At the forthcoming glasstec 2016, however, the industry will prove the opposite: further savings are to be expected through innovative approaches for automation, smart networking of production machines and value-creation stages as well as through new handling devices. This means that the glass industry should be well geared up for international competition.
The glass industry is under massive pressure. On the one hand, globalisation enables producers, processers and suppliers of manufacturing technology to gain a global foothold and serve international markets. On the other hand, in the wake of globalisation price-aggressive Chinese companies are heading to Europe with inexpensive products to conquer local markets.
In photovoltaics, as an important customer of flat glass, the Chinese have already taken the lead in this cut-throat competition – only very few German producers of solar modules have survived the price war with Asian competitors. The technology leadership of the German solar industry is no longer a given.
Things are also likely to become difficult for the glass industry – especially for enterprises that do not have a foothold abroad and are dependent on the German market. This is the case with many insulating glass producers whose business is largely regional in the vicinity of their manufacturing sites.
They not only have to give China and low-price competitors from Eastern Europe as good as they get in technical terms and pricewise, they also face dwindling demand on the domestic market. After all, the impact of this price battle is also seen at the end of the value chain where window makers are forced out of business ever more often because they can no longer cover their costs.
Nevertheless, experts are convinced that the German glass industry will be able to sustain its technology leadership long-term. “The glass industry can ward off cheap imports by undertaking continued quality efforts,” says Johann Overath, General Manager of the Federal Association of the German Glass Industry (Bundesverband Glasindustrie e.V.). Quality made in Germany, he adds, continues to be in demand especially for highly specialised applications.
At the same time, duties on imports from non-EU states could also be suitable instruments for individual products in order to counter cheap imports. The big questions is: how can technology leadership and quality stand their ground in the face of rising cost pressure?

Still room for innovations
The good news is: the innovation and cost-cutting potential in glass production and handling is far from being fully exploited. Many steps in production and processing such as sorting sheets after insulating glass production are still manual today.
This slows down material flows and costs time. Appropriate automation as well as integration and smart networking of processes could achieve a more balanced production flow at a higher speed – thereby saving costs.
In this context Industry 4.0, i.e. the digital networking of the individual value chain stages starting with production, could provide an important approach. The opportunity: by making machines and work pieces communicate directly with each other via special interfaces, products could be manufactured more individually, faster and at a lower price, says Linus Schleupner, Professor of Economics at the Rhenish University of Applied Sciences in Cologne.
“Digitisation enables quantum leaps in production efficiency.” And not only there: thanks to smart networking with customer insights and market intelligence companies can capture shoppers’ behaviour precisely and optimise their product ranges accordingly.
The result, he explains, are portfolios that are perfectly geared to customer needs. Furthermore, the close networking with customers as well as with upstream and downstream stages of production could help handling jobs faster. “Time optimisation is a huge asset and means a crucial competitive edge,” adds Schleupner.
He admits that Industry 4.0 has caused some confusion in medium-sized businesses because there is uncertainty as to the costs associated with implementation. But the economic expert reassures that the investment for Industry 4.0 is manageable.
“It primarily takes interfaces and software for linking and data evaluation rather than new machinery. The true challenge for companies is to reflect on what they want to achieve with Industry 4.0 beforehand, and how they have to adjust their processes accordingly. How are the individual value creation stages and production partners to be linked with each other?” asks Schleupner.
