This paper was first presented at GPD 2023 by Maximilian Möckel from Technische Universität Dresden.
Maximilian Möckel is a research associate at the Institute of Building Construction of the TU Dresden. He works at the Institute since 2019 and is part of the research group for structural glass applications. His research topic is the fire resistance of load-bearing laminated glass structures.
Link to the full GPD 2023 conference book: https://www.gpd.fi/GPD2023_proceedings_book/
Authors
- Maximilian Möckel - Technische Universität Dresden, Institute of Building Construction, Dresden, Germany
- Hermann Wegmann - Hero-Fire GmbH, Dersum, Germany
- Andreas Hotes - Hero-Fire GmbH, Dersum, Germany
- Michael Engelmann - Technische Universität Dresden, Institute of Building Construction, Dresden, Germany
Abstract
Glass is a fascinating material with maximum transparency and high strength. All-glass structures and glass façades are getting more impressive and increasingly popular with architects and engineers. Nevertheless, the fire resistance of structures made of soda lime silicate glass is still unregulated and not yet comprehensively studied. A common outcome in experimental fire resistance tests is a melted interlayer within a few minutes of exposure to fire. The most relevant safety aspect is lost. From this point of view, the fire resistance of laminated glass beams is negligible. The glass and the interlayer start to melt within the first 10 minutes in case of fire. To meet the high fire requirements, alternative safety systems such as sprinkler systems must be used in most cases. Therefore, new fire-resistant load-bearing glass beams are under development and examined within a joint research project between Hero-Fire GmbH, Taupitz GmbH & Co. KG and Technische Universität Dresden.
This paper presents the conceptual idea of these beams, how they work in case of fire and gives an overview about the possible applications in building industry. Additionally, a guide to assessing the fire resistance of glass structures according to the European standards is included. This guide is a detailed overview of different standards and how they are connected to each other. Furthermore, a detailed list of all necessary experimental examinations to assess the fire resistance of the components is presented. As an outlook, the proposed fire-resistant glass beams will undergo further assessment to proof their fire resistance while maintaining high transparency and strength at the same time.
1. Introduction
Fire safety is an essential part of building design. Especially in Germany, glass structures have to meet high fire safety requirements. In order to stay within a regulated area, most non-regulated structures were built with a secondary safety concept such as additional sprinkler systems. However, these solutions are costly and often fail the architectural concepts. As shown in Figure 1, fire protection engineering can be divided into two parts. The first part is preventive fire protection and the second is defensive fire protection.
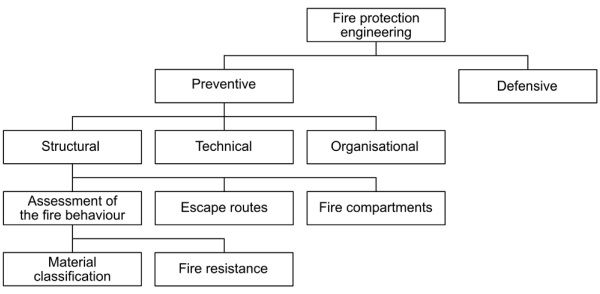
The latter includes all responsibilities of the fire brigade and is not assessed in this paper. Civil engineers focus on the preventive fire protection, which is divided into structural, technical and organisational aspects. Technical fire protection includes all the equipment used to prevent a fire from spreading, such as fire extinguishers or sprinkler systems. Organisational fire protection includes all measures to prepare a company for the event of fire. This comprises fire safety plans, staff training and the marking of escape routes. Finally, structural fire protection is divided in three parts. The first part is the assessment of the fire behaviour by addressing the material class and the fire resistance class. These are regulated in the standards EN 13501-1 [1] and EN 13501-2 [2]. Additional structural aspects include planning the escape routes and dividing a building into fire compartments to prevent the fire from spreading to other areas of the building.
