Author: Shady Attia
Sustainable Building Design Lab, UEE, Applied Sciences, Lie`ge University, Lie`ge, Belgium
ABSTRACT
The assessment of adaptive facades presents a barrier as there is no established assessment technique. Many of the available facade performance evaluation systems or frameworks have limited applicability for such advanced building facades.
The complexity of adaptive or dynamic facades’ evaluation is related to the performance evaluation of facade elements, systems, and overall building performance coupled with occupant behavior and occupant satisfaction. In this context, this paper presents a case study of an adaptive sunscreen facade and evaluation of its performance and occupant behavior.
The evaluation mainly focuses on pre- and post-construction phases of adaptive facades: the design assist phase (including the durability test, visual mockup, onsite mashrabiya mounting, and weather stripping), the commissioning phase (field verification and performance testing), and the monitoring phase.
The selected project is a 150-meter-high twin tower that stands with a honeycombinspired structure and automated dynamic solar screen that responds to the sun’s movement. These solar screens respond dynamically and automatically to the angle of the sun, which improves the control over energy consumption, solar radiation, and glare with the ability to allow natural light into the building.
This paper is part of the research activities of working group 3 of the European COST Action 1403 on “Adaptive Facades”. Different methods were used for evaluation and these include the following: interviews with the architect, facade engineer, technical control specialist and occupants, reviews of standards and codes, review of energy models, and a systematic design process mapping.
A documentation of the case study describing the post-construction occupant comfort and facade operation was prepared. This paper’s audience comprises mainly project managers, architects, and building facade engineers together with facility managers who are concerned with the process of design, construction, and operation of adaptive sunscreens facades.
The outcome of this study identifies quantifiable performance indicators and effective strategies for the design and performance evaluation of optimal adaptive facades.
Keywords: sunscreens, occupant comfort, solar gain, daylight, operation and control
1. INTRODUCTION
In a world confronting environmental challenges, there is an earnest requirement for dynamic building envelopes that respond to climatic changes in an ideal way, thereby giving the best comfort and indoor environmental quality, while keeping up high effectiveness.
Adaptive facades can provide step-change upgrades in the energy efficiency and the use of renewable energy while improving the comfort of buildings for tenants. In this manner, they are vital in accomplishing Europe’s 2020 targets.(1)
Adaptive facades are building envelopes that can adjust to changing climatic conditions on an hourly, daily, seasonal, or annual basis. Here the word “adaptive” means the capacity to react or profit from outside climatic conditions to meet productivity and more essentially to successfully meet the inhabitant’s comfort and well-being.(2)
Adaptive facades are multi-objective, high performance envelopes that, unlike static curtain walls, respond mechanically or chemically to external climate dynamics to meet inside load requirements (cooling, heating, lighting, or ventilation) and occupants’ needs.(3)
Various existing projects integrating adaptive building envelopes are constructed worldwide. According to the Climate Adaptive Building Shells (CABS) database, which is continuously updated, there are at the moment more than 500 examples of buildings with adaptive facades.(4)
However, detailed data on the performance, design, and construction process of those facades are not commonly available. Commissioning and construction verification details, performance data about adaptive facade’s monitored operational performance and post-occupancy evaluations are lacking in literature.(5–7)
Currently, European research in the field of adaptive building envelopes is coined by numerous nationally funded projects. COST Action TU1403 is one among those projects that aim to create a knowledge transfer between the individual research institutes among each other and the industry.
The initiated COST Action TU1403 “Adaptive Facades Network” aims to pool together knowledge, technologies, and research from across European countries and beyond. The initiated COST Action TU1403 project started in 2014 and will run for four years.
Currently, 26 COST member countries and Liechtenstein, China, and Australia are involved in this COST Action project with more than 80 participants from research institutions and industries.(8)
The main objective of this action is to harmonize, share, and disseminate technological knowledge on adaptive facades at the European level.
This will lead to increased knowledge sharing between European research centers and between these centers and the industry, thereby leading to the development of novel concepts, technologies, and new combinations of existing technologies for adaptive facades, as well as gaining knowledge on effective evaluation tools/design methods for adaptive facades.
As part of Workgroup 3, we address challenges and identify gaps in the systematic assessment and operation of such solutions, in terms of both commissioning and operation, through literature review and mapping analysis.(9,22)
Therefore, the aim of this study was to investigate the adaptive facade of a 150-meter-high twin tower with a unique honeycomb-inspired structure and an automated dynamic solar screen.
