Authors: Faidra Oikonomopoulou & Telesilla Bristogianni
Source: Glass Structures & Engineering | https://doi.org/10.1007/s40940-022-00178-w
This article will be presented at the Challenging Glass Conference 8 – June 2022 – Ghent – Organisers: Jan Belis, Freek Bos & Christian Louter
Abstract
Cast glass is a promising, three-dimensional expression of the material for architectural and structural applications, particularly for the creation of all-transparent, self-supporting structures and envelopes. Typically applied in the form of solid blocks, cast glass components can be used as repetitive units to comprise fully-transparent, cast glass masonry walls. To maximize transparency and ensure an even load distribution, the glass blocks are bonded together by a colourless adhesive. Currently, there is a lack of standardized structural specifications, strength data and building guidelines for such adhesively-bonded cast glass-block systems.
As a result, any new application is accompanied by experimental testing to select the adhesive and certify the adhesively bonded system. Since the choice of adhesive is highly dependent on the prerequisites set for each case-study -such as the structural and visual performance, available budget, the structure’s geometry and climate conditions- the preselection of the most prominent adhesive family at an early project stage can prevent an excessive budget and construction complications.
This paper, therefore, aims to shed light on the selection process of adhesives for cast glass assemblies by first providing an overview of the most suitable bonding media families for such systems; these include stiff adhesives, flexible adhesives and cement-based mortars. Following, the paper reviews the research & development process of the adhesively-bonded glass-block systems in three distinct built projects, in which the TU Delft team has been involved: The Crystal Houses façade (NL), the LightVault, a robotically assembled glass vault (UK) and the Qaammat pavilion in the arctic circle (GL). The adhesive requirements for each of the three case studies are discussed in terms of structural and visual performance and ease-of-assembly (constructability).
These criteria are decisive in pointing out the most promising bonding media family per case-study. The final shortlist of adhesive candidates within that bonding media family is subject to the full list of performance criteria, but also to market availability. The shortlist of adhesive candidates are typically experimentally evaluated, first via application testing and then via strength tests in order to choose the most suitable candidate. Based on the above, the review concludes in proposing guidelines for the effective selection, design and experimental verification of adhesively-bonded cast glass assemblies.
Introduction
Solid cast glass components are a promising, alternative, three-dimensional expression of glass for structural and architectural applications in the built environment. Typically, in self-supporting applications, cast glass components are applied in the form of solid blocks, comparable in size to conventional terracotta bricks (Oikonomopoulou 2019). Combining transparency, durability and a considerable compressive strength, such components can be used as repetitive moduli for creating all-transparent, self-supporting envelopes and even entire structures. To avoid the use of a secondary substructure, the solid glass blocks are bonded together; towards maximized transparency, the bonding media can be a clear, transparent adhesive.
Yet, despite the large architectural and structural potential of adhesively-bonded solid glass brick systems, their application in the built environment remains very limited. This can be attributed to a lack of large-scale, automated and controlled production of architectural cast glass components, as well as to the absence of standardized structural specifications, strength data and building guidelines for both cast glass components1 and the corresponding adhesive application (Oikonomopoulou 2019). Indeed, no self-supporting structure consisting of adhesively-bonded solid glass bricks, follows a similar approach and materialization to another.
On the contrary, each realized case-study opts for a different bonding media, based on the respective prioritized performance criteria. Application testing of the bonding media is crucial for verifying the constructability of the system, whereas structural tests are necessary to validate the overall performance of the assembly; as, similarly to conventional masonry structures, it is not the individual strength of each element, but rather the degree of collaboration between glass blocks and bonding media into one structural unit that defines the structural capacity and behaviour of the system (Oikonomopoulou et al. 2017a).
Methodology
Aim of this paper is to shed light on the selection process and respective performance criteria for the bonding media for adhesively-bonded glass brick systems and the influence the pre- and final bonding media selection has to the design. Moreover, it aims to establish relevant guidelines for the bonding media selection and verification. First an overview of the most suitable bonding media families is provided, discussing their main properties in respect to the key performance criteria. Goal is to reveal the main advantages and limitations/implications of each discussed bonding media family for such applications.
Following, three distinct, realized adhesively-bonded glass brick structures are analysed in order to (i) elaborate further on the impact of the prioritized performance criteria to the pre- and final bonding media selection and (ii) discuss the experimental work (research and development) involved towards the realization of each respective case-study. The paper concludes in proposing guidelines for the effective selection and experimental testing of bonding media for adhesively-bonded cast glass assemblies.
Bonding media selection: main families and characteristics
This section presents an overview of the most promising bonding media families for adhesively-bonded glass brick structures. According to (O' Regan 2014; Wurm 2007) the most common adhesive families employed for structural glass connections are either (i) flexible, soft-elastic adhesives, which include silicones, polyurethanes and MS polymers or (ii) stiff adhesives, which include epoxies and acrylates. In this paper, the application of (iii) cement-based mortars and tile adhesives, typically employed in hollow glass brick structures, is also considered.
The key selection criteria of the bonding media for cast glass assemblies can be linked to the assembly’s (i) visual and (ii) structural performance, (iii) ease-of-assembly (constructability) and (iv) available budget. According to which performance aspect(s) is/are prioritized, an initial indication of the most suitable adhesive family can already be derived. The aforementioned criteria are comparatively assessed in terms of the main properties that are considered crucial for the initial indication of the most suitable adhesive family, such as: transparency in terms of visual performance; bond (shear) strength, resistance to creep, elongation to failure and service temperature in terms of structural performance; gap filing capability in terms of ease-of-assembly; and need of post-processing of the glass components in terms of budget, which can greatly influence the associated manufacturing costs and production time of the glass components (Oikonomopoulou 2019).
The full list of performance criteria for the final adhesive selection is considerably more detailed, including for example UV-resistance, resistance to aging and weathering, avoidance of toxic or poisonous emissions, processing properties (e.g. viscosity, curing conditions, surface preparation), low shrinkage, etc.; properties that can be highly variable within each bonding media family and subject to the final chosen adhesive
Flexible adhesives: silicones, MS Polymers and polyurethanes
Flexible adhesives typically present an elongation at break > 150% (Wurm 2007) and a gap filling capability of at least 2–5 mm – thicker bondlines, up to 10 mm are also possible. The latter enables the adhesive to accommodate possible discrepancies in the size and surface quality of the bricks, sparing the necessity and associated costs of mechanically post-processing their finishing surface (Oikonomopoulou 2019) and allowing for a relatively easy assembly. The adequately thick bondline and flexible nature of such adhesives can compensate for stresses in the construction, as in the case of thermal stresses originating from the different thermal expansions of the joining materials (Banea and Silva, 2009).
In terms of structural performance, flexible adhesives typically exhibit a shear strength in excess of 1 MPa2 (Wurm 2007), although the exact value is highly susceptible to the type of test performed, the overlap length and bondline thickness of the specimens,3 as well as to temperature variations (Banea and Silva, 2009). Flexible adhesives generally behave well against dynamic loads and present a considerably higher short-term strength compared to their long-term strength, which can be compromised due to their tendency to creep.
