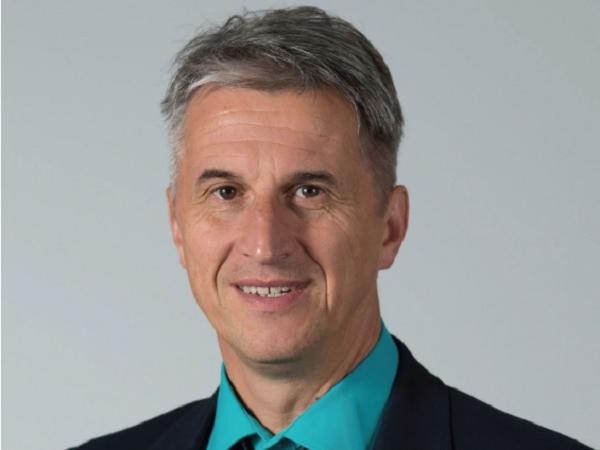
Date: 5 July 2017
We asked Andreas Kotzke, the Product Manager of Rottler and Rüdiger and Partner GmbH (R&R), to share his thoughts about the importance of quality control in the manufacturing process.
Furthermore, Mr. Kotzke discusses about the systems, certifications and standards that are commonly in use to control the quality of the production.
Finally, he sheds some light on what the insulating glass manufacturers can do to gain competitive advantage through new innovative technologies now available on the market.
“Because of the increasing global competition and customers’ higher expectations for insulating glass performance, we are likely going to see a development towards a 100% quality controlled and documented IGU’s,” Mr. Andreas Kotzke says.
Mr. Kotzke joined the insulating glass market in 1991 as the Operating Manager for a private company with two insulating glass lines.
After five years working for the company, Mr. Kotzke started to work for R&R. Currently his responsibilities are in quality and brand management for their trading department. Rottler and Rüdiger and Partner GmbH started in 1982 as a specialty retailer for the glass industry.
During the early 1990’s oxygen analysis of IG increased significantly in the DACH area. To correspond to this change, R&R started to sell oxygen analysis with paramagnetic systems like Servomex, as well as distinct devices with electro chemical measuring cells.
Insulating glass market in the DACH area
The global insulating glass market is undergoing a significant growth. One of the regions that has always being in the forefront of new developments when considering insulating glass industry and manufacturing technologies, is the DACH area.
This area includes three German speaking countries; Germany, Austria and Switzerland. For the past 25 years, in particular Germany, has been one of the leading countries to ensure high quality insulating glass unit production.
As the insulating glass market is growing, the competition also in the DACH area is growing rapidly. While the technology and information flows know very little national boundaries, recently insulating glass manufacturers from Poland have entered the DACH market causing the local demand for insulating glass units to reduce significantly.
Therefore, it has become even more important to differ from the competitors and to provide added value to the end-users or customers by producing high quality insulating glass units.
In other words, quality control plays an ever-increasing role in all aspects of the insulating glass manufacturing process. In order to manufacture comparative, proven and documented quality, what are then the most commonly used quality control systems, certifications and standards?
Quality control with RAL certification and Quality Management System standards
Over the past 20 years, quality requirements have increased constantly in order to improve the performance of insulating glass units. Therefore, it has become necessary for manufacturers to control product quality to ensure that the IGU’s meet all necessary requirements.
As in many countries, but in particular in the DACH area, there is a "double stage" system for quality control that consists of self-control of IG production and external control by accredited testing institutes such as IFT Rosenheim, MPA and KIWA.
Furthermore, insulating glass anufacturers delivering to France have to also deal with the ambitious requirements set by CEKAL. The external specialists guarantee a constant quality referring to RAL-certification.
It marks characterized products and services that are manufactured or provided according to high, precisely specified quality criteria. In addition, operators in the DACH area also follow these Quality Management System (QMS) standards:
- EN ISO 9001 is a standard that requires an organization to meet its own requirements and those of its customers and regulators. It is based on the plan-do-check-act methodology, which helps organizations establish, implement, monitor and measure their processes to deliver results that align with the organization’s requirements and continually improve performance by taking appropriate actions.
- EN ISO 1279 is the product standard for insulating glass units, which defines insulating glass units, and ensures by means of the evaluation of conformity to this standard, that over time:
- energy savings are made because the U-value and solar factor do not change significantly
- health is preserved because sound reduction and vision do not change significantly
- safety is provided because mechanical resistance does not change significantly.
Finally, manufacturers need to know the quality of their produced insulating glass units, because they adopt at least a 5-year warranty of function and values for their customers or end-consumers.
If these are the prevailing requirements and general guide lines, what options do insulating glass manufacturers have to affectively and reliably assess the quality of their production?
