This paper was first presented at GPD 2023.
Link to the full GPD 2023 conference book: https://www.gpd.fi/GPD2023_proceedings_book/
Authors:
- Matthias Seel - TU Darmstadt | Institute of Structural Mechanics and Design | Glass Competence Center, Darmstadt, Germany
- Steffen Müller-Braun - TU Darmstadt | Institute of Structural Mechanics and Design | Glass Competence Center, Darmstadt, Germany
- Peter Hof - TU Darmstadt | Center for Structural Materials | Glass Competence Center, Darmstadt, Germany
- Frank Schneider - TU Darmstadt | Center for Structural Materials | Glass Competence Center, Darmstadt, Germany
- Jens Schneider - TU Darmstadt | Institute of Structural Mechanics and Design | Glass Competence Center, Darmstadt, Germany
- Matthias Oechsner - TU Darmstadt | Center for Structural Materials | Glass Competence Center, Darmstadt, Germany
Abstract
The desire to apply annealed float glass with its economic and optical advantages in comparison to tempered glass is limited in part by the reduced edge strength. In the design standard for glass DIN 18008 the edge strength amounts only 80 % of the surface strength. Due to temperature stresses, the edge strength of annealed float glass is a decisive factor, especially in the design of insulating glazing. This stress reduction is mainly a result of the applied cutting process with the corresponding parameters and the glass handling. The type of cutting process and the related cutting parameters (pressure, cutting wheels, etc.) have a significant influence on the development of micro cracks and finally on the edge strength. A defined cutting process allows reproducible and enhanced edge strength. This paper presents results of destructive tests regarding the edge strength.
For the investigations, glass panes were cut on an industrial cutting machine with various process settings. Among others, the following cutting parameters were varied: type of cutting wheel, cutting pressure, cutting speed and cutting fluid. In addition to the process parameters, different glass types, glass thicknesses and both surfaces (tin and atmosphere) were investigated. The tests were examined with the aim to determine the correlations between cutting process / glass parameters, edge strength and micro crack geometry as well as to optimise the parameters. The destructive tests were carried out with a modified four point bending test, but also with the standard four point bending test according to EN 1288-3.
1. Introduction
1.1. Motivation
Flat glass, which today is produced almost entirely by the float process, is the most important basic product for modern glazing of the most varied kinds. It is processed particularly into insulating glass units (IGU), which is a standard product in the building sector for both window and facade constructions. Annealed float glass is preferred with its economic and optical advantages compared to thermally pre-stressed glass. In the further text, annealed float glass is referred to as annealed glass. Glass edges are subjected to tensile stress, especially in case of two-sided linear support, point-fixed support, thermal action (load) and the thermal tempering process. Glass breakage due to temperature action on insulated glass units occurs due to insufficient edge strength, as shown in Figure 1. The range of applications for annealed glass is limited due to its reduced edge strength.
The characteristic tensile strength of the annealed glass edge is reduced in the design process. According to DIN 18008-1 [1], the edge strength of annealed glass amounts 80% of the surface strength, independent of the edge finishing. The draft of the European design code for glass structures FprCEN/TS 19100-1 (2021) [6] considers the edge strength of annealed float glass depending on the edge processing by an edge finishing factor ke. The factor ke ranges from 0.8 for as cut edges (as-cut ) to 1.0 for polished edges. The surface strength of annealed glass is generally known ([4]) and accepted. The edge strength, on the other hand, is often discussed and, in case of uncertainty, very conservatively applied. Therefore, in addition to the investigations of Bukieda[1], Ensslen [5], Kleuderlein [7], Lindqvist[8], Müller-Braun [9] and Vandebroek [15] this paper is intended to contribute to a better understanding of the edge strength of glass as well as the factors influencing edge strength.
