This paper was first presented at GPD 2019 by Liang Zhang, Hongxia Zhang, Aifen Wang, Yan Zhao and Yanbing Li from LandGlass, China.
This paper is focused on the main advantages of vacuum glass comparing the characteristics such as sound insulation, thermal transmission and anti-condensation with insulated glass based on the application area of vacuum glass. In addition, the comparison between the insulated glass and vacuum glass from 1999 to 2018 is made by published patents to state the future of energy efficient glass. The key technology of vacuum glass and the trend are also clarified for the current vacuum technology.
1. Introduction of VIG
The typical VIG structure is constituted with two pieces of glass which are separated by pillars with height of 0.1 to 0.5mm, the edge is connected with solder to be able to sealed as a vacuum chamber, which contains less than 0.1pa pressure. In order to keep the stability of vacuum degree, the getter is applied inside of the vacuum chamber. As of now the current VIG in the market are made by using the following two steps
1) Sealing the edges of glasses;
2) Sucking the air out from the reserved sucking inlet for about one to three hours, and then sealing up the inlet to form a vacuum chamber.
With different original clear glass pieces, come with a huge difference of heat transfer performance on the VIG structure (shown Figure 1). As is shown in Table 1, if anyone of the glass is low-E glass, the thermal performance of the VIG would be increased significantly and its coefficient of heat transfer would be decreased to 0.4 W·m-2·K-1.
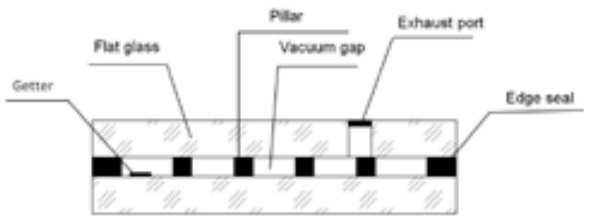
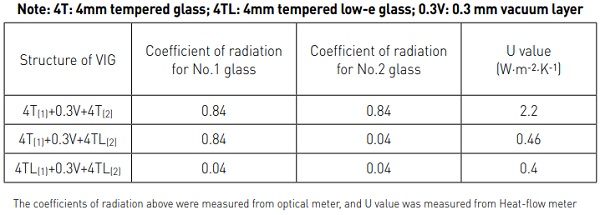
Since 1913 A.Zolleret al. first proposed the concept of VIG, with over 100 years of development, the VIG has walked out from laboratory to industrialization and become a new generation of energy-saving glass. As is shown in Figure 2, in Chinese market, there were only five VIG patents were disclosed in 1999, and the concept of VIG was just initially brought up; however, the number of VIG patents had reached 363, and the number of VIG patents had accounted for 29.73% of the total number of patents that related to energy-saving glass by the end of 2015, thus the VIG had played more and more important roles in the energy saving field.
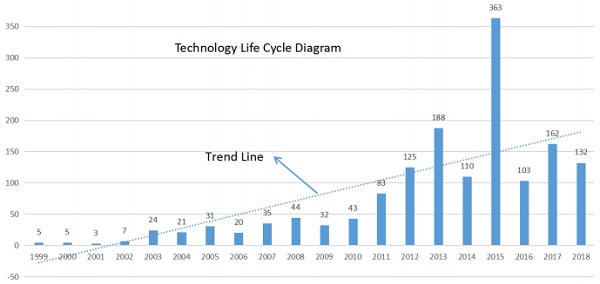
From 1999 to 2018 in China, the number of VIG patents has increased numerously and from global site, there were 35 VIG patents disclosed outside China, which maintains the same growth tendency with the number of China’s domestic patent disclosure in 2015. Therefore, VIG will become the main direction of development on energy saving glass in the future.
2.The advantages of VIG
Because of its high vacuity, VIG has performed excellent heat insulation, anti-condensation, and sound insulation to the world.
