This paper was first presented at GPD 2019 by Julia Endress and Viviana Nardini from Sika Services AG, Switzerland.
In the early days of the 1970s, Structural Sealant Glazing (SSG) technology was introduced in the U.S. to bond glass panels to metallic frames. Silicone adhesives were the only accepted bonding technology for this application due to the unique UV resistance and thermal stability they could offer, at that time. Considering that no options for controlling the UV radiation and temperature on the adhesive joint existed for façade design, the unique properties of silicone adhesives were essential.
Compared to the past decades from the ‘70s to the ‘90s, the facade industry has experienced extraordinary technological developments: Nowadays numerous solutions exist to control temperature as well as UV radiation on façade components and bondlines. Consequently, new criteria for selecting the best performing adhesives available in the market should be used. Beyond silicone technology for SSG applications the benefits of other adhesives technologies and the new market requirements should be considered.
In this paper the mechanical and application properties of Sikaflex®-268, a high performance polyurethane adhesive are presented and compared to Sikasil® SG-500, a typical silicone adhesive used for structural glazing applications in facades. All obtained results illustrate that Sikaflex®-268 outperforms Sikasil® SG-500 and makes it an ideal solution wherever high loads need to be transferred.
In blast scenarios, Sikaflex®-268 can introduce significant opportunities for reducing the SSG joint dimensions and optimizing systems. The PowerCure technology patented by Sika provides a combination of high flexibility for on-site bonding and reglazing with fast curing of the adhesive, widely independent of climate conditions. Furthermore, there are no limitations in terms of maximum joint dimensions in a single-step application with the boostered polyurethane technology.
1 Impact of façade technology evolution on Structural Sealant Glazing solutions
Early in the 1970s a new technology, Structural Sealant Glazing (SSG), was developed in the U.S. to bond glass panels to metal framing systems by use of an adhesive.
The success of such technology in the construction industry was already evident in the ‘80s and ‘90s: At least one third of the building curtain walls and windows installed in the U.S. used SSG systems, relying on the properties and adhesion performance of the adhesive to connect glass and frame without the need of using mechanical fasteners. Consequently, many activities started in order to develop standards regulating design, application and requirements of the new technology [1].
At that time, only a silicone adhesive was considered acceptable for structural glazing applications in facades due to its unique properties that no other technology could offer simultaneously:
• Thermal stability
Mechanical properties of silicones remain almost unchanged over a wide range of temperatures. Unlike other adhesive technologies, glass transition occurs at very low temperatures (usually lower than -50 °C), apart from service temperatures. Most structural silicones available on the market provide stable mechanical behavior within a temperature range from -40 °C up to +150 °C, covering typical service temperatures in façade systems.
• Very high weathering and UV resistance
Long life expectancy and durable adhesion on the interface between silicone joints and transparent substrates can be ensured, with no negative effects due to exposure to UV radiation and weathering impacts.
• Elasticity / Elongation capabilities
Elastic behavior of bonded connections is a key requirement in façade applications. Indeed, thermal movements are imposed to joints, which bond components of different size and material and which are subject to temperature variations; such movements need to be accommodated elastically, exploiting the adhesive elongation capabilities.
Considering the state of the art in façade systems available in the ‘70s, the unique properties offered by silicones were essential as other options for controlling the temperature of the adhesives joints and protecting them from UV radiation were nonexistent.
Nowadays, the scenario has completely changed: The façade industry has faced extraordinary developments and new advanced solutions, systems and tools are available for design and construction, which also provide opportunities to control temperatures and UV radiation on bondlines. In most façade applications, the following solutions are stateof-the-art:
• Insulating Glass (IG) units had replaced the use of monolithic and laminated glass panels. This helps significantly in reducing the temperatures on the bonded area between inner glass layers and inner metallic profiles. In addition, the secondary sealing joints of the IG units helps to protect the SSG joints from UV.
• Climate control systems allow managing indoor temperatures, with significant impact on temperature of façade elements where SSG bond lines are applied.
• Thermal break, e.g. polyamide bars, introduced into profiles and systems, can minimize the temperatures in bonded areas.