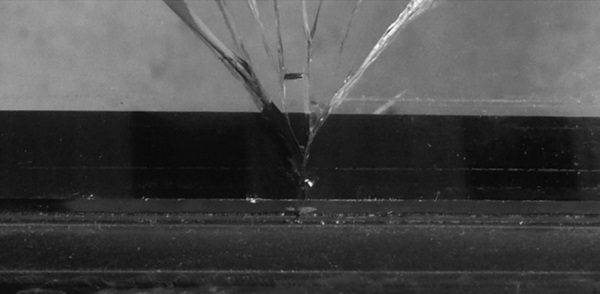
1.2. Cutting process parameters
The classic industrial glass cutting process is typically done by a cutting tool with a cutting wheel on a cutting machine. Other techniques such as laser or waterjet cutting are not the subject of this paper. In this process, the cutting wheel in combination with a cutting fluid creates a fissure on the surface and a median crack in the glass. Afterwards, the glass will be broken along the generated median crack by local bending. The cutting fluid assists the breaking process and prevents the edges from chipping. Further details regarding to the cutting process and the crack system which arises during cutting are described in detail in [9] and Müller-Braun [10]. Based on literature [7]-[10], [15] and the experience of the cutting process different cutting process parameters are summarized and categorised in Table 1.
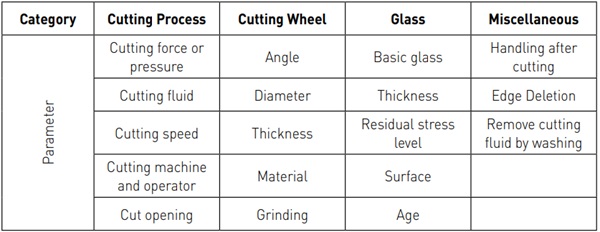
2. Methods and investigation
2.1. Determination of the edge strength by a modified four point bending test
For the determination of the edge strength of the glass sample, a modified four point bending test and the standard four point bending for glass according to EN 1288-3 [3] were applied. In contrast to the standard procedure corresponding to [3], the samples were tested along the strong axis. Therefore, one cut edge is fully exposed to a maximum tensile stress over a length of 200 mm. The schematic image of the test setup is illustrated in Figure 2. The detailed description of the test setup is published in [9]. This test setup is better suited to obtaining information on the edge strength in comparison to [3] and is more consistent with the thermal fracture scenario. The dimensions of the samples used for the modified four point bending test amount 1100 mm in length, 125 mm in height. The value of the thickness varies.
The bending tests were conducted until failure with a stress rate of 2 N/(mm² s) in accordance to [3]. Only specimens that broke within the load points were considered in the evaluation. The failure stresses σf were calculated based on the linear beam theory in dependence of the failure load F and the origin of failure. The transferability and comparison of the results out of the modified four point bending test (m4PB) to the results of the standard bending test according to [3] are of regulatory interest. For this purpose, four additional test series were conducted according to [3] with the cut edge line positioned in the tension zone. The results were compared with the corresponding m4PBseries (similar process parameters).
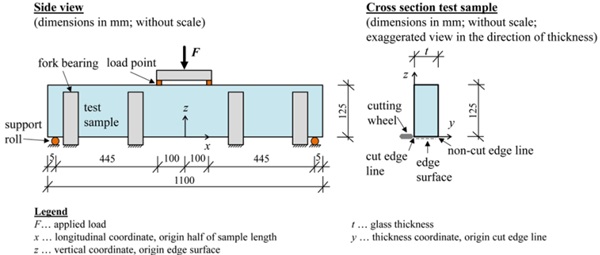
2.2. Statistical evaluation
For the statistical evaluation of the parameters and due to the large number of parameter settings, the test data including all parameters were edited into a database. The parameters were identified and optimised with the help of multiple regression and an analysis of variance in the software R [11]. For each series, the expected values (mean value), the coefficients of variation and the characteristic edge strength values (5% fractile value at a confidence level of 95%, two-parametric Weibull distribution) were determined.
2.3. Investigation – Overview of the test series
For the identification and optimisation of the cutting parameters and the further development of the cutting process, 94 series were investigated as part of the research project "Kantenfestigkeit" [16]. In general, 30 samples per series were tested. A basic overview of the parameter variation during the project is listed in Table 2. In addition to the listed parameters, the edge deletion and the washing influence of the cutting fluid (nonevaporating) were also examined. In general, all series with one exception were cut at the atmospheric surface. The tests were conducted on soda lime glass according to [4] provided by two glass manufacturers (HB1 and HB2).