Today, there are a great number of facades and envelopes’ technologies that are readily available in the market. The decision as to how they are designed, operated, maintained, and assessed remains a challenge. Our case study, presented in this paper seeks to provide better understanding of their design process, modeling, and real performance.
It will help illustrate the benefits as well as the challenges seen in specific solutions with respect to energy use, comfort, operation, and maintenance. Currently, only a limited number of case studies have been documented.(5,6)
This includes Al Bahr Towers in Dubai,(7) AGC Building in Louvain La Neuve,(10) and the BIQ house in Hamburg.(11) The decision as to how they are designed, operated, maintained, and assessed remains undisclosed and this in turn affects the wide expansion of adaptive facades.
The paper is mainly concerned with the adaptive facades’ system design and assessment. The work group explores to understand how adaptive facades were designed and assessed during the following major project delivery phases:
- Predesign and design process;
- Schematic and conceptual design;
- Design development and construction;
- Design assist (pre-construction testing);
- Commissioning;
- Occupant operation (behavior);
- Post-occupancy evaluation and monitoring.
In this paper, different research methods were used for the case study, including: literature review, site visit, interviews with the architect, facade engineer, glass manufacturer, commissioning agents, reviews of standards and codes, and systematic process mapping.
Within the scope of this study, we present a case study description and technical details for the adaptive facade of Al Bahr Towers.
The case study provides significant insights into the design and construction process and the overlap between the glass product development and manufacturing and the building delivery process including mockups and onsite testing and verification.
Section 2 begins with the description of the research methodology followed in the present work. Section 3 describes the case study and discusses the main findings of the literature review. Section 4 presents the paper findings and results along with three themes: (i) process mapping, (ii) interviews result, and (iii) performance evaluation.
Sections 5 and 6 conclude with setting a list of learned lessons, emphasizing the need for addressing some of the recommendations and key performance indicators to guarantee a successful performance of adaptive facades.
2. METHODOLOGY
The goal of this work was to describe in detail the process of design, construction, and use of an adaptive glass facade of Al Bahr Towers, and to evaluate its performance. Furthermore, it aims to propose a generic performance process map that could be used as a visual guideline support by companies in the building industry.
First of all, several existing documents were reviewed. Almost all Al Bahr Towers publications(6,7,12 – 15) as well as the different standards and codes used for the building design and construction were reviewed, including: the CWCT(16) Standard Test Methods for Building Envelopes and British standards including the BS6399-2:1997, loading for buildings, and code of practice for wind loads.(23)
Secondly, a design and construction process map was developed. The development of such a map required more than a literature review. Indeed, the created map had to be validated and tested through live one-to-one interviews with different project stakeholders.
Thus, this case study follows an iterative loop of development, test, and review of information as presented below:
- Extraction of the required information on actual integrated processes from the literature with a main focus on the three specific points (steps, roles, and tools).
- Development of a map of the design process based on the previous information.
- Correction of the map conceived in Step 2 by conducting interviews with architects or engineers involved in the Al Bahr Towers project.
- Final discussion and recodification of the maps.
- Comparison with literature – back to Step 1.
The software MindMap was used to realize global and specific maps of the project delivery process. This software allowed drawing clearly hierarchical scales, task charges suite, and information flows.
To limit the scope of the process map, we focused on the identification and modeling of generic processes that were associated with the Al Bahr Towers project delivery. The generic process identification can be generalized and used as a check-list for future designs of adaptive facades.
Therefore, we focused on the following three main questions:
- Steps: what series of phases an integrated process has to pass through and what are the determinant criteria for each step?
- Roles: repartition on the responsibilities and scope of work, who must do what, how, and when?
- Tools: which software is used during the process and for what purpose?
Creating a process map involved systematic data-based interviews. Interviewees were asked to explain exactly what they did during the project delivery of Al Bahr Towers as well as to share their technical challenges and to express their expectations. For every interviewee, a scope was defined identifying the parameters he or she was dealing with during the project.
A technical drawing software program was used to visualize the process. After completing the first round of interviews, interviewees were asked for feedback (reviews) and confirmation to validate the process maps. Finally, a documentation of the case study was prepared, thereby describing the post-construction occupant comfort and facade operation.
The evaluation focuses mainly on preconstruction and postconstruction phases of adaptive facades. We conducted several interviews mainly with the towers’ designer, Abdulmajid Karanouh, director of facade design and engineering as well as the technical control specialist.
The third part of the study addresses occupant satisfaction and thermal comfort of Al-Bahr occupants. Physical monitoring was not allowed by the building manager and the facility manager could not share any real consumption or comfort data.