They can also present an excellent resistance within a broad temperature range, which makes them ideal for applications in extreme climate conditions (Fig.1)—this includes aerospace applications as well, where the adhesive has to withstand very high temperatures, typically > 200˚C.4 An example of an adhesively-bonded cast glass structure using a flexible adhesive solution is the Qwalala Scupture in Venice (IT): the 2.4 m high, 75 m long and 70 t in weight curved glass brick wall was bonded using Dowsil™ 993 Structural Glazing Sealant, a two-component, white in colour, structural silicone of high UV-resistance, 0.95 MPa tensile strength and 7 mm layer thickness (Hautekeer,Dow Group 2018).
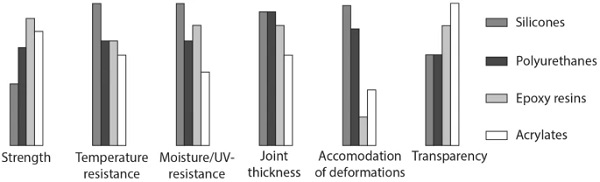
Flexible adhesive families include both mono-component and two-component adhesives. The former set in contact with the air while the latter as a result of a reaction between the two components (O' Regan 2014). The use of mono-component moisture/heat-activated adhesives for adhesively-bonded glass block assemblies is not recommended. This type of cure chemistry requires a favorable water vapor pressure in the atmosphere, which is a function of both temperature and humidity that has to be highly regulated (Hayez et al. 2021).
Therefore, this chemical hardening mechanism, subject to an external, natural, energy source, is not suitable for wide joints, typical in adhesively-bonded cast glass systems. Such adhesives cure from outside to inside at a relatively slow rate (a few mm/day); thus, increased width impedes the necessary penetration of moisture from the interface to distant parts of the adhesive; for this reason (Bedon and Santarsiero, 2018) suggest a maximum depth to thickness ratio of 1:2 – 1:3 for flexible adhesives. Shear tests performed at TU Delft on specimens of solid glass components bonded by a mono-component silicone of the Simpseal series at a 130 mm × 157.5 mm surface have confirmed the above (Fig. 2, left).
The specimens were left to cure for a month at room temperature and humidity conditions prior to testing. It was evident from the failure mode that only an approx. 15–20 mm thick peripheral zone of the adhesive had completely hardened, as suggested by the cohesive failure in that area. The inner zone of the bond exhibited an adhesive failure and was still soft upon contact, indicating that is was still not-hardened/insufficiently cured (Fig. 2, right). Moreover, as the adhesive solidifies and shrinks externally, pulling forces can be formed, sufficient to tear the still soft, uncured adhesive at the bond’s interior; potentially resulting in visible cracks within the bond layer.
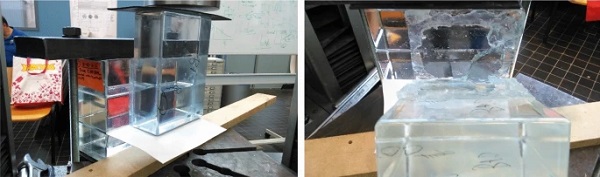
Stiff adhesives: epoxies and acrylates
Epoxies and acrylates exhibit, by a considerable margin, the highest strength among the adhesive families typically used in structural glass applications (see Fig. 1). They typically present low elongation at break, leading to a sudden, brittle failure. Failure is usually shown as plucking of the glass component as the bond is usually stronger than the glass; as demonstrated by 4-point testing on adhesively-bonded glass brick beams by (Oikonomopoulou et al. 2015b; Oikonomopoulou 2019) Combining high strength with the possibility of maximized transparency, stiff adhesives have been traditionally preferred for adhesively-bonded cast glass applications, namely in the Atocha Memorial (Paech and Göppert, 2008; Schober et al. 2007), Crystal Houses (Oikonomopoulou et al. 2015b, 2017a) and LightVault (Parascho et al. 2020).
Nonetheless, the high bond strength of such adhesives, which also ensures a good composite action and creep resistance (O' Regan 2014), can only be guaranteed when they are applied at their optimum bond thickness. This typically ranges between 0.1 and 1.0 mm. According to (O' Regan 2014) variations in the thickness of such stiff adhesives may result in stress concentrations. Furthermore, experimental work by (den Ouden 2009; Riewoldt 2014; Grant et al. 2009; da Silva et al. 2006; Crocombe 1989; Oikonomopoulou et al. 2017b; Machalická and Eliášová, 2017) suggest that a stiff adhesive’s strength decreases as the adhesive’s thickness increases due to a variety of factors.
As a direct consequence, such adhesives are incapable of accommodating dimensional discrepancies within their limited bond thickness, calling in turn for an extreme dimensional accuracy in both component and system level. In component level, mechanical post-processing of the glass bricks may be necessary to match the required accuracy in flatness and height of each component. In system level, a meticulous construction of extreme precision by a highly-specialized building crew is essential: the thickness of each construction layer has to be meticulously controlled, as any accumulated deviation larger than the required bonding thickness will lead to uneven and improper bonding (Oikonomopoulou et al. 2017a).
This level of dimensional precision has a direct negative impact on both manufacturing and construction costs. Moreover, due to their limited thickness and rigid nature of such adhesives, they have limited shock resistance (Nijsse and Veer, 2015) and may result in stress concentrations in the joints due to differences in the thermal expansion of the connecting materials. Another practical challenge linked to stiff adhesives is that the glass blocks are hard to repair or replace5 in case of damage of the structure.
Cement-based mortars and tile adhesives
Besides adhesives, cement-based mortars, conventionally applied in bonding hollow glass bricks, can also be considered for solid glass block assemblies. Cement-based mortars and tile adhesives demonstrate an excellent gap-filling capability (optimum joint thickness for solid-glass block assemblies is suggested to be 3–7 mm by (Fíla et al. 2019)), allowing for an easy assembly by a conventional building crew. Compared to stiff and flexible adhesives, they are considerably less expensive and their application is less sensitive to site conditions such as temperature, moisture and dust (Fíla et al. 2019). They typically set within 24–48 h but require a considerable amount of time (typically 28 days) to fully harden.
Subsequently, depending on the geometry of the structure, a scaffolding may be essential during construction. Compared to flexible adhesives, such mortars exhibit a low elongation at break and relatively lower bond strength. Experimental work by (Barou et al. 2020) has shown that cement-based mortars and tile adhesives typically function as the weakest link in solid glass block assemblies: failure typically occurs by progressive cracking of the bond, without any damage to the adjacent glass components. An inherent advantage of this failure mode is that it provides a visible warning and sufficient time to evacuate prior to complete collapse.
An inherent disadvantage of a system using cement-based mortars or tile adhesives is the resulting compromised transparency due to the opaqueness of the bonding media. Another consideration is that cement-based mortars and tile adhesives require a rougher surface to achieve a good adhesion; this is contradictory to the characteristic glossy, smooth finishing surface of solid cast glass components. Experimental work on solid glass blocks with a smooth finishing surface bonded with a selection of cement-based mortars by (Fíla et al. 2019) indicated an adhesion failure mode and a shear strength considerably lower than 1 MPa. In comparison, specimens comprising glass bricks with a sandblasted surface presented a higher shear strength.