Fire safety is becoming increasingly important with the construction of larger glass surfaces and all-glass structures. There is a lack in research and examination of the fire behaviour of load-bearing glass structures such as glass beams or columns. Therefore, their fire resistance is unregulated. In a research project between Technische Universität Dresden, Hero Fire GmbH and Taupitz GmbH & Co. KG, a new glass beam with a defined fire resistance is under development. This paper describes the beam and its functionality as well as an overview about the standards to achieve safety in use. The combination of these topics result in a guide to assess the fire resistance of laminated glass beams.
2. Basics
2.1 Fire Behaviour of Glass
Fire in a building is an unpredictable and extraordinary event. The design of load-bearing structures in the event of fire is one of the exceptional load combinations according to EN 1990 [3]. In order to represent the temperature of a fire as reproducibly as possible in a fire test, the standard temperature-time curve was developed to EN 1363-1 [4]. This curve represents the temperature that develops during the event of fire over a defined time (Figure 2).
![Figure 2 Standard temperature time curve according to EN 1363-1 [4] in comparison with the transformation temperature of soda lime silicate glass and the glass transition temperature of EVA, SGP and PVB.](/sites/default/files/inline-images/Fig2_334.jpg)
Due to the amorphous properties soda lime silicate glass has no melting point. It has a transformation temperature at which the material changes from a solid to a viscous state. This point is about 530 °C ([5], p.9). For polymeric interlayers like polyvinyl butyral (PVB) this temperature is called glass transition temperature. PVB reaches its glass transition temperature already at room temperature ([5], p.98), ionoplast interlayers, such as SentryGlas® (SGP) at about 50 °C ([6], p.94) and ethylene vinyl acetate interlayer (EVA) at about 110 °C [7]. Figure 2 shows the standard temperature-time curve in black colour. The transformation temperature of soda lime silicate glass as well as the glass transition temperature of EVA, SGP and PVB are represented in the figure as horizontal lines. In comparison with the temperature-time curve, the glass transition temperature of the interlayer materials is too low for a significant influence on the load-bearing behaviour of laminated glass or laminated safety glass. The temperature-time curve reaches the transformation temperature of soda lime silicate glass within the first 5 min. The overview shows that the loadbearing behaviour of laminated safety glass in case of fire is limited by the transformation temperature of the used glass type as the interlayers glass transition is transcended at very low temperatures.
2.2. State of the Art and Standardisation
Fire compartments are separated from each other by fire walls. Mostly, these fire walls consist of concrete or other fire-resistant materials that can endure fire 30 min or more. To meet demands of high transparency, partition walls made of glass are required. To meet fire protection requirements, fire-resistant glazing is applied. They are state of the art and can be found in many variations from different manufacturers. Figure 3 a) shows a photo of a fire-resistant glazing with partially foamed gel. In addition, the figure shows two schematic illustrations of the composition of two different fire-resistant glazing. Figure 3 b) illustrates a multiple layer glazing that consists of multiple glass panes with thin interlayers of fire-resistant gel. Figure 3 c) shows a single layer glazing that consists of two glass layers with a thicker interlayer. In both variants the glass panes are separated with a special spacer.
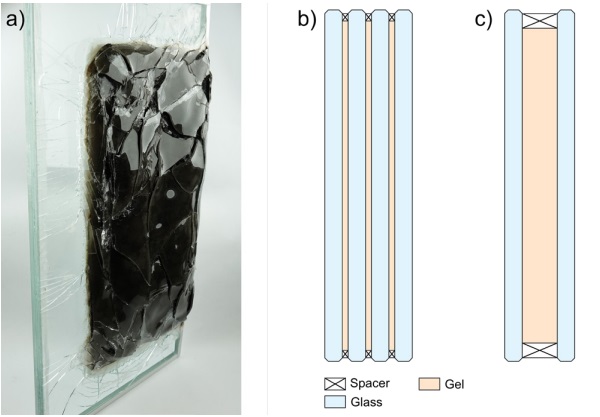
To provide the room closure EN 13501-2 [2] defines three classes of fire-resistant components – E, EW and EI. Figure 4 illustrates their functionalities. Numbers such as “E30” or “EI60” label the minimum time during which the component have to meet its requirements in case of fire. Class E has the lowest requirements. These components just prevent fire and smoke from spreading to the next fire compartment. EN 13501-2 [2] defines three failure modes for components with class E.
