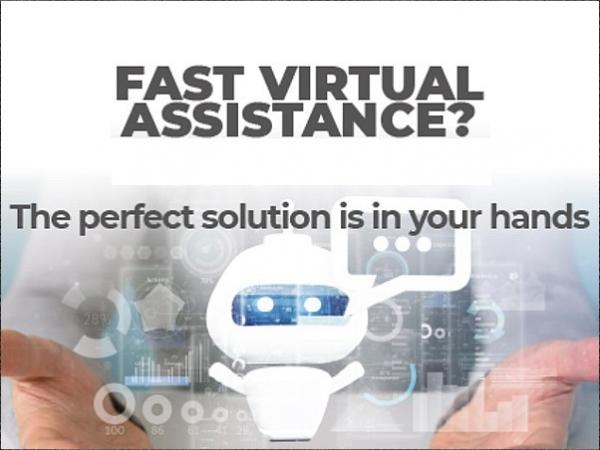
Date: 30 November 2020
SMART MANUFACTURING: PRODUCTION IN THE GLASS PROCESSING SECTOR GOES DIGITAL
The digitization of processes is having a strong impact on the world of industrial production. Through this revolution that takes the name of Industry 4.0, manufacturing companies dedicate significant resources to the provision of tools that enable them to digitize production processes and constantly monitor their performance, with a view to being increasingly competitive.
THE CONTRIBUTION OF BOVONE TO THE ADVANCEMENT OF THE GLASS INDUSTRY TOWARDS THE 4.0 HORIZON
Producing in a smarter way: giving fast and flexible answers to the market is of vital importance for companies that want to regain competitiveness. This productive attitude passes through the digital revolution.
Bovone Virtual Assistant – BVA – the virtual assistant that accompanies Bovone machines and systems fits into this panorama. BVA is an interactive, easy-to-use digital tool that, through an iPad device, assists the customer and guides him through the initial installation stages, enabling him to immediately optimize the investment.
In the subsequent phases of installation, BVA, thanks to the Database in which all the technical information relating to the purchased machine is expertly organized and easily accessible, concretely helps the customer in solving any production problems or in the calibration of the various settings. Instead of getting lost in search of user manuals, instructions, diagrams, the operator has immediate access to all information through a simple online search. The DB is structured on specific points of interest: the structure is functional to the usability of the contents and opens the way to a virtuous process of predictive maintenance that protects the customer from costly downtime.
In synergy with BVA, the Remote Assistance packages that accompany the Bovone machines connect the customer’s machine to the network, opening up exclusive access to the manufacturer’s service which, in this way, can operate remotely, intervening, diagnosing and solving any problems, or even just by adjusting and improving any settings based on the customer’s specific processing. Also updates of the software / firmware that drives the machine can be done remotely.
The Bovone stone and glass processing machines are designed to be connected online and to comply with the protocols imposed by the financial benefits provided for by the Industry 4.0 plan. The different packages that the customer can activate allow to equip himself with the basic remote assistance functions, but also to integrate the machine data in the ERP management information system.
Bovone’s remote assistance packages accompany the entire range of glass and stone machinery, allowing the Service to connect to the machine for quick diagnostics and troubleshooting. In addition, you can perform some minor software updates. To supplement this standard package, Bovone makes two optional additions available to its customers:
1. INDUSTRY 4.0 STANDARD PACKAGE
Through this option the customer can access the main production data of his machine. This data is updated at a fixed interval on a shareable file on a gateway that allows the customer to connect to the main PLC of the machine. The customer will have to organize his own management system to access this file and manage the data.
2. ADVANCED PACKAGE INDUSTRY 4.0
This package includes all the features of the Standard Package, and also provides the power consumption data of the machine: the main consumption data are the total current consumption, for each phase and the current consumption of each grinding wheel. This option provides for the supply of both an Energy Meter and acquisition interfaces for the main PLC.
In this particular moment of distancing, the remote assistance service acquires even more meaning and value: Bovone is at the forefront in countering the critical issues generated by the forced distancing, guaranteeing its customers on a global scale 24/7 accessibility to the skills of a highly qualified service team ready for direct contact with the machines to diagnose, solve, optimize.
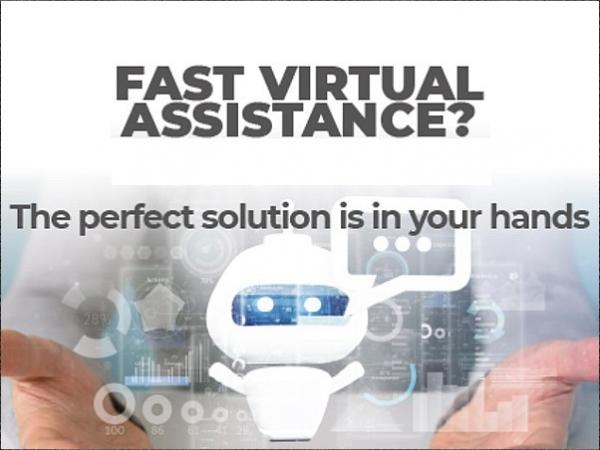

Add new comment