This paper was first presented at GPD 2023.
Link to the full GPD 2023 conference book: https://www.gpd.fi/GPD2023_proceedings_book/
Authors:
- A. Rota - Dipartimento di Ingegneria Civile, Ambientale, del Territorio, Edile e di Chimica (DICATECh), Politecnico di Bari, Bari, Italia
- M. Zaccaria - AGC Glass Europe - Technovation Centre, Gosselies, Belgium
- F. Fiorito - Dipartimento di Ingegneria Civile, Ambientale, del Territorio, Edile e di Chimica (DICATECh), Politecnico di Bari, Bari, Italia
1. Closing the linear life-cycle of post-consumer glass
1.1 Construction & Demolition waste management in Europe
The construction and demolition waste (C&Dw) comprises the largest waste stream in Europe, with a mass of 374 million tonnes, in 2016, excluding excavated soil (EEA, 2020). C&D waste arises from construction and total or partial demolition activities. Despite the effort done by the legislation in promoting circular action and asking for CO2 reduction in the construction sector, the waste management is still characterized by a low value circular process. The Waste Framework Directive of Europe set the target of 70% of recycling for the C&D waste, within the 2020 (DIRECTIVE 2008/98/EC). Although, this target is mostly achieved with backfilling and low-grade recycling operations (EEA, 2020). Moving toward a truly circular economy model means prioritizing the processes with higher environmental benefit, such as reuse and waste prevention (Figure 1).
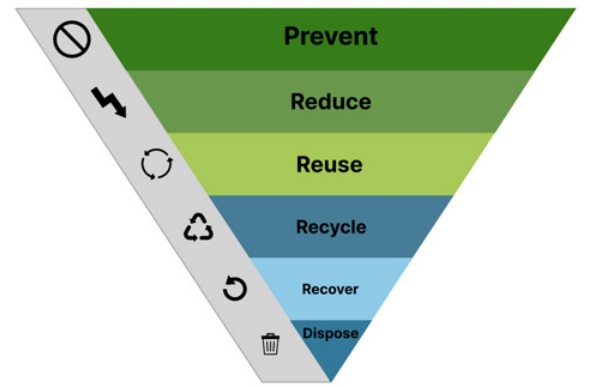
The development of a circular management for the C&D waste calls for a variety of actions, which could be undertaken at the early stage of the materials life cycle (i.e., the design process) or also at the end (i.e., the demolition process). It appears clearly that is necessary to rethink the construction chain. Some examples of possible actions that improve the construction chain are listed below.
- Selective demolition, which enables to remove hazardous materials and increase source separation into high value, pure material fractions;
- Design for disassembly means that buildings are intentionally designed for material recovery. All pieces of the building can be easily separated, and the components and materials reused, recycled or remanufactured;
- Material passport contains a set of data describing defined characteristics of materials and components in building products. It could facilitate the sourcing operation of the materials end-of-life;
- Certification of secondary materials provide a guarantee of their quality level and could help to promote the application of these materials among the stakeholders.
All these circular actions can have important benefit for improving the C&D waste management, but they might also have the same barriers preventing their implementation, such as the lack of regulations and the not well quantified financial benefits compared to normal practices (Geboes et al., 2022). Furthermore, numerous are the technical barriers that needs to be studied and solved to implement these circular actions.
1.2 The linear life cycle of architectural glass
Among the C&D waste, the flat glass is one of the waste fractions characterized by a lower recovery rate. The life-cycle of glass is linear (Figure 2) for two main reasons (DeBrincat & Babic, 2019). Firstly, the post-consumer glass is characterized by inter-connection between glass and other materials (i.e. silicone, butyl, spacer for the case of insulating glazing). The contaminations could generate serious problems during the production and only a limited fraction of pre-consumer glass cullet is currently accepted in the float plant. To reduce the number of contaminants it would be necessary to fully separate the glass material from the other parts of the product. As second main reason the repatriation chain from the consumer to the float plant is deemed to be more expensive and complex than landfill (Geboes et al., 2022).