- The formation of gaps and openings larger than permitted.
- The ignition of a wad of cotton wool held to the side away from the fire.
- The persistent ignition on the side away from the fire.
![Figure 4 Fire resistance classes of components with room closure requirements according to EN 13501-2 [2].](/sites/default/files/inline-images/Fig4_308.jpg)
Components of class EW have to meet the requirements of class E. In addition, the heat radiation through the component is limited to 15 kW/m². According to EN 1363-2 [8] this value is measured at a maximum distance of 1 m from the component during test. The third class EI has the highest requirements. EI-components have to meet the requirements of E and W. “I” stands for insulation. EN 13501-2 [2] defines two failure modes. The temperature change compared to the initial temperature may only be a maximum of 140 K on average and a maximum of 180 K at one point.
The requirements of class E can be met with monolithic glass panes such as heat strengthened glass made of soda lime silicate or borosilicate glass. Monolithic glass panes are also used for class EW. These are provided with a special thermal insulation coating to meet the limitation on radiation. Due to the high requirements for class EI, monolithic glass panes cannot be used. The use of special fire-resistant glazing is required. These constructions are similar in structure to insulating glazing. They consist of two glass panes connected with an edge seal. The cavity is filled with a special fire-resistant gel, which expands when exposed to heat. This gel consists mostly of water and salt. In the event of a fire, the gel foams up. The water cools the side facing away from the fire. The salt encrusts and forms an opaque insulating layer. With this technique, up to 120 min heat insulation can be provided. Figure 3 shows a fire-resistant glazing where the gel has already foamed up.
3. Fire-resistant glass beams
3.1. State of the research
The fire behaviour of glass and especially loadbearing glass is largely unresearched. Just a few publications focus on this topic. Veer and Bokel ([9] and [10]) were among the first to examine the behaviour of load-bearing glass under fire load. Other works such by Kozłowski et al. and Sjöström et al. ([11] and [12]) examined the influence of the combination of timber with load-bearing glass elements on the fire behaviour of the structure. Louter et al. focused on the load-bearing behaviour of laminated glass beams itself ([13] and [14]). They examined the fire performance of glass beams in both experimental and numerical studies. Extended research of these studies can be found in the publications by Möckel et al. ([15] and [16]). Sturkenboom shows in his master thesis also experimental fire performance tests on laminated glass beams [17]. In addition, first ideas and construction details about protecting the glass beam from the heat of fire were shown in this work. Especially possible applications for the use of fire-resistant glass beams were shown. The different test set-ups of Louter ([13] and [14]) and Sturkenboom [17] are not comparable to each other. The outcome of the tests of Sturkenboom [17] and Möckel et al. ([15] and [16]) reveal specimen failure after maximum 25 min due to melted glass panes.
3.2. Composition and functionality
Within the presented research project, many different compositions of the glass beam were engineered. One of them is shown in Figure 5. The left image shows its composition. The load-bearing structure consists of a laminated safety glass made of three annealed glass panes 8 mm thickness each and standard PVB interlayers of 1.52 mm thickness each. This laminated glass beam is encased in a gel layer with a thickness of 3 mm, except both front sides and the top edge. In case of application, these three areas are protected within the support. To build a formwork for the gel, sacrificial fully tempered glass panes of 4 mm are applied on the outside. The gap between the glass panes is filled with silicone that seal the gel.
Figure 6 shows the functionality of the fireresistant glass beam. In case of fire, the concept is that the sacrificial glass panes break first due to the high temperature differences between the surface and the supporting surfaces. Afterwards, the gel starts to react and foams up. The resulting insulating layer protects the load-bearing laminated safety glass in the core of the structure. The outer protective and sacrificial layers of the composite protect the inner load-bearing core from excessive temperature rise (Figure 6 c)). This will maintain the structural resistance for a longer period of time.