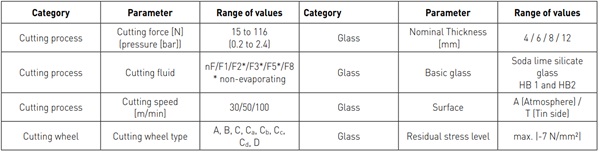
3. Results
3.1. Destructive testing of the edge strength by a modified four point bending test
Figure 3 shows the edge strength (mean value with standard deviation) of the series depending on the parameters cutting wheel type, cutting fluid, glass thickness and cutting force. The corresponding characteristic values (5% fractile value) are illustrated in Figure 4. The results indicate that a low cutting force and the choice of a suitable cutting wheel in the combination with a cutting fluid lead to an increased edge strength. It should be noted that too low cutting forces may result in significant scattering within a series and that the fracture opening process can no longer be conducted adequately. Also Figure 4 demonstrates very clearly that, with appropriate cutting parameters, it is possible to obtain characteristic edge strengths values of at least 60 N/mm² for all investigated glass thicknesses. This value of 60 N/mm² is significantly higher than the normative value of 36 N/mm² for annealed cut glass (as-cut) according to [1] and [6].
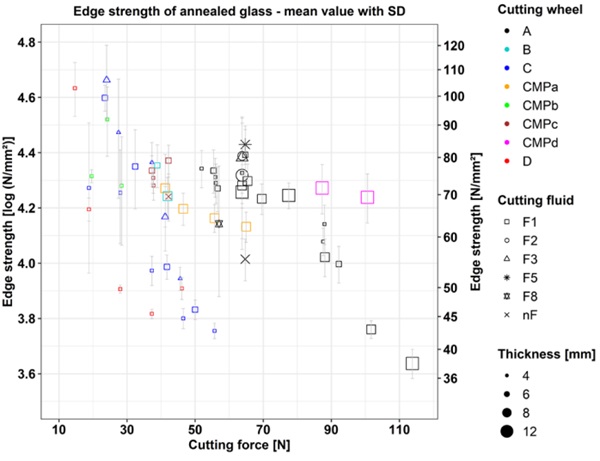
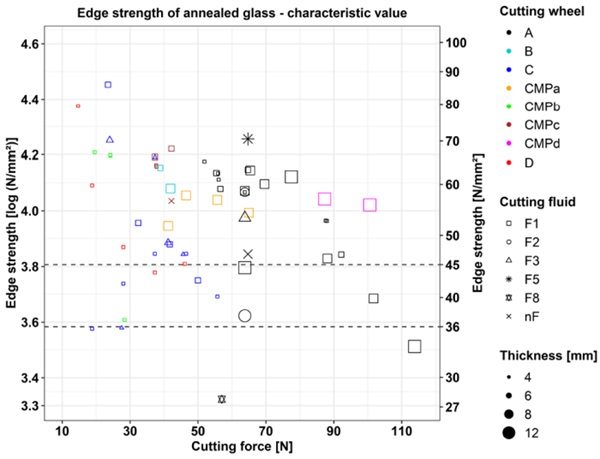
A direct comparison of the edge strength values at different cutting speeds is addressed as an example of the research project “Kantenfestigkeit” [16]. The cutting speed has a significant influence on the edge strength. The cutting speed was modified from the standard 100 m/min to 30 and 50 m/min in two series. Comparing these three series, it can be seen in Figure 5 that with otherwise identical parameter settings (cutting fluid F1 and wheel A), the edge strength increases with increasing cutting speed.