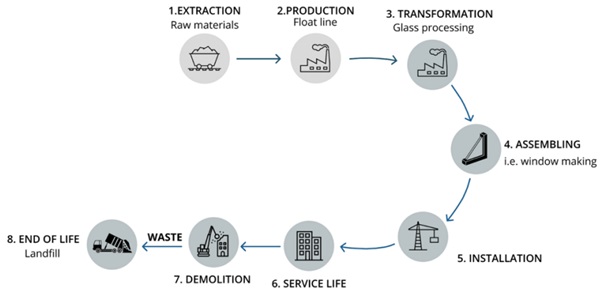
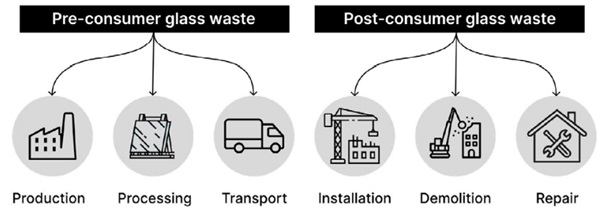
During the open-loop of flat glass the waste generated could be distinguished into two categories (Figure 3):
- Pre-consumer glass waste: is the waste generated before the glass reaches the market, therefore it is generated during the production, processing, transport and placement phase;
- Post-consumer glass waste: waste generated during or after the use, regardless of the cause.
- This research focuses on the management and qualification of the glass waste coming from the post-consumer phase.
1.3 Closing the life cycle of flat glass by remanufacturing Insulating glass unit
The linear life cycle shown in Figure 2 could be closed with the recovery and reuse of the glass panels constituting the IGUs. Figure 4 illustrates all the steps of this reuse process, which involves: the disassembly of the insulating glass from the facade of the building at the end of its service life; the disassembly, or the separation of the glass panels from the other components of the insulating glass; the quality assessment of the glass panels and based on the assessment, it could be decided if the panels should be reused, recycled, or disposed of in landfills (Rota et al., 2023). In this context, AGC and Helga have joined forces to develop a disassembling machine able to separate the panels of an IGU and obtain glass for being re-used or of that qualifies for high quality cullet by not having contaminants (Glass on Web, 2023).
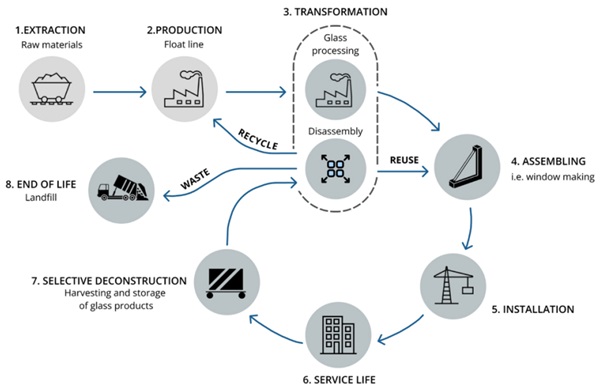
1.4 Qualify the post-consumer glass
A quality assessment for the annealed monolithic glass should consider both the mechanical performance of the post-consumer glass and the surface quality condition. Glass is known for its excellent durability, but its strength is very sensitive to the characteristics of the surface. The glass panels during their service life accumulate a variety of defects on the surface, like punctual and linear defects, which can be invisible to the human eye, but also affect the strength of the glass. Zammit and Overend (2010) investigated and confirmed this aspect by showing that a glass panel, used for about 40 years, has a significantly lower resistance than that of new glass. Besides, they also found that the face exposed outside is more damaged than the face exposed inside.
Datsiou and Overend (2017) also confirmed the phenomenon of strength decreasing and moreover, they compared the naturally degraded glass with the artificially degraded glass in order to determine the state of damage induced to the glass. The qualification of the state of damage of the glass surface is a fundamental aspect, since a quality protocol for the post-consumer glass should be able to qualify the surface of the glass used with a level of detail such that its strength is predictable. In this context, the real challenge is to find a quick and easy way to classify the glass surface.
More recently, by using an optical profilometer and a digital microscope, Sofokleous measured the depth of the glass flaws, followed by CDR analysis. It was found that the technique is effective to measure the flaws depth, but the size of the equipment and the time needed to analyse the data create a problem of scale. With these equipments the investigation could be performed only at a laboratory scale (Sofokleous, 2022). Surface flaws in the form of spot-like or scratchlike defects are commonly inspected during the glass manufacturing processes. In this research, the mechanical and surface quality of post-consumer glass is assessed. The quality classification of the glass surface was made based on the EN 572-8+A1 (2016) surface quality criteria.