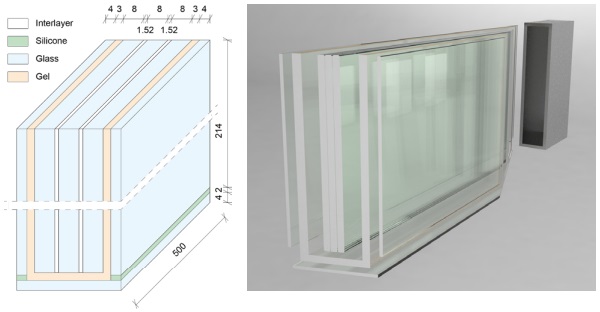
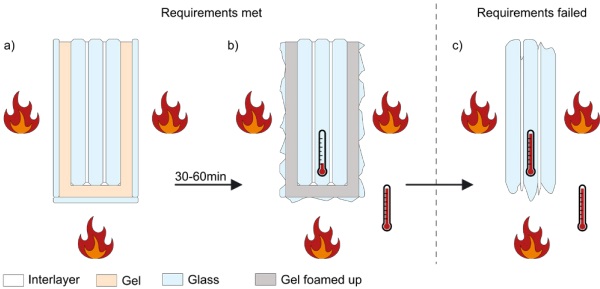
3.3. Application
Figure 7 shows three examples to get an overview of the possible applications of this new glass beam. Picture a) presents a glass floor and a glass roof in the Museum Hotel in Nashville USA made of the GPX firefloor system from Safti First®. Picture b) shows two glass floors in Terminal 2 of the airport Cologne Bonn in Germany. Picture c) presents a fire compartment separation in a parish home in Aufkirchen in Germany made of fireresistant glazing. In all examples the glass panes are supported by metal or concrete beams to meet the high fire requirements. The vision in the research presented is to replace the load bearing beams with structural glass beams with a specific fire rating to increase the overall transparency and provide safe and reliable architectural options in this field.
A glass roof is another promising application opportunity for the fire-resistant glass beams. More and more roofs consist of glass to increase the transparency of the building and to harvest more natural light in foyers or courtyards. Even courtyards that were designed without a roof become more attractive with a retrofitted glass roof, so that the area can be used even in bad weather. One example is the glass roof of the courtyard of the Federal Ministry of Health in Berlin, Germany (Figure 8). These roofs often have to meet fire requirements such as separation of the courtyard to the rising walls from the rest of the building.
![Figure 7 Application examples of fire-resistant glass beams: glass floor and roof in Museum Hotel in Nashville, USA [18] (a), glass floors in Terminal 2 airport Cologne Bonn, Germany [19] (b), fire compartment separation in a parish home in Aufkirchen, Germany [20] (c).](/sites/default/files/inline-images/Fig7_255.jpg)
![Figure 8 Glass roof of the courtyard of the Federal Ministry of Health in Berlin, Germany [21].](/sites/default/files/inline-images/Fig8_221.jpg)
3.4. Standardisation and guide to assess the fire behaviour
The general use of laminated glass beams is unregulated in European standards even so they are quite common and popular. Examples are the House of European History in Brussels, Belgium, the Hungarian Academy of Arts [22] or the entrance of the Tottenham court road station [23]. In Germany, these components can only be used with individual approvals. Therefore, the original structure or at least the relevant part must be tested for structural stability in cost intensive component tests. The future Eurocode 10 part 3 [24] will define the structural design of in plane load-bearing glass elements such as beams or columns without fire protection requirements. In addition to the structural design requirements, the fire-resistant beam has to meet the fire requirements as well in harmonisation to European product declarations to get the CE symbol. According to European construction products regulation 305/2011 [25], the structure has to meet five main requirements in the event of fire.
![Table 1 Overview of the required tests to define the construction product class according to EN 13501-1 [1].](/sites/default/files/inline-images/Tab1_213.jpg)
- The load-bearing capacity can be assumed for a specific period of time.