2.1 Heat insulation
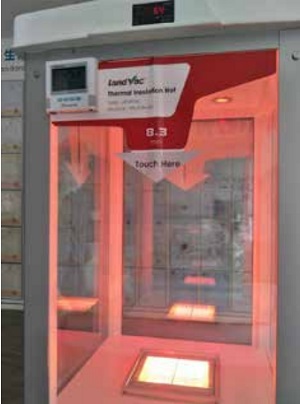
From the point of view of VIG structure: the edge is soldered, and the center is separated by supports to become a vacuum chamber; As a result of the above structure, the heat transfer coefficient in the central area of the VIG is far less than that its edge, and considering to practice in the reality , the heat transfer in the edge is associated with window frames material. Therefore, the U value in the central area of the glass is only measured for the sake of parameter comparability.
The heat transfer in the center of the VIG is conducted by radiation, supports contact and gas residual. According to The Vacuum Insulated Glazing heat transfer coefficient and the calculation of the condensation temperature by Jianzheng Tang, when the vacuity is less than 0.1 Pa, the heat transfer from residual gas can be ignored, thus the heat transfer coefficient of VIG is determined by the emissivity of glass as shown in Formula 1.
For insulated glass, the heat transfer is determined by both the air heat transfer and the radiation of the glass, but the air heat transfer is dominant. The heat transfer of insulated glass is much higher than that of VIG from the original glass with the same emissivity based on Table 2.
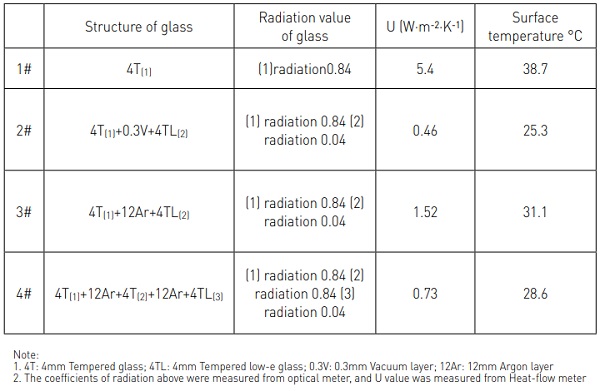
On the basis of glass structure in Table 2, the Vacuum observation box has showed better insulating ability by comparing with the observation box which made by other material; when the outside temperature is 25 °C, the temperature inside kept 60± 5 °C with an hour, the VIG (2 # observation window) of the surface temperature is 25.3 °C which nearly consistent with the outdoor temperature.
Note: R1 thermal resistance of inside glass; R2 thermal resistance of outside glass; Rradiation thermal resistance of radiation; Rsupport thermal resistance of support; Rair thermal resistance of gas residual; Rvacuum thermal resistance of VIG; Cvacuum conductivity of VIG.
2.2 Anti-condensation
Anti-condensation performance includes two parts:
1) The VIG is sealed all around and there would be impossible for condensation in the vacuum layer.
2) While outside temperature is low, inside is high; therefore, the temperature on the surface inside of the VIG layer is higher than dew point temperature, so even the outdoor temperature is low, the inner layer of VIG will not be condensate.
The condensation performance between insulated glass and VIG was compared in Table 3, and the result came to be better anticondensation performance of VIG. Under the condition of 25 °C inside and the humidity of 75%, when the VIG starts to condensate, the temperature outside has to be blow -69.5 °C; however with insulated glass, the critical temperature only needs to be reached at -4 °C.