• Advanced technologies such as ceramic screen printing have been developed, providing a safe solution for the protection of bondlines from UV.
• Shadow systems and blinds are often integrated in façade elements to control temperature and radiation on the façade components and consequently of the adhesive joints as well.
• Specific PVB interlayers exist for controlling UV radiation; tinted interlayers are reducing heat gain from sunlight.
• Dedicated software has been developed and is used on a daily basis to evaluate a building`s physical performance and estimate temperatures on components with the target of minimizing extreme conditions.
• Many others (advanced coatings, etc.)
Considering all these factors, the technologies currently available within the façade industry prove that limiting the SSG applications to the silicone adhesives is outdated.
New solutions for SSG applications should be investigated in order to select the best performing adhesive technology available on the market depending on specific requirements (driven by systems, loads, design, production, boundary conditions, etc.) in an effort to gain greater benefits for the whole application.
2 Adhesive selection in blast scenarios
Figure 1 compares the mechanical behavior of different adhesive technologies, evaluating the tensile strength versus the elongation offered. Considering that elasticity and high elongation capabilities are a must to accommodate thermal movements occurring in façade components, two adhesive technologies can be selected for SSG applications:
• Silicones – offering a typical elongation at break in the range of approx. 50 – 400 % and a tensile strength in the range of approx. 0.5 – 4 MPa [2].
• Polyurethane adhesives – offering a typical elongation at break in the range of approx. 250 – 650 % and a tensile strength in the range of approx. 4 – 8 MPa [2].
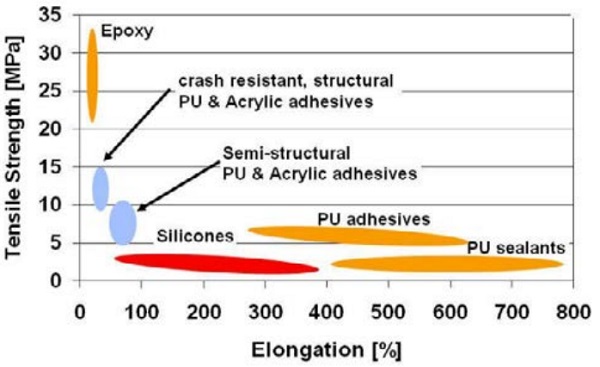
It is clear that whenever high loads need to be transferred by an SSG connection, the use of polyurethane technology can be beneficial in minimizing joint dimensions and optimizing system design.
In the following sections the behavior of two adhesives will be compared, with the target of identifying the most suitable one in terms of mechanical behavior offered for blast design. Sikasil® SG-500: a 2-component silicone adhesive ideal for structural glazing and widely used in the façade industry on a global scale and different climate regions.
Sikaflex®-268 PowerCure: a 1-component accelerated polyurethane adhesive designed for large component assembly and direct glazing applications in the rail and transportation industry, where it is widely used for structural bonding of windshields and windows to frames.
In their typical application fields, both Sikasil® SG-500 and Sikaflex®-268 PowerCure adhesives are commonly exposed to similar loads of equivalent magnitude:
- High temperatures
- Fatigue phenomena due to cycling loading
- UV radiation
- Aging of adhesive in service life
- High loads e.g. wind load, barrier loads, etc.
- Extreme impact loads
In the case of Sikasil® SG-500 these can be determined from blast loads or hurricanes.
In the case of Sikaflex®-268 PowerCure these can be identified in tensile/pressure waves and transient variations in air pressure caused e.g. by the passage of trains through tunnels and by aerodynamic interaction with other trains travelling in the opposite direction. Typically, windshield joints of high-speed trains must withstand sustained pressures of approx. 6.0 kPa when travelling, up to 15–20 kPa equivalent static pressure when entering into tunnel.
3 Mechanical behavior under standard test conditions
In the following sections the mechanical behavior of Sikaflex®-268 PowerCure and Sikasil® SG-500 were analyzed and compared.
3.1 Mechanical behavior at 23 °C / 50 % r.h.
Table 1 and Figures 2 and 3 summarize the lap-shear strength and shear strain at break for the adhesives tested after curing with a constant speed of 5 mm/min on singleoverlapped lap-shear specimens. The joint overlap, width and thickness were 12 ± 0.5 mm, 25 ± 0.1 mm and 6 ± 0.5 mm respectively. The speed of 5 mm/min was selected according to the test speed specified by [3] to evaluate the adhesives strengths under wind load.