- The generation and spread of fire and smoke within the structure are limited.
- The spread of fire to neighbouring structures is limited.
- Occupants can leave the building or be rescued by other means.
- The safety of rescue teams is taken into consideration.
With regard to the fire-resistant glass beam, the first three bullet-points are important for further examinations. More specifically, EN 13501-2 [2] defines the specific failure modes in the ultimate limit state during a fire event. The load-bearing capacity is regulated in fire resistance class R. Part 7.2.4 [2] specifies the requirements for beams in general. The standard limits the maximum deflection and the maximum deflection rate using the following two equations.
With
L … clear span of the beam
d … height of the beam
If the specimens exceed one of the limit values (maximum deflection or maximum deflection rate), the test is finished. The measured time defines the fire resistance class (e.g. if the specimen fails after 35 min, it is declared as “R30”). EN 1363-1 [4] specifies the number of specimens, the furnace temperature and the test set-up. The latter has to be carried out in a way that is reproducible and mimics the installation situation of the beam in the building as close as possible.
Requirements 2 and 3 lead to the definition of the construction product classes. The European regulation 96/603/EC [26] defines glass, laminated glass and laminated safety glass as non-combustible (class A1 according to EN 13501-1 [1]). For other components like the complete structure of the fire-resistant glass beams the standard specifies various tests. Depending on the construction product class of the component maximum two tests have to be carried out. Table 1 provides an overview about the necessary tests for defining the construction product class according to EN 13501-1 [1]. According to the limit values in EN 13501-1 [1], the tested components are assigned to the corresponding class.
The last two items in the list of requirements (4 and 5) of the European construction products regulation 305/2011 [25] can be met by using the fire-resistant glass beam for loadbearing structures above or beneath escape routes. These points do not define specific material requirements, but building design requirements. Therefore, they have to be considered in the specific context of a building and are not subject of this research.
4. Summary and Outlook
To extend the range of possible applications of transparent glass structures, the Institute of Building Construction of Technische Universität Dresden is developing a new laminated glass beam to use it safely even in the event of fire. The composite is a glass beam that is encased by fire-resistant gel. In the event of fire, the gel reacts, foams up and cools the inner load-bearing layers of the glass beam. This paper introduces the composition of the new beam and discusses possible applications. In addition, the paper provides a guide to design according to European standards and assesses the main requirements for fire protection.
The current results show that neither the use of load-bearing glazing nor fire-resistant glazing with in-plane load is permitted in Europe. However, these considerations referred exclusively to European standardisation. National standards were not taken account. The use of these structures requires special national approvals. Therefore, Eurocode 10 part 3 [24] is currently in progress. It will regulate the use of glass structures with in-plane load such as beams or columns but without additional remarks on design requirements in case of fire.
Although most Eurocodes, such as those for steel, timber or reinforced concrete, have a part 1-2 (e.g. EC 3-1-2 [31]) in which the structural design in case of fire is considered. Due to the very present and important topic of the fire protection engineering, further examinations may focus on that for a safe use of glass structures even in the event of fire. For the development of the new fire-resistant glass beam at Technische Universität Dresden the existing standards EN 13501-1 [1] and EN 13501-2 [2] are considered in the examinations.
The next steps in the project are testing specimens in temperature and four-point bending tests to examine effect of the gel and the sacrificial glass layers around on the structural properties of a laminated glass beam. In addition, further temperature tests are planned. In these tests, the temperature gradient of different types of monolithic glass panes, laminated glass panes or fire-resistant glazing will be examined. In parallel, numerical simulations examine the temperature transition through glass. The experimental examinations will validate the numerical models. The aim of this procedure is the precise simulation of the new fire-resistant glass beam in the event of fire with the intention to reduce the number of temperature and fire tests. This causes in less emissions and less use of gas and energy for the fire tests. This will prepare ground for future standardization of structural glass elements during fire.