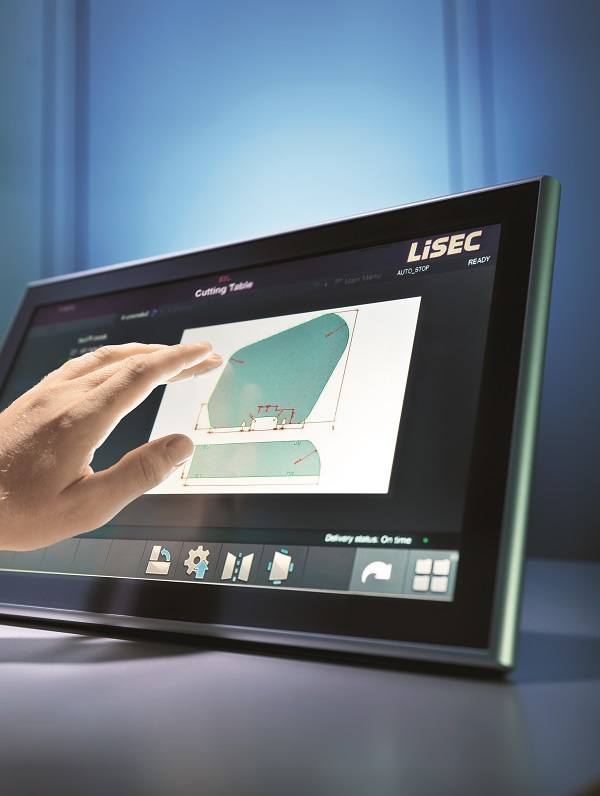
Intelligence rather than new machines
With their cooperation French machinery producer Tecauma and German software supplier A+W have already suggested that intelligence can also benefit the end of the value creation chain – window making.
So far, automatic glazing has required a so-called glass buffer into which the individual sheets were introduced manually for each job after being picked from the insulating glass line. Now the two companies have jointly developed a concept that does without glass buffers and permits glazing via robots right from the transport rack.
This was made possible by the special A+W Rack Optimizer software. With the help of this software the insulating glass producer’s output is controlled by the window maker’s specifications: the glazing units can be packaged at the end of the line in exactly the order specified by the window maker – which means manual sorting into the interim buffer is rendered superfluous.
The packaging robot at the end of the line also receives the data from the A+W Rack Optimizer via an interface. It places the panes on the transport rack in the reverse picking order of the window maker. The glazing robot of the glazing unit producer is also linked with the insulating line and the packaging robot of the insulating manufacturer. It permanently exchanges production data with the other machines via the interface.
In the event of unforeseen changes in the job order, caused by glass breakage or short-term job changes, for example, the machines adapt to the new requirements in a coordinated manner.
This means automatic production continues without interruptions and that efficiency increases. This example shows: the real drivers of Industry 4.0 are intelligent interfaces between manufacturer and client rather than novel machines.
Other leading glass industry players such as Lisec from Austria, a solutions provider for flat glass processing and finishing, also want to focus more on digitisation. “Industry 4.0 makes for transparent and efficient production processes in the glass processing and finishing industries,” says Hannes Pils, Business Unit Manager at Software Lisec.
The consistent networking from quote generation to delivery optimises production processes and enables gapless product tracking plus consistent quality reporting, which can double as quality check for specific jobs.
Lisec sees another positive effect of 4.0: learning and self-optimising production machines and lines could in future decide autonomously about the tools and machine settings to be used thereby increasing efficiency. And last but not least, permanent and consistent plant monitoring by means of built-in sensors and assistance systems enables predictive and preventive maintenance and repair. These in turn help to prevent unplanned stoppages thereby increasing plant availability.
“Even service jobs and the required spare parts can be planned and organised in an automated way,” rejoices Pils. At glasstec 2016 held in Düsseldorf from 20 – 23 September 2016 the expert audience can form a concrete picture of what Lisec has in store for 4.0. “We will exhibit integrated complete solutions for optimising production and will present our take on Industry 4.0 for flat glass processors.”
The experts at Bystronic glass, suppliers of manufacturing equipment and complete insulating glass lines, see similar advantages in digitisation. “As a machine builder we do see opportunities in Industry 4.0,” says Bystronic Product Manager Tobias Neff and adds that today’s glass production already embraces some 4.0 elements.
He explains that work pieces are triggered by individual data that permit tracking all the way from manufacturing to delivery and even confirm a “successful production complete” to customers.
In future, he goes on to explain, Bystronic lines could be equipped with additional software that allows customers to specify the precise sorting order for sheets. “The link between the line and window makers is a key aspect for us,” remarks Neff.