2. Method
The mechanical performances of postconsumer glass was evaluated in this study, together with the classification of their surface quality. 43 Insulated glazing were collected form residential building in Belgium, during replacement and refurbishment intervention, and after disassembled manually. The recovered glass was collected with the purpose of performing a quality investigation. The lifetime of the collected glass panes varies in a range of 28 and 41 years. After the collection of the glass panel, the following operations was performed:
- Disassembling of the IGUs;
- Sorting by type and analysis of the glass surface quality;
- Sampling preparation;
- Destructive test.
The manual disassembling of the insulating glass units was performed following the standard practice of the water permeability test of and IGU, as displayed in the EN 1279- 2 (2018). A perimetrical cut of the insulated glazing was done in the space between the sealants and the glass, followed by the components’ separation (glass, spacer and sealants). The portion of the glass polluted by the sealants was completely removed by cutting the glass perimetrically for about 3 cm. Then the glass panes were cleaned with a washing machine and manually washed for removing the hardest dust. The disassembled glass panes were inspected visually and classified by type of glass. This sorting operation was followed for the clear annealed glass by an assessment of the glass pane optical quality using an industrial quality scanner, which is able to provide information about the density of the spot and scratch defects. Based on these information, the glass quality was classified according to the specs summarized in Table 1 and Table 2 for the spot flaws and linear faults, respectively. These metrics correspond to an in-house ranking based on the quality specs specified in the EN 572-8+A1 (2016).
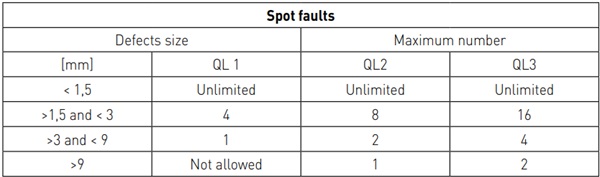
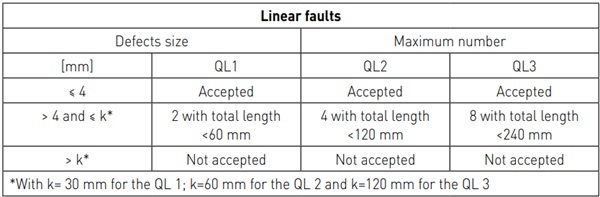
The destructive test of the coaxial double ring (CDR) was used to determine the glass's characteristic bending strength. The international ASTM C1499-03 (2003) standard was followed for performing the test. In particular, the samples sizes were chosen respecting the limits fixed by the standard to ensure that the shear force is negligible compared to the axial forces. As a result, the following ring size combination was used for the test setups:
- 20 mm of loading ring with 80 mm of support ring diameter;
- 40 mm of loading ring with 80 mm of support ring diameter;
- 80 mm of loading ring with 150 mm of support ring diameter.
The samples cutted from the glass panel was after grouped by homogeneous parameter and tested. The quality level and the position of the glass panel in the IGU (i.e., face P1, P2, P3, P4) are the parameters used for grouping the series. In Table 3 is summarized all the tested series and the relative parameters, such as the samples size and the setup of the loading/supporting ring used. Thermal treatment was also performed in this study to the new and post-consumer glass to assess any benefits provided by the thermal healing of defects (Zaccaria & Overend, 2016). The series of “annealed new glass” in the Table 3 represents the batch of new glass, classify with a QL 1, and used as reference for evaluating the performances of the thermally tempered post-consumer glass.
All the glass specimens were tested using a universal testing machine fitted with a 30-kN load cell. Silicone rubber was placed between the supporting ring and the glass specimens to avoid any stress concentration in the glass. To hold the fragments together after the breakage and allow to locate the fracture origin, a selfadhesive film was applied to the side of the specimens facing the loading ring. For the statistical analysis of the test results, only the samples with a fracture origin inside or above the loading ring were considered as valid data.