5. Acknowledgements
The research is part of a joint research project between Hero-Fire GmbH, Taupitz GmbH & Co KG and the TU Dresden, supported by the German Federal Ministry of Economic Affairs and Climate Action.
6. References
[1] EN 13501-1, ‘Fire classification of construction products and building elements – Part 1: Classification using data from reaction to fire tests; German version; European Standard’, Beuth Verlag GmbH, Berlin, 2019.
[2] EN 13501-2, ‘Fire classification of construction products and building elements – Part 2: Classification using data from fire resistance tests, excluding ventilation services; German version; European Standard’, Beuth Verlag GmbH, Berlin, 2016.
[3] EN 1990, ‘Eurocode 0: Basics of structural design; German version; European Standard’, Beuth Verlag GmbH, Berlin, 2021.
[4] EN 1363-1, ‘Fire resistance tests – Part 1: General requirements; German version; European Standard’, Beuth Verlag GmbH, Berlin, 2020.
[5] J. Schneider, J. Kuntsche, S. Schula, F. Schneider, and J.-D. Wörner, Glasbau: Grundlagen, Berechnung, Konstruktion. Berlin: Springer-Verlag, 2016. doi: 10.1007/978-3-540-68927-0.
[6] M. Kothe, ‘Alterungsverhalten von polymeren Zwischenschichtmaterialien im Bauwesen’, 2013.
[7] Folienwerk Wolfen GmbH, Ed., ‘Datenblatt evguard MPE’. 2023. Accessed: Mar. 31, 2023. [Online]. Available: https://www.evguard.de/images/download/Datenblaetter/NEUETDS/evguard-MPE.pdf
[8] EN 1363-2, ‘Fire resistance tests Ð Part 2: Alternative and additional procedures; German version; European Standard’, Beuth Verlag GmbH, Berlin, 1999.
[9] F. A. Veer, M. van der Voorden, H. Rijgersberg, and J. Zuidema, ‘Using transparent intumescent coating to increase the fire resistance of glass and glass laminates (zie ook BIM)’, Glass Process. Days, no. 1, pp. 392–396, 2001.
[10] R. M. J. Bokel, F. A. Veer, and L. Tuisinga, ‘Fire resistance of glass’, Glass Process. Days Educ. Glass Conf., no. 1, pp. 362–363, 2003.
[11] M. Kozlowski, P. Lenk, M. Dorn, D. Honfi, and J. Sjöström, ‘Structural Considerations on TimberGlass Composites at Fire Scenarios: Challenging Glass Conference Proceedings, Vol. 6 (2018)’, Challenging Glass Conf. Proc., no. 6, pp. 229–240, 2018, doi: 10.7480/cgc.6.2150.
[12] J. Sjöström et al., ‘Fire Resistance Testing of a Timber-Glass Composite Beam’, Int. J. Struct. Glass Adv. Mater. Res., vol. 4, no. 1, pp. 24–40, 2020, doi: 10.3844/sgamrsp.2020.24.40.
[13] C. Louter and A. Nussbaumer, ‘Fire Testing of Structural Glass Beams: Initial Experimental Results’, in 2016 GlassCon Global Proceedings Book, LLC. FCA Conferences, Ed., Chicago, 2016, pp. 143–150.
[14] C. Louter, C. Bedon, M. Kozlowski, and A. Nussbaumer, ‘Structural response of fire-exposed laminated glass beams under sustained loads; exploratory experiments and FE-Simulations’, Fire Saf. J., no. 123, 2021, doi: 10.1016/j.firesaf.2021.103353.
[15] M. Möckel, K. Lohr, and C. Louter, ‘Exploratory Study on the Load-Bearing Behaviour of Laminated Glass Beams Exposed to Fire’, Challenging Glass Conf. Proc., vol. 8, Jun. 2022, doi: 10.47982/cgc.8.444.
