?
Imagine your operation without rework. How much more could you make in a shift? A week? A year?
How much could you shorten lead times? Would this give you an edge on the competition?
It starts with knowing how much time you spend on rework each shift.
I’ve seen companies decrease rework and shorten manufacturing lead times by days. Customers receive a better product and get it faster. You see an increase in revenue and profit margins. I’d call that a win-win.
How can you transition from a reactive environment to a proactive and productive environment?
We address that next month when we examine five strategies to reduce rework.
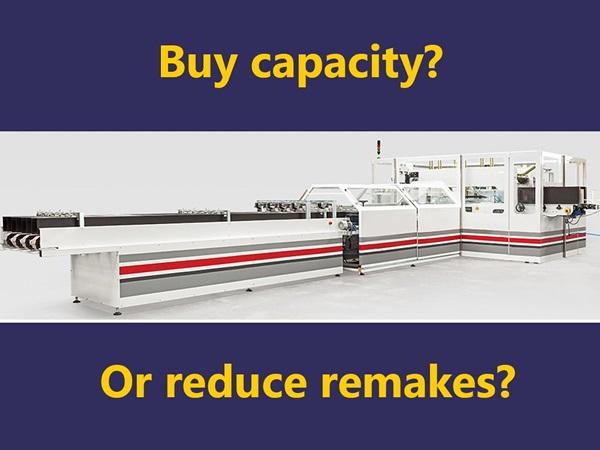

Add new comment