The results show that the lap-shear strength of Sikaflex®-268 PowerCure is more than 3.4 times greater than Sikasil® SG-500, with a shear strain at maximum force over 2.6 times greater.
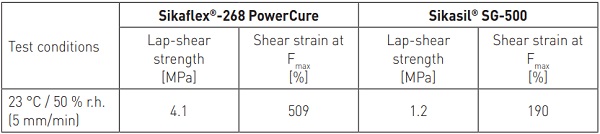
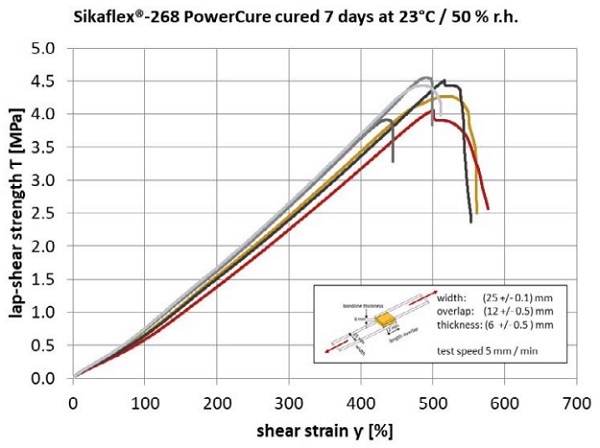
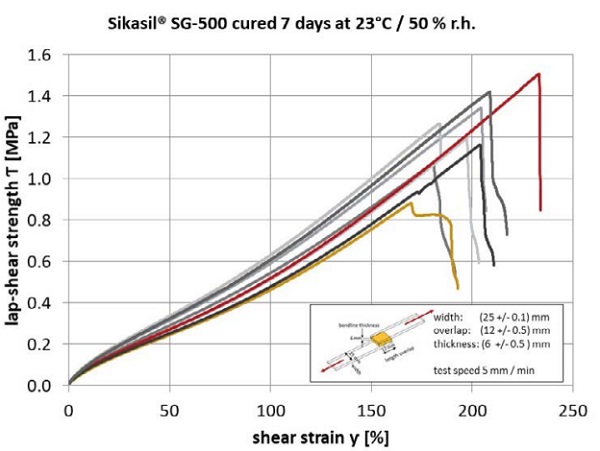
3.2 Mechanical behavior under fatigue
Figure 4 and Figure 5 show the reduction of lap-shear strength depending on the number of load cycles the adhesives were exposed to, based on Whöler tests defined in DIN 6701 [4]. Test results refer to a number of load cycles ranging from 103 to 107 and show that Sikaflex®-268 is more sensitive to fatigue than Sikasil® SG-500. Nevertheless, the strength offered by Sikaflex®-268 is consistently higher than that of Sikasil® SG-500 for all load cycle ranges.
