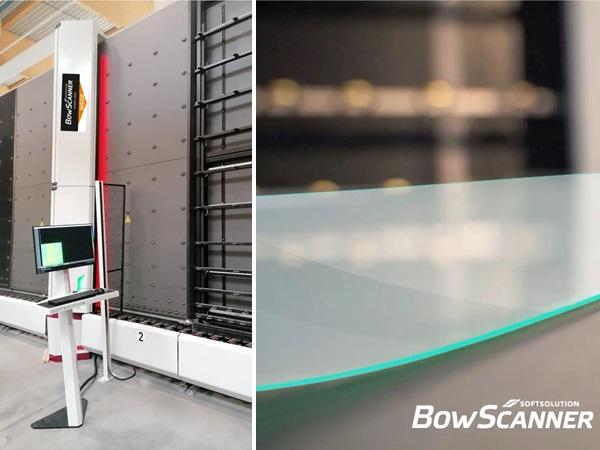
Date: 3 July 2024
Laminated glass, valued for its strength, UV-filtering, and impact resistance, is used in many applications. Producing it requires precise control, with properly sized, flat panes and correctly applied inter-layers. If either pane is bowed, adhesion issues and breakage during pressing can occur, leading to costly remanufacturing and downtime for cleaning and repairs.
Previously, measuring glass bows was manual and time-consuming. Softsolution’s new BowScanner system now offers a fully automated, non-contact solution. It measures the bow in real time as the glass moves along a conveyor, providing a detailed map of all deflections and specific bow values along various edges and diagonals.
The BowScanner also stores all measurement data for further analysis. This helps prevent the costs and failures associated with laminated units and allows the facility to identify and address the causes of bowing.
Key Benefits of the BowScanner:
- Fully automated: No more manual measurements! The BowScanner offers a non-contact, automated solution.
- Real-Time Measurements: It measures the bow in real-time as the glass moves along a conveyor, providing a detailed map of all deflections.
- Comprehensive Data: It offers specific bow values along various edges and diagonals, and stores all measurement data for further analysis.
- Cost Efficiency: By preventing adhesion issues and breakage, it helps avoid the significant costs and failures associated with laminated units.
With BowScanner, facilities can now quickly identify and address the causes of bowing, ensuring high-quality production and reducing downtime. This innovation is a leap forward in maintaining the integrity and performance of laminated glass.
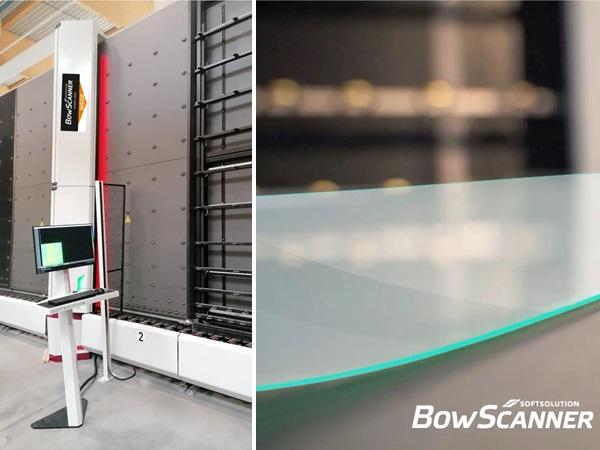

Add new comment