Article Information
- Digital Object Identifier (DOI): 10.47982/cgc.8.439
- This article is part of the Challenging Glass Conference Proceedings, Volume 8, 2022, Belis, Bos & Louter (Eds.)
- Published by Challenging Glass, on behalf of the author(s), at Stichting OpenAccess Platforms
- This article is licensed under a Creative Commons Attribution 4.0 International License (CC BY 4.0)
- Copyright © 2022 with the author(s)
Authors:
- Markéta Zikmundová - Faculty of Civil Engineering, Czech Technical University in Prague
- Martina Eliášová - Faculty of Civil Engineering, Czech Technical University in Prague
Abstract
Glass is an attractive, transparent but brittle material which is increasingly popular in civil engineering. Not only small and secondary glass structures such as canopies or railings, but also load-bearing structures or structural elements such as stairways, beams, facades, etc. are commonly designed today. The wider use of glass places demands on the connections of glass-to-glass or glass-to-other materials. Mechanical connections are commonly used owing to their known mechanical properties but there is pressure to use adhesives for their considerable advantages. Unfortunately, there is not enough information about the mechanical properties of adhesives exposed to environmental effects and elevated temperature. The paper is focused on experimental testing of glass-to-glass connection using transparent adhesives.
The specimens were prepared as double-lap shear joints with 1 mm adhesive joint thickness. In the study, three two-component epoxy adhesives were selected, one rigid adhesive and two semi-rigid adhesives. Specimens were tested at room temperature (reference set) and at elevated temperature (80 °C), six sets of specimens were prepared in total. The test was controlled by displacement with continuous loading until the specimen’s collapse. The cross-head speed was 0.05 mm/min. Shear strength at failure rapidly decreased for specimens exposed to elevated temperature and each specimen failed due to loss of adhesion between adhesive and glass.
1. Introduction
Glass structures provide transparency, illuminate the interior of the building, but at the same time protect against external influences and are also used as load-bearing structures. Their elegance attracts many investors and architects to implement them. During the solution of the glass structure, it is necessary to solve the connections with respect to their safety and reliability. Nowadays, mainly mechanical joints are used, their mechanical properties are known and their behaviour is verified. However, there is a growing interest in adhesive joints, which provide a number of advantages either from an aesthetic (flat surface, transparency) or mechanical point of view (elimination of stress peaks in the glass, no drilling of holes, vibrations dampening, allowing of thermal expansion, etc.).
However, regulations or standards are missing for adhesive joints, especially for rigid and semi-rigid adhesives. There is ETAG 002 (2012), which only deals with structural sealant glazing kits. There is lack of knowledge about mechanical behaviour of adhesives at elevated temperatures and their resistance to ageing. There is many research dealing with adhesive joints, whether for glass structures, hybrid structures or facades (Blyberg et al. 2012; Goss 2002; Liška et al. 2014; Overend et al. 2011; Silvestru et al. 2019).
This paper investigates two-component transparent semi-rigid and rigid adhesives for glass structures and the effect of elevated temperature on their mechanical properties.
2. Experimental program
The research is focused on the material properties of transparent adhesives, which are suitable for glass-to-glass load-bearing joints. Several selection criteria were determined – large bonded area (around 250x250 mm), thickness of the adhesive 1 mm, low viscosity of the adhesive (bonding technology – pouring into the gap between glasses), long open time (minimum 30 min), transparency of the adhesive, resistance to environmental effects, operating temperature from -20 °C to +80 °C. Preliminary pilot research with 6 adhesives in reference sets was earlier prepared on specimens with different geometry to verify suitability of adhesives for intended application for glass to glass load bearing connection.
Based on the mentioned pilot research, 3 two-component adhesives were selected, one rigid adhesive (R 3) and two semi-rigid adhesives (SR1, SR3). The research is extended to other adhesives. However, not all experimental data are available at the moment. The adhesives are tested in reference set, at elevated temperature of 80 °C and 2 sets of specimens are aged by different artificial ageing methods. This paper describe experiment where mechanical properties were tested at room temperature and at an elevated temperature of 80°C. Six sets of specimens were prepared in total.
2.1. Materials
Float glass with a flat surface was used for the specimen. Three glass panes with dimensions 50x50 mm and nominal thickness 19 mm were bonded as double-lap joint; see Fig. 1. The surface of the bonded area was cleaned and degreased with isopropyl alcohol, no additional treatment was applied.