Moreover, the same experimental work demonstrated that in this case as well, with decreasing joint thickness, the shear strength increases considerably – similar to adhesive connections. Shear experiments by (Barou et al. 2020) on float glass-terracotta brick specimens bonded with cement-based mortars and tile-adhesives revealed that even with the application of a primer, these bonding media still do not tend to properly bond to a smooth, vertical glass surface (Fig. 3, middle) and can easily lead to adhesive failure at low strength values. In comparison, specimens that followed an interlocking, saw-tooth edge geometry at their glass interface exhibit an increased strength (Fig. 3, right).
Hence, it can be derived that a 3D surface of the glass brick, achieved either by sandblasting in macroscale or by implementing a 3D geometry on the connecting surface of the glass block, can increase the bond strength of cement-based mortars and tiles. Nonetheless, obtaining such a surface may also increase the manufacturing costs, either due to the post-processing involved for sand-blasting the brick surface or in the use of a customized mould and brick geometry. In this direction, cement-based mortars can be a promising solution for bonding interlocking cast glass components, such as the osteomorphic glass blocks described in (Oikonomopoulou et al. 2018); the 3D interlocking geometry of such blocks already ensures an improved toughness resistance of the assembly, enabling in turn the use of a bonding media of compromised strength.
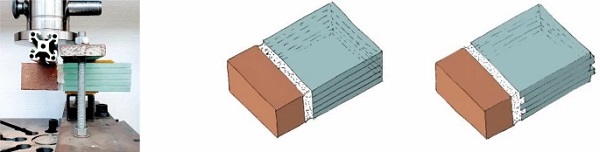
Overview of main properties
Table 1 summarizes the main properties and considerations of the aforementioned bonding media families, according to the key performance criteria of strength, visual performance and constructability. In Fig. 4 a schematic relation between shear strength and elongation to fracture (left) and gap-filling capability (right) for the discussed bonding media families can be seen. It can be deducted that, in general, high shear strength in adhesives is linked with low gap-filling capability and low elongation to failure (Nijsse and Veer, 2015).
Table 1 Typical properties of adhesive families used in glass to glass bonding based on the established performance criteria. For stiff and flexible adhesives, the properties of the finally selected adhesive per a characteristic built case study have been added to provide an indication of the desired values. However, these by no means serve as absolute limits; each category contains numerous different adhesives that can range outside the stated values - Full size table
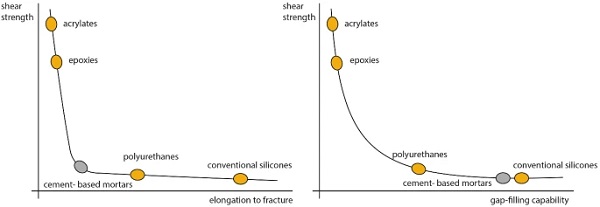
Stiff adhesives (epoxies, acrylates) present the highest bond strength and composite action, as well as a possibility for a visual result of high transparency. Yet, their inability to accommodate size deviations at their limited bond thickness can lead to localized stresses and, most importantly, to multiple arising engineering challenges linked to a construction of extreme dimensional accuracy; this in turn has a negative impact on associated costs. Flexible adhesives, mortar-based cements and tile adhesives exhibit considerably lower strength but are able to accommodate construction tolerances, allowing for a relatively simple assembly process and for the different thermal expansion of the bonding media and glass.
Despite their comparatively reduced strength, they are eligible for structural cast glass assemblies as the large bonding surface of the cast components allows for reduced stresses within the adhesive layer. Flexible adhesives present a higher strength than cement-based bonding media and do not require any post-processing of the typical glossy, smooth surface of standard, rectangular cast glass blocks. They can also offer a system of high transparency and a quick construction, if they are 2-component with a fast reacting catalyst that can guarantee fast setting and curing time.
On the contrary, cement-based mortars and tiles do require a rougher or three-dimensional glass brick surface for an increased bond strength and also result in an overall compromised transparency, as they are opaque in color. Moreover, their prolonged curing mechanism may necessitate the use of a scaffolding/framework, subject to the final geometry of the structure. Compared to flexible adhesives, they present a lower elongation at break and a better resistance against creep.
Case-studies
To further shed light on the selection process of adhesives for solid glass block assemblies, three distinct realized case studies (Fig. 5), in which the authors have been involved in the research & development of the glass-block bonding system, are reviewed in terms of adhesive selection and associated experimental validation prior to implementation: (i) the Crystal Houses façade in Amsterdam, NL (2016), (ii) the LightVault robotic assembly in London, UK (2020) and (iii) the Qaammat Pavilion in Greenland (2021). The presented case-studies showcase the impact on the final adhesive selection of the prioritized key performance criteria, which in turn are subject to the geometry and location of the case study, the available sources, budget, timeline and desired final outcome.
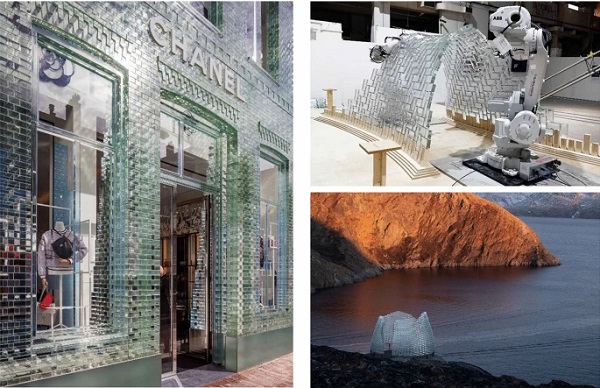
Towards maximum strength and transparency: the Crystal Houses façade
The Crystal Houses façade (Fig. 5, left) was conceived by MVRDV architects as an accurate, yet completely transparent reproduction of the previous nineteenth century historic elevation. The architects’ desire for unimpeded transparency imposed the use of a transparent adhesive for bonding the cast glass components, that would not discolor when exposed to sunlight. The resulting 10 × 12 m adhesively-bonded façade should be self-supporting, further imposing the need for an adhesive of high bond strength and composite action that would allow the bonded glass masonry wall to behave as a single rigid unit under loading (Oikonomopoulou et al. 2015b). In short, the chosen adhesive should:
- be completely transparent and not discolour when exposed to sunlight (high UV resistance)
- have good short and long term compressive behaviour and resistance against creep – permanent compressive stresses occurring at the bottom row of the bricks due to own weight are estimated to be approx. 0.2 MPa
- establish high bond strength with glass: according to the structural calculations by ABT Engineers, the adhesive should have a tensile strength > 2 MPa under standard loading and > 7.7 MPa in case of vehicle impact that would result in the complete destruction of the pillar between two glass windows (see Table 1)
- achieve high composite action and result in a monolithic, rigid masonry wall
- have good resistance to weathering
- allow for a relatively fast and controllable construction (fixing time < 5 min, curing time < 24 h)
Figure 6 provides a schematic illustration of the R&D process followed for developing the adhesively-bonded system. The prioritization of a high structural and visual performance led to the preselection of a stiff adhesive for bonding the structure. Initially, both epoxies and acrylates were explored. Preliminary application and 4-point bending tests on (4) beam specimens comprising adhesively-bonded glass blocks (Fig. 7), lead towards the use of Delo Photobond 4468 as the most promising option (Oikonomopoulou et al. 2017a); a colourless, UV-curing, one-component acrylate, designed for high strength bonding between glass components (Fig. 7, bottom).