Therefore, we opted to use questionnaires for indoor environmental quality assessment. A total of 22 employees responded to our online survey comprising multiple choice questions with one or more responses and short or long open answers (not exceeding 10 minutes).
The questionnaire was based on Annex “Thermal Environment E2 Satisfaction Survey” of the standard ASHRAE(17) 55 and the Center of Built Environment standard questionnaire that seemed complementary.(24)
3. CASE STUDY
Abu Dhabi Investment Council is the investment arm of the Government of Abu Dhabi that is responsible for investing part of the government’s surplus financial resources. In 2008, the Abu Dhabi Investment Council launched an international competition for its new headquarters.
The new headquarters is located on the North Shore of Abu Dhabi Island, overlooking the Eastern Mangroves and toward Sadiyaat island and the Persian Gulf beyond. Therefore, the project was named Al Bahr, which means “the sea” in Arabic.
Abu Dhabi experiences hot and humid climate and extremely sunny days with temperature and humidity reaching 498C and 100%, respectively during summer. Aiming to design two iconic towers, the design brief called for two 25 story towers to create an outstanding landmark reflecting the regions’ architectural heritage together with the corporate status of the clients’ organization.
The primary business functions of the towers include financial transactions, brokering, and dealing including Al Hilal Bank. At the same time, the project brief requested a contemporary sustainable building using modern technology without setting any performance or certification requirement.(21)
3.1. Concept
The project concept is inspired by the traditional Islamic object the “Mashrabiya” and motifs to stand out with two circular towers covered by a honeycomb-inspired structure and its automated dynamic solar screen.
The “Mashrabiya” is a wooden lattice screen found in traditional Islamic architecture and used as a device for achieving privacy and environmental control including natural ventilation, solar control, and glare reduction. The project area is 56,000 square meters primarily for office use (Bank).
The design submitted by architect Abulmajid Karanouh (Aedas) offers two 150-meterhigh circular towers clad with curtain wall covered with a kinetic shading system (Figure 1a). The tower floor is open plan office spaces with service core.
In some floors, the space is divided into cellular offices and meeting rooms. Each tower has a two-level basement with 24-story office space that includes catering, auditoria, prayer rooms, gymnasium, and plant rooms. There is a basement for car parking and secure vaults for banking services.
Following an international design competition, the client chose the striking concept submitted by a UK-based multidisciplinary design team (Aedas/Arup). There is an entrance podium for both towers covered with a 100-m curved roof.
The buildings are fully air-conditioned with various back areas associated with storage and catering. Finally, the project won the 2012 Council on Tall Buildings and Urban Habitat (CTBUH) Innovation Award5. The project concept was placed second at the Emporis Skyscraper Award – the world’s premier event for high-rise architecture – for projects completed in 2012.
The project has been featured on the Chicago-based Council on Tall Buildings and Urban Habitat’s “Innovative 20” list of buildings that challenge the typology of tall buildings in the 21st century.
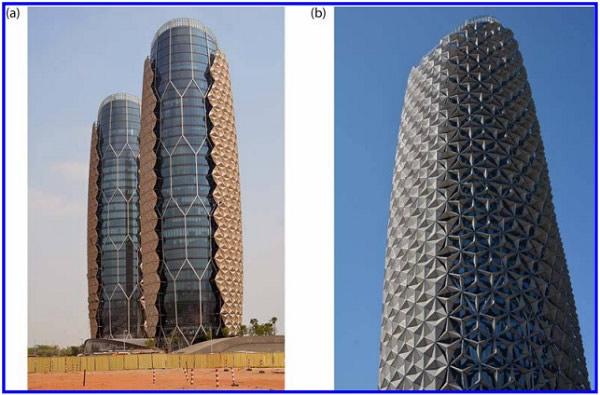
3.2. The envelope
The two circular towers are clad with weather-tight glass curtain wall. The curtain wall is comprised of unitized panels with a floor-to-floor height of 4200 mm and a variable width of 900– 120 mm. From floor to ceiling, the vision area of the curtain wall spans 3100 mm.
The curtain wall is separated from the kinetic shading system through a substructure by means of movement joints. The fixation of the substructure movement joints (cantilever struts) is at the first basement, ground floor, and podium levels, thereby allowing them to respond independently from the substructure.
The dynamic shading system is a screen comprised of triangulate units such as origami umbrellas. The triangular units act as individual shading devices that unfold to various angles in response to the sun’s movement in order to obstruct the direct solar radiation.