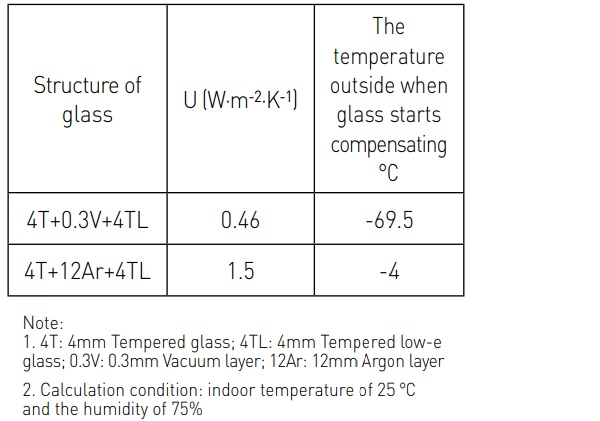
2.3 Sound insulation
According to building sound insulation measurement standard(GBJ75-1984) , the size of 550 x 650 mm VIG with thickness of 10.3mm is chosen for its sound insulation performance test by using the free field microphone BSWA BK2716, 3560B, amplifier BK2716 and Omnidirectional sound source BK4296 in the reverberation chamber and anechoic chamber. The acoustic curve could be illustrated through the computer and sound calibrator 4321 with sound insulation quantity calculated by 1/3 octave, as is shown in Figure 4.
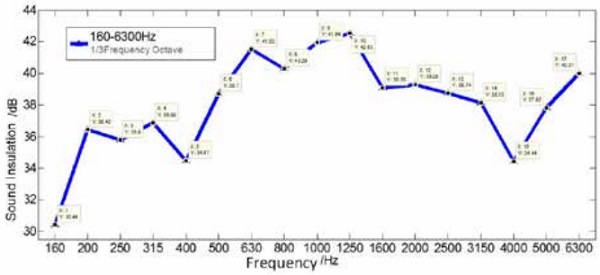
As can be seen from Figure 4, in the range of 160-6300hz the acoustic insulation performance less than 500Hz is relatively low. The reason is the low frequency which is more likely to cause the vibration of the glass, and the sound energy is transferred from one side to the other side through the pillars.
At the frequency range from 500Hz to 3150Hz, the sound insulation of glass is relatively high. The maximum is 42.5db at 1250Hz while the minimum is at 35dB. The sound transmission loss of 5+ 0.3V +5 VIG is 39dB, that of 5+9A+5 insulated glass is only 26dB, and that of 5+0.76p +5 laminated glass is 32dB, Therefore, the sound insulation performance of VIG is obviously better than laminated glass and insulated glass.
3. The technology development tendency of VIG
Patents are not only to have commercial value, and to protect the legitimate rights and interests of inventors, but also directly reflect relevant technical concerns and development trends. Through the analysis of 167 VIG-related patents published internationally in 2018, the composition of its patented technology is refined, and the development trend of VIG in the future is clarified as well.
3.1 Flexible sealing technology
In the published literature, VIG sealing technology includes metal sealing, glass powder sealing, metal with organic adhesive sealing, metal with glass powder sealing, organic adhesive sealing, glass powder with organic adhesive sealing, resin sealing and other processes. Among the patents made public in 2018, eight patents concerning metal material sealing were made public, accounting for 40% of the whole sealing method patent, and it became the new technology focus.
In order to realize the flexible connection of the two glass sheets, to reduce the sealing force, and to slow down the deformation of the VIG at the same time caused by the temperature difference between inside and outside, the metal materials are applied for edge sealing of the VIG. Metal sealing VIG has been seen in the market at present, the method is to sinter at the high temperature first, to form a dense metal layer on the surface of VIG as shown in the following figure, and then to combine two sets of glass together with soft solder to become a vacuum chamber.
Although the above sealing structure reduced the edge sealing force and realized the flexible connection, it still needs continuous improvement to achieve the true flexible sealing technology which is no stress at the sealing edge and no restrain in the process of thermal expansion for the glass. The microstructure of metal layer of a glass sheet is shown in Figure 5.