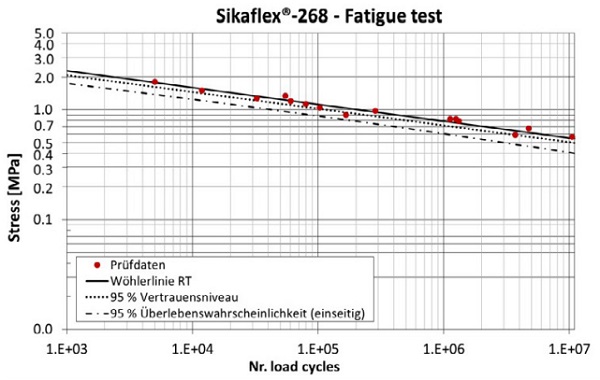
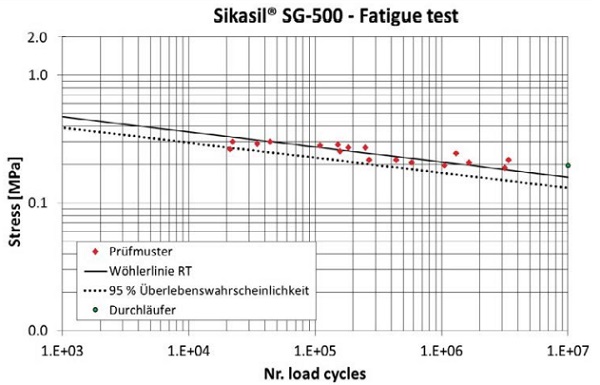
3.3 Mechanical behavior after accelerated aging
Sikaflex®-268 PowerCure and Sikasil® SG-500 are high-performance elastic adhesives designed for large component assembly and glazing applications. Both offer outstanding weathering resistance. In order to evaluate the impact of external effects during service life, the lap-shear strength was tested after accelerated aging. The accelerated aging conditions were: 7 days of curing at 23 °C / 50 % r.h., followed by 7 days of water immersion at 23 °C, 1 day of conditioning at 80 °C and finally 7 days of exposure to high temperature and high humidity (70 °C / 100 % r.h.). After the accelerated aging, the tests were performed at 23 °C and 80 °C at a speed of 5 mm/min. Table 2 summarizes the results obtained.
The mechanical values of Sikaflex®-268 PowerCure are more sensitive to accelerated aging and high temperatures compared to Sikasil® SG-500. However, the lap-shear strength offered by Sikaflex®-268 PowerCure is more than double the strength of Sikasil® SG-500.
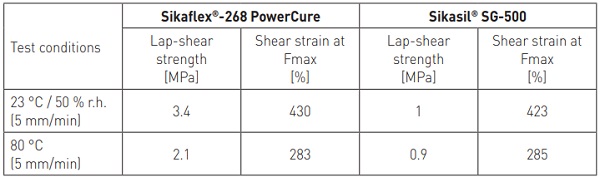
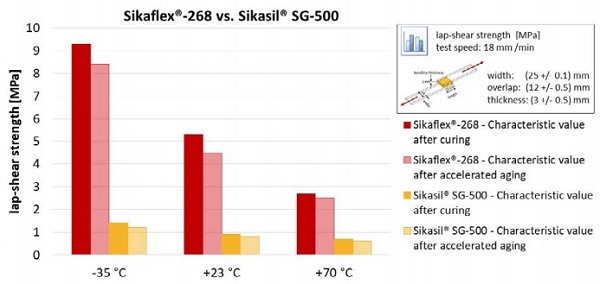
3.4 Mechanical behavior at different temperatures
The lap-shear strength of Sikaflex®-268 and Sikasil® SG-500 were determined with a constant test speed of 18 mm/min at -35 °C, 23 °C and 70 °C, after curing and after accelerated aging (described in section 3.3). In accordance with DIN 6701-3 [4] the specimen geometry of overlap of 12 mm, width of 25 mm and adhesive thickness of 3 mm was used. Figure 6 summarizes results and confirms the outstanding mechanical performance of Sikaflex®-268. The strength offered by Sikaflex®-268 at 70 °C is more than 3 times greater compared to the strength offered by Sikasil® SG-500 at 23 °C.
The glass transition temperature of Sikaflex®-268 is approx. -57 °C (API [5]).
In general, test speed and geometrical factors (overlap / adhesive thickness) influence the results obtained on lap-shear specimens and need to be considered when the mechanical behavior of elastic adhesives are compared. Lap-shear values of elastic adhesive show lower strength with increased joint thickness, whereas higher test speeds usually result in higher lap-shear strength. Therefore, a direct comparison of the results provided in sections 3.4, 3.1 and 3.3 might be difficult due to the different test speeds and adhesive thicknesses used.
4 Mechanical behavior at high test speeds
Section 3 highlights that Sikaflex®-268 offers outstanding mechanical performance compared to Sikasil® SG-500. The higher strength and elongation makes Sikaflex®-268 an ideal adhesive solution for systems where high loads need to be transferred. With reference to the demands in blast scenarios, the lap-shear properties of Sikaflex®-268 and Sikasil® SG-500 were investigated by testing at high speeds of 1 m/s, 3 m/s and 5 m/s. The tests were carried out on lap-shear specimens with an overlap of approx. 12 mm and joint width and thickness of approx. 25 mm and 6 mm respectively.
