By the laws of physics, convection is the most efficient way to transfer heat. But what arguments back it up in practice? Let’s dive deeper and explore beyond the laws of physics what convection heating promises to users in the glass industry.
Promise 1: No glass breakage due to temperature differences
An even temperature between the glass pair and the mold avoids glass breakage during heating. In furnaces using radiation heating, glass breakage is caused by the quick heating speeds inherent to radiation heating. The mold cannot heat as rapidly as the glass, creating too large of a temperature difference between them. As a result, the glass breaks from thermal shock before being bent. What a waste!
With convection heating, hot air circulates in the heating chamber, heating the glass and the mold at the same speed. Thus, heating speeds can be much faster – and glass breakage is avoided.
Promise 2: Better optical quality
Convection heating is indifferent to glass surface materials. It doesn’t matter whether the glass is clear, printed or coated.
Think of those wide black printed areas at the sides, bottom and top of a windshield. And think of the large black printed areas reserved for the ADAS camera mounted near the top of the windshield. Without convection, you must spend a lot of time to find out the correct size and position for heat suction plates or radiation shields between the glass and the heaters to avoid overheating those black printed areas.
Overheating the printed area is a well-known problem that causes an optical distortion known as the “burn line,” which is visible just above the printed surface of the windshield.
This problem doesn’t occur with convection heating. Hardly any temperature difference develops between the black printed area and the clear glass area right next to it. You waste no time on extra precautions or experiments with heat suction plates or radiation shields. Convection heating delivers – every time.
Promise 3: Higher heating rates for higher capacity
A traditional infrared radiation heating furnace heats the glass at a rate of 40–50 °C per minute. The rate is only limited by the slower heating of the mold. Convection heating reaches a rate of 75 °C per minute.
A higher heating rate means you can get along fine with a shorter furnace, a smaller furnace footprint, fewer molds and less energy, while still producing the same capacity.
Even more importantly, with fast convection heating at the beginning of the process, glass heating speeds in the bending chambers can be relatively slow. Therefore, convection heating allows a longer time for shaping the windshields.
Promise 4: Measurable savings in millions
As said before, convection is the most efficient way to transfer heat. Let’s do some simple calculations to prove this.
In a test with a convection Glaston Matrix furnace filled with windshield compositions in sizes of 2.1 + 2.1 mm and 3 + 3 mm, the power used was measured to be 5 kW/m2. That is significantly less power than the best non-convection furnaces use, typically around 10 kW/m2.
To allow for measuring errors, let’s say the glass processing furnace with convection technology produces 1 m2 of glass using 4 kWh/m2 less energy than conventional machines with no convection.
Now – the math. Say your annual production is 300,000 windshields. On average, the size of one windshield is 1.2 m2. So, 300,000 x 1.2 m2 results in an annual output of 360,000 m2 of glass.
Let’s assume the energy price is 0.12 EUR/kWh.
360,000 m2 x 4 kWh/m2 x EUR 0.12/kWh = EUR 172,800 in annual savings.
That’s right – convection furnaces can save you a million euros in less than six years!
Promise 5: Visible results
From better glass quality to lower costs, the promises of convection technology are substantial. But perhaps the most important promise is that the benefits will be noticed. Your customers will see the optical quality improvement of the windshields they receive. And you might lose a zero or two off your energy bills.
You can’t argue with the laws of physics. And the efficiency of convection heating is something glass processors can determine for themselves.
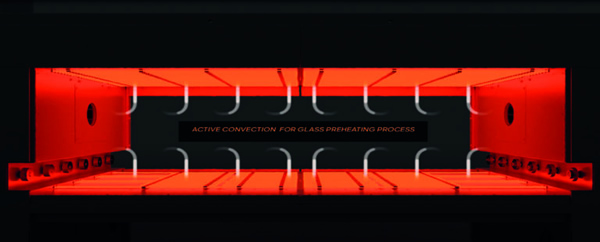