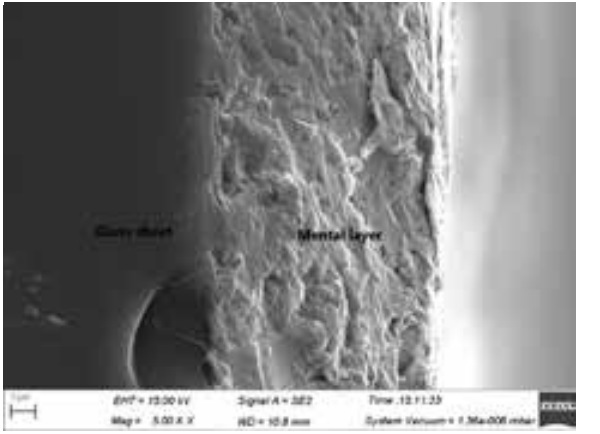
3.2 Tempered VIG
By using the tempered glass sheet to synthesize the VIG, the mechanical strength of the VIG can be effectively improved. However, if the temperature is high or the time is too long, it will lead the tempered glass sheet back to the quenching state in the process of VIG sealing. According to the published data, when the 4.6 mm tempered glass heating 0.5~1 hour in 350 °C, tempered degree retains only 80%. Thus it is very important to develop a solder which can work below 350 °C in the production of tempered VIG.
At present, the tempered VIG in the market is mainly produced by the following two methods: the first one is to use infrared absorption of low glass powder solder; by using infrared radiation to heat glass edge, most areas of the VIG can qualify the tempering state. The second one is to use the traditional process used to seal the glass with metal solder, raising the temperature to 300 °C instantly and keeping the heat for 3 to 5 seconds to make the metal solder melt completely, then the VIG surface and the edge stress can be greater than 90 Mpa.
From the patents released in 2018, it can be seen that more than 60% of the patents focus on tempered VIG, mainly including VIG welding materials, sealing equipments, sealing methods and etc.
3.3 Continuous machining technique
In 2018, there are 31 international open patents in the continuous processing technology field of VIG industry which come to about 18.6% of all patents. Figure 6 shows the technical composition of 31 continuous processing technology patents.
In Figure 6, continuous processing technology mainly includes production line and production process, and the number of patents disclosed are 10 and 21. Compared with 2017, the number of patents doesn’t change much and is basically in a stable state. It means the continuous processing technology of VIG is in the stage of sustainable development and has not reached the mature stage yet. The continuous production lines still need to be constantly improved to ensure the quality of each piece of VIG, and to achieve greater productivity in the future.
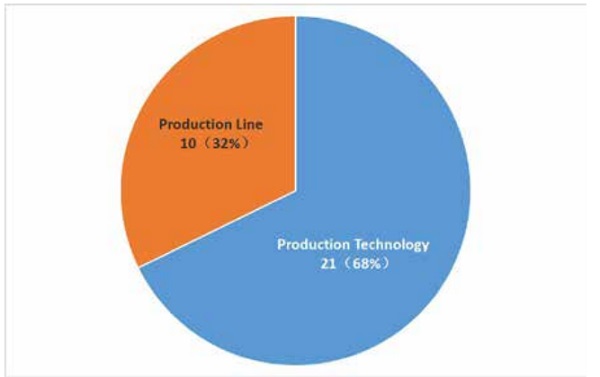
3.4 Composite VIG
The combination of VIG and other glass can further improve the mechanical and optical properties of the VIG, and endow the VIG with certain function at the same time, such as composite laminated vacuum glass which can improve the safety of the VIG and enable the vacuum glass to be used for curtain wall; photovoltaics (BIPV) combine the VIG with the solar PV panel to form the photovoltaic curtain wall; VIG- Electrochromic glass can adjust shading coefficient based on different demands and improve the photothermal performance of VIG.
As can be seen from Figure 7, 22 VIG product application patents were disclosed in 2018, including 15 composite VIG patents, about 68.2% overall which mainly involves VIG-Electrochromic glass, VIG-Coated glass, VIG-Multilayer composite glass, VIGThermochromic glass and VIG-Laminated glass.