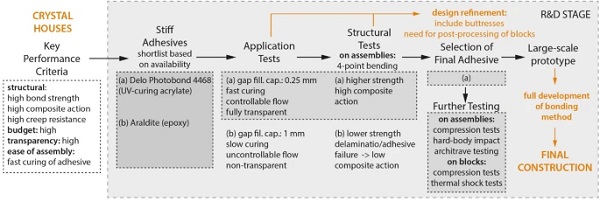
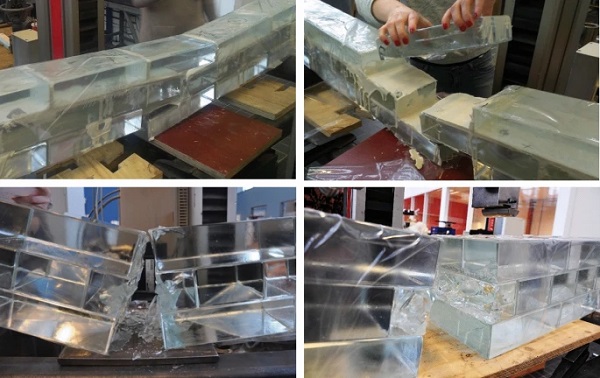
Compared to the UV-curing acrylate, the chosen Araldite epoxy, despite exhibiting an unusually large gap-filling capability, involved many practical challenges linked to its applicability, including a lack of transparency and of controllable flow of the adhesive due its prolonged setting time that lead to excessive overflow even with the use of spacers (Fig. 7, top). In comparison, the photo-catalytic curing of the selected acrylate allowed for a fast, controllable construction: Delo Photbond 4468 can be fully cured, attaining its full structural capacity and becoming moisture- and water- resistant, in a minimum of 40 s using 60 mW/cm2 UVA intensity (Delo Industrial Adhesives 2014).
Moreover, initial 4-point bending tests indicated a lower bond strength and composite action for specimens bonded with epoxy, also evident from the adhesive failure (Fig. 7, top right) compared to the cohesive and substrate failure of the specimens bonded with the chosen UV-curing acrylate (Fig. 7, bottom right). Specifically, a total of 4 specimens bonded with the selected UV-curing adhesive, indicated a monolithic behaviour of the adhesive-block assembly under loading with a flexural strength > 4.79 MPa6 (Oikonomopoulou 2019), when the adhesive is applied in a uniform layer of the optimum thickness.
To evaluate the visual result and develop the bonding method for the system, several visual mock-ups of wall segments were built at the TU Delft lab facilities. After the 4-point bonding tests indicated the most suitable adhesive candidate, to obtain satisfactory data on the performance of the adhesively-bonded system copious structural tests were needed, summarized in Fig. 8. Both structural and visual experiments suggested an optimum joint thickness for the selected adhesive between 0.2 and 0.3 mm (Oikonomopoulou et al. 2017a).
Subsequently, to guarantee the highest bond strength and composite action, the CNC-polishing of the glass blocks’ top and bottom surfaces to a matching flatness of ± 0.25 mm was deemed inevitable (Oikonomopoulou et al. 2015b): the natural shrinkage of the soda-lime glass, occurring during the cooling of the molten glass, was larger than the required flatness. This extreme dimensional accuracy was not only required per glass block, but also per construction layer, as any accumulated deviation larger than the established thickness of the adhesive could lead to uneven and improper bonding and consequently to the generation of localized stresses (Oikonomopoulou et al. 2017a).
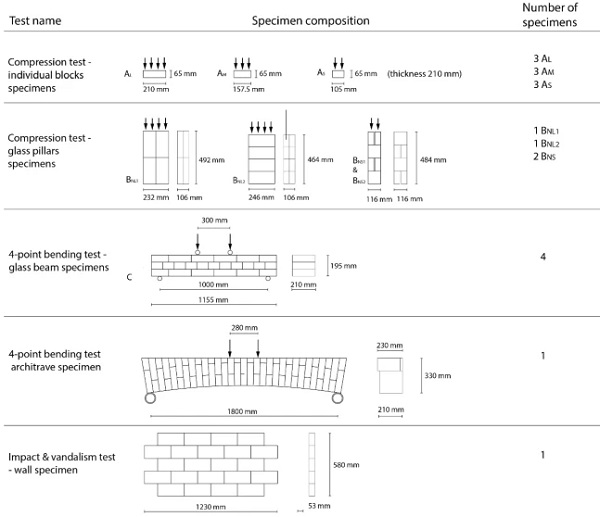
The demand of this unprecedented high level of accuracy together with a request of high level of transparency, introduced various additional challenges in the construction of the Crystal Houses façade. These included the development of a customized bonding method for achieving a uniform, air-gap-and-bubble-free bond and of special gauging equipment for controlling the dimensional accuracy of the polished blocks and for levelling the starting bonding surface to the desired accuracy; and the recruitment of a highly-skilled building crew in order to execute the strictly controlled construction.
Given the central location of the building in Amsterdam and its commercial use, a method for the replacement of a damaged block had to be developed (e.g. in case of vandalism of the façade): The stiff nature of the adhesive and the lack of a known solvent rendered as sole solution the initial mechanical removal of the main mass of the damaged component; then, with the aid of controlled heat the adhesive was softened in order to be able to be locally removed. It should be noted that this is a time-consuming and labor-intensive process that may still lead to the damage of the adjacent bricks.
Towards a fast, automated assembly process: the LightVault
Aim of the LightVault project, a joint effort between SOM and Princeton University c.r.e.A.te lab and Form Finding Lab, with assistance from the TU Delft Glass Group, is to demonstrate the potential of automated robotic construction. The project evolves around the robotically-assembled construction, without the aid of a scaffolding, of a large-scale double-curved glass brick vault, approx. 2 m high and 2.6 m wide (Parascho et al. 2021). The structure was assembled live onsite by 2 robots through the course of SOM’s Anatomy of Structure 2020 exhibition in London.
The glass brick vault, which follows a herringbone pattern, has been designed as a compressive-only shape. Still, the application of an adhesive media was necessary in order to stabilize the structure during its assembly, as no scaffolding should be used. The limited budget for this research project implied that (i) a repetitive and readily-available glass brick moduli should be used and (ii) post-processing of the blocks should be avoided; thus, the adhesive media should be able to compensate for the dimensional deviations linked to the casting of the blocks (± 1 mm).
Additional construction tolerances, arising from the robotic assembly and the double-curved geometry should also be compensated by the bonding media. Due to the double-curved geometry of the structure and the utilization of a standard brick modulus, the gaps between the bricks varied widely in terms of dimension and shape. Further computational optimization of the geometry led to 80% of the gaps between bricks in the final vault to be below 17.5 mm (Parascho et al. 2021).