Glass panes were bonded with 1 mm adhesives. The gap between glasses was defined by inserts with 1 mm thickness. The gap was sealed and subsequently filled with liquid adhesive.
Each set of adhesives includes 5 specimens except adhesive SR1 in the set at elevated temperature where only 3 specimens were tested.
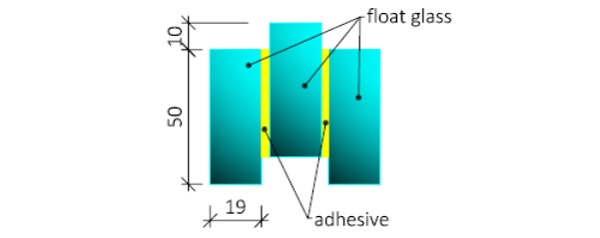
2.2. Test procedure
The test was performed using Shimadzu AGS-X 300 test machine. The specimens were subjected to shear mode loading. Shear stress in the adhesive was induced by compression load on the middle glass pane, see Fig. 2. The test was controlled by displacement applied continuously until the specimen’s collapse. The speed of the crosshead was 0.05 mm/min.
The specimens were placed on the elastic pad and the same elastic pad was located on the loaded surface of the middle glass. This is due to ensuring uniform stress distribution and the elimination ofstress peaks in the glass. The displacement of the middle glass pane and the compression of the pad were measured by four linear potentiometers (two potentiometers per each kind of displacement).
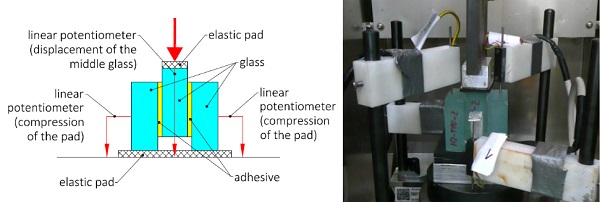
Specimens exposed to elevated temperature were preheated in a heat chamber for about 90 minutes to ensure the temperature 80 °C of the adhesive in the middle of the specimen. Subsequently, the specimen was replaced and tested using the test machine with an integrated heat chamber. After the test, the temperature of the adhesive in the middle of the broken specimen was checked and was 80 °C ± 2 °C in all cases. It can be said, the temperature of the adhesive was during the test at the given temperature 80°C.
3. Results
3.1. Set at elevated temperature
Semi-rigid adhesive SR3 achieved the highest shear strength 0.45 MPa; see Table 1. Other two adhesives, SR1 and R3, reached only about 0.13 MPa average shear strength. Each specimen in all sets failed due to loss of adhesion between adhesive and glass; see Fig. 3.
Table 1: Set of specimens exposed to elevated temperature.
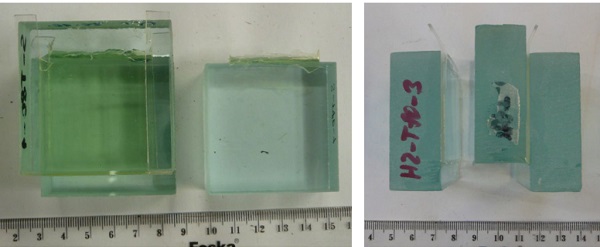
The set of specimens with adhesive SR3 includes two specimens with relatively low shear strength (only about 0.33 MPa); see Fig. 4. The other three specimens achieved approximately the same shear strength 0.52 MPa. The specimens do not contain any air bubbles and no loss of adhesion was observed before the test. The lower shear strength of two specimens probably occurred due to insufficient symmetrical sample placement / loading in the test machine; see Fig. 2.