The comparison between the two types of testing - modified four point bending test "m4PB" and the standard one "EN 1288_3” [3] - is shown in Figure 6. Apart of one series (thickness 8 mm, cutting force 64 N), the test according to [3] leads to higher mean (4 to 10 %) and characteristic values (8 to 18%) of the edge strength compared to the values of the corresponding "m4PB" series. An explanation for the one difference (17% in mean value) between the results with the same parameter sets (8 mm thick and a cutting force of 64 N) and the same type of test is not found yet. Fig. 6: Edge strength (mean value with standard deviation (error bars) and characteristic value) depending on glass thickness, cutting force and type of testing with cutting fluid F1 and cutting wheel type A.
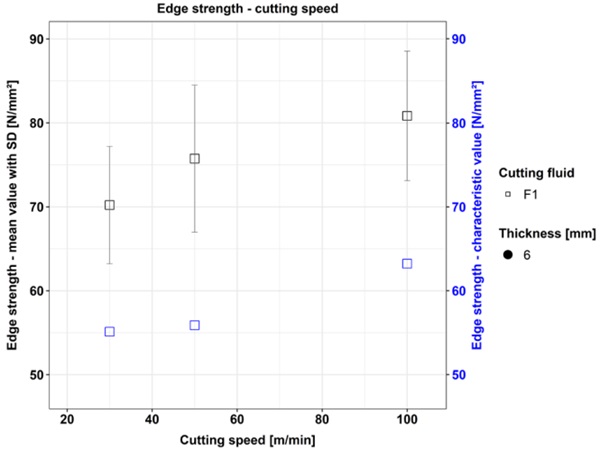
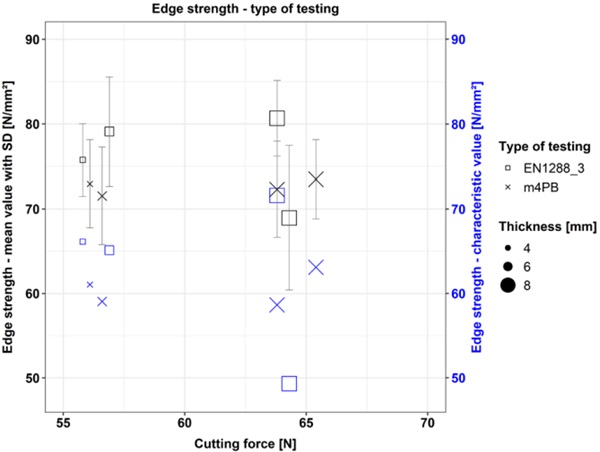
3.2. Identification of cutting process parameters
The parameter identification and their effect on the edge strength are based on a multiple regression model and an analysis of variance. The Interaction effects between the cutting force and the parameters cutting wheel category, nominal thickness, cutting fluid and surface (atmospheric or tin side) are considered. The corrected determination coefficient (R²) of the applied regression model with logarithmic edge strength amounts 77 % with a standard error of 1.1 N/mm². Without taking the interactions into account, the corrected coefficient of determination is 70 %. Due to the large scattering of the glass strength (coefficient of variation 0.3 [13]) and the large number of parameters considered in the model, a determination coefficient of 0.77 or 0.7 is a very satisfactory value according to experience. Due to the large scattering of the glass strength (coefficient of variation 0.3) and the large numbers of parameters considered in the model, a determination coefficient of 0.77 or 0.7 is a very satisfactory value according to experience.
The evaluation of the resulting data is shown in Table 3 including effect size and effect rank (ranked from higher to lower influence). All listed parameters and their interactions show a significant influence on the edge strength (significance level α = 0.05 for p-value). Based on the effect size (method omega²) the parameters cutting wheel type, cutting force, the choice of cutting fluid and the interaction between cutting force and cutting wheel type have the greatest influence on the edge strengths. The regression coefficients for the individual parameters clearly show that cutting wheel A and the use of non-evaporating cutting fluids (SFL2, SFL3 and SFL5) lead to the high edge strengths as long as the cutting forces are low. On the other hand, if no cutting fluid (“nF”, dry cut) is applied, the strength values are lower. Furthermore, to achieve high strength values, the glasses should be cut on the atmospheric side and then further processed without washing away the cutting fluid. The influence of the base glass and the nominal glass thickness on the edge strength is low compared to other parameters.
