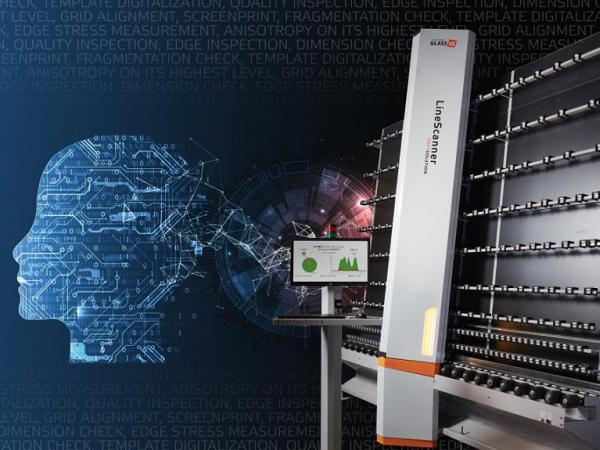
Date: 7 October 2020
For over 20 years SOFTSOLUTION has been developing and manufacturing quality assurance systems for glass processors at its site in Waidhofen/Ybbs (A). Thanks to the latest developments, the LineScanner Management Console and artificial intelligence are now used to optimize processes.
NEW // LineScanner Management Console
The newly developed LineScanner Management Console provides processors with an online overview of the current status of all scanners in production and thus integrates the scanners into the extensive automation and workflow control. This software tool records the quality and quantity of produced and scanned slices per line and gives a quick overview of all scanners in operation.
The LineScanner Management Console provides the user with the most important data (status of the line, service requirements - also foresighted - as well as current production figures with corresponding quality results) in real time. A complete documentation of the glass quality is indispensable and, thanks to lot and Industry 4.0, will be even easier in the future.
Thus artificial intelligence prevents "false quality rejects"
Artificial intelligence is already finding practical application in many areas - including inspection systems from SOFTSOLUTION - and replaces traditional automated methods, which often suffer from a high rate of "false rejects" (= false quality rejects).
SOFTSOLUTION has understood this customer requirement and relies on the use of artificial intelligence to solve problems with "false quality rejects" with the help of algorithms. Existing standards regulate the tolerances, but practice shows a different picture. Today's quality demands go far beyond that and every customer has individual requirements and tolerances. In practical use, this often leads to a high rate of "false rejects" - a false quality rejection by the plant. The scanner delivers results continuously - which defects were found on a glass, what kind of defect and is the defect acceptable or not for this customer.
An operator may have a different picture of an assessment. In this case SOFTSOLUTION now allows the operator to correct the LineScanner's decision. Such "changes" by the operator are collected and used for continuous improvement. Thus, it can be said that the LineScanner increasingly learns from feedback and constantly adapts its evaluation behaviour.
With SOFTSOLUTION – always one step ahead!
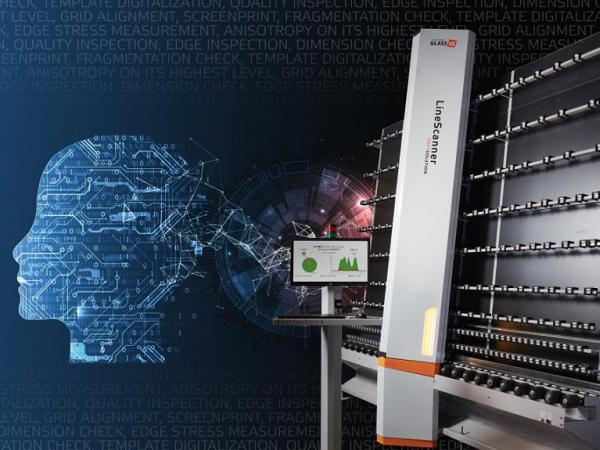

Add new comment