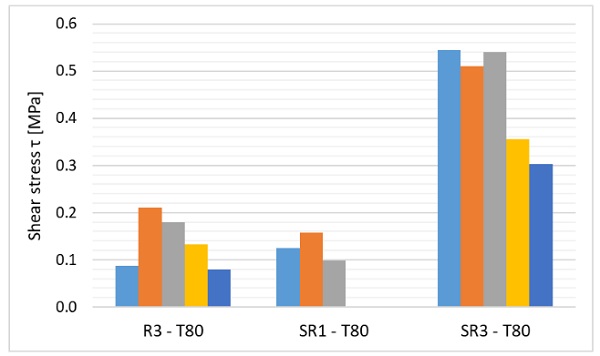
The set of specimens with adhesive R3 showed significant differences in shear strength for each specimen; see Fig. 4. The adhesive layer contained air bubbles. For each specimen in a different quantity. The specimens with the lowest shear force contained the largest number of bubbles. Specimen No. 1 and No. 5 contained a large amount of small air bubbles in all bonded area, see Fig. 5 top left. Specimen No. 2 was bonded almost without bubbles, see Fig. 5 top right. Specimen No. 3 contained more small air bubbles than specimen No.2, but the amount was still small compared to other specimens (Fig. 5 bottom left).
Specimen No. 4 contained larger air bubbles in approximately half of the bonded area, see Fig 4 right. It is not possible to say whether the bubbles were near the glass, but they could (and the experiment seems to have verified this) weaken the adhesion of the adhesive to the glass. The experiment showed that a larger number of small air bubbles over the entire adhesive area is worse for the shear strength of the joint than a larger number of larger bubbles in only part of the bonded joint.
No significant differences in shear strength were observed for specimens with SR1 adhesive as for other sets.
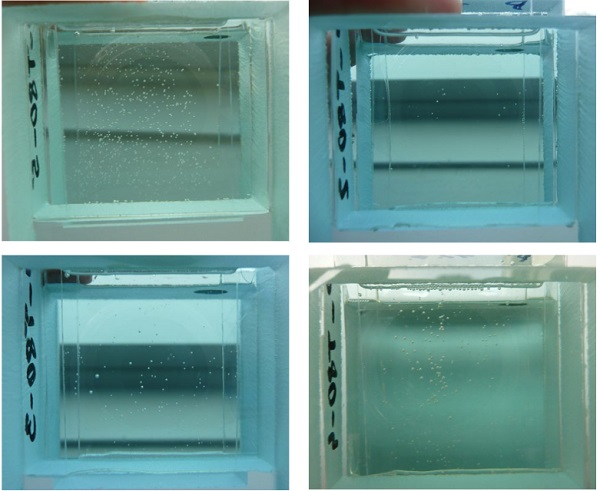
3.2. Comparison of the reference set and the set at elevated temperature
Set of specimens with semi-rigid adhesive SR3 demonstrated the lowest decrease in shear strength at elevated temperature; see Table 2. The adhesive also reached the highest shear strength at elevated temperature and a very high shear strength in the reference set. The shear strength in the reference set was given by the strength of the glass. Failure mode of all specimens was substrate failure. There was not achieved strength of the adhesive in the test.
The lowest resistance to elevated temperature was obtained for specimens with semi-rigid adhesive SR1, only 1.4% of the shear strength in the reference set. Shear strength in reference set was the highest from the tested sets. And the standard deviation of strength was relatively low. Varying failure modes were observed in the reference set; see Fig. 6. Critical was strength of the glass and some specimens showed partly loss of adhesion between adhesive and the glass; see Fig. 7.
Table 2: Reference set of specimens and set of specimens exposed to elevated temperature.
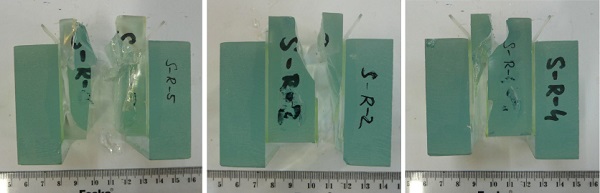
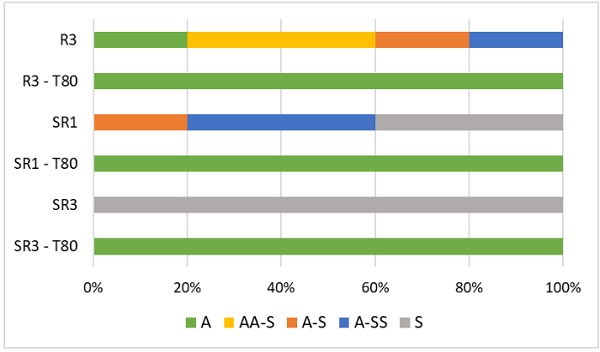
The rigid adhesive showed the lowest shear strength in the reference set. However, decrease in shear strength at elevated temperature was not as poor in comparison to other sets. The loss of adhesion between adhesive and glass proved as a cause of the low shear strength. The specimen with the best adhesion of the adhesive to glass reached twice higher shear strength in comparison to other specimens in the set; see Fig. 8.