New practices for quality control - non-invasive insulating gas fill analysis
“Insulating glass manufacturers put in a lot of effort to follow the guidelines to achieve acquired level of quality for their production by drilling holes in the insulating glass units, what a paradox. Luckily, that is not necessary any longer, since quality can be verified the non-invasive way”, Mr. Andreas Kotzke says.
It has become common place to have a Viprotron scanner attached to the production line to ensure that all the glasses manufactured are quality controlled, and no faulty glasses or windows will be leaving the factory.
However, in order to fully meet the requirements, set for energy saving and to improve performance of the IGU’s, other components of the insulating glass units’, such as the insulating gas concentration, also need to come under the scrutiny.
Insulating glass units are typically filled with insulating gases such as argon, xenon and krypton. These gases are invisible without any odour, therefore, in order to ensure acceptable gas concentration levels, a gas concentration analyzer is needed.
Commonly used analysis method has been the invasive analysis where the seal has been broken in order to calculate the insulating gas concentration. However, due to the new advances in the measurement technology, a new non-invasive analysis method developed by Sparklike is now available on the market.
Sparklike Laser™ product line includes three distinct devices that allow the non-invasive insulating gas fill analysis for double and triple glazed insulating glass units. In addition, the measurement can be done also through coated and laminated glasses.
Therefore, with Sparklike Laser devices™, manufacturers have:
- the opportunity to test already produced IG units without penetrating the seal
- as the seal does not need to be broken, the non-invasive technology allows multiple measurements for the same unit, which in return improves the consistency of the measurement results
- the non-invasive analysis method also allows the manufacturer to be certain that their customers are getting what was promised, since the tested unit can be delivered to the end-consumer
- this, on the other hand, makes the manufacturing of “special test samples” unnecessary. In other words, the non-invasive technology diminished the need to alter or suspend the production, which in return helps manufacturers to save on both, costs and time.
As can be seen from the benefits listed above, Sparklike’s new technology has the possibility to affect the production process in a very positive way.
While producing special test-pieces is a good and a widely-used practice, it falls a bit short in comparison with the option to test every single unit produced by integrating the non-invasive analyzer as a part of the production line, as can be done with Sparklike Laser Online™ devices.
Other devices within the product line are Sparklike Laser Standard™ – an offline solution frequently used by test laboratories and for desktop use – and Sparklike Laser Portable™, which in return has the whole system integrated into a heavy-duty case with wheels and a battery for mobility in factories and building sites.
With more than 60 devices sold, the Sparklike Laser™ product line has been getting a very reassuring feedback. Several companies have already started to use this new technology with encouraging results.
Mr. Kotzke believes that the insulating glass manufacturers have come to the realization that there’s need to guarantee the quality for all the components of the insulating glass unit.
“Even though, any additional investments may seem like a somewhat important financial effort, it is vital to understand what is less desirable – in terms of cost, time and reputation – acquiring the necessary devices to achieve comprehensive quality control, or to notice too late that the gas fill rates are too low and there might be a need to face the replacement of all delivered units. You will probably quickly come to the conclusion that any quality control equipment is well worth their price.”, Mr. Andreas Kotzke says.
Future of the insulating glass industry
Because of the increasing global competition and customers’ higher expectations for insulating glass performance, we are likely to see a development towards a 100% quality controlled and documented IGU’s for the both ends of the "double stage" system; self-control of IG production and external control by accredited testing institutes.
The development will be driven by the “high value” providers for architectural glazing. As soon as this trend will take an affect, also the “mass production” will follow suit.
“I strongly believe that there is a need to have integrated solutions to achieve automated testing during the IG-production. Glass is a fascinating material with seemingly unlimited design options, and therefore deserves our highest efforts to keep the DACH area in the lead for technology and progress. Sparklike Laser™ devices can support this in a very effective way. Furthermore, they have the possibility to bring quality standards to the next level”, Mr. Andreas Kotzke says.
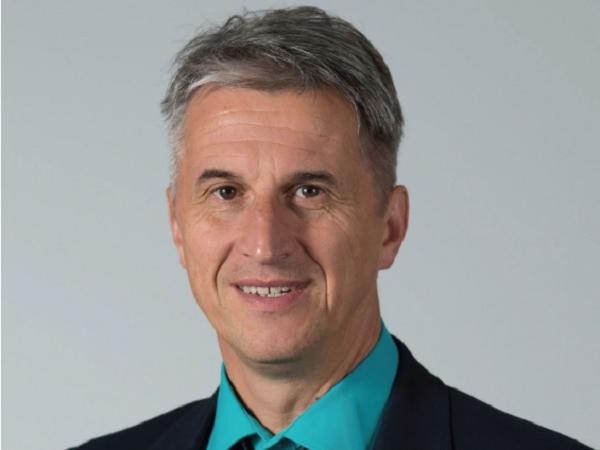

Add new comment