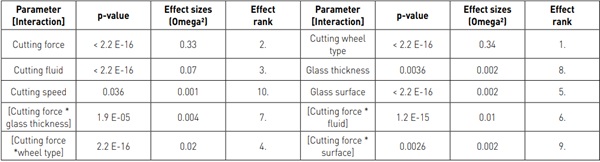
3.3. Optimisation of cutting process parameters
The multiple regression model provided the basis for the prediction and optimisation of the edge strength as a function of the process parameters. The results show that for increased edge strength, the cutting force must be reduced on the one hand. On the other hand, the reduced cutting forces lead to a higher scatter in strength and to the fact that the crack opening process is no longer practically feasible, especially for large nominal glass thicknesses. Hence, there are competing objectives. Therefore, in addition to the equation for the optimisation of the edge strength as a function of the process parameters, another model equation was developed to predict the fracture opening process.
Based on both equations and the results of the destructive and non-destructive tests, the cutting procedure was enhanced in such a way that a safe execution of the crack opening process is guaranteed even with minimal cutting forces and high edge strengths can be achieved at the same time. The boundary conditions for this two-stage optimisation task derived from the process limits of individual parameters (e. g. speed), the interests of the project participants (e. g. use of evaporating cutting fluids (here F1) and cutting wheel category (wheel type A)) and the specifications for the minimum crack depth of the median crack.
The results of the optimisation are, for instance, to cut a 4 mm thick glass with a force of 38 N and a cutting wheel CMPc or with 56 N and cutting wheel A to achieve reproducible and high edge strength values. For the validation of the model equations, series with the optimised process settings and series with high cutting forces ("negative control") were produced and tested. The results of this validation process are shown in Figure 7. Figure 7 compares the experimental results “test” with the theoretical output of the multiple regression model or prediction model (“model”). Observing the data points "opt" in comparison to the reference data points "ref", it can be seen that the optimised cutting process leads to reproducible and partly higher edge strength. The maximum error of the model amounts 9 %.
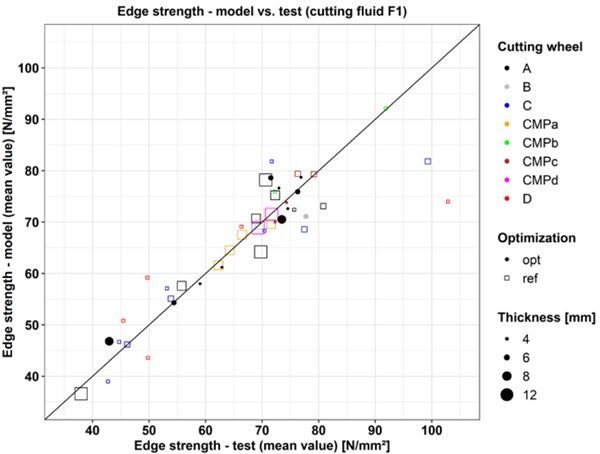
4. Conclusion and Outlook
This paper presents investigations with the aim to enhance the edge strength of annealed float glass. For this purpose, in total 94 series (30 samples per series) with different parameter settings were tested with a modified four point bending test (89 series) and a standard bending test for glass according to [3] (4 series) to identify and optimise the cutting process parameters. The main influences on the cutting process were identified during the investigations and implemented in model equations for an optimisation procedure. It was shown that cutting force, cutting wheel type, cutting fluid and the interaction between cutting force and wheel type are the main influencing factors on the edge strength. These investigations demonstrate that high and reproducible edge strength values can be produced by a glass cutting process with different cutting wheels. Furthermore, these results confirm the general findings obtained in [9], Technical Note Edge strength [14] and enlarge the data regarding the edge strength of annealed float glass.