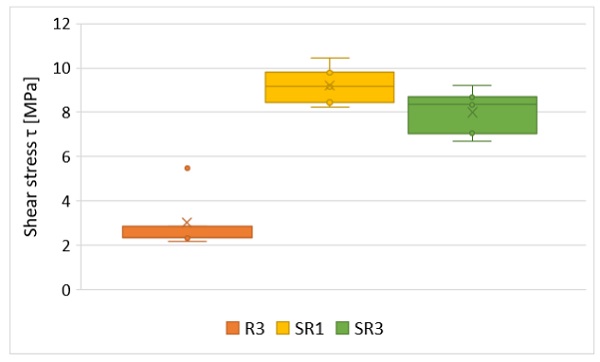
4. Conclusion
Shear strength decreased rapidly with exposure to elevated temperature. Loss of adhesion was observed at elevated temperature for all specimens. Set of specimens with SR3 adhesive reached more than three times higher shear strength at elevated temperature in comparison to other two sets. This adhesive does not contain air bubbles and showed high shear strength in the reference set. The other two sets (with SR1 and R3 adhesive) reached a similar shear strength at elevated temperature, with an average shear strength only 0.13 MPa. Set of specimens with R3 adhesive showed that the shear strength of the bonding is significantly influenced by the number, size and location of air bubbles.
It would be advisable to try another surface treatment before bonding, which would increase the adhesion between the adhesive and the glass when exposed to elevated temperature. For example, plasma treatment achieved very good results in reference testing (Buček et al. 2017; Lundevall et al.2018). Plasma treatment would be appropriate also for R3 adhesive in the reference set where low adhesion between glass and adhesive was observed.
Acknowledgements
The authors thank SPT and Henkel for the adhesive sample and OGB for adhesive and glass panes. The authors also thank Michal Gschray for assistance during experimental testing. This work was supported by the grant No. GA18-10907S and the Student Grant Competition of CTU, grant No. SGS22/140/OHK1/3T/11.
References
Blyberg, L., Serrano, E., Enquist, B., Sterley, M.: Adhesive joints for structural timber/glass applications: Experimental testing and evaluation methods. Int J Adhes Adhes. 35, 76–87 (2012). https://doi.org/10.1016/j.ijadhadh.2012.02.008
Buček, A., Brablec, A., Kováčik, D., Sťahel, P., Černák, M.: Glass bond adhesive strength improvement by DCSBD atmospheric-pressure plasma treatment. Int J Adhes Adhes. 78, 1–3 (2017).https://doi.org/10.1016/j.ijadhadh.2012.02.008
ETAG 002: Guideline for European Technical Approval for Structural Sealant Glazing Kits (SSGK). EOTA, Brussels, Belgium (2012)
Goss, B.: Bonding glass and other substrates with UV curing adhesives. Int J Adhes Adhes. 22, 405–408 (2002). https://doi.org/10.1016/S0143-7496(02)00022-2
Liška, P., Šlanhof, J., Nečasová, B.: Revitalization of Facade Cladding with the Use of Bonded Joints. AMR. 1041, 191–194 (2014). https://doi.org/10.4028/www.scientific.net/AMR.1041.191
Lundevall, Å., Sundberg, P., Mattsson, L.: Improved glass bonding with plasma treatment. Appl Adhes Sci. 6 (2018). https://doi.org/10.1186/s40563-018-0111-6
Overend, M., Jin, Q., Watson, J.: The selection and performance of adhesives for a steel–glass connection. International Journal of Adhesion and Adhesives. 31, 587–597 (2011). https://doi.org/10.1016/j.ijadhadh.2011.06.001
Silvestru, V. A., Kolany, G., Freytag, B., Schneider, J., Englhardt, O.: Adhesively bonded glass-metal façade elements with composite structural behaviour under in-plane and out-of -plane loading. Eng. Struct. 200, 109692 (2019). https://doi.org/10.1016/j.engstruct.2019.109692
CertBond - COST Action CA18120
This paper was presented as part of a special session organised at Challenging Glass Conference 8 by the CertBond Cost Action CA18120 “Reliable roadmap for certification of bonded primary structures”.