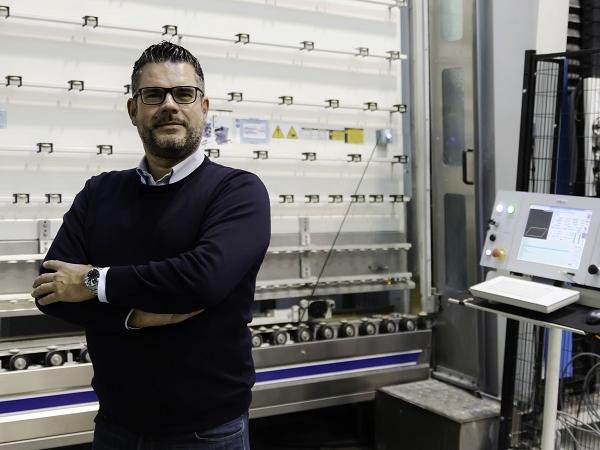
Date: 20 February 2019
The glass balustrades of the Tour Odeon Skyscraper of the Principality of Monaco, the interior of the Doha Airport in Qatar, the new BBC Headquarter, the facades of the Manchester University in the U.K., the glasses for the Winter Garden in the “Shard” tower of London and for the cruise ships of Costa Crociere, Princess, Carnival Cruise Lines…
These are just a few projects accomplished by Formator Ltd, glass factory from Rijeka (Croatia). The company employs approx. 70 people and it is focused on special glass installations (laminated, tempered, electrically heated, screen-printed, etc.) to be used in innovative buildings, following very straight quality requirements.
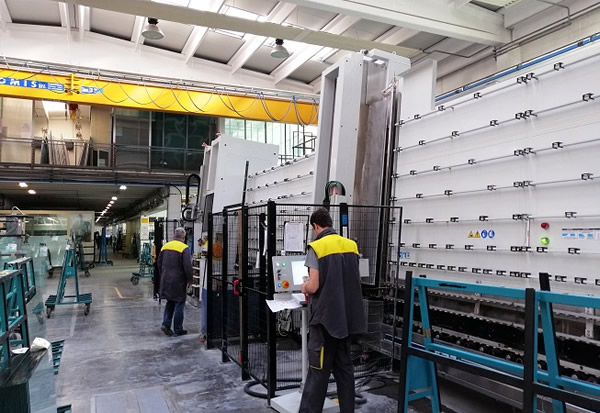
“Our company was established 15 years ago” explains the owner Mr. Robert Miklus “From the very beginning we started competing in the international market, offering superior quality and precision. Our glasses are now in some of the most innovative and luxurious architectures in the world: buildings where the tolerance limits for the glasses are near zero”
For the edging, drilling and milling of the glasses, Formator uses a vertical processing line by Forel. The line is composed by the edging machine Art. EM (for seaming, grinding and polishing), the drilling and milling machine Art. DM and the washing machine Art. VW.
Why did you choose the Forel line, made up of three different machines, instead of a single machine which collects together the different processes?
“Because we needed the highest possible precision and we found it just in this line. We are experiencing a trend of continuous research of innovation and originality in the architecture: actually, there is an impressive creative impulse from designers and architects. When we receive an order for an innovative project, it is never a “standard” order, with the same “recipe” for 100, 1.000 or more glass sheets.
Architects order glasses to compose their creations and every sheet could have different size: the final effect requires the maximum precision. Think about serigraphy: sometimes we received orders for huge quantities of different laminated glass panes with serigraphy on both sheets. All the glasses will be placed to create a graphic design; therefore, all the panes have to be extremely precise.
Another common case are the order of “glass fins”. These orders are for laminated glass panes of 2-3 sheets that are very long and tight (up to 4 m x 400 mm), with up to 20 holes per sheet. That means possibly up to 60 holes. If after the lamination process just one hole is not placed in the correct position, the pane has to be discarded. Minimum errors cause not only time and material waste but also a critical delay for the customers”.
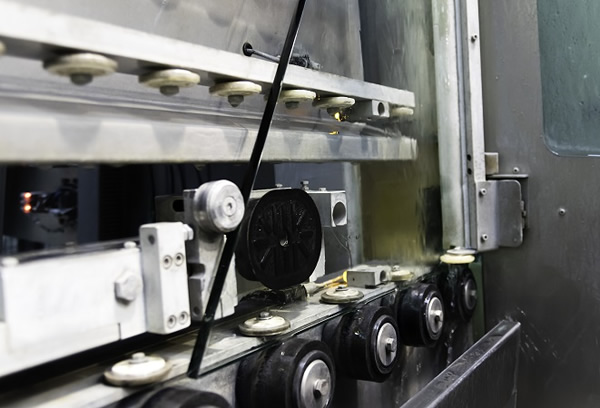
How does the Forel Edge Processing line meet your needs?