The normative value of the characteristic edge strength of 36 N/ mm² according to [2] in combination with [4] could be confirmed as the lower limit. With appropriate cutting parameters, characteristic edge strength values for cut edge (as-cut) of at least 60 N/mm² can be achieved for all nominal thicknesses investigated here. The overall results of the investigations in [16], including normative implementation and correlations with relation to the resulting crack system, will be presented in a further paper. Initial preliminary investigations by the working group “Edge Strength” of the Fachverband Konstruktiver Glasbau e.V. (FKG) and results in [1] show that cut edges (as-cut) with low strength can generally be increased by further processing (e. g. grinding), this is not the case per se. The edge strength of the edges processed (seamed, smooth ground, polished) depends on many factors and varies significantly (see [1], [7]). The results presented here for the cut edge (as-cut) and the values for the processed edges, which should be determined in the future research, can serve as a basis for the design process of glass components [2], [6], especially under thermal stress [12].
5. Acknowledgements
The authors would like to thank the Fachverband Konstruktiver Glasbau e.V. (FKG), especially to the members of the working group “Edge Strength”, and the participants of the research project “Kantenfestigkeit” [16] who made it possible to carry out this research work. The research project [16] was funded by the Federal Ministry for Economic Affairs and Energy.
6. References
[1] Bukieda, P., Weller, B.: Impact of Cutting Process Parameters on the Mechanical Quality of Processed Glass Edges. Challenging Glass 8, Vol. 8 (2022). https://doi.org/10.47982/cgc.8.418
[2] DIN 18008-1: Glass in Building – Design and construction rules – Part 1: Terms and general bases. Beuth, Berlin (2020)
[3] EN 1288-3: Glass in Building-Determination of the Bending Strength of Glass – Part 3: Test with Specimen Supported at Two Points (Four Point Bending). Beuth, Berlin (2000)
[4] EN 572-1: Glass in Building – Basic soda-lime silicate glass products – Part 1: Definitions and general physical and mechanical properties. Beuth, Berlin (2016)
[5] Ensslen, F., Müller-Braun, S.: Kantenfestigkeit von Floatglas in Abhängigkeit von wesentlichen Schneidprozessparametern. ce/papers, 1: 189-202 (2017). https://doi.org/10.1002/cepa.20
[6] FprCEN/TS 19100-1: Design of glass structures - Part 1: Basis of design and materials. Final draft, Brussels (2021)
[7] Kleuderlein, J., Ensslen, F., & Schneider, J.: Investigation of edge strength dependent on different types of edge processing. Engineered transparency, 259-268 (2014).
[8] Lindqvist, M.: Structural glass strength prediction based on edge flaw characterization. PhD-Thesis, École Polytechnique Fédéreale de Lausanne (2013)
[9] Müller-Braun, S., Seel, M., König, M., Hof, P., Schneider, J., Oechsner, M.: Cut edge of annealed float glass: crack system and possibilities to increase the edge strength by adjusting the cutting process. Glass Struct Eng 5, 3–25 (2020). https://doi.org/10.1007/s40940-019-00108-3
[10] Müller-Braun: Risssystem und Festigkeit der geschnittenen Kante von Floatglas. PhD-Thesis (2022) Darmstadt https://doi.org/10.1007/978-3-658-36791-6
[11] R: The R Project for Statistical Computing. Software, Version 4.3.0, (2023)
[12] Schwind, G., Paschke, F. , Schneider, J., Seel, M. : Numerische Studien zur Glaskantentemperatur im verschatteten Bereich von Isoliergläsern. Glasbau 2023, Ernst & Sohn. https://doi.org/10.1002/9783433611739.ch18
[13] Schneider, J., Kuntsche, J., Schula, S., Schneider, F.,Wörner, J. D.: Glasbau: Grundlagen, Berechnung, Konstruktion. 2. Auflage, Springer-Verlag (2016).
[14] TN FKG: Technical Note FKG 02/2019 - Edge strength. Fachverband Konstruktiver Glasbau e.V., Köln (2019)
[15] Vandebroek, M.: Thermal Fracture of Glass. PhD-Thesis, Universiteit Gent and Universiteit Antwerpen (2014)
[16] Wipano FKZ 03TN010F: KantenfestigkeitHerstellungs- und Nachweismethodik zur Sicherung der Kantenfestigkeit von Floatglas. Final report TU Darmstadt, WIPANO-Project FKZ 03TN010F, TU Darmstadt (2021)