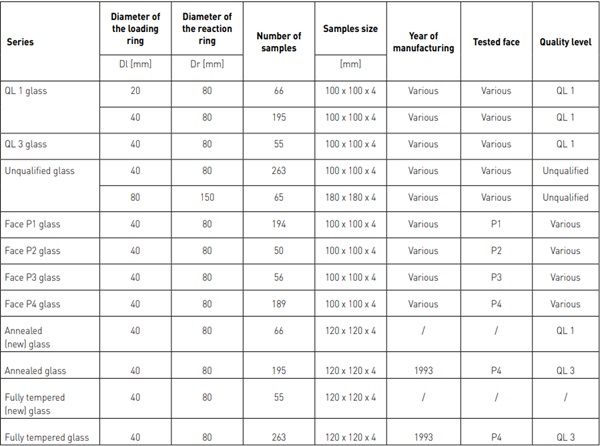
3. Results
The glass panels collected after the disassembling can be sorted in the following types:
5. Annealed clear glass: 79%;
6. Annealed coated glass: 12%;
7. Laminated glass: 9%.
Only the annealed clear glass was inspected trough the scanner, which allowed to classify the surface quality of the panels according to the specs of the three fixed quality levels. The percentage of glass panes classified in the different quality levels is shown in the Table 4.
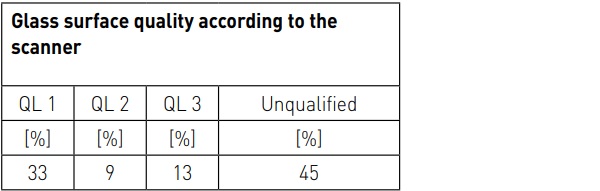
The failure stress data gained from the CDR test were sorted by quality levels or position of the tested face in the IGU and grouped to perform a statistical analysis with a two-parameters Weibull distribution. The parameters were estimated with the Weighted Least Squares Regression (WLR) using the method of moment (Datsiou & Overend, 2018). The characteristic bending stress obtained from this distribution, fg;k, is defined as the stress corresponding to the 95% lower bound interval at the 5% probability of failure. The results of the data analysis are reported in Table 5, including the scale parameter θ, the shape parameter β and the goodness of fit ρAD.
In Table 6 is shown the strength data of the thermally tempered series. To better compare the results of the tempered series, in the table, is also reported the results of the annealed series collected from the same glass panel.
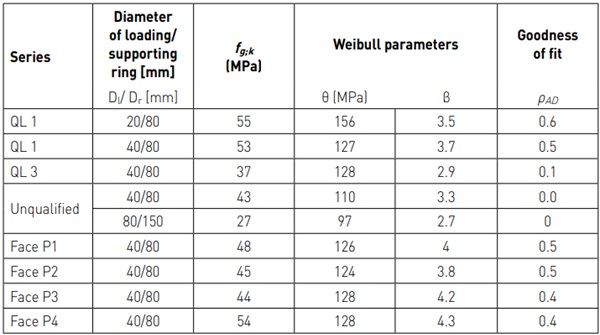
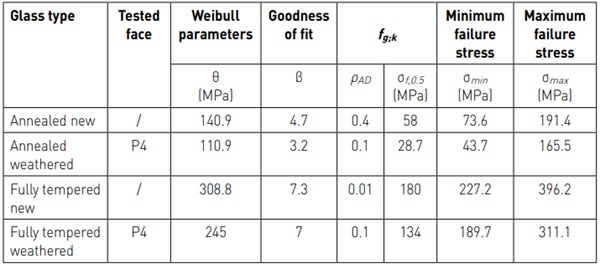
4. Discussion
4.1 Parameters affecting the mechanical performances of glass
It is expected that the quality of the glass surface and the position of the glass panel in the IGU will influence the performance of the post-consumer glass. The effect of the surface quality on the glass strength is visible when comparing the results of the statistical analysis for the QL 1 and QL3 group of series tested with the same ring size. The characteristic bending strength of the QL 1 glass is 53 MPa against the 37 MPa of the glass with QL 3. To confirm this trend it would have been useful some data coming from a QL 2 glass, but not enough glass panes qualified with a QL 2 in order to a statistically reliable series. The strength data coming from the unqualified glass seems to confirm the trend of strength decreasing with the decrease of the surface quality, but still this value couldn’t be reliable compared with that of the other QL series. The surface quality of these glass (unqualified glass) is unknown, since they weren’t event scanned due to the visible rough conditions of the surface (i.e. glass with corrosion or deep contamination by sealants).