4.1 Mechanical behavior at high speeds at 23 °C / 50 % r.h
Results are provided in Table 3
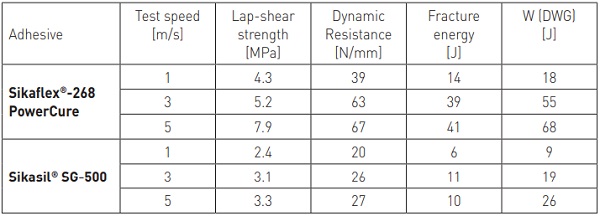
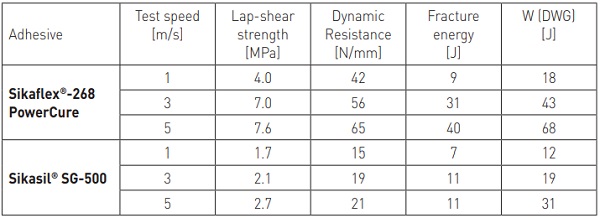
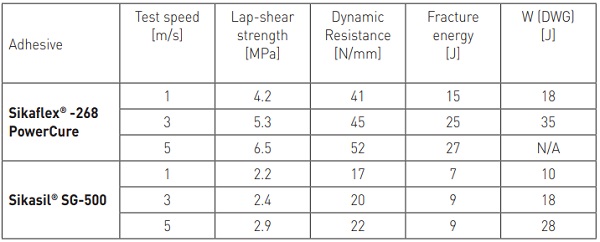
4.2 Mechanical behavior at high speeds after accelerated aging
In order to compare the adhesives performance after accelerated aging, the high-speed lap-shear tests were conducted after the conditioning described in section 3.3.
4.3 Mechanical behavior at high speeds after accelerated aging and testing at 80 °C
The mechanical strength of Sikaflex®-268 PowerCure is temperature dependent; as highlighted in Section 3.3, the higher the temperature, the lower the strength offered. In order to investigate this behavior at highspeed conditions, Sikaflex®-268 PowerCure and Sikasil® SG-500 were tested at 80 °C (specimen temperature) after the same accelerated aging outlined in section 4.2.
Figure 7 summarizes the obtained results of lap-shear strength and fracture energy at high speeds.
For all test conditions, the strength and fracture energy of Sikaflex®-268 PowerCure is always consistently higher than that of Sikasil® SG-500, being always at least double. The strength offered by Sikaflex®-268 PowerCure under the most unfavorable conditions is always higher than the strength offered by Sikasil® SG-500 in its most favorable condition.
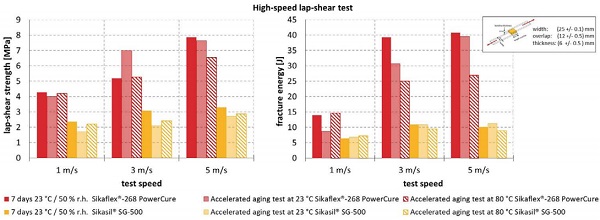
5 UV resistance
The most relevant benefit offered by silicone adhesive is the undiscussed resistance to UV light. That means a durable adhesion can be expected over service-life when a transparent glass substrate is bonded to a frame and the adhesive joint is permanently exposed to natural light and UV radiation passing through the glass.
Polyurethane adhesives are usually more sensitive to UV radiation, which can impair joint adhesion performance in the long-term. Despite that, well-known strategies, design rules and protective measures exist today to overcome this. Tests and experience gained from the rail and transportation industries teach us that the most common ways to overcome the obstacle of bonding transparent or translucent substrates with polyurethane adhesives are (as alternative options):
• Using a proper UV-opaque ceramic screen printing. The application of such a ceramic printing can be limited to the precise glass perimeter area where the adhesive joint is applied. Especially for bonding of insulating glass units to metallic frames, the design impact of a ceramic print is limited. Indeed, any screen printed area along the perimeter can be usually hidden by the spacer and the secondary sealing.