To negotiate the joint size variations, upon consultation with TU Delft, it was determined to insert standardized wooden wedges in gaps > 17.5 mm, as these would be unrealistic to fill solely with an adhesive media of satisfactory strength. As there were only 2 robots available and were both needed for the assembly of the glass brick structure, the adhesive would be manually applied in each brick. Hence, the chosen adhesive should:
- have a fast-fixing (within 5 min), hardening (< 25 min) and curing time (< 1 h) in order to facilitate the robotic assembly
- have sufficient thickness and be flexible enough to absorb construction tolerances ≤ 17.5 mm
- be creep resistant, preventing movements of the structure during its assembly
- ensure a good bond to both wood (wedges) and glass (blocks)
- have sufficient tensile strength to hold the bricks in place during construction without scaffolding – in specific, it should have enough tensile capacity to hold a brick in place during the temporary construction condition (Parascho et al. 2020)
- high strength was not deemed necessary; the structure is self-supportive once completed and is an interior installation; other than the self-weight of the structure no forces are anticipated to act on it
- transparency was not highly prioritized, allowing for the use of an opaque adhesive media
Figure 9 shows a simplified diagram of the R&D methodology followed for the adhesively-bonded system for the LightVault project and how both the performance criteria and the adhesive selection informed the design and the assembly process. The primary requirements for the bonding material were to be fast-setting, rigid, and creep resistant; equally importantly it should have a gap filling capability of up to 17.5 mm. The requirements for rigidity and creep resistance led to a preference towards stiff adhesives, despite their reduced strength over an increased gap-filling capability.
Mortars were rejected due to their prolonged curing mechanism that necessitated a scaffolding (which was in contrast to the concept of the project). Therefore, preliminary research and applicability tests, held both at TU Delft and Princeton, first on bonding two glass bricks in a cantilevered configuration at TU Delft (Fig. 10, top and middle) and then on small- and large-scale robotically assembled arch prototypes at Princeton (Fig. 10, bottom), focused on the application of either epoxies or acrylates, but also on alternatives such as double-sided tape, reusable Nano Gel Tape, for the connection between the individual glass bricks.
An unforeseen additional logistical challenge towards the pre- and final- selection of the bonding media, was that not the same adhesives were readily available in both the USA and European market. Most candidates were discarded during the applicability tests (Fig. 10) due to a lengthy setting time linked with an inability to control excess overflow or due to a limited gap-filling capability as explained in Fig. 9. Eventually, a fast-setting two-component Epoxy Putty, PIG™ Multi-Purpose Epoxy Putty available in USA, typically used for auto repairs, seals and custom-formed gaskets, was selected. The putty has a grey color, a handling time of 3–5 min, is hardened within 20 min and fully cured within 60 min (New Pig).
The putty form of the epoxy allows for a gap-filling capability of up to 20 mm thick joints. Τhis epoxy, even though not designed for structural applications, has also satisfactory compressive strength (55 MPa) and leap shear tensile strength (6.2 MPa). In point of fact, an adhesive of lower strength could be acceptable, as the bond is anticipated to take up forces only during assembly. Thus, given also the time and budget restrictions of the project, no structural testing was performed; the sufficient structural capacity of the putty was instead confirmed via the real-scale robotic assembly prototyping (Fig. 10, bottom) of an arch of the vault at Princeton University (Parascho et al. 2021): as a maximum, a single epoxy putty connection could support the self-weight of up to 5 cantilevered glass bricks (Parascho et al. 2020).
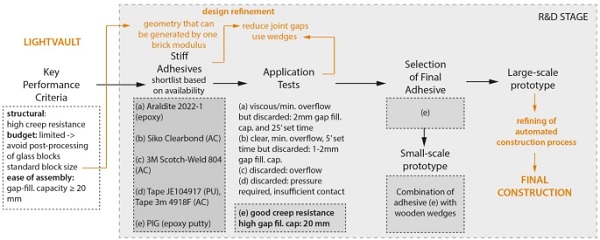
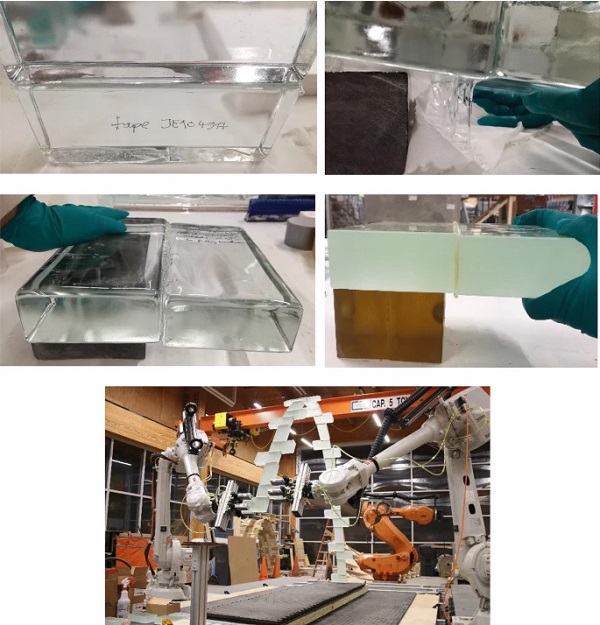
Towards an easy assembly in extreme climate conditions: the Qaammat Pavilion
The Qaammat Pavilion, designed by architect Konstantin Ikonomidis, is an adhesively-bonded glass brick pavilion, which serves as a landmark in the village of Sarfannguit, the only active village within the UNESCO Aasivissuit World Heritage Site – Nipisat. The pavilion follows a conical frustum shape (circa 3.2 m in diameter and 2 m high). It consists of two semi-circular, perforated walls made of solid cast glass bricks, resting directly on the rock through metal bars—a method borrowed from local house building.
Compared to the previously presented adhesively bonded glass brick structures, the Qaammat Pavilion, faces a diverse set of engineering challenges. Firstly, the structure should be built under a limited budget and with the aid of the unskilled local population, commanding a simple bonding system and the use of standardized, readily available glass bricks without any post-processing that would lead to an increase in manufacturing costs. The pavilion’s remote and hardly accessible location on top of a rocky hill with no access to electricity and other commodities conventionally available in construction sites further imposed the need for a simple bonding method. Most importantly the location of the pavilion just north of the arctic circle, mandated an adhesively-bonded system that would be able to withstand temperatures as low as − 35 °C.
Hence, key for the successful construction of the Qaammat Pavilion was finding an adhesive that satisfies the structural and aesthetic requirements of the project, can withstand the extreme winter temperatures of the polar climate and can offer a simple and fast construction that spares the necessity for a specialized building crew and equipment and prevents the post-processing of the bricks. In specific, the following prerequisites were set for the adhesive (Oikonomopoulou et al. 2022a):
- a shear and tensile7 strength ≥ 1-10 MPa and ability to equalize stresses
- a good creep resistance is not considered critical, considering the limited weight of the pavilion8
- a service T as low as − 40 °C
- transparent, translucent or light white/grey in color and UV resistant
- fast fixing (< 30 min) & curing time (< 48 h)
- up to 3 mm gap filling ability; the thickness of the adhesive should accommodate the manufacturing tolerances of bricks (± 1.50 mm), as well as deviations occurring during construction
Figure 11 shows a schematic illustration of the R&D methodology followed for the development of the adhesively-bonded system. Ease-of-assembly and a demanding range of operating temperatures were considered the most imperative aspects, pointing towards two-component adhesives from the silicone and polyurethane families as the most suitable candidates for this application. The satisfactory, yet limited tensile and shear strength of such adhesives led to initial adjustments in the design, reducing the cantilevering inclination of the glass-block walls.
