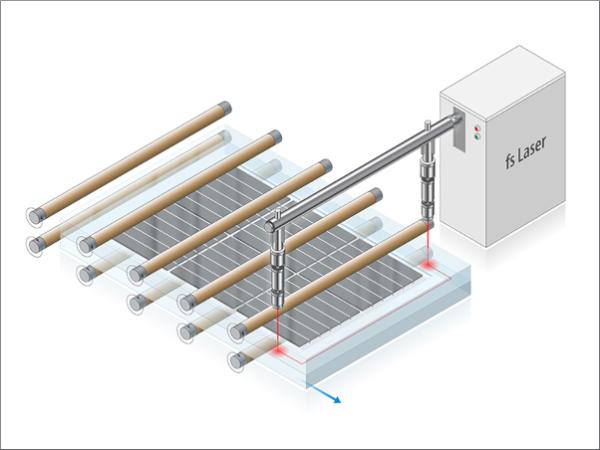
Date: 2 May 2024
The use of femtosecond lasers to form glass-to-glass welds for solar modules would make the panels easier to recycle, according to a proof-of-concept study conducted by researchers at the U.S. Department of Energy’s National Renewable Energy Laboratory (NREL).
The welds would eliminate the need for plastic polymer sheets that are now laminated into solar modules but make recycling more difficult. At the end of their useful lifespan, the modules made with the laser welds can be shattered. The glass and metal wires running through the solar cells can be easily recycled and the silicon can be reused.
“Most recyclers will confirm that the polymers are the main issue in terms of inhibiting the process of recycling,” said David Young, senior scientist and group manager for the High-Efficiency Crystalline Photovoltaics group in the Chemistry and Nanoscience department at NREL. Young is lead author of a new paper outlining the use of laser welds for solar modules. The paper, “Towards Polymer-Free, Femto-Second Laser-Welded Glass/Glass Solar Modules,” appears in the IEEE Journal of Photovoltaics.
Written with NREL colleagues Tim Silverman, Nicholas Irvin, and Nick Bosco, the paper also counts as its coauthors two employees of Trumpf Inc., the California company that made the femtosecond laser involved. A femtosecond laser uses a short pulse of infrared light that melts the glass together to form a strong, hermetic seal.
The glass weld can be used on any type of solar technology—silicon, perovskites, cadmium telluride—because the heat of the weld is confined to a few millimeters from the laser focus.
Solar modules are made of semiconductors designed to capture a specific portion of the solar spectrum, harnessing sunlight to create electricity. Typically, the semiconductors are sandwiched between two sheets of glass laminated together with polymer sheets.
NREL’s research showed that femtosecond laser, glass/glass welds are essentially as strong as the glass itself.
“As long as the glass doesn’t break, the weld is not going to break,” he said. “However, not having the polymers between the sheets of glass requires welded modules to be much stiffer. Our paper showed that with proper mounting and a modification to the embossed features of the rolled glass, a welded module can be made stiff enough to pass static load testing.”
NREL’s research is the first to use a femtosecond laser to form glass/glass welds for use in a module. A different type of edge sealing using nanosecond lasers and a glass frit filler was tried in the past, but the welds proved too brittle for use in outdoor module designs. The femtosecond laser welds offer superior strength with hermetic sealing at a compelling cost.
Young said the research is “definitely high risk, high reward,” but points to a direction for further research to extend the life of solar modules to beyond 50 years and to allow easier recycling.
This research was done through the Durable Module Materials Consortium, which is led by NREL and funded through the U.S. Department of Energy's Solar Energy Technologies Office in the Office of Energy Efficiency and Renewable Energy
NREL is the U.S. Department of Energy's primary national laboratory for renewable energy and energy efficiency research and development. NREL is operated for DOE by the Alliance for Sustainable Energy LLC.
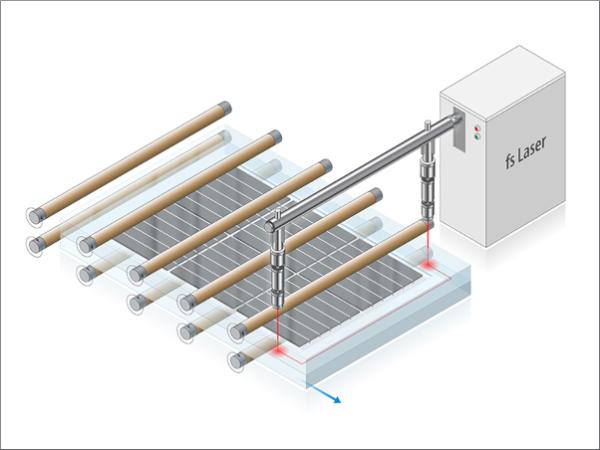

Add new comment