Each mashrabiya was conceived as a unitized system, cantilevering 2.8 m from the primary structure. The shading device system contains stainless steel supporting frames, aluminum dynamic frames, and fiberglass mesh infill. The folding system transforms the shading screen from a seamless veil into a lattice-like pattern to provide shade or light.
Each shading device comprises a series of stretched polytetrafluoroethylene (PTFE) panels. When the shading device is closed, occupants can still see through from inside to the outside (Figure 2). In total, each tower has 1049 mashrabiya shading devices, each weighing about 1.5 tonnes.
The shape of the building in plan and elevation led to 22 different variations in the mashrabiya geometries, which in itself created a challenge for managing their manufacture and assembly.
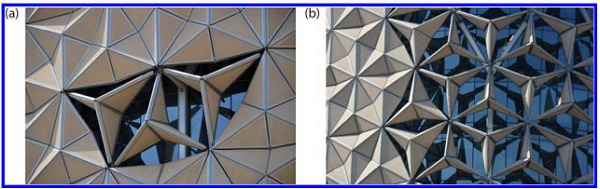
3.3. Automation and adaptations
The shading screen is computer-controlled to respond to optimal solar and light conditions. The mashrabiya shading devices are grouped into sectors and are operated through sun tracking software that controls the opening and closing sequence according to the sun’s angle.
Each shading device comprises a series of stretched PTFE panels and is driven by a linear actuator. The actuator is responsible for opening and closing once per day based on a pre-programmed sequence to prevent direct solar radiation.
Under overcast conditions or high wind conditions, a series of sensors integrated on the building envelope will send its logged signals to the control unit to open all units.
Figure 3 shows a detailed 3D model of an individual shading device with the actuator, sleeves, arms, and fabric mesh. The 1049 mashrabiyas are controlled through a central Building Management System (BMS) that can control each unit individually or in groups.
The system is run with Siemens technology in a preset automated control following the sun’s path through the year. The system is updated every 15 minutes using a light meter and an anemometer on the roof. In case of weather events, the automated program gets overridden.
Power and data transmission is enabled through the strut sleeves, as shown in Figure 4a. The mashrabiya has a service life of 20 years including the PTFE-coated fiberglass fabric and the actuators have a service life of 15 years.
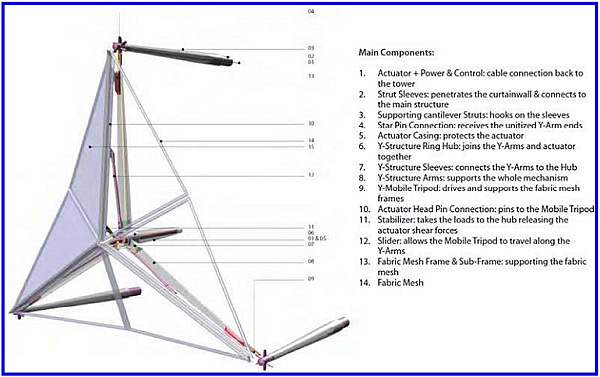
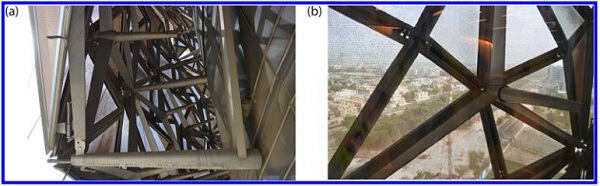
4. RESULTS
Several interviews have been conducted to identify exactly the roles of the project’s main stakeholders in different stages. This included the architect, energy consultant, building’s users, adaptive glass facade sub-contractor, shading system manufactures, commissioning agent, and the facility manager. The key steps of the adaptive facades’ delivery process are identified as follows: decisions, checklists, and teams engaged in each stage respectively.
One of the most significant findings related to this project was that the client required a “sustainable office building” similar to Northern or Western type of concrete and steel structures with a panoramic glass facade similar to mainstream offices that you find in the Gulf Countries.
Surprisingly, the project did not get certified by any LEED rating system and Arup modified its reporting by stating that the project is designed in accordance with the US Green Building Council’s LEED rating system instead of stating that the project failed to get certified.
4.1. Al Bahr Towers’ building project stakeholders and process map
The process mapping was completed by interviewing seven project stakeholders representing the facade contractor, architect, general contractor, energy and building physics consultant, commissioning agency, and facility manager. Figure 5 shows the results of the interviews and represents the different stakeholders of the project.