Despite the visual inspection of the glass trough the scanner revealed in many cases a clear difference between the internal and external glass panel of the IGU in the number of defects, the mechanical performance of the external (Face P1 and P2 in the Table 5) and internal (Face P3 and P4 in the Table 5) glass doesn’t show a similar difference. The parameter of the tested face highlights an unexpected phenomenon: the faces towards the cavity (i.e., P2, P3) have lower strength than the faces towards the environment (i.e. P1 and P4) (Table 5)
4.2 The influence of thermal tempering on the glass strength
Glass strength increases with thermal tempering. By comparing the data in Table 6, the strength gain attributable to the tempering is higher for the new glass, characterized by an increase of 122 MPa, compared to the ~105 MPa for the post-consumer glass. Based on the results obtained from the two series of post-consumer glass sorted from the panel of QL3, thermal treatment may improve the performances of the post-consumer glass. In order to understand whether the thermal treatments (i.e., tempering and annealing) of the post-consumer glass are economic and environmental profitable, further research is needed.
5. Conclusion
In this study the feasibility of reusing the post-consumer glass to remanufacture an insulated glazing was investigated. The main goal of this research was the evaluation of the post-consumer glass quality, with the effort to find a relationship between the surface state of damage and the mechanical strength. A group of insulated glazing recovered from residential building in Belgium was disassembled manually and the recovered glass tested destructively with a coaxial doble ring test. Before sampling and testing, the glass panes were scanned and classified according to density of surface flaws. These quality classification shows to have an impact on the glass strength. The QL 1 glass with surface quality comparable to the new glass shows also high value of stress at failure. As a result of this study, further research should be directed toward developing a quality protocol for glass surface assessment; extending the performance assessment to other glass types; and identifying valid reconditioning methods of for the post-consumer glass that can improve performance and have a positive impact on the environment.
References
ASTM C1499-03. (2003). Standard Test Method for Monotonic Equibiaxial Flexural Strength of Advanced Ceramics at Ambient Temperature. In ASTM International.
Datsiou, K. C., & Overend, M. (2017). The strength of aged glass. Glass Structures and Engineering, 2(2), 105–120. https://doi.org/10.1007/s40940-017-0045-6
Datsiou, K. C., & Overend, M. (2018). Weibull parameter estimation and goodness-of-fit for glass strength data. Structural Safety, 73, 29–41. https://doi.org/10.1016/j.strusafe.2018.02.002
DeBrincat, G., & Babic, E. (2019). Rethinking the life cycle of architectural glass. Glass International, 42(2), 17–20.
EN 572-8+A1. (2016). Glass in building - Basic soda-lime silicate glass products - Part 8: Supplied and final cut sizes.
EN 1279-2. (2018). Glass in building - Insulating glass units - Part 2: Long term test method and requirements for moisture penetration. In CEN Europe.
European Commission. (2008). DIRECTIVE 2008/98/EC.
European Environment Agency. (2020). Construction and demolition waste: challenges and opportunities in a circular economy.
Geboes, E., Galle, W., & De Temmerman, N. (2022). Make or break the loop: a cross-practitioners review of glass circularity. Glass Structures and Engineering. https://doi.org/10.1007/s40940-022-00211-y
Glass on Web. (2023). How to gain added value from faulty and ‘end-of-life’ insulated glass. https://www.glassonweb.com/news/how-gain-added-valuefaulty-and-end-life-insulated-glass-hegla
Rota, A., Zaccaria, M., & Fiorito, F. (2023). Towards a quality protocol for enabling re-using post-consumer flat glass. [Manuscript submitted for publication in Glass Structures and Engineering]
Sofokleous, I. (2022). Methodology for the prediction of the strength of naturally aged glass based on surface flaw characterization [TU Delft]. https://repository.tudelft.nl/islandora/object/uuid%3Ab6ad7619-da9c-448c-aaf4-10cd065bbe14
Zaccaria, M., & Overend, M. (2016). Thermal Healing of Realistic Flaws in Glass. Journal of Materials in Civil Engineering, 28(2), 04015127. https://doi.org/10.1061/(asce)mt.1943-5533.0001421
Zammit, K., & Overend, M. (2010). Increasing the design strength of glass - fractography and stress testing. In A. Domingo & C. Lazaro (Eds.), International Association for Shell and Spatial Structures (IASS) Symposium 2009.