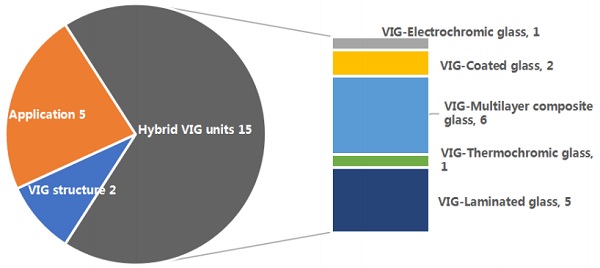
4. Application of VIG
4.1 Application of VIG in home appliances
Creating the artistic value of home appliance products, improving the intelligence of products, reducing pollution and reducing energy consumption are the main design concepts of home appliance manufacturers. Glass is widely used as a component of household appliances due to its excellent physical and aesthetic properties. In 2004, LG refrigerator began to use crystal glass panels instead of plastic and metal panels. Subsequently, Siemens, Panasonic and Gree introduced crystal glass refrigerators and washing machines. In 2018, AWE and LG launched the smart perspective window refrigerator, which adopts the door in door technology.
The perspective window is made of three layers of tempered glass with two layers of argon, the inner tempered glass is Nanocoating with a touching sensor, and presents a mirror effect in general; while using it, the sensor can light up the perspective window by taping twice of the door, and the internal food storage situation can be seen without opening the refrigerator door. By reducing the opening times and the cold air would maintain the same amount, so that the food shall keep fresh for a longer time, and the life of the compressor shall extended as well. Therefore, this device makes the refrigerator not only healthy for people, but also saves the energy for the earth.
In the same year, Siemens, Anthony, and Haier showed a refrigerator with a VIG as the perspective window, but thickness of the panel decreased from 50mm to 30mm, makes the box much thinner and lighter; also the heat transfer coefficient of the window frame decreased from 1.0W·m²·k-1 to 0.45W·m²·k-1, which reduced the energy consumption of the refrigerator; because of the VIG observation window, the refrigerator does not need to install an extra electric heating defogging device, so that the structure of refrigerator can be simpler.
Based on the advantages above, the intelligent refrigerator with VIG as observation window has become the main direction of future development of refrigerator industry. At the same time, VIG as the door of the large refrigerator, wine cabinets have come out, it indicates a good energy saving and anticondensation performance.
4.2 Application of VIG in architecture
VIG has shown absolute performance advantages and wild application prospects in the field of architecture due to its excellent thermal insulation, anti-condensation and sound insulation properties. In 2005, the world’s first office building with VIG curtain wall was completed; in 2006, the world’s first VIG greenhouse was completed; in 2011, the first large-scale library with full VIG was built. Although the buildings with VIG as the wall keep appearing, due to the various ways of VIG sealing methods, some VIG damages and vacuum degree failures also has been seen.
In view of the quality problems in the early stage of VIG, manufacturers constantly optimize the process, improve the stability of equipment. As for the untempered VIG, it can be satisfied the requirement of safe building standards by using insulated glass. In 2014, tempered VIG sealed with metal materials was introduced at first time. It has greatly improved the safety performance of VIG, reduced the sealing stress and the self-explosion rate of VIG. In 2018, 6mm ultra-thin unsealed VIG was exhibited, which represents that VIG would move towards a thinner direction.
At the same time, the VIG product standard was also continuously established and improved. From 2014 to 2017, the general research institute of building materials of China revised TC/T 1079-2008 issued in 2008 and passed the review version in 2017. In December 2014, the Brussels ISO/TC160/SC1/WG10 working group on VIG was established and held its first meeting. In 2018, the ISO19916 standard for building VIG products was released.
5. Summary
Considering the heat transfer coefficient for VIG of 0.46W· m-2 ·K–1, transmission loss of 39dB, and dew point of -69.5 °C with indoor temperature at 25 °C and humidity of 75%, VIG has showed absolute advantage of performance. According to the data that was quoted in the article, the future development trend of VIG technology mainly includes:
1) Flexible sealing is adopted at the edge to reduce the sealing force;
2) Tempered glass is applied to improve the strength and safety of the VIG, while the stress distribution on the surface of the VIG is required to be even;
3) The large-scale production line should be used to ensure the quality stability and reliability of VIG and to lower the cost.
With the constant improvement of producing process of VIG, the improvement of equipment of the manufacturers and consummating standard of VIG, eventually VIG will be more and more mature and will become the main development direction in energy-saving field.