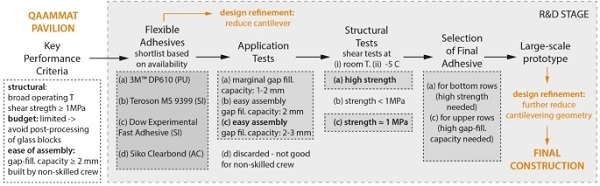
Accordingly, based on market availability, a selection of suitable transparent and white two-component adhesives were preselected to be experimentally further evaluated via application and shear tests9 (Fig. 12). The applicability tests involved bonding two glass bricks, in order to further understand and evaluate the speed of reaction and strength development, evaluate the ease-of-assembly and get acquainted with the necessary equipment to dispense each adhesive. For the shear tests, triplets of specimens, each consisting of two cast soda-lime silica glass bricks bonded together, were prepared per adhesive candidate and tested at (i) lab temperature conditions and (ii) − 5 °C.
Based on the tests, an Experimental Fast Curing Adhesive, formulated specifically for this project by Dow, with a shear strength of circa 1 MPa, 2–3 mm gap filling capability (guaranteed by the use of double-taped spacers) and white color, was selected for bonding most of the glass-brick pavilion. Based on the prerequisites set by the TU Delft team, DOW has removed the coloring pigment of the reacting component in order to achieve a final white color instead of dark grey, and altered the mixing ratio in order to reduce the snap time down to 4 – 6 min and the time to handle strength to approx. 24 h (Hayez et al. 2021).
The 9 bottom rows of the pavilion were bonded by 3 M™ Scotch-Weld™ Polyurethane Adhesive DP610, a 2-component polyurethane adhesive of a higher shear strength, necessary in this location, due to the reduced overlapping of the bricks (and thus smaller bonding surface). Tolerances in the first rows of the pavilion are minimal and can be absorbed within that adhesive’s limited gap filling capability of 1 mm.
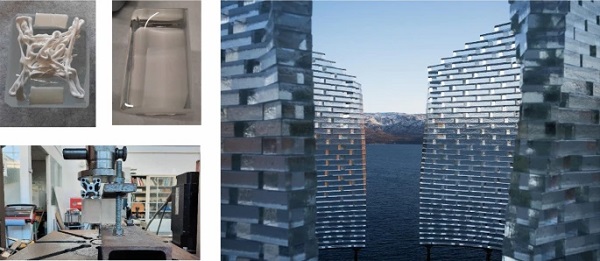
Prior to the actual construction, a final large-scale mock-up (0.8 × 0.8 m) of a segment of the wall was built at the TU Delft lab together with the architect of the project. The prototype showed that the application of both adhesives was simple and fast and the desired joint thickness could be guaranteed with the aid of double-tape spacers; most importantly, it indicated that the initially designed cantilevering gap should be reduced in order to prevent the bonded structure from tilting (see Fig. 13).
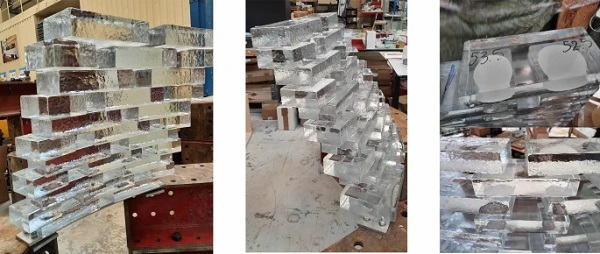
Conclusions
On adhesive pre- and final- selection
Table 2 summarizes the main characteristics of each analyzed adhesively-bonded case-study.
Table 2 Summary of main characteristics of each case-study - Full size table
The present work illustrates how the prioritized criteria per case-study lead to the initial preselection of the most suitable adhesive family. In the presented examples, the main criteria for pointing out the most suitable adhesive family lie between high bond strength, characteristic of stiff adhesives, versus ease of assembly, supported by the gap-filling properties of flexible adhesives and cement-based mortars. A flowchart illustrating the impact of the prioritized criteria per case study to the final adhesive selection is shown in Fig. 14.
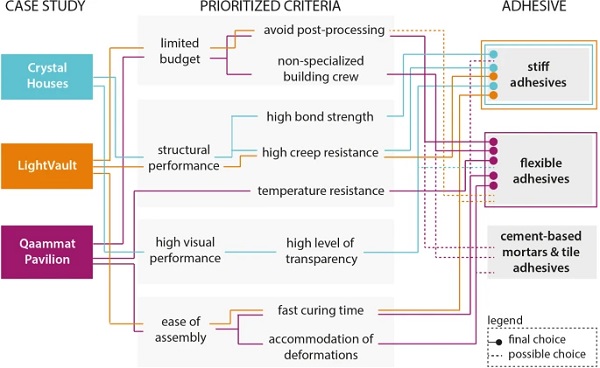
When high strength of the adhesively-bonded system is the most crucial aspect, such as in the Crystal Houses façade, then stiff adhesives, from the epoxy and acrylate families, are the straightforward choice. Such adhesives offer high bond strength and composite action; they can also yield a system of high transparency. The main drawback of using such adhesives is their limited application thickness to guarantee optimum bond strength, typically between 0.1 and 1.0 mm; which in turn suggests an inability to accommodate dimensional tolerances within the bond thickness.
In essence, the limited gap-filling capability of stiff adhesives yields a system fundamentally different to that of a conventional mortar masonry, where the mortar can accommodate possible discrepancies in size and surface quality of the bricks. This, in sequence, calls for a construction of extreme dimensional accuracy by a highly-skilled building crew, and moreover for the need of post-processing of the blocks to virtually perfect flatness; these aspects also have a significant negative impact on the associated construction costs.
Most of the engineering puzzles involved in the Crystal Houses façade could be solved if a thicker transparent adhesive of equal structural performance existed (Oikonomopoulou et al. 2017a). It should be noted here that as shown also by the discussed examples, adhesives from the epoxy and acrylate family can also offer a larger gap-filling capability, e.g. in a putty form or even in the conventional adhesive form; yet these offer a compromised strength and uncontrollable overflow that can be a challenge in terms of constructability.
In order to facilitate the assembly but also prevent the post-processing of the glass bricks to high dimensional accuracy, the other two case studies involved the adhesive’s gap-filling capability as a key adhesive selection criteria. In the case of the LightVault, finding a fast-setting adhesive with satisfactory gap-filling capability (pointing towards the direction of flexible adhesives) and good creep resistance (pointing towards stiff adhesives) proved to be a challenge. Eventually, a stiff, gray epoxy patty was selected that had a quick handling time and a 20 mm gap filling capability – this can be considered an exception overall, as the putty form of the epoxy does not present the same properties as a typical, stiff epoxy adhesive and is non-typical for such a structural application. Yet, it was acceptable in this case, as due to the compressive-only geometry and absence of external, variable loads, the bonding media had to essentially be able to withstand creep and absorb dimensional tolerances primarily during assembly.
Finally, in the Qaammat Pavilion, the focus was placed in finding an adhesive that would allow the structure to perform well under the extreme, arctic temperatures of Greenland and provide an easy construction by a non-skilled building crew. In contrast to the Crystal Houses façade, here the structural adhesive should function similarly to a mortar in traditional brickwork; able to provide sufficient strength and at the same time absorb, within its thickness, the dimensional discrepancies of the bricks as units and of the entire construction. Based on the above, soft-elastic, flexible adhesives were preferred leading to the eventual use of a white structural silicone, custom-developed for this project by Dow.
It should be added here that mono-component flexible adhesives are not recommended for the wide joints of cast glass assemblies due to their chemical curing mechanism.