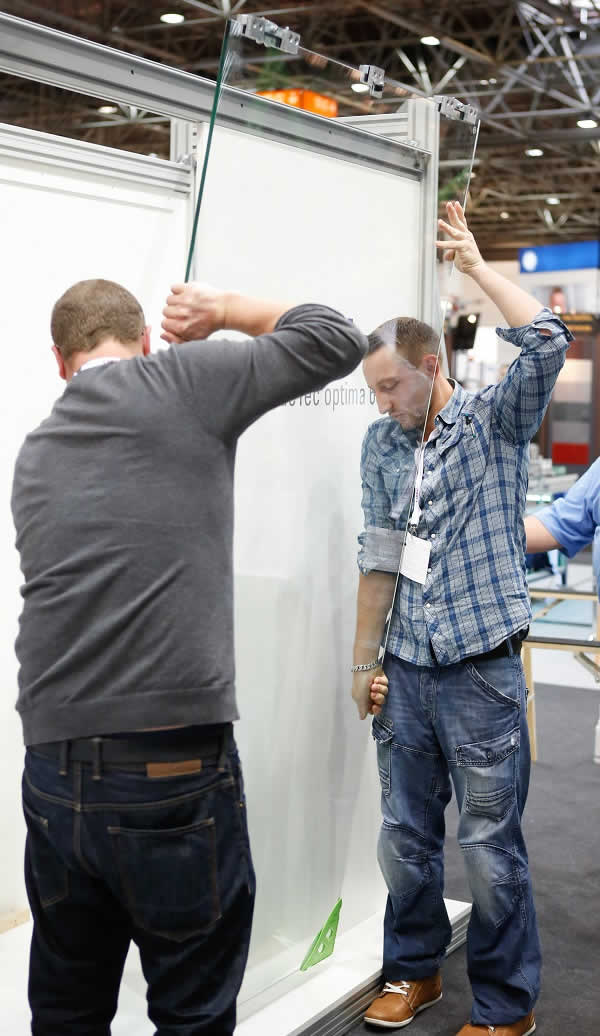
Robots do not always help
Bystronic’s cooperation partner Hegla, a solutions provider for flat glass production, has also made automation the highest priority for some time now. The sorting system Sortjet and the dynamic residual plate storage Remaster have already laid the foundation for applying the 4.0 strategy to further developments in flat glass processing, says General Manager Manfred Vollbracht, and adds that customer-oriented networking and communication potential to complete the 4.0 strategy rank high in Hegla’s current development projects.
Vollbracht also points out that automation and digitisation in glass finishing are not always the panacea for higher efficiency. Automatic edge deletion and system-controlled PVB trimming tools were pioneering solutions when introduced to the market, he says. Before their introduction the production process had to be interrupted so that operators could perform these jobs manually – while now these process steps are in-line, forming part of glass cutting.
“The success of these solutions can also be attributed to the fact that no elaborate, multi-axis robots had to be installed for this but the existing controls, drive technology and sensors of the cutting system could be used,” explains Vollbracht. This means integration and the efficient use of existing equipment deliver more benefits than additional machinery.
And what about innovations for glass handling devices? Is there also still room for improvement when it comes to vacuum lifters, glass tongs and the like? Holger Schadwinkel of Wirth, a company specialising in solutions for industrial construction and material handling, explains that the potential for innovations in lifting devices for internal applications is low. “By using compressed air to generate a vacuum and a faster air supply for suction devices we already achieve very short cycle times today.”
This is unlike the devices for construction site applications. The demands made in architecture are rising: ever bigger, ever heavier, ever more convex, concave and even 3D curved sheets are in demand, Schadwinkel reports and adds: “This is why we now build devices nobody would have thought of five to six years ago in terms of load-bearing capacity and functions built into the devices.”
At glasstec 2016 in Düsseldorf, the world’s biggest and most international trade fair in the glass sector, companies can take a closer look at the innovations of all of these machinery producers and equipment providers and find out about the decisive trends from 20 to 23 September 2016.
Smart manufacturing technologies will not only be demonstrated hands-on by the exhibitors but also discussed by experts at the technical symposium of the special show “glass technology live” held on 21 September 2016 under the auspices of VDMA’s Forum Glass Technology. The expert audience is sure to see: there is still plenty of room for innovations in the glass sector.