• Using proper caps to protect the bonded area. This solution is quite often implemented in blast design to retain the glass units and allow the joints to work only in shear.
• Using other UV-radiation reduction elements as UV-absorbing interlayers, system configurations, etc.
6 Application benefits offered by Sikaflex®-268 PowerCure for blast design
Sikaflex®-268 is a 1-component polyurethane which cures (as 1-component silicones) under exposure to atmospheric moisture forming a durable elastomer. This curing process is dependent on the atmospheric conditions and limits the speed of production due to slow curing reactions. To overcome this limitation, accelerated curing options were developed for Sikaflex®-268 and are permanently in use.
• Sikaflex®-268 can be applied by pump equipment in combination with SikaBooster®-20 S, so that adhesive cures fast by reaction with the moisture provided by the booster system. The curing process is largely independent from the atmospheric moisture.
• Sikaflex®-268 PowerCure: This patented technology consists of the on 1-component Sikaflex®-268 adhesive, boostered with an accelerator paste while extruding it with a professional electric dispenser (PowerCure Dispenser). The integration of the booster ensures fast curing, largely independent of the atmospheric moisture. The handy dispenser compared with the curing properties is the ideal solution for onsite applications and reglazing.
Six hours after the boostered adhesives application, more than 50 % of the final strength can be achieved.
Unlike a 1-component polyurethane and a 1-component or 2-components silicones, no restrictions of maximum joint dimensions exist for a one-step application if a boostered versions of Sikaflex®-268 is used. This ensures high flexibility in terms of system design as well as application feasibility, confirming the adhesive potential for design in blast scenarios where big joints are usually required.
7 Conclusions
In the façade industry, silicone adhesives are commonly used to structurally bond glass and opaque panels to metallic frames. Nevertheless, polyurethane technology can open opportunities for new adhesive solutions where higher strength in combination with high elongation is required. Consistent experience and design standards for use of polyurethane technology exist in industry fields (e.g. rail industry) other than facades, where demands in terms of substrate types, weathering exposure and loading are similar.
In this context, properties and mechanical performance of Sikaflex®-268 polyurethane adhesive have been analyzed and compared with those of Sikasil® SG-500, a typical silicone adhesive used for structural glazing in facades. Tests carried out at different temperatures after curing and after aging prove that the mechanical strength of Sikaflex®-268 is always consistently higher than Sikasil® SG-500. This opens opportunities for optimizing joint dimensions, improving design safety levels and increasing feasibility for systems exposed to high loads.
Especially in blast scenarios, polyurethane technology shows great potential. At high testing speeds Sikaflex®-268 confirms a lap-shear strength much higher than Sikasil® SG-500 (factor dependent on joint thickness, test speed and boundary conditions). In addition, Sikaflex®-268 adhesive is available in boostered version not only for pump equipment but also for application by electrical dispenser, offering two major benefits on façade applications: a) fast curing not only for factory production but also for site applications and/or reglazing b) no limits in maximum joint dimensions, which confirms the value of Sikaflex®-268 in blast scenarios where bigger joints are usually required.
In the ‘70s, silicones were selected among adhesive technologies for their unique UV resistance and thermal stability as the right solution for SSG bonding, based on the level of development of façade systems of that time; indeed, limited options for temperature control and UV radiation protection existed. Nowadays, advanced criteria and technologies for designing and building façade components are available to control their impacts. Therefore, the best performing adhesives should be selected among different technologies, to exploit benefits they can offer based on actual system and design needs.
8 References
[1] ASTM C 1401, Standard Guide for Structural Sealant Glazing
[2] ISO 527-2, Plastics – Determination of tensile properties – Part 2: Test conditions for molding and extrusion plastics, 2012
[3] EOTA ETAG 002-1, Guideline for European Technical Approval for Structural Sealant Glazing Kits (SSGK) – Part 1: Supported and Unsupported Systems, 2012
[4] DIN 6701 – Adhesive bonding of railway vehicles and parts – Part 3: Guideline for construction design and verification of bonds on railway vehicles, 2014
[5] API Sikaflex®-268: Chemical and mechanical properties according DIN 6701-3, 2015