Lastly, in all cases, the adhesive selection led to refinements in the design. Overall, the geometry of the design can have a significant impact on the adhesive selection. For example the LightVault spares the necessity for an adhesive of high-strength due to its compressive-only geometry. Whereas the vertical, self-standing 10 m high façade of the Crystal Houses necessitates the use of a stiff adhesive to ensure the required strength and rigidity of the structure. In the Qaammat Pavilion the cantilevering of the walls towards the interior had to be reduced to enable the application of a flexible adhesive that would allow for an easy assembly. Accordingly, it is important that the architects and structural engineers of a project implementing an adhesively-bonded cast-block system consult the respective research team from the early stages of the design, as alternations in the design can influence the initial adhesive family selection and can in turn reduce the complexity of the construction and associated costs.
On experimental validation
After preselecting the most suitable adhesive family, the final shortlist of adhesive candidates per case-study is subject to the extensive list of performance criteria, and equally importantly to the local market availability. All case-studies have followed a similar R&D approach, starting with application tests, followed by structural testing and finally by a large-scale mock-up prior to construction.
Application tests are essential for evaluating the visual performance and constructability of the bonded assembly; particularly for revealing the practical challenges entangled to the use of the selected adhesive, such as achieving a uniform bonding and dealing with excessive overflow, need of spacers, etc. These aspects can in turn lead to effectively narrowing down the shortlist of preselected adhesive candidates and to alternations in the design during an earlier stage, when there is still room for more flexibility.
Given the lack of existing guidelines and strength data on adhesively-bonded glass-brick assemblies, structural testing is necessary to point out the most suitable adhesive candidate and to certify/quantify the structural performance of the bonded glass-brick assembly. The involved experimental testing varies significantly per case-study as it is subject to the type of structure, available budget and timeframe, and to local building regulations. For example, in the case of the Crystal Houses façade, extensive structural testing was necessary in order to provide the structural engineers with sufficient strength data of the adhesively-bonded system to structurally verify the structure prior to its realization.
In the case of the smaller-scale examples of the LightVault and the Qaammat Pavilion, where there was limited budget and less building regulations involved, the verification of the assembly’s performance was limited to the most necessary experiments. In specific, LightVault is, in essence, an indoor installation of a full-scale research prototype. The lack of variable forces, the possibility to restrain the access of the public below the vault, and the compressive-only nature of the structure once completed, allowed for the verification of the adhesively-bonded vault structure via assembly prototypes only. In the case of the Qaammat Pavilion, the limited budget and the sculptural nature of the structure also led to a limited structural verification, focusing on shear tests in both room temperature and − 5 °C, as the extreme cold temperatures of the arctic climate were one of the biggest considerations.
In all case-studies, the built-up of large-scale mock-ups with the final selected adhesive have also proved to be essential in order to fully develop the relevant bonding method and assembly process.
Proposed R&D methodology for adhesively-bonded systems
Based on the above, Table 3 provides a proposal for the initial selection of the most suitable adhesive system according to the desired gap-filling capability (ease of assembly), type of load (strength) and transparency level (visual performance).
Table 3 Selection of most suitable bonding media according to gap-filling capability, anticipated load and transparency level, based partially on (Nijsse and Veer, 2015) - Full size table
Figure 15 provides a schematic illustration of the proposed methodology for developing an adhesively-bonded system; highlighting as well the stages at which the bonding selection informs the design. The concept design and the respective prioritized performance criteria can already indicate the most suitable bonding media family; this can in turn already lead to adjustments in the design’s geometry. The final shortlist of adhesives is subject to the elaborate list of performance criteria and to market availability. Application testing should be done first, to further narrow down the shortlist of adhesive candidates and provide a first indication of the desired bondline thickness based on application considerations. Following, to identify the most suitable candidate and verify the assembly’s performance, initial structural tests should be performed in adhesively-bonded assembly specimens.
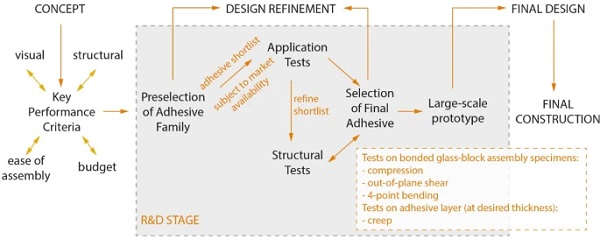
There is currently a lack of relevant building guidelines for the verification of the structural performance of an adhesively-bonded glass-block system, which is further amplified by the individual requirements set by each case-study. As a first step, the authors of this work suggest the establishment of a test standard for evaluating solid glass masonry structures; this should include, but not be limited at, compression tests, out-of-plane shear and 4-point bending tests of small-scale assembly specimens (as shown in Fig. 15) with the final selected adhesive candidate in the desired bondline thickness in order to derive the main structural properties of the assembly. Creep tests on an adhesive layer of the desired thickness can provide further insights in the long-term performance of the system and the suitability of the selected adhesive for the transfer of the given dead loads.
Artificial aging tests of the adhesive, such as the ones described in ETAG 002 for adhesive connections in glass construction, can reveal the influence of environmental factors in its long term performance. The experimental testing of the adhesive bond in different temperatures for applications in moderate climates is not deemed necessary, given that the desired service temperature range is within the range certified by the supplier; yet, it is important that provisions are made in the engineering of the structure so as to be able to accommodate movements due to the thermal expansion of the glass components. This can be solved for example, either by employing a flexible adhesive that can accommodate deformations within its thickness, or, in the case of rigid adhesives by leaving open joints (e.g. in both the Atocha Memorial and the Crystal Houses the vertical joints were left open) and/or by allowing the structure to expand as a whole.10
Finally, the build-up of a large-scale visual prototype is highly recommended in order to fully develop the bonding method, familiarize with the relevant equipment and indicate any necessary alternations to the design prior to the actual construction.
Recommendations
The discussed bonding media have not been developed specifically for solid cast glass assemblies; most adhesives for structural glass applications are engineered for linear bonding or for application in a limited surface. Therefore, the development together with an adhesive manufacturer of a bonding media explicitly for cast glass assemblies and masonry systems could lead to a significant expansion in their applicability. The collaboration of TU Delft with Dow Silicones Belgium for the development of a customized glue for the Qaammat Pavilion is an excellent example in this direction.
In essence, adhesively-bonded glass block systems call –ideally- for an adhesive solution that can be applied in a large surface, yields high strength and transparency, while being able to compensate for dimensional discrepancies within the bond thickness. In that sense, the bonding mechanism in cast glass structural assemblies is closer in principle to lamination rather than to commonly encountered localized adhesive glass connections. Hence, the ideal solution would be the development of a hot-melt foil that could be heated and pressed in situ (via a portable heating and pressing equipment) to bond the glass blocks together.
In-situ lamination via a hot-melt foil is as of yet to be available to the knowledge of the authors: this is also exemplified by the bonding solutions adopted for the horizontally stacked glass-sheet sculptures of the Glass Sphinx and the Glass Angel: in both, lamination was discarded as a solution, most probably due to the amount of multiple layers that should be bonded together and the total dimensions of the sculptures. Instead a solution utilizing tape as the bonding media was adopted (Nijsse 2012; Bos et al. 2012); illustrating as well that structural glass adhesives are yet to be developed for bonding considerably large surfaces of glass in a stacked configuration (Oikonomopoulou et al. 2022a).