[16] M. Möckel, T. Juraschitz, and C. Louter, ‘Numerical simulation of the heat flow through laminated glass beams exposed to fire — a parametric study’, in Current Perspectives and New Directions in Mechanics, Modelling and Design of Structural Systems, 1st ed.London: CRC Press, 2022, pp. 872–877. doi: 10.1201/9781003348443-143.
[17] J. Sturkenboom, ‘Fire Resistant Structural Glass Beams’, Masterarbeit, Delft University of Technology, 2018.
[18] ‘1-Hour Fire Resistive Glass Floors Case Study | SAFTI FIRST’, SaftiFirst. https://safti.com/casestudies/fire-resistive-glass-floors-make-a-dramaticstatement-in-nashvilles-historic-neighborhood/ (accessed Apr. 04, 2023).
[19] D. Kriesel, ‘Flughafen Köln-Bonn: Stille, Einkehr, Dystopie’, D. Kriesel, May 05, 2020. https://www.dkriesel.com/blog/2020/0505_flughafen_koelnbonn_stille_ einkehr_dystopie (accessed Apr. 04, 2023).
[20] C. Baart, ‘Pfarrheim Aufkirchen - Architekturobjekte - heinze.de’. https://www.heinze.de/architekturobjekt/pfarrheimaufkirchen/12766979/ (accessed Apr. 04, 2023).
[21] C. Wolf, ‘Bundesministerium für Gesundheit, Berlin’. https://www.windeck.de/referenzen/lichtdaecher/2022-bundesministerium-fuergesundheit-berlin.html (accessed May 02, 2023).
[22] GLASSCON GmbH, ‘Hungarian Academy of Arts Structural Glass Atrium (Hungary)’, Glasscon. https://www.glasscon.com/projects/hungarianacademy-of-arts-structural-glass-atrium-hungary/ (accessed May 04, 2023).
[23] seele holding GmbH, ‘Tottenham Court Road Station – Plaza Entrances’, seele fassadenbau. https://seele.com/de/referenzen/tottenham-courtroad-station-plaza-entrances (accessed May 04, 2023).
[24] CEN TS 19100-3, ‘Design of glass structures - Part 3: Design of in-plane loaded glass components and their mechanical joints (Draft)’, European Committee for Standardization, Brüssel, 2021.
[25] European Parliament, Regulation (EU) No 305/2011 of the European Parliament and of the Council of 9 March 2011 laying down harmonised conditions for the marketing of construction products and repealing Council Directive 89/106/EEC (Text with EEA relevance)Text with EEA relevance. 2021. Accessed: Apr. 05, 2023. [Online]. Available: http://data.europa.eu/eli/reg/2011/305/2021-07-16/eng
[26] European Parliament, Commission Decision of 4 October 1996 establishing the list of products belonging to Classes A ‘No contribution to fire’ provided for in Decision 94/611/EC implementing Article 20 of Council Directive 89/106/EEC on construction products (Text with EEA relevance) (96/603/EC). 2003. Accessed: Apr. 05, 2023. [Online]. Available: http://data.europa.eu/eli/dec/1996/603/2003-06-12/eng
[27] EN ISO 1182, ‘Reaction to fire tests for products – Non-combustibility test; German version; European Standard’, Beuth Verlag GmbH, Berlin, 2020.
[28] EN ISO 1716, ‘Reaction to fire tests for products – Determination of the gross heat of combustion (calorific value); German version; Euopean Standard’, Beuth Verlag GmbH, Berlin, 2018.
[29] EN 13823, ‘Reaction to fire tests for building products – Building products excluding floorings exposed to the thermal attack by a single burning item; German version; European Standard’, Beuth Verlag GmbH, Berlin, 2020.
[30] EN ISO 11925-2, ‘Reaction to fire tests – Ignitability of products subjected to direct impingement of flame – Part 2: Single-flame source test; German version; European Standard’, Beuth Verlag GmbH, Berlin, 2020.
[31] EN 1993-1-2, ‘Eurocode 3: Design of steel structures – Part 1-2: General rules – Structural fire design; German version; Euopean Standard’, Beuth Verlag GmbH, Berlin, 2010.