“Both the edging, with its patented glass sheet holder feature, and the drilling machine, with its system of fixed and adjustable suction cups, offer an outstanding stability during the processing. The machines are very flexible and work at high productivity always guaranteeing quality and repeatability. And that is exactly what we need.
At first, we were looking just for a drilling machine: we discarded the horizontal solutions, because of the difficulties in the glass positioning and the impossibility to put the drilling machine in line with the traditional edging machinery. So, we started considering brands which offer vertical all-in-one solutions, but we were not convinced about performance and quality. Then, we heard that Forel was designing a new vertical line for edging, drilling and milling and we decided to wait. That was a wise decision: in the last two years, the line has been working without interruption 24/7.
The productivity about shaped and special glasses is quadrupled, giving full satisfaction to us first and foremost, but above all to our customers”
Your core business is “special projects”. That means that you are not processing “common” or low quantity orders?
“Not at all. Indeed, with this line we can be more flexible and manage every kind of request. In the past, when we were working on a big project, it was difficult to put into production new orders in our schedule. Now, instead, the higher performance of our machinery makes everything easier”.
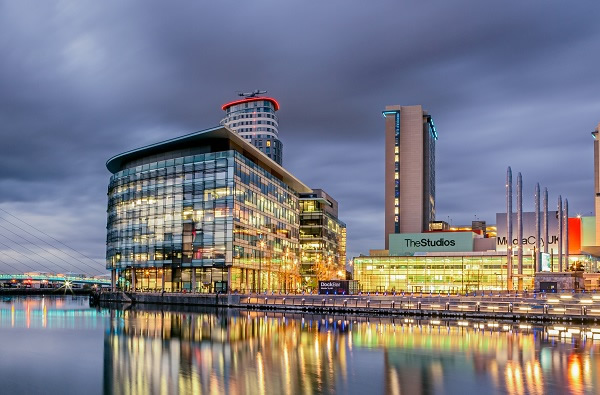
And what about the future?
“We are now in a very positive trend: our adaptability and high-quality standards have been recognized. During 2019 we will enlarge our Rijeka plant with additional 3.000 square meters. We have already ordered a new edging machine and a new washing machine. These new machines will work in line processing those sheets that only need to be polished. Obviously, they will be from FOREL”.
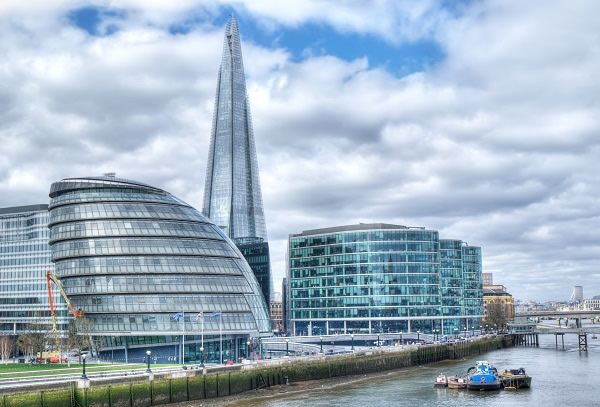
More Info:
https://www.forelspa.com/edge-processing
https://www.formator.hr/
Videos:
Automatic Vertical Edger (Art. EM) from FOREL on Vimeo.
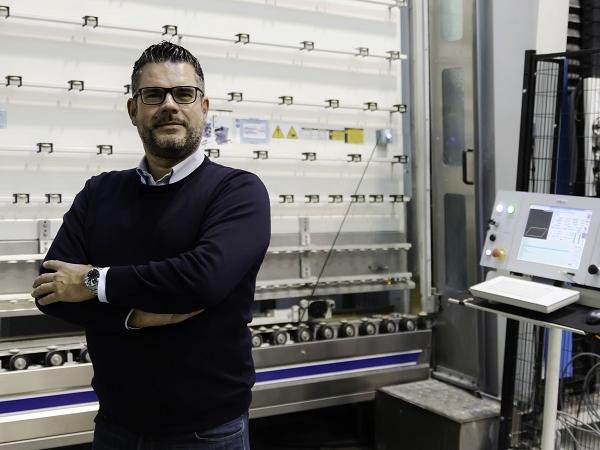

Add new comment