Pre-assembly via lamination in the factory of units consisting of multiple glass blocks although possible would only magnify the challenges of bonding instead of reducing them, as it would demand the eventual in-situ bonding of a considerably lengthier (and thus larger) surface. Even in these pre-assembled units, it would be particularly challenging to laminate multiple layers of glass blocks together, given the considerably larger size tolerances of glass blocks compared to float glass,11 the required pressure and autoclave set-up.12 The only known realized example using pre-assembled glass-block units (via bonding and not via lamination) is the Crown Fountain in Chicago, IL; here pre-assembled units of approx. 250 glass blocks each were fabricated (Hannah 2009); in this case, the adhesive connection between the pre-assembled units was not critical, as the latter were directly connected to a stainless steel substructure.
Still, a promising step towards the aforementioned bonding philosophy, is the development by Dow Silicones Belgium of a pre-cured, transparent, silicone elastomer that can be glued to various substrates with the use of a primer forming a covalent bond, for the creation of transparent spacers for IGUs with sufficient mechanical strength, (Hayez et al. 2019). Such a bonding solution could be a real breakthrough, if developed for adhesively-bonded glass brick assemblies.
Towards circularity, research on finding an adhesive that can be eventually dissolved is highly recommended. To completely evade adhesives, without a significant comprise in the structure’s transparency, a promising approach is the reversible embedded mechanical connection described in the patent by (Oikonomopoulou et al. 2022b): a mechanism utilizing magnetic balls inside the embedded -to the glass block- connection can lock and unlock the connection with the aid of a magnetic field, enabling a fully demountable, highly controllable connection (see Fig. 16).

Another circular construction system for cast glass assemblies is the dry-assembly system employing interlocking cast glass components (Fig. 17) presented in (Oikonomopoulou et al. 2018). The interlocking geometry of such blocks, renders them also a good candidate for assemblies using cement-based mortars, as it allows for a better collaboration between glass and mortar and for a structure of inherent toughness resistance. Although such mortars were not applied in any of the presented studies, the authors believe that cement-based mortars can be suitable for compressive-only structures, such as in the LightVault, if scaffolding/framework can be installed and compromised transparency is allowed. Lastly, another promising application for cement-based mortars is in the restoration of historic monuments using cast glass components, discussed in (Barou et al. 2018, 2020).
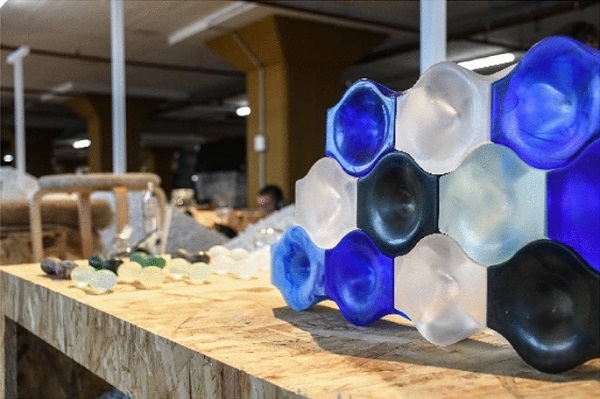
Notes
- Only recently, research by (Bristogianni et al. 2021a; Bristogianni et al. 2021b) has shed light on the structural properties of cast glass.
- For structural applications, it is advised to consider a reduced maximum shear strength value so as to account for the large deformability of such adhesives at low stress values.
- According to (Banea,da Silva 2009), structural adhesives typically show a reduction in strength with increasing bondline thickness, which can be attributed to a variety of reasons, such as internal imperfections in the joint and/or increased interface stresses and bending moments within the adhesive layer. Due to the above, it is recommended by the authors of this article to experimentally validate the chosen adhesive’s performance in specimens of the desired bondline thickness and bonding surface so as to derive the most representative strength value and behaviour.
- For example, (The Dow Chemical Company 2020) offers structural silicones with a service temperature range of -115 °C to 260 °C for aerospace applications.
- The only known replacement method for adhesively-bonded glass block systems is with the aid of controllable heat, as described in (Oikonomopoulou et al. 2015b). The process is briefly described in Sect. 4.1. Still, it is a rather time-consuming and labor-intensive process that requires extreme precision in order to prevent damaging the adjacent glass components.
- The detailed results of the experiments can be found at (Oikonomopoulou 2019). The 4 specimens suggested flexural strength values between 4.79 – 7.01 MPa. It should be noted that the mentioned values can be considered rather conservative as the specimens are only bonded horizontally, resulting in peak concentrations on the open vertical joints. An architrave specimen was also tested suggesting as well a flexural strength of 6.7 MPa.
- Due to the project’s unique open structure, tensile resistance properties were not considered crucial. However a tensile shear strength between 1 and 10 MPa was desired; this property should be stable at a wide temperature range.
- considering the total dimensions and weight (circa 2 tn) of each wall and assuming on an even load distribution, the expected pre-compression at a brick in the first row of the pavilion with 30% of its’ total surface bonded is less than 0.15 MPa.
- The experimental results are discussed in detail at (Oikonomopoulou et al. 2022a).
- For example, this was achieved at the Crystal Houses by implementing a flexible 20 mm thick connection of the facade to the top metal beam, which supported the upper level of the building (Oikonomopoulou et al. 2017a).
- Non-post processed cast glass blocks of a size comparable to standard terracotta bricks can present size deviations of ± 1.5—2 mm; in comparison, for 12 mm and 15 mm thick float glass sheets, the deviation in thickness is ± 0.3 and ± 0.5 mm respectively according to (EN 572–2:2012).
- Even in float glass, typically a maximum of 5 to 6 glass sheets are laminated together, as any deviations in size between the sheets can lead to local peak stresses at projecting points or surfaces that may cause failure. In addition, the more the glass plies, the higher the risk of visible defects on the interlayers, resulting in a considerable dropout rate for laminates with more than 3 layers (Oikonomopoulou et al. 2015a).
Acknowledgements
The success of each discussed projects lies in the good collaboration of multiple parties, from the designers to the engineers, adhesive consultants and cast glass producers. These involve but are not limited to Ashendene- Leeuwenstein BV, MVRDV, Gietermans & Van Dijk, ABT Engineers, Wessels Zeist BV, Siko BV (Rob Jannsen) and Poesia for the Crystal Houses façade; architect Konstantin Ikonomidis, UNESCO Site Manager Paninnguaq Fleischer Lyberth, Qeqqata Kommunia, Wonderglass (Christian Mussati) and Dow (Valérie Hayez and Burak Akin Aksoy) for the Qaammat Pavilion; SOM (Samantha Walker, Alessandro Beghini) and Princeton University (Stefana Parascho, Isla Xi Han, Edvard P.G. Bruun, Sigrid Adriaenssens) for the LightVault. Τhe authors are particularly grateful to Dr. Fred Veer for his valuable scientific guidance and feedback on the discussed projects, and to Kees Bardolf and Mariska van der Velden for their valuable assistance in the lab.
Author information
Authors and Affiliations
Delft University of Technology, Delft, The Netherlands
Faidra Oikonomopoulou & Telesilla Bristogianni
Corresponding author
Correspondence to Faidra Oikonomopoulou.