The process map, as shown in Figure 6, indicates that there were 12 major design stages in this project, named according to the AIA.(18) The figure shows the process map after being validated, illustrating the design and construction stages of the adaptive facade as a whole.

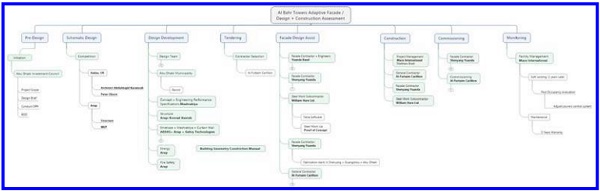
Click here to enlarge.
4.2. Description of the facade design process
The interviewees revealed that the delivery process of Al Bahr Towers underwent an iterative process with an experimental validation approach. The iterative approach did allow a holistic, integrated and iterative approach. The project underwent the following 12 stages:
- Competition with the dynamic Musharabeya concept (Abdulmajid);
- Setting the design team, (AEDAS þ Arup);
- Submission of the project (July 2007);
- Wining the competition (Nov 2007);
- Assembling a design team (70 architects and 150 engineers (structure, MEP, Fire, etc.)) þ Design development and construction documentation;
- Tendering and contractor selection;
- Mock-ups;
- Benchmark (Figure 7);
- Construction;
- Occupation;
- Commissioning;
- Soft landing.
To ensure proper coordination between the various building components, a digital model was used to guarantee the coordination and integration between the concrete core, the structural steel frame, and the mashrabiya.
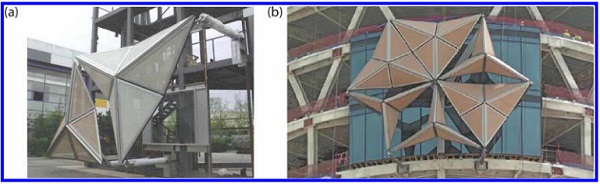
4.3. Description of the facade assessment process
Most of the facade testing took place offsite. The facade assessment had a limited budget in relation to the project size. The design team had to rely on simulation tools and computational fluid dynamic (CFD) analysis.
Then static mock-ups and the mechanical mock-ups were put on hold. It was important to set up a visual and kinematic mock-up first. A series of wind-tunnel tests were also conducted at various scales.
The fluid form of the building led to a low positive and negative pressure during the testing, averaging 1.5 kPa up to a maximum of 3.5 kPa. The facade contractor was responsible for the following three mock-ups (Figure 7):
- Onsite mock up for fabric testing;
- Laboratory tests in Switzerland (Yuanda Basel) in a special chamber to test the mechanics for 30, 000 cycles (chamber conditions: humidity 100%, temperature 658C, and sand mixed with salt). The shading devices were tested to check whether it can be operated with a high reliability and robustness. The shading devices are prone to wind-induced movements and aggressive environments containing sand, dust, and salt-laden air. A series of prototype tests on the PTFE panel were conducted at both ambient laboratory and elevated temperatures to the check the required durability and life of actuators, bearings, and overall mechanism;
- Mock-up in China for lighting (Shenyang Yuanda). Then, a benchmark was set up onsite.
The facade assessment and commissioning was mainly under the control of facade subcontractor. There were serious issues with commissioning the building facade. It was supposed to have a third party commissioning company but it was carried out finally by the facade sub-contractor after two years of operating the building.
The process was underpaid and had misrepresenting professionals. In general, testing and validation was underappreciated by the client when it came to an adaptive facade. Regarding soft-landing, the late commissioning of the buildings postponed the soft-landing to 2015; the building was constructed in 2011 and opened in 2012.
The project manager needed twentyfour months to carry out the soft-landing after occupation. The idea was to monitor the building for twelve months, then effectuate changes, and then measure again the results of their intervention to reach the optimal operation mode.
However, only a 12-month monitoring was conducted in 2015. The monitoring helped in identifying occupant behavior of building users and highlighting the deficiencies encountered during the summer and winter cycles.
4.4. Survey results
All respondents work in zone 2 of the tower (office floors from 10 to 20). Concerning thermal comfort, the initial survey results indicate that, 12% of occupants are very comfortable, 42% are comfortable, 32% are neutral, 10% are uncomfortable, and 4% are very uncomfortable.
The main reason for discomfort that was recorded by females was overcooling. For natural lighting, the results are distributed as follows: 20% are not comfortable and 40% are very uncomfortable. At the beginning, we thought that this was due to glare; however, the main reason was related to the automated opening and closing of the mashrabiya.
A large percentage of occupants stated that they were annoyed by the regular opening and closing of the mashrabiya that does not allow them to interact with the facade. Despite the user-controlled roller-blinds, which allow occupants’ personal control of their environment, they are kept open most of the time according to the respondents.
The automation is causing a widespread occupant discomfort, which is accentuated by their passivity toward their indoor environment control.
Several respondents indicated that the inability of interaction with the mashrabiya did not allow them to get involved in controlling their indoor environment. So far, we have considered this in its initial phase with a little representative number of 22 employees out of 1000 employees of the two towers.
5. DISCUSSION AND CONCLUSION
The primary objectives of this study were to present a detailed case study description of a building with an adaptive facade and to derive maps of the underlying decisions on how it was designed, operated, maintained, and assessed.
This study required time, effort, and analysis to interview Al Bahr project key stakeholders. The required data interpretation and classification were mainly based on the interviews and surveys. The facility management company refused to cooperate in this study and did not share any performance data on energy consumption or comfort conditions.
However, we succeeded in creating a sophisticated process map representing most stakeholders who participated in this outstanding project. For sure, the project is an outstanding project from the design and construction point-of-view but not from a sustainability point-of-view (see arguments 6–9).
Therefore, and after this long endeavor, some key learned lessons were drawn and these can be considered in any future building with an adaptive external shading facade:
1. The project embedded a series of innovations and is the fruit of a successful collaboration between the client, design team, and builder. The mashrabiya concept and its implementation are ground breaking and the towers succeeded as an iconic landmark. The design team pushed the boundaries of design and managed to set new standards for quality in the AEC industry.
2.Another success of the design team was that their members identified the performance requirements for the adaptive facade. Without quantified performance indicators, the project would not have succeeded. Arup in particular had the vision, early on in the project, to develop the Mashrabiya Performance Criteria Development Guide and the Building Geometry Construction Manual.
Both documents set new standards for the facade design and construction quality. The performance quantification resulted in a rigorous design assist phase with several models, mockups, and prototypes testing. Both documents set up the specification of the facade performance with a focus on structural and mechanical properties and durability of the facades.
3. The use of BIM (building information modeling) and parametric geometrical modeling was a crucial tool in concept development and team collaboration. The use of building information technology and parametric modeling allowed the team to operate in an efficient, integrated, and effective manner.
The advanced computation design capacity of the design team (AEDAS þ Gehry Technologies) allowed the building envelope development and the rationalization of the complex facade geometry including the curtain wall glass panels in a uniform and coherent manner.
The use of Rhino Script to calculate the deflection limits of glass panels based on established algorithm rules was a key step in refining and optimizing geometry. The glass panel optimization process led to the elimination of custom manufacturing of glazing.
Moreover, the paramedic advanced modeling technique was the key methodology used in controlling the mashrabiya folding limits and generating precise shop-drawings for implementation. The procurement of the building envelope under one contract was the reason to valorize the BIM model and empower the modeling team.
Gehry Technology, which assisted AEDAS in generating the parametric models in the Digital project and CATIA-based tool during the design development phase, was retained in the construction phase in order to guarantee compatibility while achieving the highest degree of standardization integration during construction.
The outcome of parametric modeling and analysis was integrated into one BIM model, which was the main red thread across the project unifying and integrating both the design and constructions teams. The construction phase had an almost identical as-built drawing compared to the design development drawings.
The coordination of work among various contractors, manufactures, and suppliers in a seamless way with minimal class detection was BIM’s cause of success.
4. Based on the BIM model and seamless exchange of information, the team collaboration in this project was outstanding during the design and construction phase. Architects and engineers stood behind the project in an iterative design approach as one integrated design team.
Global collaboration for the design, manufacturing, assembling, and erection of the adaptive facade was remarkable. The facade was designed in London, the design assist was undertaken in Basel, Nantes, and Shenyang, the manufacturing was carried out in Shenyang and Guangzhou, and finally the assembly and completion took place in Abu Dhabi.
5. The design assist was another reason for the project’s success. Indeed as indicated by Mac’s Matthew Brett, the facade system was the greatest risk in the construction. Therefore, engaging the construction industry as early as possible was a crucial step resulting in a rigorous testing program.
The testing allowed the assessment of prototypes and full-scale models as mapped in Figure 6. On the negative side of the learned lessons, there are four major issues related to the Al Bahr project that should be avoided in future by clients and design teams:
6. The project has little to do with sustainability and occupant satisfaction. From the beginning, the client had defined a concise design brief with one focus mainly: Dazzle. The brief stated explicitly the will of the client to build an iconic building with highest quality materials, finishes, and architectural features.
The exterior of the building should have made it a landmark. Even the project principal architect stated the same.(19) The desire for signature buildings by powerful clients in the UAE alters the focus from energy-efficient and green architecture toward iconic signature buildings most of the time.
The two towers embed an ill-contradiction where a curtain wall in Abu Dhabi is protected by a complex electronic and mechanical technology. A root cause analysis will reveal an ill-design and ill-logic behind this project. Even calling the project Islamic or inspired by Islamic architecture makes no sense.
According to Fiqh or Islamic jurisprudence of priorities, it is not acceptable to create a problem; in this case, a glass facade in the desert is created and then they have tried to succeed in solving it. The Department of Municipal affairs in Abu Dhabi had already recommended to limit the glass surface to 30% (window-to-wall ratio) of the building facade. This is one of the reasons why the building failed to obtain the LEED certificate.(20)
7. The Design Bid Build process and contract were not suitable for such a sophisticated project. The project would have been delivered much more smoothly and at a lower cost if the contractor had collaborated on the side of the design team from the beginning.
The buildability control of the movement both mechanically and electrically was left at the last moment to be shouldered by the subcontractor for commanding advanced orders.
The wisdom and experience of the project management firm and the use of BIM models allowed the team to engage the construction contractor at the earliest with opportunities to validate the design concept. However, a Design-Build project delivery process would be more suitable for such a project.
8. The commissioning was another issue that was underestimated in this project. Although a dynamic mashrabiya system on this scale is without precedent, similar systems should have been commissioned by a third party and not the facade subcontractor.
Despite the advanced design assist phase, the development of performance specifications, and the strict quality checks of Yuanda, all the installation of wiring and mechanical components including the actuators, slides, tension rods, and mobile tripods required independent testing and calibration.
One of the key challenges through the whole process stage is the underestimation of what it takes to design and construct a structure that is as unique as these dynamic screen facades.
People do not have manufacturing and high-tech production background and appreciation, and the AEC industry lacks protocols and standards for seamless commissioning.
9. Also, the client did not take the soft-landing process and post-occupancy evaluation seriously. There was an underestimation of the complexity of the facade and the importance of validating its performance and assessment of its impact of indoor environmental quality and occupant satisfaction.
Almost every piece of the mashrabiya was not like the other, requiring sufficient time for system calibration. Even the suggested operation schedules for the mashrabiya and its automated control setting required extra attention to create a satisfying environment to meet the occupant needs inside the tower.
The fact that there was no individual control of the mashrabiya remains the most annoying feature for the occupants, as discussed in Section 4.4.
Finally, it should be noted that the use of an adaptive facade in this project was meaningless from a sustainability point of view. The construction cost of Al Bahr Towers in Abu Dhabi was e390 million; it was not commissioned by a third party and the commissioning process and soft-landing were underpaid and had misrepresenting professionals.
The use of mashrabiya in the Al Bahr project led to missing the huge opportunity to promote adaptive shading systems as a sustainable technology. The client did not consider energy consumption or occupant satisfaction from the beginning and therefore, the mashrabiya lost its meaning as a sustainable element while acting on the side of being a gadget.
On the other hand, the design team revealed the difficulty of integrating adaptive facade technologies. Adaptive Facades require much more effort to standardize and quantify the performance of adaptive facades and their evaluation process and protocols in order to increase their use in future buildings.(25)
Competing interests
I declare that I have no significant competing financial, professional or personal interests that might have influenced the performance or presentation of the work described in this manuscript.
Acknowledgements
The author is grateful to Fabio Favoino, Abdulmajid Karanouh, Peter Osborn, Esraa Elgezery, Matthew Brett, Alain Anthony, Ian Inglis, and all anonymous interviewees for their valuable comments and feedback.
The author would like to gratefully acknowledge COST Action TU1403 “Adaptive Facades Network” for providing excellent research networking. The author acknowledges the support of Workgroup 3 members.
REFERENCES
[1] Annunziata E, Frey M, Rizzi F. Towards nearly zero-energy buildings: The state-of-art of national regulations in Europe. Energy. 2013;57:125–133.
[2] Luible A, Memorandum of understanding for the implementation of a European Concerted Research Action designated as COST Action TU1403: Adaptive Facades Network. COST Action TU1403; 2014. Available from: http://w3.cost.eu/fileadmin/domain_files/TUD/Action_TU1403/mou/TU1403-e.pdf
[3] Loonen R, Trcˇka M, Co´stola D, Hensen JLM. Climate adaptive building shells: State-of-the-art and future challenges. Renew Sustain Energy Rev. 2013;25:483–493.
[4] Loonen R, Climate adaptive building shells; 2013. Available from: http://pinterest.com/CABSoverview/
[5] Attia S, Bashandy H. Evaluation of adaptive facades: The case study of AGC headquarter in Belgium. In: Belis J, Louter C, eds. Challenging Glass 5. Conference on Architectural and Structural Applications of Glass. Ghent, Belgium: Ghent University; ISBN 978-90-825-2680-6 2016.
[6] Boake TM. Hot climate double facades: Avoiding solar gain. Facade Tectonics. 2014;14:2–24.
[7] Karanouh A, Kerber E. Innovations in dynamic architecture. J Facade Des Eng. 2015;3:185–221.
[8] Luible A, COST Action TU1403 – Adaptive facades network. 12th Conference on Advanced Building Skins, 2–3 October 2017, Bern, Switzerland 2015:1226– 1233.
[9] Attia S, Favoino F, Loonen R, Petrovski A, Monge-Barrio A. Adaptive fac¸ades system assessment: An initial review. Adv Build Skins. 2015a;1226– 1233 (Economic Forum, 2015).
[10] Samyn P, De Coninck J, AGC Glass Building, 2014a, E´ditions Racine, Brussels, Belgium, ISBN 978-2-87386-882-6.
[11] Wurm J. Developing bio-responsive fac¸ades: BIQ House – The first pilot project. Arup J. 2013;90–95.
[12] Cilento K, Al Bahar Towers Responsive Facade/Aedas; 2013. Retrieved 13 January 2014.
[13] Linn C. Kinetic Architecture: Design for Active Envelopes. Shanghai: Images Publishing; 2014.
[14] Oborn P. Al Bahr Towers: The Abu Dhabi Investment Council Headquarters. Hoboken, NJ: John Wiley & Sons; 2013.
[15] Wood A. Best Tall Buildings: The 2010 CTBUH Reference Guide. New York, NY: Routledge; 2013.
[16] CWCT. 2006, Standard for systemised building envelopes. Available from: http://www.cwct.co.uk/publications/list. htm#cont26 [Accessed 2016 July 30].
[17] ANSI/ASHRAE, ANSI/ASHRAE Standard 55-2010: Thermal environmental conditions for human occupancy. American Society of Heating, Refrigerating and Air-Conditioning Engineers, Atlanta, 2010. Page 11 of 12 Attia. QScience Connect 2017:6
[18] AIA. Integrated Project Delivery: A Guide. Sacramento, CA: American Institute of Architects, California Council; 2007.
[19] Al Bustani H. 2014, UAE sustainable skyscrapers: Understanding Abu Dhabi’s Al Bahar Towers, the National AE, Available from: http://www.thenational.ae/business/industry-insights/property/uae-sustainable-skyscrapers-understanding-abu-dhabis-al-bahar-towers [Accessed 2016 March 21].
[20] DMA. The Code Handbook: Abu Dhabi International Building Codes. Abu Dhabi: Department of Municipal Affairs; 2012.
[21] Armstrong A, Buffoni G, Eames D, James R, Lang L, Lyle J, et al. The Al Bahar Towers: Multidisciplinary design for Middle East high-rise. Arup J. 2013;2:90–95.
[22] Attia S, Bashandy H. Evaluation of Adaptive Facades: AGC Building a Case Study of an Automated Glass Facade. Interviews and process mapping of the design team. 12. Lie`ge, Belgium: SBD Lab, Universite´ de Lie`ge; Available from: http://www.sbd.ulg.ac.be/research/Files/AGC%20Report%20v1.pdf 2015b.
[23] Causone F, et al., Experimental facilities for adaptive fac¸ades characterization. Adv Build Skins. 2015;1244–1252, (Economic Forum, 2015).
[24] CBE – Center for the Built Environment (s.d), Available from: http://www.cbe.berkeley.edu/aboutus/index.htm [Accessed 2016 April 23].
[25] Struck C, Almeida M, Silva S, Mateus R, Lemarchand P. Adaptive facade systems – Review of performance requirements, design approaches, use cases and market needs. Adv Build Skins. 2015;1254– 1262, (Economic Forum, 2015).
Comments
By enhancing the comfort of buildings for tenants, adaptive facades can offer revolutionary improvements in energy efficiency and renewable energy utilization.